I participate in the Amazon affiliate program and may earn commissions from purchases made through links on this page.
Table of Contents
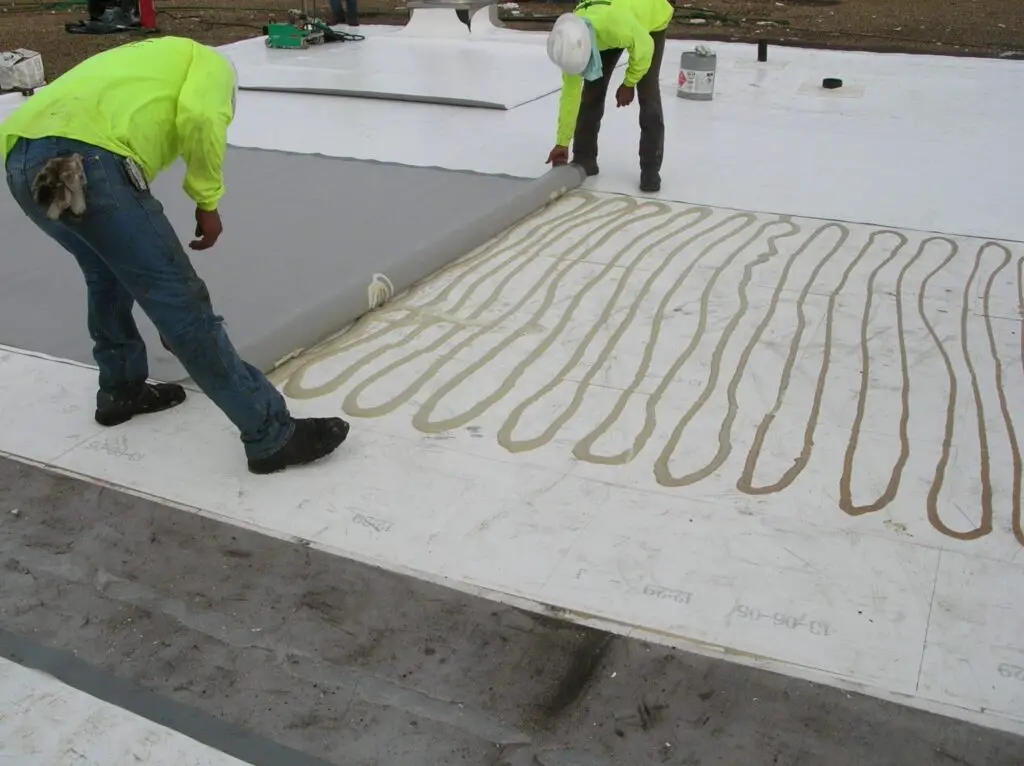
Introduction
The slope of your roof affects how well it sheds rain, snow, and debris, and determines which roofing materials are appropriate and code-compliant. This article explains the minimum roof pitch for single-ply membrane roofing systems, including EPDM, PVC, and TPO (the most common types of single-ply roofing used on residential and commercial low-slope roofs).
Note: Pitch and slope are not technically the same thing, but I’ll be using the terms interchangeably here. The building code uses “slope.”
Single-ply roofing refers to a class of flexible membrane systems installed as large sheets seamed together to form a continuous waterproof barrier. These membranes are engineered for low-slope roof applications and are designed to resist ponding water, UV exposure, and thermal expansion. Single-ply membranes are made from synthetic compounds like EPDM (rubber), TPO (thermoplastic polyolefin), and PVC (polyvinyl chloride).
Single-ply membranes are cheaper and easier to install than other low-slope systems like modified bitumen or built-up roofing. These membranes can be fully adhered, mechanically fastened, or ballasted and are used on approximately 75% of the low-slope roofs in North America. Read more about single-ply roofing.
If you aren’t sure what your roof pitch is, you can get a very cheap, very accurate slope finder from Amazon. I have one of these and it works pretty well.
Minimum Allowed Roof Slope for Single-Ply Roofing
According to Section R905.12.1 of the International Residential Code (IRC) and Section 1507.12.1 of the International Building Code (IBC), single-ply roofing systems, including EPDM, PVC, and TPO, must be installed on roofs with a slope of ¼:12 or greater. This means the roof must rise at least ¼ inch for every 12 inches of horizontal run. A ¼:12 slope can also be expressed as 2% or 1.193°. This slope is required to ensure proper drainage and to prevent water from ponding on the membrane surface.

