Table of Contents
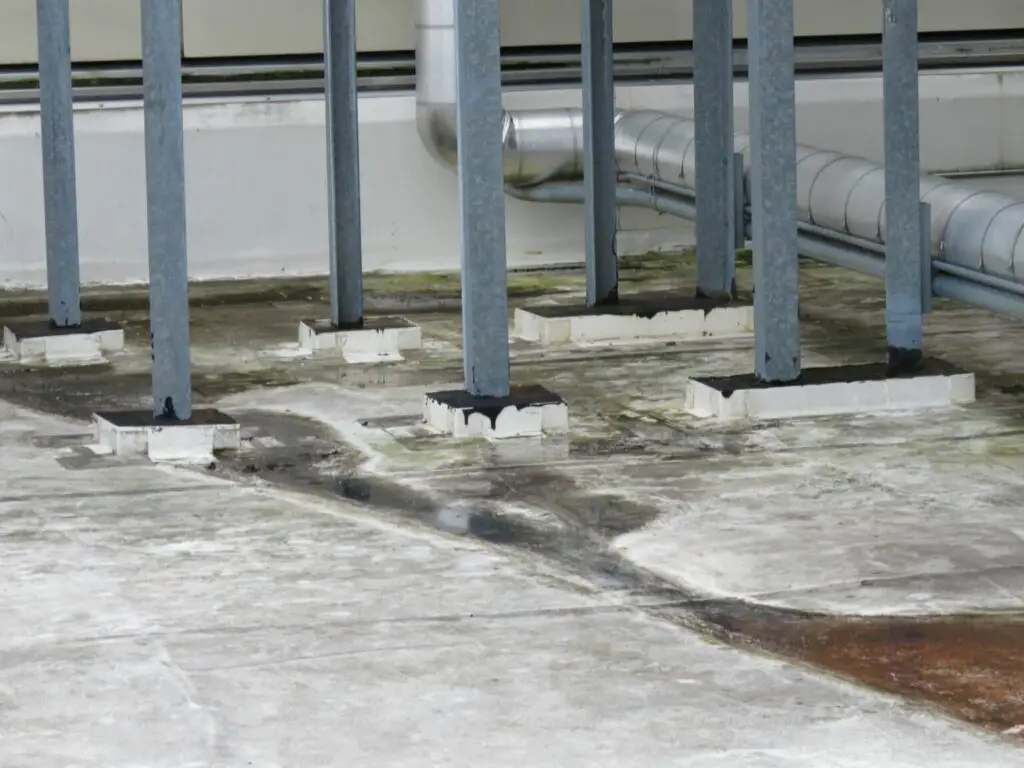
Introduction
A pitch pocket (or pitch pan) is a type of roof flashing used to seal small or irregular roof penetrations. Pitch pans are very common on low-slope roofs. Pitch pockets look like boxes, rings, or cylinders made out of sheet metal (normally galvanized steel) or a pre-molded polymer. Although they are usually open at the top, some specifiers require pitch pockets to have caps or covers on them for added weather protection.
Pitch pockets function as containers for the relatively large amount of sealant required to seal these small or irregular roof penetrations.
Pitch pockets are also called pitch pans, penetration pockets, pitch boxes, or sealant pockets. “Pitch pocket” and “pitch pan” are by far the most common terms used to refer to this particular type of roof flashing, and the use of one name or the other by roofers typically depends on what geographical region you’re in.
I am going to use “pitch pan” and “pitch pocket” interchangeably in this article.
Pitch Pockets: History & Name
Pitch pockets, or pitch pans, are called that because they originally held actual pitch in place around penetrations to keep them watertight. The original waterproofing pitch was a resin derived from the sap of pine trees that was widely used in shipbuilding and maintenance. Bitumen from asphalt deposits near the earth’s surface was also used where available. Pine pitch was replaced by coal tar pitch, a by-product of industrial coal processing (coke production for steel manufacturing), in the middle of the 19th century.
Coal tar pitch was the main waterproofing material in the flat roof industry for around a century, from the 1860’s to the 1960’s. It was particularly valued for its adhesive quality and truly excellent waterproofing properties, as well as its ability to provide a flexible seal in a variety of climate and temperature conditions. During this period, pitch pockets became a common solution for sealing roof penetrations such as pipes, conduits, or other irregularly shaped objects passing through the roof surface.
