Table of Contents
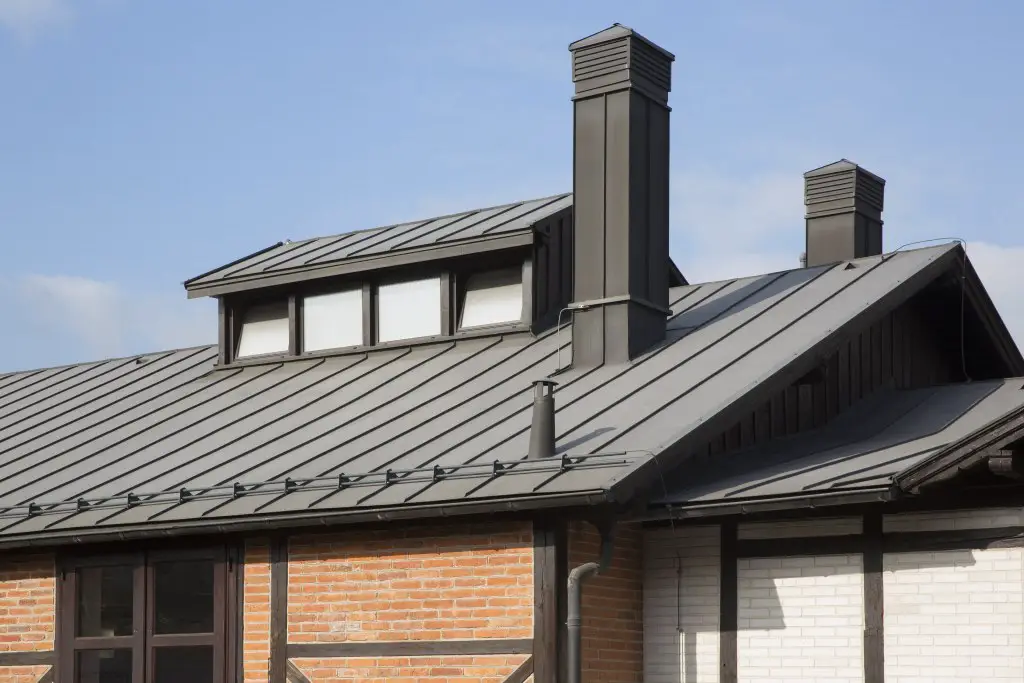
Introduction
I’ve spent a lot of time researching roof replacement costs for my clients. I’ve had to keep up-to-date with roofing material and labor costs for years. I thought keeping and updating accurate zinc roof cost estimates online (among other roof material types) would be a helpful resource for me, my clients, and homeowners in general, so here you go.
Keep in mind that zinc is considered a semi-premium roofing material and the price of zinc can fluctuate somewhat based on market conditions and supplier availability. With metal roofing in particular, the materials make up a more significant portion of the overall roof cost, so the cost of a zinc roof can fluctuate more abruptly than the cost of most other types of roofing. Copper roofing prices tend be more noticeably affected by this factor, though. Also, unlike copper roofing and most types of roofing in general, most zinc roofing in the United States is manufactured in Europe and imported.
A good way for you to get the best ballpark numbers is to contact a local roofing contractor who actually currently installs zinc roofs and ask him how a zinc roof usually compares to an asphalt shingle roof cost-wise (very unlikely a contractor will outright give you a quote without being invited to bid on the job). I do think this article provides reasonably accurate average estimates.
The cost of a zinc roof depends on factors such as roof size, roof pitch, roof complexity, labor costs, and the zinc roofing style chosen. The prices provided here are averages and intended to give a general idea of costs involved.
On average, zinc roof costs in 2025 range from around $12 per square foot for corrugated zinc panels to approximately $24 per square foot for standing seam zinc roofing. These prices reflect commonly used architectural zinc products, typically in 22 to 24 gauge (0.031″–0.028″) thickness, fabricated as panels or shingles from 1-meter wide coils or sheets.
