Table of Contents
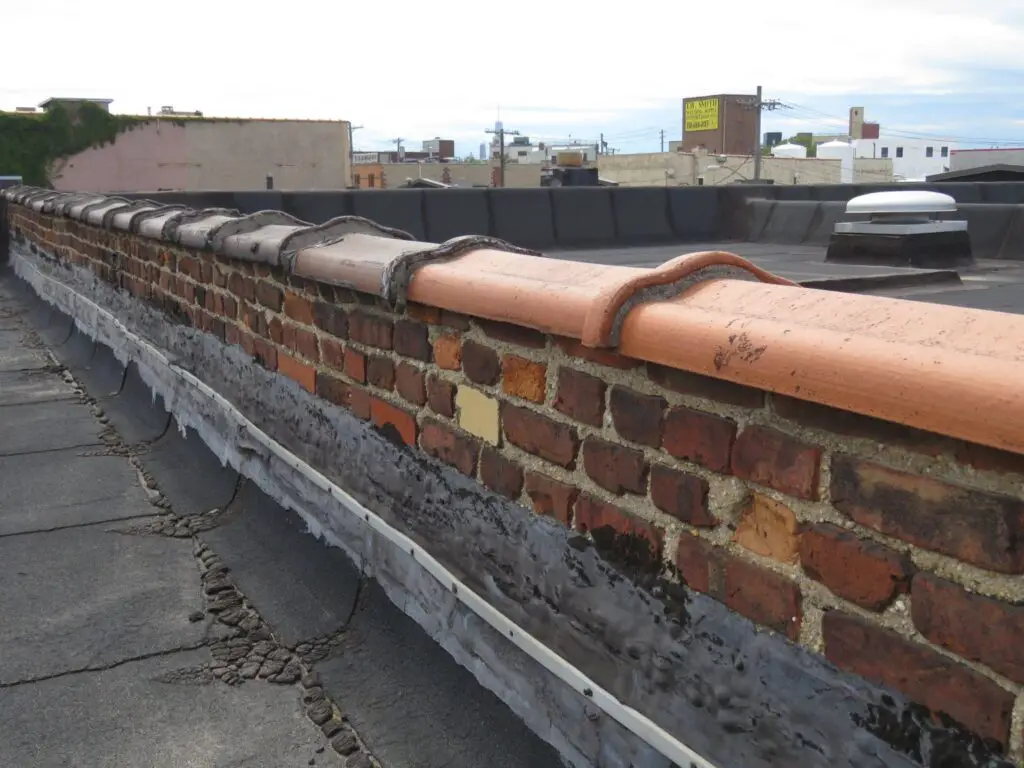
What is Coping in Roof Construction?
Wall coping serves as a protective cap or cover on the top of a wall, designed to prevent water infiltration from above. Coping is typically slanted or curved in order to shed water, reducing the likelihood of moisture penetration that could lead to wall degradation or damage to the roof system. In the context of roofing, the term “roof coping” commonly refers to the coping installed on parapet walls to protect both the wall and the roof.
Other terms used for coping include “wall cap”, “wall cover”, “coping cover”, and “coping cap”. Which term is used typically depends on the geographic region and the specific design purpose of the coping. Where the coping also serves as protective counter-flashing for the top of base flashing at a wall, it is known as “cap flashing”.
Cap flashing not only protects the wall from water infiltration from above but also serves as a part of the roof system by overlapping the upper edge of the roof base flashing. This is particularly common in roofing systems where the roof membrane terminates at low parapet walls.