After asphalt began to compete with and eventually replace coal tar pitch as a built-up roofing material in the 20th century, asphaltic mastic became the most common filler for pitch pans. It is still often used today in pitch pockets on asphalt built-up or modified bitumen roofs.
With the dominance of single-ply membrane roofs in today’s roofing industry, pitch pockets are typically filled with modern sealants, such as polymer-based elastomeric compounds like polyurethane, which offer improved resistance to ultraviolet radiation, temperature extremes, and general weathering.
So that’s why pitch pans are called “pitch pans”, even though actual pitch is almost never used any more.
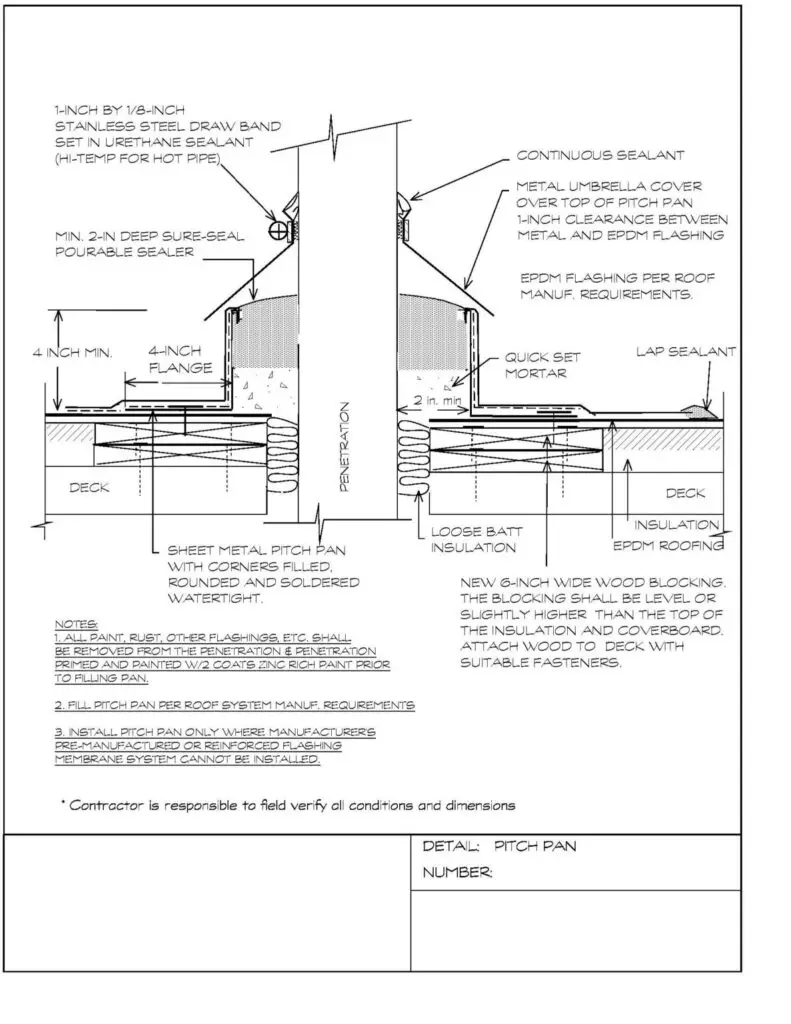
Why Pitch Pockets Are Necessary
A typical roof penetration, such as one for a round vent stack, is usually flashed with a prefabricated boot, sheet metal stack flashing, or a lead sleeve. Large straight-sided penetrations on single-ply roofs can be flashed by installing regular flexible membrane flashings using adhesive.
These options are effective for standard penetrations because they create a tight, reliable seal without relying heavily on sealants to remain leak-free. These other methods work well for round, uniform, or straight-sided penetrations, but they are not suitable for every situation.
Pitch pockets are very useful when dealing with challenging roof penetrations that are difficult or impossible to flash using other methods. For example:
- Small Penetrations: Penetrations required by electrical conduits, small piping, or antenna mounts are often too small for prefabricated pipe boots. Pitch pockets can be custom-sized to fit these small openings, ensuring a proper seal.
- Irregular Shapes: Roof penetrations with irregular or non-circular shapes, such as I-beam supports or brackets, present a challenge. Typical flashing materials are not flexible enough to conform to these shapes, making pitch pockets a practical solution.
