I participate in the Amazon affiliate program and may earn commissions from purchases made through links on this page.
Table of Contents
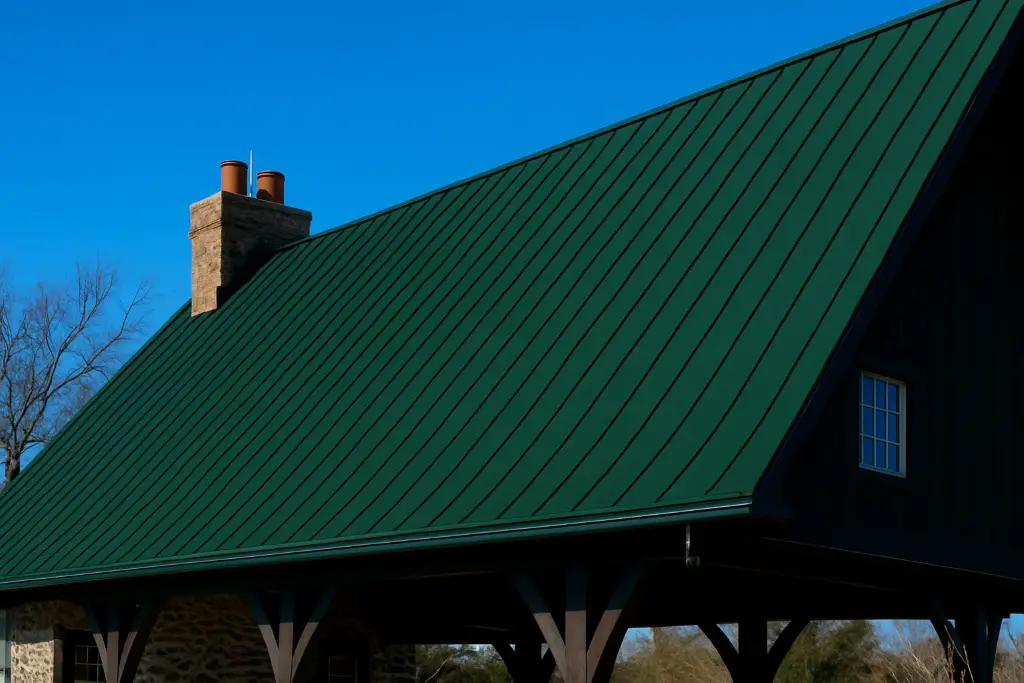
Introduction
The slope of your roof affects how well it sheds rain, snow, and debris, and determines what types of roofing materials are appropriate and can be legally installed. This article explains what the minimum roof pitch is for metal roofing, including metal shingles, standing seam panels, and other metal panel roofing systems.
Note: Pitch and slope are not technically the same thing, but I’ll be using the terms interchangeably here. The building code uses “slope.”
Metal roofing systems vary widely in design and function. Some are designed to be watertight, like standing seam systems with sealed joints, while metal shingles and many lapped panel systems are water-shedding and rely on gravity and panel overlap to function properly. If these systems are installed on a roof that is too flat, water can enter the system through seams or back up under the panel laps, leading to leaks, rotten roof sheathing, and possibly mold. This can void warranties, violate code, and cost a lot of money to fix.
If you aren’t sure what your roof pitch is, you can get a very cheap, very accurate slope finder from Amazon. I have one of these and it works pretty well.
Minimum Allowed Roof Slope for Metal Roofing
The minimum allowed roof slope for metal roofing depends on the type of metal roof system being used. The 2024 International Residential Code (IRC) defines minimum slope requirements for four distinct categories of metal roofing: metal shingles, standing seam panels, and two types of lapped metal panel systems (with and without lap sealant). For a little more information on these different types of metal roofing, see here.
Flat-Seam Metal Panels, Fully-Soldered
Note that while metal roofs with fully-soldered joints are not mentioned in the building code, the Copper Development Association indicates that they can be installed on any roof pitch, no matter how low. Fully-soldered metal systems are very labor-intesive and require an unusually high skill level on the part of the installer, and so they tend to be pretty expensive.
Metal Roof Shingles
Metal roof shingles can only be installed on roofs with a slope of 3-in-12 or greater. This means the roof must rise at least 3 inches for every 12 inches of horizontal run. A 3-in-12 slope can also be expressed as a 14° slope or a 25% slope. Metal shingles function like other shingles in that they rely on gravity and overlapping courses to shed water. Unlike other types of shingles, they are composed of interlocking panels, with each shingle interlocking with the shingles above, below, and to the sides. On low slopes, metal shingles are vulnerable to wind-driven rain and ice damming, which is why installation below 3:12 is prohibited by code.
Even though it’s allowed by code, I wouldn’t recommend installing metal shingles on pitches below 4:12. Standing seam metal panels are preferable for slopes that shallow. They perform much better under low-slope conditions.
