Table of Contents
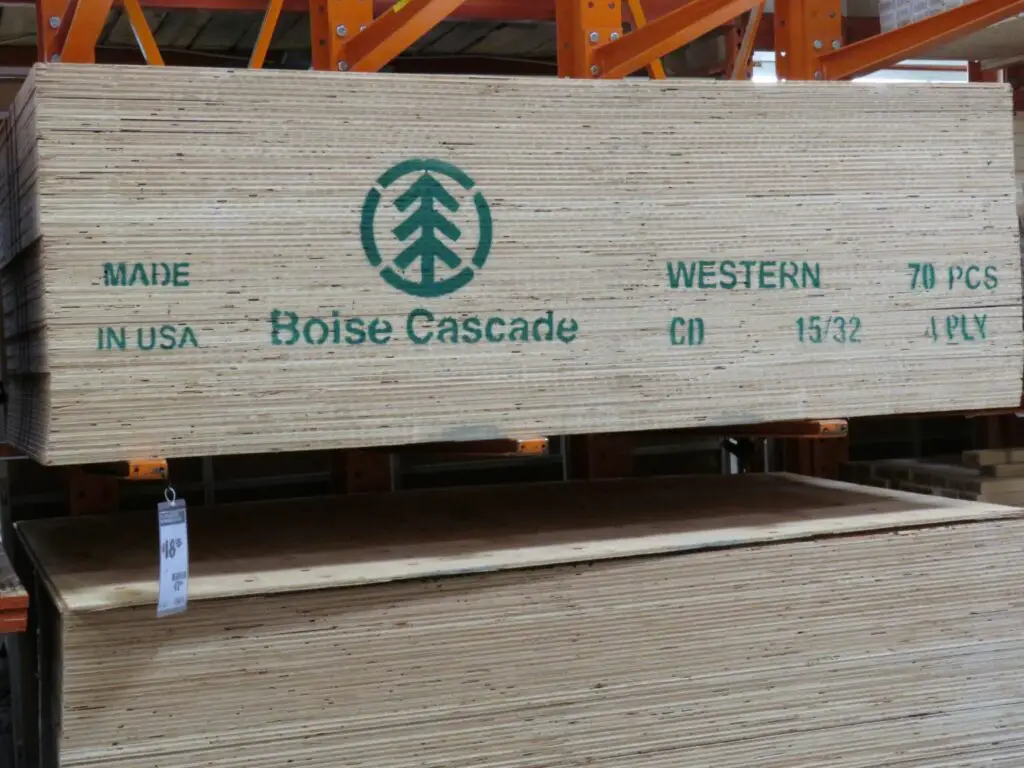
What is Plywood?
Plywood is an engineered wood product made from thin layers, or plies, of wood veneer glued together. Each layer’s grain is typically oriented perpendicular to adjacent layers, which enhances strength, stability, and resistance to warping.
Common subcategories of plywood include structural plywood, sheathing plywood, marine plywood, hardwood plywood, softwood plywood, and specialty plywood designed for specific applications. Plywood comes in standardized thicknesses and dimensions, which provides significant efficiencies in construction.
Plywood is widely used for roof decking, wall sheathing, subflooring, cabinetry, furniture making, and numerous other structural and non-structural applications. The weight and thickness of plywood and other engineered wood panels can be important values for accurate structural design. Material weight values are of particular importance in roofing.
Plywood Weight Calculator
When using this calculator, note that:
- CDX plywood is a common grade of softwood plywood typically used for exterior sheathing or roof deck applications.
- When entering a plywood thickness greater than 1 that contains a fraction, such as 1 1/8, make sure to include a space between the whole number and the fraction. Type in “1 1/8”, not “11/8”. Fractions without a whole number (e.g., “3/4”) should be entered normally.
- The weight values produced by this calculator are based on the values in the charts below, but may be slightly different due to internal rounding during the calculations. But all of these values are simply approximations anyway, since real plywood weights will vary and these are estimates. Close estimates, but still estimates.
- This calculator is intended to give you an idea of what plywood weighs, but even the same type of plywood panel with the same dimensions can vary in weight from product to product. Differences of up to 20% in weight are common due to variations in wood species, adhesives, and manufacturing processes. Always check with the manufacturer for the weights of specific products. For structural or load-bearing applications, consulting manufacturer data sheets or product specifications is especially important.
Plywood Weight Calculator
What is Plywood Made of?
Plywood is composed of approximately 90% – 97% wood, with the remainder made up by primers, sealants, and adhesives such as phenol formaldehyde resin.
Other engineered wood panel types, such as particle board or OSB, contain a much higher percentage of adhesive resin, and since these resins are heavier than wood, these panels tend to be significantly heavier than plywood. Particle board, for example, often contains as much as 20% to 30% adhesive resin by weight.
