Table of Contents
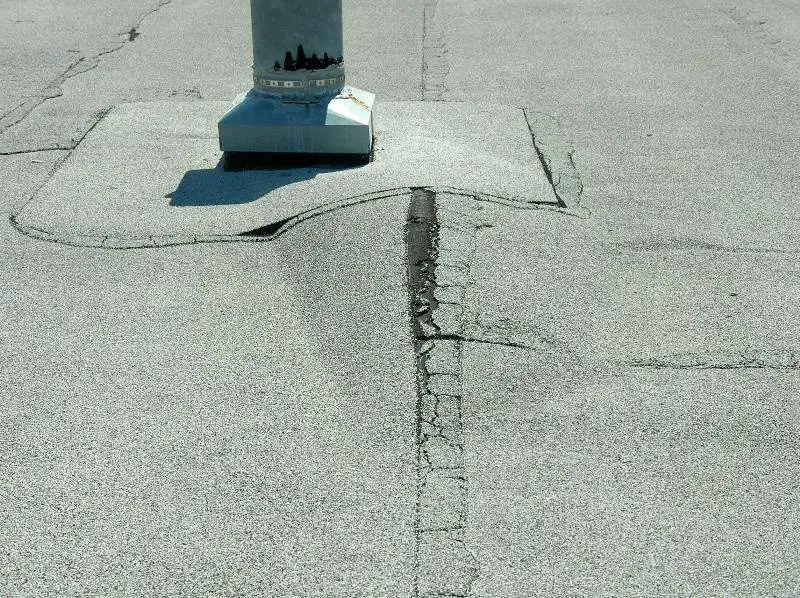
Introduction
Roof blisters are a common but often misunderstood issue in various roof systems, including built-up, modified bitumen, and asphalt shingle roofs. These raised pockets form due to trapped air, moisture, or volatile gases within the roofing materials. While some blisters remain stable and do not immediately compromise the integrity of the roof, others can lead to the loss of protective surfacing, premature deterioration, and roof leaks.
Blister formation is typically caused by installation errors, such as applying roofing materials in wet conditions or using improper adhesion techniques. Roof blisters may also form due to an overheated roof because of inadequate ventilation. In built-up and modified bitumen roofs, interply voids caused by improperly-heated asphalt, poor torching technique, or incorrect material selection can create widespread blistering soon after installation. Blistering in asphalt shingles is typically due to excessive heat retention from poor attic ventilation, leading to the expansion of trapped gases within the asphalt.
Although manufacturers and contractors may not always classify blisters as defects covered under warranties, excessive blistering – especially within the first year of installation – can indicate significant workmanship or material issues. Understanding the causes, effects, and best practices for preventing blisters can help homeowners and roofing professionals improve roof performance and extend the lifespan of a roof.
What is a Roof Blister?
A roof blister is a pocket of air, moisture, or volatile gases trapped between the plies of a built-up or modified bitumen roof membrane. In asphalt shingles, blisters usually contain trapped moisture or asphalt volatiles that may form due to overheating during manufacturing or insufficient curing of the asphalt. Poorly ventilated attics may overheat the shingles and either exacerbate manufacturing defects, or be the sole cause of blistering in non-defective shingles.
Flat roof blisters typically start as lamination voids within the system and grow larger over time due to continuous cycles of thermal expansion and contraction of the trapped gases or moisture inside the blister.
Improper installation techniques, inadequate interply adhesion, or moisture present in the roof system during application can also contribute to blister formation. Mop skips, excessive asphalt viscosity, or poorly bonded layers can create voids that develop into blisters over time. This is a particular issue when hot asphalt has cooled too much between the time it leaves the kettle and the time it’s applied.
Roof blisters will sometimes fill with water over time without causing noticeable roof leaks. This can be a serious issue if the blister is not repaired before the weather turns cold enough to cause the water in the blister to freeze and expand, splitting the roof membrane. Trapped water within blisters can expand dramatically as water vapor when heated, exerting pressure on the membrane that accelerates blister growth.
While some minor blisters may remain stable for years, larger or numerous blisters can significantly reduce the lifespan of the roof. Blisters in aggregate-surfaced membranes pose an additional concern, as the sloped edges of a blister can lead to gravel displacement, exposing the underlying bitumen to premature weathering and further UV damage.
