I participate in the Amazon affiliate program and may earn commissions from purchases made through links on this page.
Table of Contents
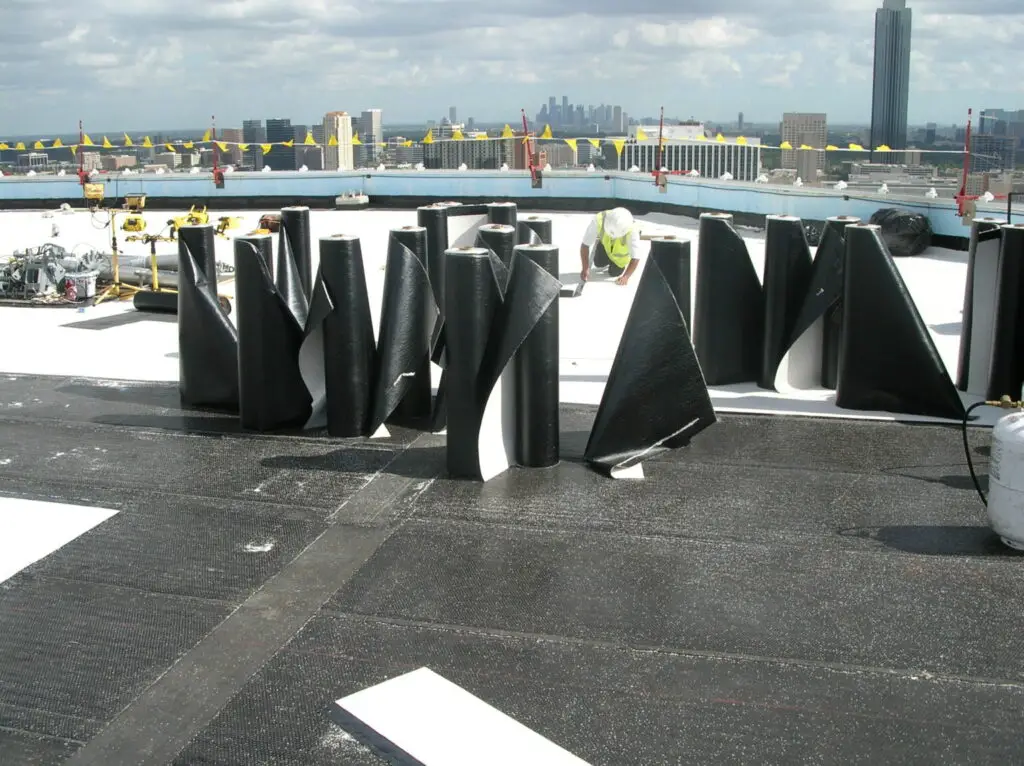
Introduction
The slope of your roof affects how well it sheds rain, snow, and debris, and determines what types of roofing materials are appropriate and allowed by the building code. This article explains what the minimum roof pitch is for modified bitumen roofing, a high-performance, multi-layer system commonly used on low-slope residential and commercial roofs.
Note: Pitch and slope are not technically the same thing, but I’ll be using the terms interchangeably here. The building code uses “slope.”
Modified bitumen is an asphalt-based roofing material that’s been enhanced with plastic or rubber polymers to improve elasticity, flexibility, and weather resistance. It’s applied in multiple layers (typically two plies, sometimes three) using heat-welding (propane torch), fluid adhesive, or peel-and-stick methods, and it is specifically engineered for low-slope roofs. Unlike traditional roll roofing, which is a single-ply material with limited water resistance, modified bitumen creates a watertight membrane that can perform reliably even under marginal drainage conditions.
Modified bitumen is not the same thing as roll roofing, despite some similarities. Roll roofing is cheaper and easier to install, but roll roofing is not designed for long-term performance or for slopes below 1:12. Modified bitumen systems are also very different from single-ply membrane systems (like TPO, PVC, or EPDM), which are installed as single sheets and typically used on commercial flat roofs. And unlike asphalt shingles, modified bitumen is fully waterproof, not just water-shedding.
See my article on roll roofing for a better understanding of how it compares, and check out my other article on single-ply membranes if you’re trying to choose the best system for a “flat” or low-slope roof.
If you aren’t sure what your roof pitch is, you can get a very cheap, very accurate slope finder from Amazon. I have one of these and it works pretty well.
Minimum Allowed Roof Slope for Modified Bitumen Roofing
According to both the International Residential Code (IRC) and the International Building Code (IBC), modified bitumen roofing can be installed on roofs with a slope of ¼:12 or greater. This means the roof must rise at least ¼-inch for every 12 inches of horizontal run. A ¼-in-12 slope can also be expressed as a 1.2° slope or a 2% slope. This is the lowest roof slope permitted by code for any type of low-slope roof, unless you’re using coal-tar pitch roofing (which you almost certainly are not) which is allowed on slopes as low as ⅛-in-12. While ¼:12 is a very low slope, modified bitumen roofs, like all low-slope materials mentioned in the code, still require some positive drainage to avoid ponding water and other issues.