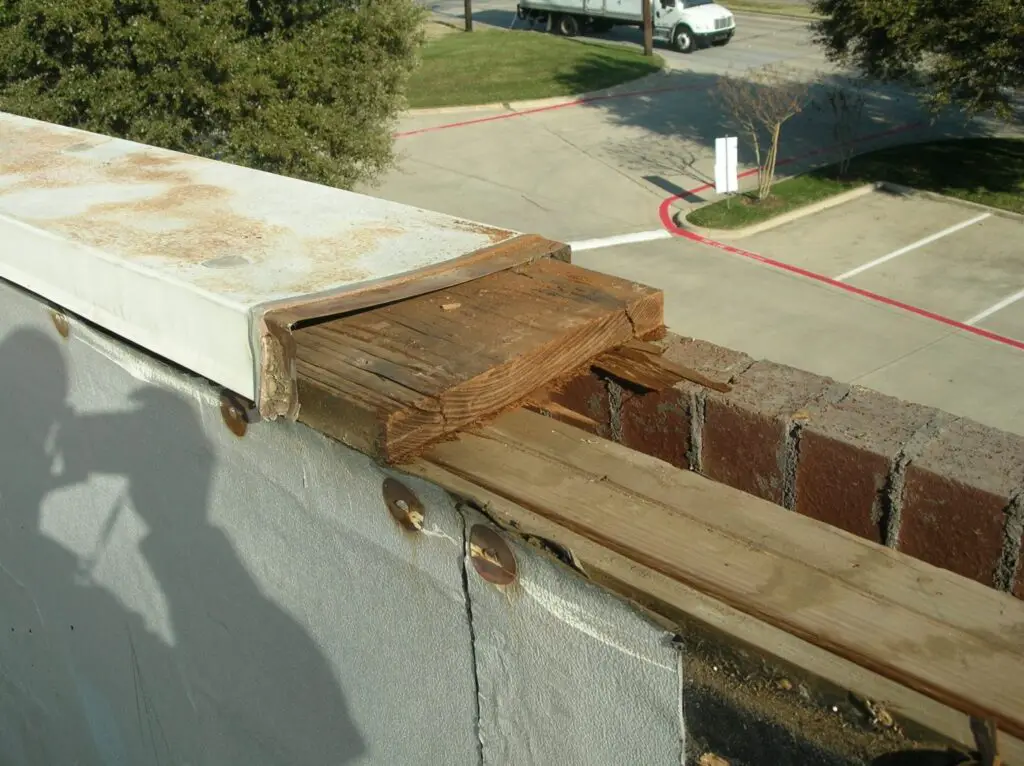
Materials
Coping materials vary depending on structural requirements, aesthetic considerations, and climate conditions. Common materials include metal (such as galvanized steel, aluminum, stainless steel, and copper), precast concrete, natural stone, and masonry units.
Metal coping is often preferred for commercial buildings; it’s relatively cheap, lightweight, and quick and easy to install. Stone, terra cotta, and concrete provide a more traditional appearance as well as excellent long-term weather resistance.
See my article Types of Wall Coping to learn more about parapet wall coping materials.
Purpose of Parapet Wall Coping
Why does a wall need coping? To keep water out of the wall! Water infiltration into a wall can lead to a number of things, none of them good.
When water gets into the interior of a masonry wall and then migrates out through porous masonry such as brick or concrete masonry units, it can lead to unsightly efflorescence.
Efflorescence is a commonly seen white discoloration on the outside surface of a wall caused by deposits of natural salts from the wall material. The salts are absorbed by moisture as it travels through the material and then left behind when the moisture evaporates. Efflorescence alone does not necessarily mean that you have a problem with your coping. Moisture from interior humidity can condense within the wall structure and migrate outwards.
Efflorescence is typically harmless, but it can look bad. Heavy efflorescence deposits are often a sign of chronic moisture movement through the wall, which may lead to accelerated deterioration.
Far worse than efflorescence is what happens when water within the structure of a wall freezes. The freeze-thaw cycle is not kind to walls.
When water freezes, it expands with tremendous force, and this can cause cracks in the masonry units, mortar joint failure, and a general deterioration of the wall’s structural integrity. Repeated cycles of freezing and thawing can cause spalling, where flakes or chunks of brick, stone, or concrete break off from the surface, leaving the wall pitted and vulnerable to further damage.
Pieces of mortar can fall out of the joints, which will let even more water in. The masonry units themselves can become loose, leading to serious structural instability. Steel masonry ties and anchors embedded in the wall for lateral support can corrode when exposed to moisture. Rust formation on steel not only weakens the ties but also causes expansion, exerting additional pressure that can widen cracks and push masonry units out of alignment.
Other wall components fare even worse when exposed to moisture.
Steel framing, lintels, and reinforcement bars are highly susceptible to long-term corrosion. Rusted steel can expand up to eight times its original thickness, exerting enormous pressure on surrounding materials. This can lead to buckling of masonry walls, fractured mortar joints, and even catastrophic structural failure if left unaddressed.