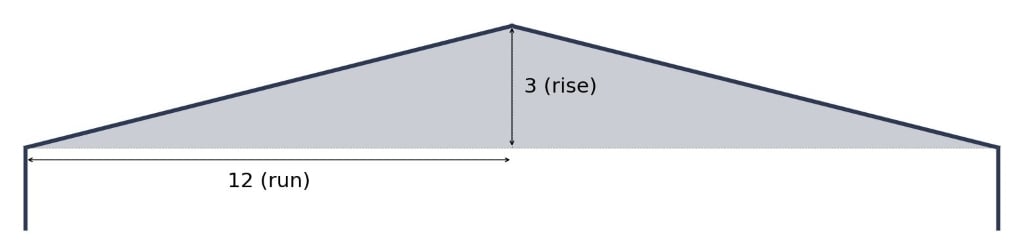
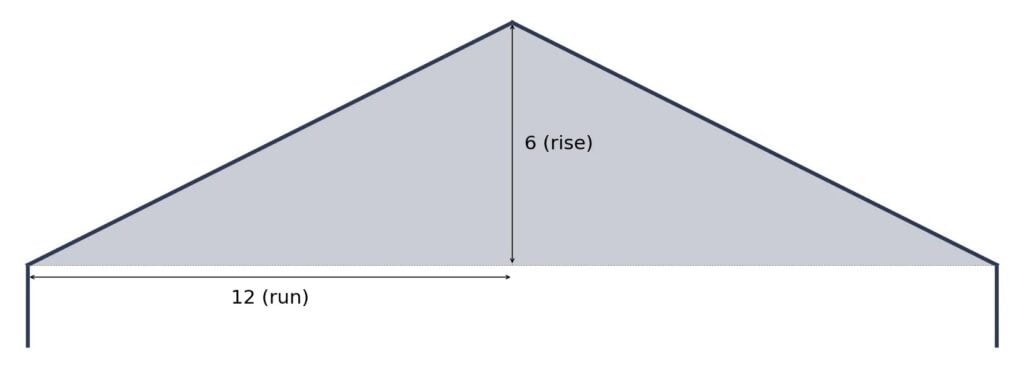
Lapped Metal Panels
Lapped, nonsoldered-seam metal panel roofs without lap sealant also require a minimum slope of 3-in-12. These are typically “through-fastened” or “exposed fastener” panel systems, with panels that are typically from 24 to 36 inches wide and up to 30 feet long. The seams are not soldered or mechanically locked, and there is no sealant applied in the laps. This type of metal roof depends entirely on gravity to keep the water moving and out of the laps. On shallower slopes, water is more likely to be driven up-slope by wind or capillary action, which can allow it to work its way into the laps and cause leaks.
Lapped, nonsoldered-seam metal panel roofs with lap sealant are permitted on slopes as low as ½-in-12. A ½-in-12 slope can also be expressed as a 2.5° slope or a 4% slope. In these systems, a continuous bead of sealant, typically a butyl-based or polymer-modified bitumen tape or caulk, is applied inside the overlapping edges of each panel. This creates a watertight barrier that prevents water intrusion, even at low slopes. The sealant must be applied exactly according to the manufacturer’s instructions. If it is left out, improperly applied, or the wrong product is used, the roof may fail prematurely. Because these systems rely so heavily on the quality of the sealant and the configuration of the system, the manufacturer’s installation instructions must be followed precisely.

Standing Seam Metal
Standing seam metal roofs can be installed on slopes as low as ¼-in-12, which is the lowest allowable slope for any roofing system in the IRC (except for coal-tar built-up roofing at ⅛-in-12, which hardly anyone installs any more). A ¼-in-12 slope can also be expressed as a 1.2° slope or a 2% slope. These systems use long, vertical panels with interlocking raised seams that are either mechanically crimped or snapped together. Most standing seam systems include concealed fasteners and factory-applied or field-applied seam sealants to provide full watertight protection. Because they are engineered as sealed systems, they are well suited to low-slope applications as long as they are installed with precision and proper detailing at penetrations and terminations.

Installing metal roofing on a roof with a slope below the code-required minimum can lead to serious problems. The risks depend on the type of system, but in general, lower-slope installations are more vulnerable to water intrusion, ice damming, and wind-driven rain. Because some metal roofing systems rely on gravity and overlapping joints to shed water, too shallow a slope can allow water to get through the roof at the laps and into the structure below. This can saturate the underlayment and deck, leading to rot, corrosion, mold, and interior damage.
Manufacturers explicitly prohibit installation below the minimum slope for each product type, and doing so will void the product warranty. It also violates the building code, which can result in failed inspections, insurance claim denials, and legal or financial liability for the contractor.
