Table of Contents
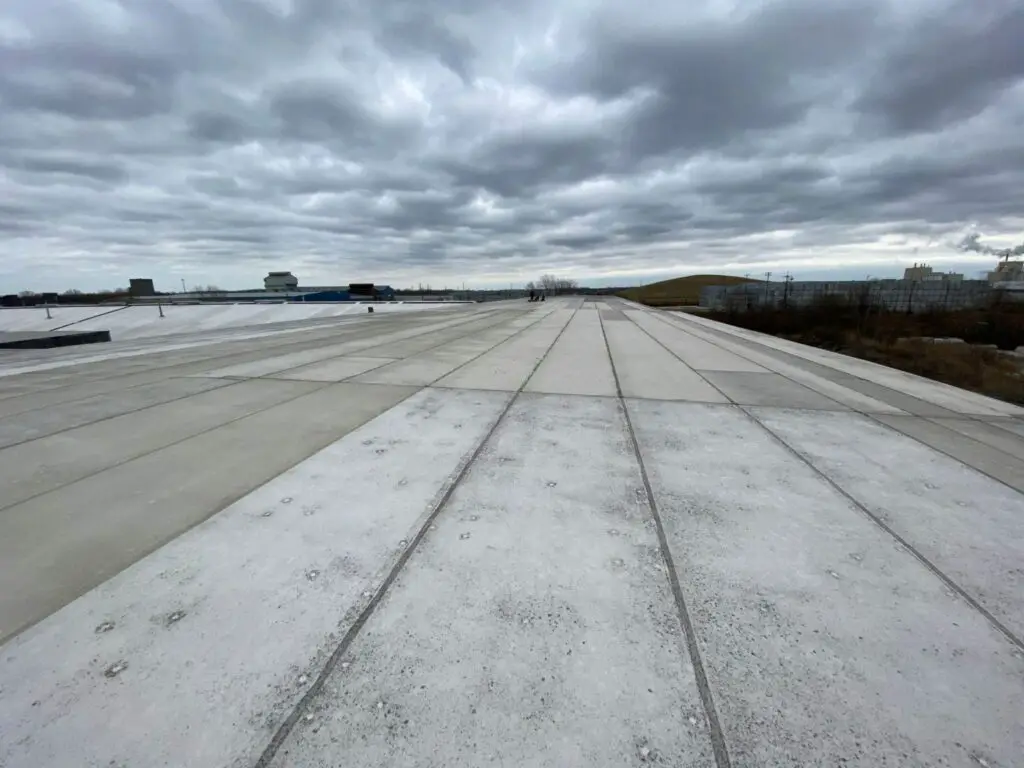
Introduction
Hypalon is a somewhat unique single-ply roofing membrane material that used to be installed on commercial low-slope roofs. “Hypalon” is a brand name used by DuPont for chlorosulfonated polyethylene (CSPE), a type of synthetic rubber; sheets of CSPE were joined together to form the finished roof membrane. CSPE roof membranes are known for their durability, heat resistance, and resistance to UV light, chemicals, and weathering.
CSPE has both thermoplastic and thermoset properties. Its thermoplastic qualities allowed for installation that did not rely on adhesives, and its thermoset properties allow it to withstand extreme temperature fluctuations, which made it a suitable roof type for buildings in areas with harsh sun and heat. Hypalon (CSPE) roofs were installed using fully-adhered, mechanically-fastened, or ballasted attachment methods.
History of Hypalon (CSPE Membrane)
Hypalon was originally developed by DuPont in the 1950s and was used as a substitute for natural rubber, which was then becoming scarce and expensive. It began to be used as a roofing membrane in the mid-1960s as a cheaper alternative to the labor-intensive built-up roofs which were prevalent at the time.
Professionals in the roofing industry soon began to promote Hypalon for its ability to resist degradation from industrial pollutants and acid rain, which meant that it performed quite well in industrial environments. It was also able to resist ponding water better EPDM roofing and far better than asphalt built-up roofing. This and the fact that roofers could repair it by heat-welding patches rather than needing to use adhesives (laps or seams that relied on adhesives tended to be weak points in single-ply roof systems) became additional selling points.