- Clusters of Penetrations: When multiple penetrations are located close together, such as in areas with grouped electrical conduits or multiple small pipes, individual flashings for each penetration may not be feasible, simply because there isn’t enough room. A single pitch pocket can encompass all the penetrations within a shared sealant reservoir, simplifying the flashing process while providing effective waterproofing.
Additionally, pitch pockets filled with elastomeric sealant can typically accommodate movement or vibration at certain penetrations, such as mechanical equipment supports, by allowing the flexible sealant inside the pocket to absorb the motion.
While not ideal for all applications, the pitch pan’s design compatibility with complex penetrations makes them a useful tool in the roofer’s repertoire.
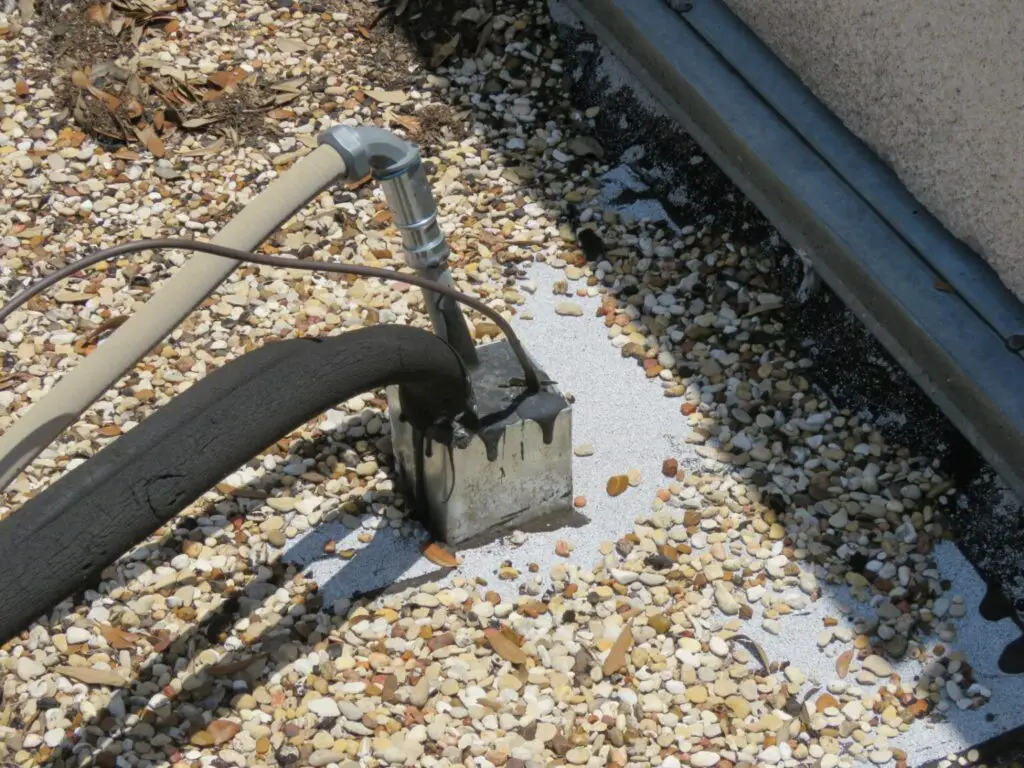
Problems with Pitch Pockets
Pitch pockets are well-known for being a frequent source of roof leaks. Their reliance on sealant for waterproofing creates vulnerabilities in a roof system, as sealant is inherently subject to degradation. Over time, the sealant within a pitch pocket can shrink, harden, or crack due to exposure to ultraviolet radiation, temperature fluctuations, and weathering. This natural aging process reduces the pitch pan’s effectiveness, and can eventually allow water infiltration through the penetration.
This is a very common issue on asphalt roofs when the pitch pan is filled with asphalt roof cement. Asphalt roof cement is cheap and highly compatible with other asphalt-based materials, but it’s particularly prone to shrinking and cracking as it ages, especially under prolonged exposure to heat and UV rays.
Asphalt’s increasing brittleness over time makes it less capable of maintaining a watertight seal, particularly in cases where the roof penetration is subject to movement or vibration. Asphalt-based materials are less flexible than modern elastomeric sealants, but many polymeric sealants are not fully compatible with asphalt roofing. So roof cement remains in use and should be treated as a priority maintenance item.