Wood components suffer a different but equally severe fate. Wood sheathing absorbs water and swells, delaminates, or even disintegrates, particularly in the case of low-quality OSB (oriented strand board), which is highly vulnerable to moisture. Wood framing members undergo a slow but relentless process of deterioration, warping, twisting, and weakening as they cycle through absorption and drying. Over time, this can result in misaligned wall structures, nail pops, and even mold or fungal decay, creating an environment conducive to rot and pest infestations.
Beyond the structural implications, water-damaged walls impact insulation performance. Saturated insulation loses its ability to resist heat flow, leading to energy loss, increased heating and cooling costs, and a less comfortable indoor environment.
Coping serves as the first line of defense against these issues. By keeping water out of the wall, coping protects the building from premature component failure, reduces maintenance costs, and extends the lifespan of the structure.
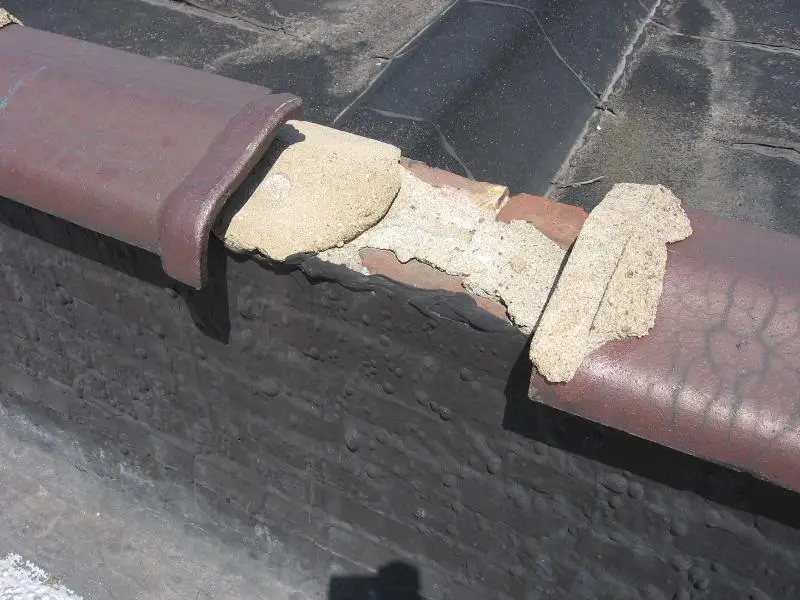
Building Codes and Coping
The International Building Code mandates that parapet walls be adequately protected by noncombustible, weatherproof materials. Specifically, the code states that parapet walls “must be properly coped with noncombustible, weatherproof materials of a width not less than the thickness of the parapet wall.”
Also note that when roof coping doubles as perimeter edge securement for single-ply roof membranes, it should follow the standard laid out in ANSI/SPRI/FM 4435/ES-1 “Test Standard for Edge Systems Used with Low Slope Roofing Systems”. See the next section, “Coping as Roof Membrane Perimeter Edge Securement” farther down this page.
Here’s what the 2024 versions of the IBC and IRC have to say about coping:
International Building Code (2024 IBC):
“Parapet walls shall be coped or covered in accordance with Sections 1503.3.1 and 1503.3.2. The top surface of the parapet wall shall provide positive drainage.”
1503.3.1 Fire-Resistance-Rated Parapet Walls
“Parapet walls required by Section 705.12 shall be coped or covered with weatherproof materials of a width not less than the thickness of the parapet wall such that the fire-resistance rating of the wall is not decreased.”
“Parapet walls meeting one of the exceptions in Section 705.12 shall be coped or covered with weatherproof materials of a width not less than the thickness of the parapet wall.”
International Residential Code (2024 IRC):
“Flashings shall be installed in a manner that prevents moisture from entering the wall and roof through joints in copings, through moisture permeable materials and at intersections with parapet walls and other penetrations through the roof plane.”
“Parapet walls shall be properly coped with noncombustible, weatherproof materials of a width not less than the thickness of the parapet wall.”
Coping as Roof Membrane Perimeter Edge Securement
Parapet wall coping as roof edge securement: Single-ply roofing membranes often run up the inside of the parapet wall and terminate underneath a metal coping. This termination method not only protects the membrane edge but also secures it against wind uplift forces. Properly designed coping ensures that the membrane remains in place under varying weather conditions and prevents water from infiltrating the roof assembly.