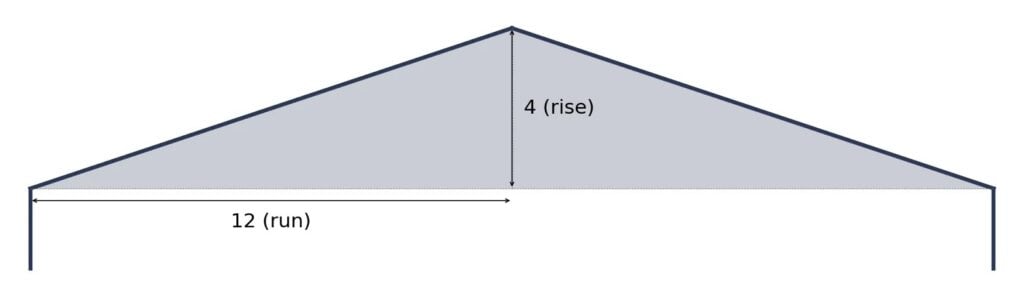
This is the lowest roof slope permitted by code for any type of roof, unless you’re using coal-tar pitch roofing (which you almost certainly are not) which is allowed on slopes as low as ⅛-in-12. While ¼:12 is a very low slope, it is not actually flat. All low-slope materials mentioned in the code still require some slope so water can drain off the roof.
EPDM, PVC, and TPO membranes are not designed to sit under standing water for prolonged periods. Ponding water can accelerate roof deterioration. Even though ¼-in-12 is the minimum allowed slope, it can be a good idea to install single-ply membranes on roofs with a slightly steeper pitch whenever possible. A slope of ½-in-12 or more helps reduce the chance of ponding, improves drainage toward scuppers or internal drains, and can increase the life expectancy of the roof system.
It’s also worth noting that single-ply systems are not ideal for steep-slope roofs (typically steeper than 3:12). As the slope increases, membranes become harder to install and secure properly, condensation within the roof assembly may become an issue, and the aesthetics will be inappropriate for residential applications. On steeper roofs, materials like standing seam metal or shingles are a better choice.
Code Sections: Minimum Roof Slope
From the 2024 International Residential Code, here’s the section that dictates acceptable roof slope for single-ply roofing:
Single-ply membrane roof coverings shall have a design slope of not less than ¼ unit vertical in 12 units horizontal (2-percent slope) for drainage.
And here’s the equivalent section from the 2024 International Building Code:
Single-ply membrane roof coverings shall have a design slope of not less than ¼ unit vertical in 12 units horizontal (2-percent slope) for drainage.
Components of a Single-Ply Roof Assembly
Single-ply roof assemblies are designed for low-slope roofs and actually consist of a few different layers. A typical single-ply assembly includes the following components:
Structural Roof Deck:
The base of the system, usually made of wood, steel, or concrete. The deck must be structurally sound, dry, and clean to properly support the roofing system.
Vapor Barrier (if required):
Used in climates or building conditions where interior moisture control is necessary. This layer limits vapor migration from the building interior into the roofing system.
Thermal Insulation:
Installed above the vapor barrier (if present) or directly over the deck. Common insulation types include polyisocyanurate, extruded polystyrene (XPS), or expanded polystyrene (EPS). The thickness of the insulation layer will depend on the R-value required by the local code.
Cover Board:
A hard, smooth layer of thin boards, typically gypsum or high-density polyisocyanurate, installed over the insulation. It provides protection from foot traffic and hail, improves fire resistance, and offers a suitable substrate for adhering the membrane.
Single-Ply Membrane (typically EPDM, TPO, or PVC):
This is the primary waterproofing layer. The material comes in very large rolls. The sheets are seamed together to create a single ply which forms a waterproof barrier on the surface of the roof.
- EPDM is a flexible synthetic rubber membrane, usually black.
- TPO and PVC are thermoplastic membranes commonly available in white, gray, and tan.
Depending on the membrane type, attachment methods include fully adhered, mechanically fastened, or ballasted systems. Thermoplastics (TPO and PVC) are heat-welded at the seams, while EPDM seams are formed using seam tape or adhesives.
When properly designed and installed, single-ply systems can provide long-term performance with a lower cost and faster installation than built-up or modified bitumen systems.