Another issue with pitch pans is that the seal can break when the item being flashed by the pitch pocket moves or shifts. For example, equipment supports, conduits, or pipes may vibrate due to wind or operational activity, with the seal between the penetration item and the pitch pocket fill gradually deteriorating. As the sealant ages and loses flexibility, it becomes less able to accommodate movement, further increasing the likelihood of leaks.
The physical design of metal pitch pans can also contribute to their problems. The relatively small flange commonly found on metal pitch pockets makes it non-trivial to achieve a robust tie-in with the roof membrane. A proper tie-in relies on stripping, which is a layer of roofing material that sandwiches the flange of the pitch pocket between the stripping and the surface of the roof system. If this stripping is improperly applied, fails to adhere, or degrades over time, the seal between the pitch pocket and the roof membrane can become compromised, allowing water penetration under the flange.
Any ponding water around pitch pockets can exacerbate these issues. Poor drainage or roof design that allows water to pool around the pitch pocket increases the risk that the bond between the pitch pan and the surface of the roof will fail. Really severe ponding may actually submerge the pitch pan and facilitate failure of the sealant in the pitch pan itself.
A concave surface created by an underfilled pitch pocket can also hold rainwater, which is not desirable.
For all these reasons, pitch pockets are often considered a solution of last resort in roofing design. When they must be used, proper installation, regular maintenance, and the selection of high-quality, UV-resistant sealants are essential to mitigate common problems.
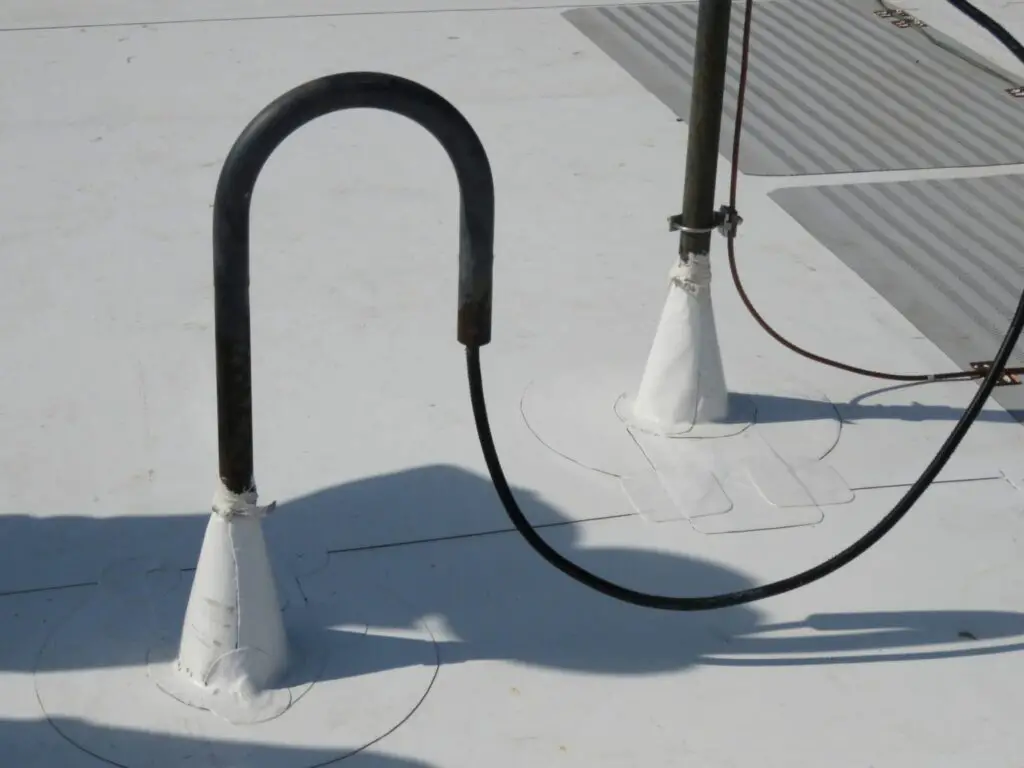
Alternatives to Pitch Pockets
There are several alternatives that provide more reliable, long-term solutions for sealing penetrations:
1. Pre-Molded Pipe Boots
- Description: Flexible boots made from materials like rubber, silicone, or thermoplastic that fit snugly around round or uniformly shaped penetrations such as pipes or conduits.
- Advantages:
- Easy to install and integrate with most roofing systems.
- Provides a secure, watertight seal without relying heavily on sealants.
- Designed to accommodate movement or thermal expansion of the penetrations.