For an average 1,700-square-foot roof using standing seam zinc (the most commonly installed zinc roofing type), the national average cost is approximately $40,800.
Also see my more general Metal Roof Cost Guide if you’re interested in other types of metal roofing.
Types of Zinc Roofing
The tables below give typical zinc roof prices according to the type of zinc roofing system chosen. Each type affects cost, appearance, longevity, and installation requirements.
Standing Seam Zinc Roofs
Standing seam zinc roofs use long panels with raised vertical seams running from ridge to eaves. This type of seam generally provides better waterproofing and drainage. Panel widths typically range between 12 and 20 inches.
Properly-installed standing seam roofs accommodate thermal expansion. The longitudinal seams allow for controlled movement under thermal cycling, which is essential for large panel spans. Zinc roofing panels require proper ventilation; typically an underlayment with a capillary break, like a mesh ventilation mat, to prevent trapped moisture beneath the panel and ensure long-term durability. This underlayment helps prevent underside corrosion of the zinc panels.
To avoid oil-canning (visible waviness in flat metal surfaces), panels can be fabricated with slight ribs, striations, or be tension-leveled during production. Factory or field hemming of panel edges is recommended to improve wind uplift resistance and prevent panel disengagement. Installations on slopes below 3:12 may require soldered or sealed joints and additional waterproofing measures.
Read more about standing seam roof costs.
Flat Lock Zinc Panels
Flat lock zinc roofing consists of smaller zinc panels (but typical larger than zinc shingles) interconnected with folded flat seams.
Flat lock zinc roofing requires skilled, attentive installers due to the seaming process, which requires that all edges of each panel are carefully inter-folded with its neighbors, slightly increasing installation costs compared to zinc shingles. Each panel is typically square or rectangular and installed in a staggered pattern, with seams hand-folded and locked together on-site.
To prevent water intrusion on slopes below 3:12, seams must be soldered or sealed with a butyl-based joint compound. Installers often use concealed clips and cleats to secure the panels while allowing for thermal movement.
Zinc sheets used for flat lock work are often cut from 0.7 mm (approximately 22 gauge) stock, with panel sizes limited to reduce oil-canning and control for thermal expansion. A breathable separation layer is recommended between the zinc and any moisture-retentive substrate such as plywood or fiberboard.
Zinc Shingles
Zinc shingles are small, interlocking tiles fastened with concealed clips or tabs. They’re easier to install than flat-lock or standing seam panels and often come with lower material costs, making them the most affordable zinc option for residential roofing.
Some zinc shingle systems are designed to maintain a ventilation gap underneath, reducing the need for a separate vented underlayment.
Corrugated Zinc Panels
Corrugated zinc panels are most often used in agricultural and industrial settings due to their lower cost and minimal aesthetic appeal. They’re rarely used in residential construction because they don’t typically meet stricter building code and performance requirements for homes.
Things to Keep in Mind
These zinc roof cost estimates should be fairly accurate; I make an effort to keep them updated using current material prices and labor data.
Costs listed here are national averages; actual local costs can vary significantly. For a better idea of local zinc roofing costs, see “Relative Construction Costs by U.S. State” and apply your local multiplier to the national average.
The zinc roof cost estimates provided here assume a roof pitch of 6/12 or below and include all standard zinc roofing components. Steeper roofs or complex designs can increase costs by up to 50%. Removal of existing roofing typically adds between $1 to $3 per square foot.