Where the coping functions as roof edge securement, the International Building Code (IBC) requires that the coping comply with ANSI/SPRI/FM 4435/ES-1 Test Standard for Edge Systems Used with Low Slope Roofing Systems (commonly referred to as “ES-1”).
This standard establishes minimum performance criteria for edge securement, ensuring that the coping can withstand expected wind pressures and prevent membrane blow-off or detachment. The full standard can be seen on the SPRI website here.
From the 2024 IBC:
1504.6 Edge Systems for Low-Slope Roofs
“Metal edge systems, except gutters and counterflashing, installed on built-up, modified bitumen and single-ply roof systems on a low-slope roof shall be designed and installed for wind loads in accordance with Chapter 16 and tested for resistance in accordance with Test Methods RE-1, RE-2 and RE-3 of ANSI/SPRI ES-1, except basic wind speed, V, shall be determined from Figures 1609.3 (1) through 1609.3 (4), as applicable.”
Wind uplift forces at the perimeter and corners of a roof can be two to four times greater than in the field of the roof, making ES-1 compliance particularly critical. Improperly secured coping can lead to failure at the roof edge, allowing wind-driven rain to penetrate the system, detaching sections of the roof membrane, and potentially causing extensive, very expensive damage.
I have personally performed roof storm damage assessments where parapet coping failure resulted in catastrophic roof failure, where the entire roof had to be replaced.
It’s important to verify that a proposed coping system which will serve as edge securement meets this standard before approving or installing it. Coping manufacturers should provide ES-1 compliance ratings based on tested assemblies, while roof system manufacturers may also allow coping fabricated by a certified metal shop to be used with their systems.
Manufacturers’ websites will usually let you know if their products comply. Factory-fabricated coping systems are typically tested for compliance, while shop-fabricated coping should be made by a certified shop. In the U.S., the National Roofing Contractors Association (NRCA) provides a list of authorized fabricators.
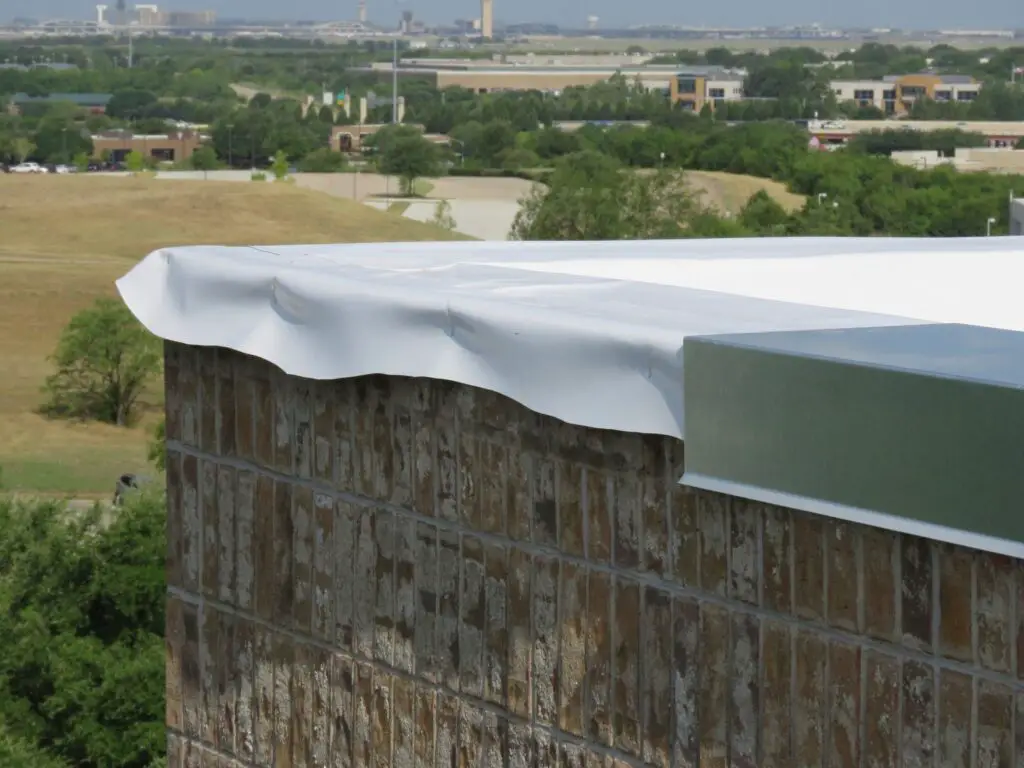
The metal in the picture is a section of the continuous cleat that the coping will be attached to.