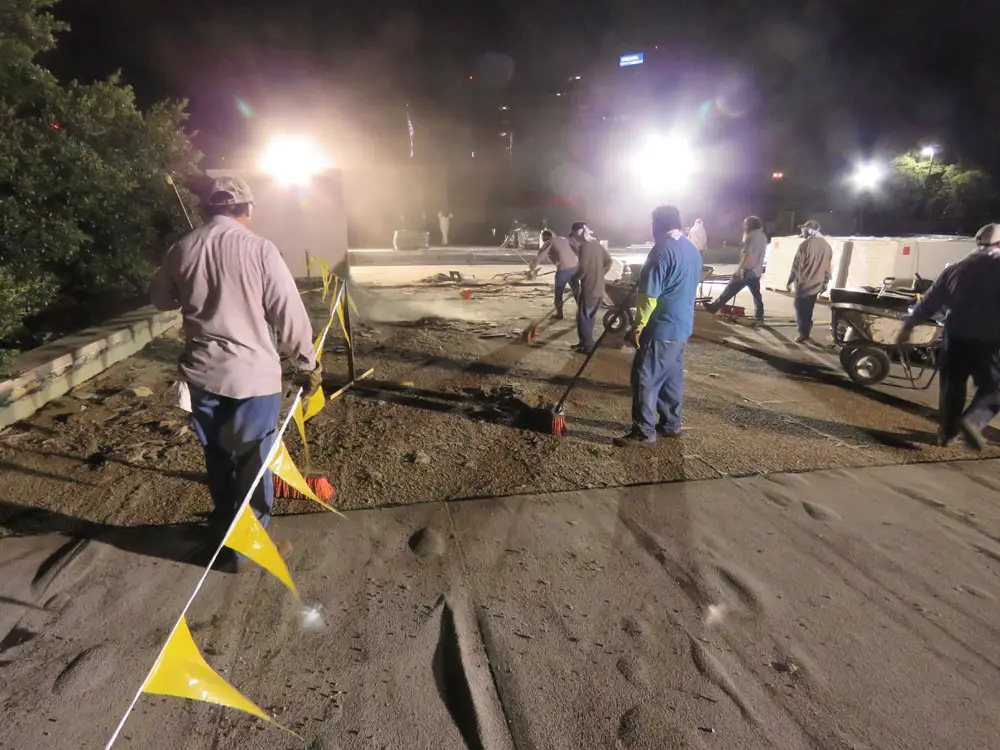
Effect of Roof Blisters on Roof Lifespan
Blisters tend to shorten the life of a roof. By stretching the surface of the roofing material, they lead to the loss of a roof’s protective granules or gravel surfacing at the blister location, which results in accelerated UV damage to the membrane or shingle. When asphalt materials are exposed to direct sunlight, they experience oxidation at a significantly faster rate, which makes them become more and more brittle as time goes by. They may crack. The process makes the affected area more vulnerable to water infiltration and premature failure.
They can also cause protective roof coatings to crack, delaminate, and fall off, removing whatever protection the coating was providing.
A roof blister in a flat (low-slope) roof system will not necessarily compromise the integrity of the roof. If the protective roof surfacing over a blister remains intact (which does sometimes happen) and the roof blister does not grow large enough to compromise roof seams, laps, or flashings, the blister can be harmless.
In many cases, small blisters remain stable for years and do not require immediate repair. However, larger or numerous blisters greatly increase the likelihood of punctures due to foot traffic or natural wear, adding to the overall deterioration of the roofing system.
Roof blisters have been known in some cases to occur within a roof system and be present for almost the entire life of the roof without causing a leak. This may happen if the blister remains small and sealed, and does not develop a hole that allows water in.
Unless a blister is the source of an active roof leak, the roofing manufacturer will not normally pay for it to be repaired under the roof warranty. The roofing contractor won’t repair it under his workmanship guarantee, either.
Manufacturers typically classify blisters as a result of installation or material handling issues rather than a defect in the roofing system itself. Contractors often exclude blisters from coverage under workmanship guarantees, as they may result from factors beyond their direct control, such as misuse or mistreatment of the roof, manufacturing defects, or building movement.