- Applications: Suitable for standard cylindrical penetrations in both steep-slope and low-slope roofs.
2. Liquid-Applied Flashing
- Description: A liquid membrane or flashing material that can be applied to roof penetrations to create a seamless, flexible, and watertight seal.
- Advantages:
- Excellent for irregularly shaped penetrations or clustered pipes.
- Bonds directly to the roof membrane and penetration, forming a single monolithic layer.
- Requires less maintenance compared to pitch pans and offers superior weather resistance.
- Applications: Ideal for complex penetrations or repairs in both low-slope and steep-slope roofs.
3. Prefabricated Flashing Assemblies
- Description: Factory-made flashing components designed for specific roof penetrations, including multi-penetration bases and custom-fit solutions.
- Advantages:
- Customizable to the specific size and shape of the penetration.
- Typically includes integrated weatherproofing features such as collars or gaskets.
- Offers consistency in quality and reduces field fabrication errors.
- Applications: Frequently used in new construction where penetration details are known in advance.
4. Metal Flashing
- Description: Custom-fabricated flashing made from materials like copper, stainless steel, or aluminum. Often paired with roof membranes for added security.
- Advantages:
- Durable and long-lasting, with excellent resistance to UV radiation and weathering.
- Provides a neat and professional appearance.
- Does not rely on sealants for primary waterproofing.
- Applications: Common for high-end or long-term roofing systems, particularly in architectural or steep-slope applications.
A gooseneck roof penetration flashing is often very good alternative to a pitch pocket. It’s less likely to leak than a pitch pocket, it won’t be a constant maintenance item, and it can accommodate flexible conduits, cables, and few other common items that require a roof penetration.
5. Mechanical Clamping Systems
- Description: Systems that use a mechanical clamp or collar around the penetration to secure it tightly and provide a waterproof seal.
- Advantages:
- Durable and resistant to movement or vibration.
- Minimal reliance on sealants, reducing maintenance requirements.
- Applications: Commonly used in industrial or commercial roofing systems.
6. Tapered Curbs
- Description: Raised, box-like structures that are designed to provide a watertight enclosure around the penetration. These are often combined with a liquid-applied or prefabricated flashing system.
- Advantages:
- Keeps water away from the base of the penetration by elevating it above the roof surface.
- Works well in areas with high water flow or ponding potential.
- Applications: Suitable for mechanical units, vents, and grouped penetrations.
While pitch pans can still be necessary for certain unique applications, these alternatives offer better long-term performance and reliability. The choice of alternative depends on the type of penetration, roof design, and environmental conditions. By opting for one of these solutions, roofers can reduce the risk of leaks, lower maintenance needs, and improve the overall durability of the roof system.
Pitch Pans and Roof Maintenance
Because of these issues, and the high risk of roof leaks developing at pitch pocket locations, you should make pitch pockets a high priority during preventative maintenance inspections. Ideally, they should all be checked twice a year. Routine inspections after severe weather events are also recommended, as high winds and heavy rain can exacerbate vulnerabilities in pitch pockets. Remember that regular maintenance not only prevents leaks but also extends the life of the roof system by addressing minor issues before they become major problems.
Pitch pans with inadequate amounts of sealant should be properly topped off immediately.
Asphalt Fill
If you have pitch pans filled with asphalt cutback (asphaltic roofing cement or “mastic”), the existing material should be cleaned with a wire brush, and new material should be packed into the pitch pocket on top of it with a trowel. Ensure that the cleaning process removes any loose or degraded material, as this will help the new layer adhere better and create a more effective seal.
Make sure that asphaltic fill is rounded on top to shed water (you can’t do this with pourable sealant). A properly shaped surface prevents water from pooling inside the pitch pan, which is important. You don’t want water to get trapped inside the pitch pocket, as prolonged contact with water accelerates the degradation of the sealant and increases the likelihood of leaks. It’s not a problem if the new roof cement overflows the box slightly, as long as the seal remains watertight and the shape facilitates water runoff.