Notes on Coping in Roof Construction
Coping Should be Sloped Toward the Interior
Slope: The top surface of a well-designed parapet wall coping should be slanted or curved to shed water. This reduces the chance that water will enter the wall through open coping joints or leave unsightly stains on the top of the coping as the water evaporates. Without a proper slope, water may pool on the surface, accelerating material degradation and increasing the likelihood of leaks.
Parapet wall copings should be slanted back toward the roof, toward the interior, in order to reduce the amount of water running down the exterior wall of the building, which can contribute to a few different issues, including unsightly discoloration of the wall and mortar failure in the joints between whatever masonry units were used to construct the wall or wall veneer.
Excessive water runoff down the exterior wall can also lead to efflorescence, a condition where dissolved salts in masonry materials are deposited on the wall surface, creating a chalky white residue. Over time, this continuous exposure to moisture may also contribute to the deterioration of exterior coatings, requiring more frequent maintenance and repair.
Coping Should Have Drip Edges
Drip edges: Good copings should have drip edges on each side of the wall. This reduces the amount of water running down the surface of the wall, but more importantly, it reduces the chance that water will be able to enter the joint between the coping and the top of the wall. Drip edges help prevent capillary action, where water can cling to the underside of coping and seep into cracks or joints.
Although the building code requires that coping be at least as wide as the wall, the coping should be slightly wider, wide enough to allow the drip edges to function properly. A sufficient overhang, typically between ½ inch and 1 inch past the face of the wall, ensures that water is effectively directed away from vertical surfaces. If the overhang is insufficient, the drip edge may be ineffective, allowing water to track back toward the wall and penetrate vulnerable areas.
For metal copings, formed drip edges should be incorporated into the design during fabrication, ensuring a continuous, uninterrupted edge. In stone or precast concrete copings, a precisely cut drip groove should be included on the underside to help break the surface tension of the water and encourage proper drainage.
Coping Should Have a Secondary Water Barrier
Secondary waterproofing membrane: A secondary water barrier should be installed on top of the wall underneath all parapet wall copings.
Coping joints and even some coping materials will typically develop cracks, become dislodged, or permit water entry in some other way as time goes by. Building sealant deteriorates, and freeze-thaw cycles can exacerbate material movement, leading to increased water penetration. Wind uplift can also loosen sections of coping, making them more vulnerable to leaks.
A secondary water barrier keeps a simple maintenance item from turning into an expensive repair job. This barrier serves as a last line of defense against water infiltration, redirecting any moisture that penetrates the coping back onto the roof system instead of allowing it to seep into the wall assembly.
This barrier is typically a layer of sheet metal, sealed at the laps, but flexible single-ply roof membrane material is often used as well, particularly under metal copings. Sometimes a single-ply roof membrane will run up the parapet and across the top of the wall, performing this function as well.
It is important to seal all holes through this barrier (at fasteners, dowels, and anchors) where the coping attachment method requires the barrier to be penetrated. In metal coping systems, fasteners should be properly gasketed to prevent water entry, and sealant should be applied around any penetrations. If anchors or dowels are used in masonry or concrete coping installations, flashing or sealant should be incorporated to minimize moisture intrusion at these points.
Coping Should Be Securely Fastened and Designed to Resist Uplift
Attachment and Structural Integrity: Proper attachment of coping is essential to ensure that it remains secure under various environmental conditions. Coping that is not adequately fastened can become loose or dislodged due to wind uplift, thermal expansion, or building movement.
For metal copings, the most reliable attachment method includes continuous cleats and concealed fasteners which allow for thermal movement. Copings secured with only face-fastened screws are more susceptible to wind load and may loosen over time, increasing the risk of water infiltration and eventual failure. The use of a continuous cleat along the exterior face, combined with interior fasteners or clips, helps distribute wind loads more effectively and enhances the coping’s ability to resist uplift.
For masonry or stone copings, mechanical anchors, dowels, construction adhesives, or a combination of these should be used to provide long-term stability. These coping materials are heavy, and if not properly secured, they pose a significant safety risk if they become loose and fall from the building. Expansion joints should also be included in long runs of masonry or stone coping to accommodate thermal movement and prevent cracking or displacement.