Table 1: Zinc Roof Cost per Square Foot
Average Cost of a Zinc Roof | |||
---|---|---|---|
Type of Zinc Roofing |
Average Installed Cost Per Square Foot |
Average Installed Cost Per Square (100 sq. ft.) |
Average Installed Cost Average Roof (1,700 sq. ft.) |
Zinc Shingles | $18 | $1,800 | $30,600 |
Flat Lock Zinc Panels | $22 | $2,200 | $37,400 |
Standing Seam Zinc | $24 | $2,400 | $40,800 |
Corrugated Zinc Panels | $12 | $1,200 | $20,400 |
Table 2: Zinc Roof Cost by Roof Size
Cost of a Zinc Roof by Roof Size | |||
---|---|---|---|
Roof Area | Average Installed Cost Zinc Shingles |
Average Installed Cost Standing Seam Zinc |
Average Installed Cost Flat Lock Zinc |
750 SF | $13,500 | $18,000 | $16,500 |
1000 SF | $18,000 | $24,000 | $22,000 |
1250 SF | $22,500 | $30,000 | $27,500 |
1500 SF | $27,000 | $36,000 | $33,000 |
1750 SF | $31,500 | $42,000 | $38,500 |
2000 SF | $36,000 | $48,000 | $44,000 |
2250 SF | $40,500 | $54,000 | $49,500 |
2500 SF | $45,000 | $60,000 | $55,000 |
2750 SF | $49,500 | $66,000 | $60,500 |
3000 SF | $54,000 | $72,000 | $66,000 |
Zinc Roof Cost Factors
Primary cost factors for zinc roofing are labor and materials, typically split 50% materials and 50% labor. The total breakdown can vary somewhat according to the roof style chosen, roof complexity, zinc panel thickness, and local labor rates and experience level required.
Material Costs
Material costs depend on zinc type, roof size, zinc panel thickness, and necessary accessories such as specialized fasteners, flashings, ridge caps, and drip edges.
Labor Costs
Labor costs are influenced by geographic location and the skill required due to the complexity of the installation. Zinc roof installations generally require skilled craftsmanship, particularly for intricate seaming and folding, increasing overall labor expenses. On average, installing zinc shingles or panels may take between 8 to 12 labor hours per square.
Roof Complexity and Pitch
Complex roofs with multiple valleys, skylights, chimneys, or intricate details increase labor time and costs. Steep roofs require additional safety measures, potentially raising labor costs by 20% to 50%.
Removal of Existing Roofing
Removing all existing roofing is absolutely recommended before installing zinc to ensure a smooth substrate that allows for properly ventilating the underside of the roof panels. Removal typically costs around $1 to $3 per square foot.
Local Taxes, Fees, and Permits
Permit fees, taxes, and disposal charges can vary widely and add to overall roofing project costs.
More About Zinc Roofing
Zinc roofs are long-lasting, require minimal maintenance, and they develop a distinctive natural patina. Patina formation takes approximately two to five years and helps protect the zinc from further corrosion. Roofing zinc is 100% recyclable.
Zinc can be vulnerable to certain types of deterioration that can significantly impact its performance if not properly managed. If you’re thinking about installing a zinc roof you should understand its compatibility with other materials and the environmental conditions it will be exposed to.
Here are some important things to be aware of:
Galvanic Corrosion: Zinc can suffer from galvanic corrosion when it comes into direct contact with more noble metals like copper or pure iron in the presence of an electrolyte such as rainwater. This interaction causes the zinc to corrode preferentially, which can compromise the roof’s integrity if dissimilar metals are not properly isolated.
Thermal Expansion: Zinc has a high coefficient of thermal expansion. This means that it expands and contracts significantly with temperature changes. If the roof system is not designed to accommodate this movement, it can lead to panel damage or metal fatigue failure over time.
Environmental Sensitivity: In highly polluted or industrial environments, zinc’s protective carbonate layer can degrade, forming zinc sulfate, which is water-soluble and easily washed away. This leads to continued exposure of fresh metal, increasing the rate of corrosion. This process can also stain nearby building materials.
Maintenance Needs: Zinc roofs require minimal maintenance, but any repair or maintenance work should take into account their sensitivity to specific environmental factors and interactions with other materials. Use appropriate primers, paints, and other materials. In particular, you should be aware of possible galvanic corrosion issues before selecting metal repair or modification materials like screws, sheet metal, or pipe boots.
Material Creep and Brittleness: Over time, zinc can exhibit “creep” – a slow, permanent deformation under mechanical stress – at normal temperatures. It also becomes somewhat brittle in cold weather (below 45°F / 7°C), so handling and installation is best put off until warmer weather.