Metal shingles and unsealed lapped panels are both limited to slopes of 3:12 or greater. While this meets the minimum code requirement, it is not ideal. These systems are water-shedding; they do not present a continuous waterproof barrier like low-slope roof membranes do. The fact that their seams are not sealed means that water can more easily be pushed upward by wind or drawn into laps by capillary action. On roofs with slopes below 4:12, these risks increase significantly, especially in snowy or high-wind areas.
Even sealed lapped panel systems and standing seam roofs – though technically allowed on slopes as low as ½:12 and ¼:12, respectively – still require extreme care in detailing and installation. Roofs with slopes under 3:12 don’t shed water quickly, and any mistake in panel alignment, seam sealing, or flashing can compromise the entire system. Sealed systems must be installed exactly per manufacturer specifications or they might fail.
Code Sections: Minimum Roof Slope
Code for Metal Roof Shingles
From the 2024 International Residential Code, here’s the section that dictates acceptable roof slope for metal roof shingles:
Metal roof shingles shall not be installed on roof slopes below 3 units vertical in 12 units horizontal (25-percent slope).
R905.4.3 Underlayment
Underlayment shall comply with Section R905.1.1.
R905.4.3.1 Ice Barrier
Where required, ice barriers shall comply with Section R905.1.2.
And here’s the equivalent section from the 2024 International Building Code:
Metal roof shingles shall not be installed on roof slopes below 3 units vertical in 12 units horizontal (25-percent slope).
1507.5.3 Underlayment
Underlayment shall comply with Section 1507.1.1.
1507.5.4 Ice Barrier
Where required, ice barriers shall comply with Section 1507.1.2.
Code for Metal Roof Panels
From the 2024 International Residential Code, here’s the section that dictates acceptable roof slope for metal roof panels:
Minimum slopes for metal roof panels shall comply with the following:
1. The minimum slope for lapped, nonsoldered-seam metal roofs without applied lap sealant shall be 3 units vertical in 12 units horizontal (25-percent slope).
2. The minimum slope for lapped, nonsoldered-seam metal roofs with applied lap sealant shall be ½ unit vertical in 12 units horizontal (4-percent slope). Lap sealants shall be applied in accordance with the approved manufacturer’s installation instructions.
3. The minimum slope for standing-seam roof systems shall be ¼ unit vertical in 12 units horizontal (2-percent slope).
R905.10.6 Underlayment
Underlayment shall comply with Section R905.1.1.
And here’s the equivalent section from the 2024 International Building Code:
Minimum slopes for metal roof panels shall comply with the following:
1. The minimum slope for lapped, nonsoldered seam metal roof panels without applied lap sealant shall be three units vertical in 12 units horizontal (25-percent slope).
2. The minimum slope for lapped, nonsoldered seam metal roof panels with applied lap sealant shall be one-half unit vertical in 12 units horizontal (4-percent slope). Lap sealants shall be applied in accordance with the approved manufacturer’s installation instructions.
3. The minimum slope for standing-seam metal roof panel systems shall be one-quarter unit vertical in 12 units horizontal (2-percent slope).
1507.5.3 Underlayment
Underlayment shall comply with Section 1507.1.1.
Underlayment Requirements
Here are the IRC underlayment requirements for metal roofing just mentioned in section R905.10.6:
Underlayment Application – Metal Roof Shingles & Metal Panels (Table R905.1.1(2))
Areas Where Wind Design Is Not Required In Accordance With Figure R301.2.1.1:
Apply in accordance with the manufacturer’s installation instructions.
Areas Where Wind Design Is Required In Accordance With Figure R301.2.1.1:
Underlayment shall be one of the following:
1. Two layers of mechanically fastened underlayment applied in the following manner: Apply a strip of underlayment that is half the width of a full sheet parallel to and starting at the eaves, fastened sufficiently to hold in place. Starting at the eave, apply full width sheets of underlayment, overlapping successive sheets half the width of a full sheet plus 2 inches. End laps shall be 4 inches and shall be offset by 6 feet.
2. A minimum 4-inch-wide strip of self-adhering polymer modified bitumen underlayment complying with ASTM D1970, installed in accordance with the manufacturer’s installation instructions for the deck material, shall be applied over all joints in the roof decking. An approved underlayment complying with Table R905.1.1(1) for the applicable roof covering shall be applied over the entire roof over the 4-inch-wide membrane strips.
3. A single layer of self-adhering polymer modified bitumen underlayment complying with ASTM D1970, installed in accordance with the underlayment and roof covering manufacturer’s installation instructions for the deck material, roof ventilation configuration and climate exposure of the roof covering.
Note that the second part of this (Areas Where Wind Design Is Required) applies to geographic regions where buildings must be engineered to withstand higher wind forces due to increased risk of strong winds. These areas include designated hurricane-prone regions, coastal high-wind zones, and areas like mountain foothills and tornado-prone zones.
The language in the code means that the double underlayment requirement applies to all roofs, regardless of slope, in these areas. Increased roofing fastener requirements will normally also apply in these areas.