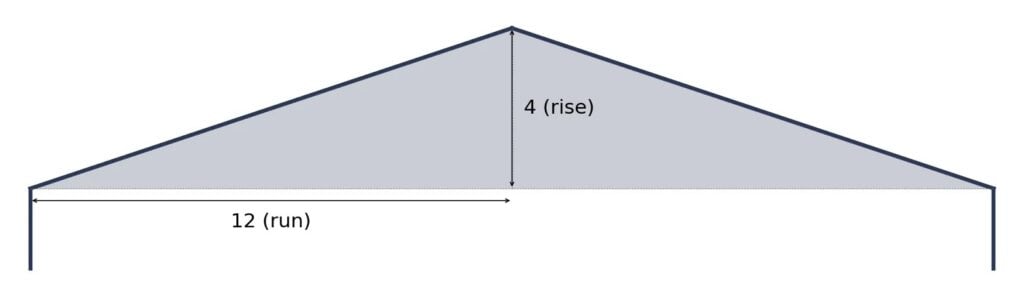
Modified bitumen roofing is designed to reasonably resist standing water, long-term UV exposure, and mechanical damage, as well as accommodate thermal expansion and contraction. When installed properly, it provides one of the most durable roofs for low-slope applications. Like any roofing system, it must be installed at or above the minimum allowed slope in order to perform properly and pass inspection.
Section R905.11.1 of the 2024 IRC and Section 1507.11.1 of the 2024 IBC both state that modified bitumen roofing must have a design slope of not less than ¼:12 (or 2%) for drainage.
It’s important to understand that a ¼-in-12 slope is not truly flat. Even so-called flat roofs are actually low-slope roofs designed with just enough slope to move water toward drains or scuppers. Modified bitumen is suitable for these kinds of applications precisely because it forms a fully-adhered, watertight barrier capable of resisting ponding and hydrostatic pressure.
While the code permits installation at ¼-in-12, it’s a good idea to install modified bitumen on slightly steeper slopes if that’s possible. Roofs with a slope of ½-in-12 or more allow water to drain more quickly and avoid the significant deterioration that asphalt can experience due to chronic exposure to standing water. This enhances the performance and longevity of the system.
On the other hand, modified bitumen is generally not used on steep-slope roofs (typically anything steeper than 3:12). On steeper slopes, adhesion/attachment becomes more challenging, seams are more exposed to runoff forces, and aesthetics or the configuration and ventilation needs of the underlying structure often make steep-slope systems like shingles or metal panels more appropriate. If your roof is steeper than 4:12, it is usually better to choose a roofing system designed for water-shedding rather than waterproofing.
¼-in-12 is the minimum allowed, not the optimal roof pitch for modified bitumen roofing.
Code Sections: Minimum Roof Slope
From the 2024 International Residential Code, here’s the section that dictates acceptable roof slope for modified bitumen roofing:
Modified bitumen roofing shall have a design slope of not less than one-fourth unit vertical in 12 units horizontal (2-percent slope) for drainage.
And here’s the equivalent section from the 2024 International Building Code:
Modified bitumen roofing shall have a design slope of not less than 1/4 unit vertical in 12 units horizontal (2-percent slope) for drainage.
Components of a Modified Bitumen Roof Assembly
A typical modified bitumen roof is a multi-layered roof assembly. It generally includes:
Structural Roof Deck: The foundation of the system, made of wood, steel, or concrete. It must be dry, clean, and structurally sound to support the roofing layers.
Vapor Retarder (if required): Installed over the deck in certain climates or building conditions to limit moisture migration from the interior into the roofing system.
Thermal Insulation: Positioned above the vapor retarder, insulation improves energy efficiency and thermal performance. Common materials include polyisocyanurate, XPS, or perlite board. The thickness of the insulation layer is determined by the type of insulation material and the R-value required by the local code.
Cover Board: A rigid board, usually gypsum board with a specialty facer, installed over the insulation to protect it from foot traffic, hail, and the heat or adhesives used to attach the mod bit base sheet. The cover board also improves fire resistance and creates a smooth surface for the membrane.
Modified Bitumen Base Sheet: This is the first ply of the waterproofing membrane and is installed as a layer of overlapping rolls of modified bitumen. It may be adhered, mechanically fastened, or self-adhering, depending on the system design.
Modified Bitumen Cap Sheet: This is the second ply and serves as the primary waterproofing and UV-resistant layer. It is similar to the base ply, but it’s surfaced with embedded mineral granules or a factory-applied reflective coating. Cap sheets are typically installed by torching, cold adhesive, or peel-and-stick methods.
Together, the base and cap sheets form a two-ply system, offering redundancy, strength, and above-average durability for a low-slope roof. Three-ply system are also used.