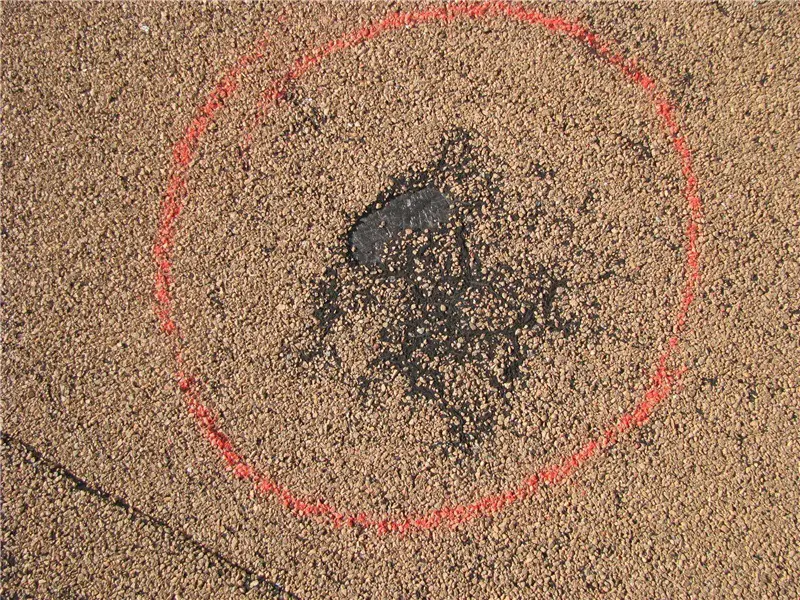
Rain During Roof Installation Causes Blisters
One very common cause of roof blistering is the installation of roofing materials while it’s raining. Even though this is forbidden by all roofing industry best practice standards, some contractors will try to maximize their rate of production by cutting it close on a day with rain in the forecast.
By waiting right until the first drops of rain start to fall before stopping, they end up with a few raindrops trapped in the system. This trapped moisture can remain within the roof assembly, leading to the formation of blisters as it heats up and expands during sunny conditions. Water between the plies of a built-up or modified bitumen roof turns into vapor when the roof is exposed to high temperatures, creating pressure that pushes the layers apart. Over time, this expansion and contraction cycle weakens the membrane.
Every trapped raindrop has the potential to turn into a roof blister. This is why you will often see blisters concentrated in one area of a roof. They got caught by the rain that day. In addition to direct exposure during installation, roofing materials that have absorbed moisture before being applied, such as felts or insulation boards stored improperly on-site, can also contribute to blister formation. When these materials are applied damp, they release their moisture within the system as the roof heats up.
Building owners should monitor all roof installation work to make sure that the roofers are not installing any roofing materials in the rain.
Blisters in Asphalt Shingles
Roof blisters in flat roof membranes are typically the result of workmanship errors during installation. This is not normally the case with asphalt shingles. Almost all blistering in asphalt shingles today is caused by improper ventilation of the roof assembly.
Poor ventilation below the roof causes the roof deck to overheat, which prevents the shingles from releasing the heat they absorb from the sun. Once the asphalt in the shingles reaches a critical temperature, the asphalt begins to release small amounts of gas. These gasses are trapped within the shingle, forming the blister. This process is known as “volatilization,” where asphalt components break down under excessive heat, generating vapors that expand inside the the shingle. As the blister grows and eventually ruptures, the protective granules are dislodged, exposing the asphalt and causing accelerated degradation.
Before modern manufacturing processes, when roofing asphalt was mixed in the factory by hand, poor quality control during production often led to roof blisters later.
Imbalances in the asphalt mix allowed gasses to form within the shingles even under normal temperatures in properly ventilated roofs. Inconsistencies in the oxidation process of asphalt during manufacturing meant that some shingles retained excessive volatiles, making them more prone to blistering once exposed to high temperatures. Damp reinforcement mats could trap moisture within the shingle, and the moisture would expand in the heat once the shingles were installed on the roof.