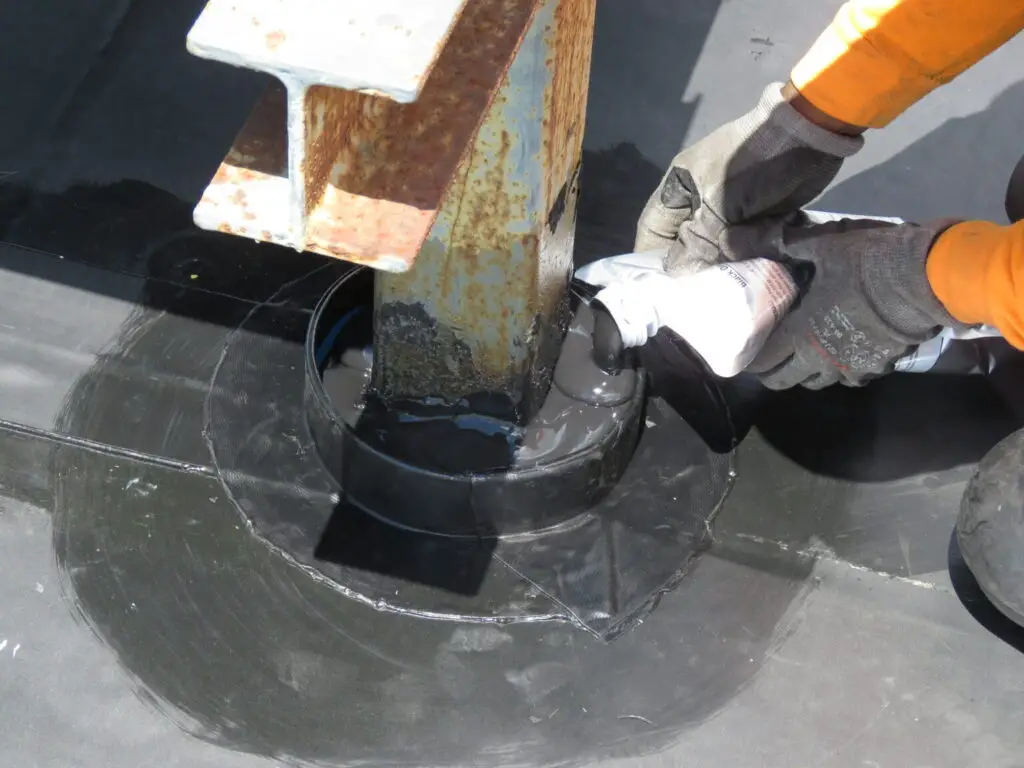
Pourable Sealant
If your pitch pocket was filled with a pourable sealant, top it off with the same kind of pourable sealant if you know what it is. If you don’t know what it is, it shouldn’t be that big of a deal. Just use any pourable sealant that advertises broad material compatibility and keep an eye on it during your maintenance inspections.
Use a wire brush to remove any debris and to scarify the surface of the old sealant for better adhesion. This step is critical for ensuring a strong bond between the old and new sealant layers. Then use water and a cloth to wipe off any remaining grit or dust. Be sure to remove all residue, as even small amounts of dirt or grease can compromise adhesion.
Wait until it’s completely dry before adding the new sealant. Moisture trapped beneath the new layer can lead to blistering, separation, or premature failure. Some roofers may use a primer specifically designed for the sealant being applied to further improve adhesion, especially in areas with extreme weather conditions.
Using Caulk
Simply caulking the tops of the pitch pans is also a bad idea, as you will not be able to achieve a proper long-lasting seal this way. Caulking is only a surface-level solution and does not address underlying issues or provide sufficient waterproofing. Properly topping off a pitch pocket requires thorough cleaning and the proper application of compatible material to ensure that the pitch pocket performs effectively over time.
Further: unless you know for certain that compatibility will not be an issue, never use silicone caulk in a pitch pocket. Silicone caulk can be incompatible with many roofing materials unless the proper primer is used. This incompatibility can result in weak bonds, leading to seal failure and water infiltration. Always verify the manufacturer’s recommendations before selecting a sealant.
Conclusion
Sometimes you have to use a pitch pocket. Sometimes it can’t be helped; a pitch pan is the only reasonable way to flash some roof penetrations. But a pitch pocket should be considered a flashing of last resort.
Sometimes a roof penetration can be avoided altogether and then you don’t need any flashing at all. At curbed HVAC units, conduit lines can often be be routed down into the building inside the curb, underneath the unit through the large hole in the roof that was cut for a duct to run through and is protected by the roof curb and the unit itself.
It’s often simply easier for the roofer to make a separate roof penetration, and that’s what he’ll do if not told otherwise, so whether this is possible or not is something that should be looked into before the work starts.