Although Hypalon never achieved the popularity of EPDM roofing, which was its main competitor in the single-ply roofing niche during the 70s and 80s, it did gain a respectable market share, and was considered an excellent low-slope roofing option for around 40 years. Despite its strengths and a mildly devoted contractor fan base, DuPont officially discontinued the production of Hypalon in 2009, marking the end of its availability for new roof installations.
Reasons for Ending Production
DuPont discontinued the production of Hypalon in 2009 due to a combination of environmental concerns, regulatory pressure, and declining demand. The key reasons for its discontinuation include:
Environmental and Regulatory Concerns
CSPE manufacturing involved the use of chlorinated and fluorinated hydrocarbons, which were coming under increasing scrutiny due to their environmental impact. The production process released hazardous byproducts, including hydrochloric acid and dioxins, which posed risks to both workers and the environment. Regulatory agencies, including the U.S. Environmental Protection Agency (EPA) and the European Union’s REACH program, were tightening restrictions on materials with high chlorine content.
Market Trends and Competition
By the 2000s, EPDM (ethylene propylene diene monomer) and TPO (thermoplastic polyolefin) roofing membranes had become dominant in the single-ply roofing market. These alternatives offered lower costs and better long-term performance, making them more attractive to contractors and building owners. EPDM manufacturers had developed new production methods that dealt with (and mostly solved) adhesive failure issues, and TPO, in particular, was rapidly gaining popularity and market share because it was white and reflective like Hypalon, it could be heat-welded like Hypalon, and it didn’t have the environmental drawbacks that Hypalon did.
Material Degradation Issues
CSPE roofs were initially praised for its UV and chemical resistance, but over the years it was found to oxidize and chalk more quickly than expected. This led to adhesion problems, especially when re-coating or performing repairs. The surface degradation made it difficult for new layers of material to properly bond, which became a maintenance and long-term performance issue.
Business Decisions
DuPont, like most companies, regularly evaluates its product lines based on profitability and market viability. With declining sales and increasing regulatory costs, the company chose to phase out Hypalon rather than invest in reformulating the product to meet stricter environmental standards.
Material Properties of Hypalon Roofing
Freshly-manufactured CSPE is a thermoplastic material. When a Hypalon roof is installed, the membrane sheets are typically heat-welded together, the same way that TPO or PVC roofing is. This welding process creates a monolithic, watertight roof membrane with outstanding seam performance, particularly on roofs where ponding water is a concern.
An interesting fact about CSPE roofing is that the material is somewhat unique in that it is thermoplastic when new (and being installed) but it loses this quality over time, and eventually becomes a thermoset material. This process takes around 5 – 10 years. After this period, the roof can no longer be repaired by heat-welding patches onto the roof; repair materials need to be applied using adhesives.
This aging process is due to cross-linking of the polymer chains, which occurs as a result of prolonged exposure to UV radiation and oxygen. While this transformation enhances the material’s overall durability, it also means that repairs will require specialized adhesives or coatings to ensure adhesion to the aged surface.
Some of the attractive qualities of CSPE roofing include its exceptional chemical resistance, its ability to withstand extreme temperatures, its fire resistance, and its flexibility, which allows it to move and expand with the building structure. Hypalon roofing is also known for its high tensile strength and elongation, which helps to prevent cracking and tearing over time. Its resistance to ozone and industrial pollutants also makes it particularly well-suited for urban and industrial environments, where exposure to harsh airborne chemicals can degrade other roofing materials more rapidly.
Even though production stopped years ago, many Hypalon roofs remain in service today, thanks to their long lifespan and ability to endure extreme environmental conditions.
Hypalon Roof Lifespan
The useful service life of a Hypalon roof typically ranges from 25 to 35 years, depending on factors such as the workmanship quality of the installation, the quality of long-term roof maintenance, local climate, and exposure to environmental stressors. Some well-maintained Hypalon roofs have even lasted 40 years or more.
Factors Affecting Hypalon Roof Lifespan:
UV and Weather Resistance:
- A CSPE membrane’s strong resistance to ultraviolet (UV) radiation helps it maintain structural integrity longer than many other single-ply membranes.
- However, surface chalking and oxidation can occur over time, which may impact long-term performance if not properly managed.