This isn’t the case today. Shingle manufacturing is now a finely-tuned automated process. However, asphalt shingles are still designed only to perform under expected normal temperatures, and warranties won’t cover temperatures that exceed these. Shingles installed in areas with poor attic ventilation or dark-colored shingles that absorb excessive heat are at greater risk of blistering. The combination of heat buildup and inadequate airflow beneath the deck can push the asphalt beyond its designed thermal limit.
Although they are very unlikely to cause roof leaks, blisters in asphalt shingles are unsightly and will likely shorten the overall life of the roof.
This is because the loss of granules exposes the asphalt to UV rays from the sun. UV rays break down the long hydrocarbon chains that make up asphalt. When these chains are broken, the asphalt quickly wears away. This can eventually expose the reinforcement mat in the shingle, which will absorb water, further compromising the shingle. The exposed reinforcement mat can become brittle, leading to cracks, curling, and premature failure. If left unchecked, this damage accelerates the aging of the shingle, potentially reducing the roof’s lifespan by several years.
When roof blisters in asphalt shingles are reported, the roofing manufacturer will usually insist that there are no manufacturing defects in the product. Unless the homeowner can prove that the roof is perfectly ventilated, the issue will not be covered under the manufacturer’s warranty. Manufacturers often categorize blistering as an issue of improper use conditions rather than a product defect, meaning that warranty claims are generally denied unless clear evidence of a material flaw can be demonstrated.
Homeowners, especially those with asphalt shingle roofs, should verify that they have proper attic ventilation or take steps to improve it as a preventative measure, though this will not reverse existing blisters.
You should also be aware that due to the risk of overheating the roof, some asphalt shingle manufacturers refuse to offer warranties for roofs where spray polyurethane foam insulation is applied in the attic to the underside of the roof sheathing.
Blisters in Built-Up Roofs

Blisters can form in built-up roof systems if the hot bitumen is too cool when it’s applied, if the roofers walk on the newly-installed felts, if the felts are installed with wrinkles, or if the roofers fail to broom and smooth the felts after placing them in the asphalt or coal tar pitch.
Other factors contributing to blister formation include moisture trapped within the plies at the time of installation, improper adhesion due to accidental mop skips, or insufficient bitumen during application. If an interply void exists, heat from the sun can cause any moisture or air inside to expand, leading to blister growth over time.
It’s very common to see a few blisters in a built-up roof. The number will increase as time goes by, and it’s a fairly normal part of the aging process. Most built-up membranes develop minor blisters, particularly in regions with high heat and humidity, where expansion and contraction cycles are more extreme. If the blisters remain small and the membrane maintains its overall integrity, they are usually not a cause for immediate concern. They will probably never lead to a roof leak before the roof itself reaches the end of its design life and needs to be replaced.
But they should never be stepped on. You don’t want to pop them. That would put an actual hole in your roof membrane. Blisters are particularly vulnerable to rupture during cold weather when foot traffic, snow loads, or equipment pressure can cause them to crack open. After that, water infiltration can lead to rapid membrane failure in that part of the roof. Any open blisters should be repaired immediately.
If a large number of blisters appear within a year of installation, however, you probably have a good claim against the contractor’s workmanship guarantee. You should ask a roof consultant to take a look and prepare a report. Blisters that form shortly after installation often indicate poor workmanship, improper material storage, or application errors. A professional inspection can determine if the blisters resulted from trapped moisture, inadequate bitumen application, or interply adhesion failures, which could justify a warranty claim.
Blisters in Modified Bitumen Roofs
Some modified bitumen roof systems are installed in a layer of hot liquid asphalt. The asphalt is heated on-site in a kettle and applied to the roof with mops just like in built-up roofing. This is a common installation technique, it’s quick and cheap, and I personally don’t like this method precisely because of how often I’ve seen widespread blistering develop in these roofs.
There are two main types of modified bitumen roofing, SBS-modified and APP-modified. Only the SBS-modified bitumen can be hot-mopped. The APP-modified bitumen will not melt and bond reliably when hot-mopped. Use of APP-modified bitumen with the hot-mop application method by careless contractors will almost certainly result in unbonded areas within the roof system. This means roof blisters. APP-modified bitumen is designed for torch applications, where the heat activates the asphalt to create a strong bond. When applied incorrectly with hot asphalt, the material remains unadhered, leading to interply separation and blistering.