Wind uplift resistance is a critical consideration, particularly in regions with frequent storms or high winds. Wind uplift force at the perimeter of a roof (including edges and corners) can be two to four times greater than in the field of the roof. Coping should be designed to comply with ANSI/SPRI/FM 4435/ES-1, which provides guidance on the securement of edge metal to withstand specified wind loads. Compliance with these standards should ensure that the coping system will remain intact even in extreme weather conditions.
Differential movement between the parapet wall and the coping material should also be accounted for in the design. Temperature fluctuations cause materials to expand and contract at different rates, which can lead to stress fractures or gaps if not properly managed. In metal coping systems, slotted fastener holes and expansion joints allow for controlled movement without compromising the securement of the coping.
A properly fastened coping system not only extends the lifespan of the parapet and the roof system but also ensures safety by preventing pieces of coping from becoming airborne hazards during high-wind events. Regular inspections should be conducted to check for any loose fasteners, displaced sections, or gaps that may have developed over time.
Roof Coping Inspection and Maintenance
Inspection Guidelines
A comprehensive roof coping inspection should be performed at least twice a year, typically in spring and fall, as well as after severe weather events such as high winds, heavy rain, or snowstorms.
During inspections, check for the following issues:
1. Physical Damage
- Cracks, Chips, or Breaks in Masonry or Concrete Coping: Inspect for signs of deterioration caused by freeze-thaw cycles, impact damage, or material aging.
- Dents, Bends, or Loose Sections in Metal Coping: Wind uplift can dislodge metal coping or cause fasteners to loosen over time.
- Displaced or Missing Coping Sections: Any missing pieces must be replaced immediately to prevent water intrusion.
2. Water Damage and Sealant Failure
- Gaps or Cracks in Sealant at Coping Joints: Sealants degrade over time due to exposure to UV radiation, temperature fluctuations, and weathering. Any failed or deteriorated sealant should be removed and replaced.
- Efflorescence on Masonry Walls Below Coping : A sign that moisture is infiltrating the wall, possibly due to coping joint failure or improper slope.
- Water Stains on the Interior Side of the Parapet: Indicates that water is bypassing the coping system and affecting the interior structure.
3. Securement and Fastening
- Loose or Missing Fasteners in Metal Coping: Fasteners should be tight and in place. Any missing or corroded screws, clips, or cleats should be replaced.
- Warped or Buckled Coping Sections: Metal coping can expand and contract with temperature changes, leading to deformation and loosening.
- Dislodged or Unstable Masonry Coping: Heavy masonry coping can shift over time, posing a falling hazard. Re-anchor any loose sections. This is a common issue with old terra cotta coping. During inspection, the individual pieces of terra cotta should be checked to see if they are loose or not.
4. Drainage and Flashing
- Proper Slope Toward the Roof: Coping should direct water toward the interior of the roof rather than the building exterior. Improper slope can contribute to wall damage and staining.
- Functioning Drip Edges: Check that drip edges extend beyond the wall surface and are free of obstructions.
- Flashing Integrity: Any roof flashing beneath or below coping should be securely attached and in good condition.
Maintenance Best Practices
1. Cleaning and Debris Removal
- Remove leaves, dirt, and debris that may accumulate on or around coping.
- Clear any obstructions that may interfere with drainage and water runoff.
2. Sealant and Joint Repair
- Reapply high-quality, UV-resistant sealant at coping joints and gaps where deterioration is found. Mortar may need to be removed and replaced on masonry coping systems.
- Use backer rod when sealing larger gaps to improve durability.
3. Fastening and Securement Checks
- Tighten any loose fasteners in metal coping.
- Replace missing or corroded screws, cleats, or anchors.
- Ensure masonry coping units are properly bedded in mortar or mechanically fastened.
4. Waterproofing Enhancements
- If moisture infiltration is suspected, consider installing a secondary waterproofing membrane under coping to act as a backup barrier.
- Verify that roof membranes terminating under the coping remain fully adhered and damage-free.
5. Addressing Structural Concerns
- Repair or replace coping sections that show significant damage or instability.
- If movement or shifting is detected, assess whether expansion joints are adequate or if additional thermal accommodation is necessary.