Chemical and Pollution Resistance:
- Hypalon is highly resistant to industrial pollutants, acids, and harsh chemicals, making it suitable for urban and industrial environments.
- Unlike some other roofing membranes, CSPE does not easily degrade when exposed to petroleum products or chemical runoff.
Physical Durability:
- It has high tensile strength and elongation properties, meaning it can expand and contract with temperature changes without cracking or tearing.
- Puncture resistance is superior to some thermoplastic membranes like TPO.
Installation and Maintenance:
- A properly installed Hypalon roof with properly-made heat-welded seams will last longer than one with poorly executed seams.
- Regular inspections and maintenance (such as cleaning, applying coatings, and repairing minor damage) significantly extend its lifespan.
Aging Process:
- Hypalon begins as a thermoplastic material, allowing for heat-welded seams at installation.
- Over five to ten years, it cross-links into a thermoset material, making repairs more challenging as it loses its ability to be heat-welded.
- Repairs after this point require special primers, patches that use adhesives, or liquid-applied coatings.
Real-World Performance:
- Many Hypalon roofs installed in the 1970s and 1980s were still functional well into the 2000s with proper maintenance.
- Failures typically occur due to neglect, improper repairs, or severe mechanical damage rather than material breakdown.
A well-maintained Hypalon roof can last 30+ years, making it one of the more durable single-ply roofing options. While DuPont discontinued Hypalon in 2009, many Hypalon roofs remain in service today, often requiring specialized coatings and adhesives for repairs as they age.
Coatings for Hypalon Roofs
Coating a Hypalon roof in order to extend its life may or may not work. That being said, maintaining and attempting to extend the lifespan of Hypalon roof systems is often done by applying a roof coating to the surface of the roof. These coatings help restore the roof’s appearance, and may also help it last longer by protecting it from UV rays and other environmental factors.
Many roof coating manufacturers have developed coatings marketed for use on Hypalon roofs. The use of a specialty primer will likely be required, so keep that in mind.
There are several good reasons why a roof coating may not be appropriate for a roof system, no matter what the coating salesman might tell you. You should have an independent professional roof consultant assess your roof before spending that much money on something that has a significant chance of providing you with little value at all.
Types of Coatings Suitable for Hypalon Roofs:
(See my article on roof coatings for more on roofing coating types and suitable applications.)
SEBS (Styrene-Ethylene-Butylene-Styrene) Coatings:
SEBS coatings are known for their excellent adhesion, flexibility, and durability. They provide a seamless, waterproof barrier that protects against UV radiation and weathering.
Silicone Coatings:
Silicone coatings offer superior UV resistance, flexibility, and the ability to withstand ponding water. They form a durable, seamless membrane that does well under extreme temperatures.
Important Note: Existing silicone coatings are an unsuitable substrate for most other types of roof coating. Always verify with the manufacturer before trying to stick any other type of product to silicone.
Acrylic Coatings:
Acrylic coatings are water-based, so application and cleanup is fairly easy. They tend to be the cheapest type of roof coating, and they can provide good reflectivity and UV protection, which helps to reduce roof temperatures and thermal stress. On the other hand, they tend to fail sooner than most other types of coating, so you have to take that into account.
Coating Application Considerations:
- Surface Preparation: Ensure the roof surface is clean, dry, and free of contaminants. It’s important that you remove the chalky residue from the surface of a Hypalon roof before applying a coating to ensure proper adhesion. Power washing and the use of appropriate cleaners are recommended.
- Weather Conditions: Apply coatings under suitable weather conditions, typically when temperatures are between 50°F and 100°F, and avoid application if rain is expected within 24 hours.
- Professional Assessment: It’s a good idea to consult a professional roof consultant before applying a roof coating to assess the condition of the Hypalon roof and determine the proper course of action.
Conclusion
Hypalon roofing was once a fairly popular choice for low-slope roofs due to its durability, chemical resistance, and long lifespan, which often exceeded (exceeds?) 30 years with proper maintenance. While DuPont discontinued Hypalon (CSPE) roof membrane in 2009, many existing Hypalon roofs still remain in service today.
Building owners or property managers responsible for an aging Hypalon roof should have annual professional roof inspections and preventative maintenance performed. You need to do this if you want to try to maximize the roof’s service life.