Another issue, even with SBS-modified bitumen, is that the roofers are often unable to get the modified bitumen rolls set into the hot asphalt before the hot asphalt cools too much to be able to melt the asphalt in the modified bitumen roll. Then the asphalt in the modified sheet doesn’t bond properly with the hot-mopped asphalt from the kettle, and you end up with voids in the system.
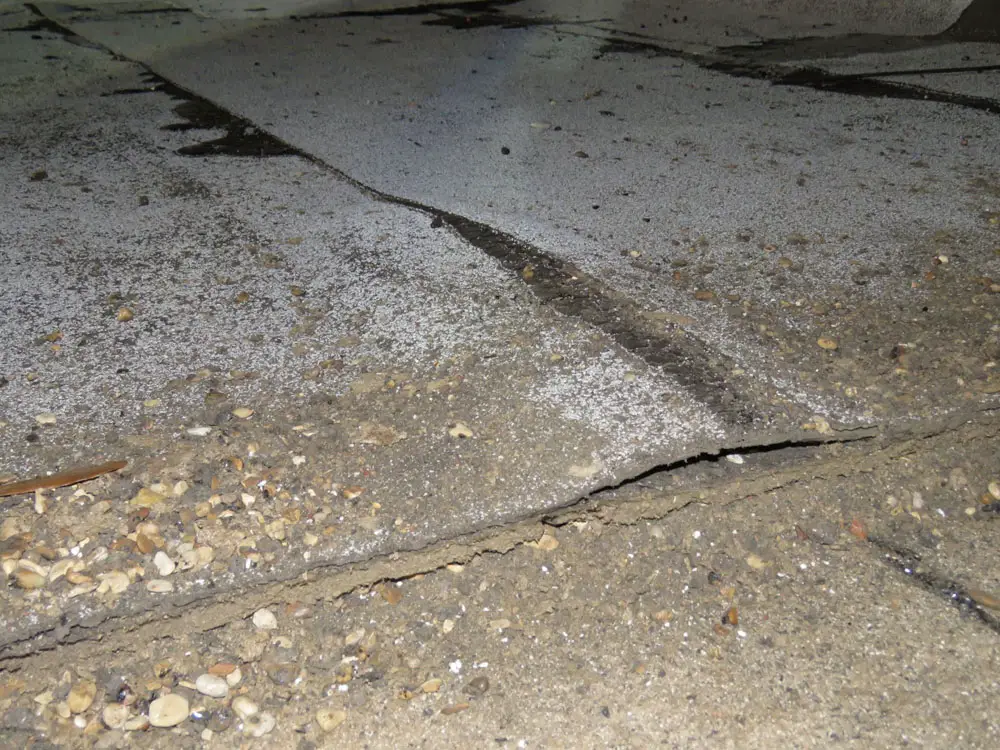
Again, this means roof blisters. In fact, if this is an ongoing issue during the installation, it can lead to an extremely large number of blisters forming throughout the roof soon after installation. In extreme cases, a poorly installed modified bitumen roof may experience systemic blistering within months, requiring extensive repairs or even premature replacement. Torch-applied systems do better, but occasionally you’ll see long (10 – 30 feet) blisters along a single roll of mod-bit. These blisters are due to a problem with one of the torch heads on the torch wagon during installation.
Say you have five torch heads melting the asphalt on the bottom of a roll of modified bitumen as it’s being rolled into place. If one of them is partially clogged and not putting out enough heat, you end up with a strip of unmelted asphalt with no bond between the roof plies there. This localized failure in adhesion creates a long, continuous blister along that line.
If the blisters in a modified bitumen roof do not cross the laps between the rolls (see the picture at the top of the page), manufacturers will say that the blisters are not an issue, that they do not compromise the integrity of the roof, and will not normally repair them under their warranty. Most manufacturers consider blisters that do not disrupt seams or flashings as cosmetic issues rather than functional defects. These blisters may still rupture (due to people stepping on them, for instance). If that happens, you’ve got a problem, and you’re responsible for it.