Plywood and OSB Weight Factors
Plywood weight is determined by the length, width, and thickness of the panel, as well as the wood species and the types and amounts of adhesives, primers, and sealants used to make the plywood. This goes for all other types of engineered wood panels as well.
Plywood, OSB, particle board, etc. are manufactured using adhesives, primers, and sealants. Some of these panel types require quite a bit more of these materials than other types. For instance, while plywood is typically 90% to 97% wood, OSB might only contain 80% wood. Particle board, due to its high adhesive content, can sometimes be as low as 70% wood content.
Since adhesive resins and sealants are much heavier than wood, this means that wood products that use a lot of them will be heavier than wood products that use less of them. For instance, OSB tends to be around 20% to 25% heavier than softwood plywood, OSB’s main competitor in the construction industry.
Another factor in plywood weight is the wood species used to make the panel. Different wood species have naturally different densities, and this can make a big difference in the weight of the finished product. For example, hardwood plywood such as birch or oak will typically weigh substantially more than softwood plywood such as pine or spruce, due to their higher density.
The use of different wood species and different proportions of adhesive by different manufacturers can result in weight differences of up to 20% for plywood or OSB panels with the exact same dimensions and product description from one manufacturer to the next, or even for different batches of the same product from the same manufacturer. These variances are normal and expected, and buyers should always check product specifications closely if precise panel weight is important for their project.
About These Plywood Weight & Thickness Charts
The following tables provide typical weights (also referred to as “dead load” or “self-weight”) for plywood, OSB, and other engineered wood panels according to thickness and panel type.
The plywood thicknesses included cover most of the standard panel thicknesses available from engineered wood panel manufacturers today. Common plywood thicknesses typically range from 1/4 inch (6 mm) up to 1 inch (25 mm) or more.
The tables provide metric and US standard plywood weights for whole standard sheets of various common thicknesses, as well as plywood weights per square foot and plywood weights per square meter. Standard plywood sheet dimensions in the US are typically 4 feet by 8 feet (1220 mm x 2440 mm), though some panels may be available in other sizes, particularly in international markets or specialized construction applications.
The plywood weights shown here were calculated using the product data sheets or manufacturer specifications of actual, specific wood panel products, and in most cases, these plywood weights are the average of product weights from more than one manufacturer.
Table 1: Plywood Weights in Pounds per Square Foot
Weight of Plywood, OSB, and Other Engineered Wood Panels in Pounds per Square Foot (lb/ft²) by Panel Thickness |
||||||||||||
---|---|---|---|---|---|---|---|---|---|---|---|---|
Panel Type | Panel Thickness in Inches | |||||||||||
↓ | 1/4″ | 11/32″ | 3/8″ | 15/32″ | 1/2″ | 19/32″ | 5/8″ | 23/32″ | 3/4″ | 7/8″ | 1″ | 1⅛” |
APA Plywood Standard |
0.80 lb/ft² |
1.00 lb/ft² |
1.10 lb/ft² |
1.40 lb/ft² |
1.50 lb/ft² |
1.70 lb/ft² |
1.80 lb/ft² |
2.10 lb/ft² |
2.20 lb/ft² |
2.60 lb/ft² |
3.00 lb/ft² |
3.30 lb/ft² |
Baltic Birch Plywood |
0.92 lb/ft² |
1.15 lb/ft² |
1.26 lb/ft² |
1.61 lb/ft² |
1.72 lb/ft² |
1.95 lb/ft² |
2.06 lb/ft² |
2.41 lb/ft² |
2.54 lb/ft² |
2.98 lb/ft² |
3.44 lb/ft² |
3.78 lb/ft² |
Hardwood Plywood |
0.80 lb/ft² |
1.00 lb/ft² |
1.10 lb/ft² |
1.40 lb/ft² |
1.50 lb/ft² |
1.70 lb/ft² |
1.80 lb/ft² |
2.10 lb/ft² |
2.20 lb/ft² |
2.60 lb/ft² |
3.00 lb/ft² |
3.30 lb/ft² |
Marine Plywood |
0.85 lb/ft² |
1.06 lb/ft² |
1.17 lb/ft² |
1.49 lb/ft² |
1.60 lb/ft² |
1.81 lb/ft² |
1.92 lb/ft² |
2.23 lb/ft² |
2.34 lb/ft² |
2.77 lb/ft² |
3.19 lb/ft² |
3.51 lb/ft² |
Pressure-Treated Plywood |
1.00 lb/ft² |
1.25 lb/ft² |
1.37 lb/ft² |
1.75 lb/ft² |
1.87 lb/ft² |
2.12 lb/ft² |
2.24 lb/ft² |
2.62 lb/ft² |
2.74 lb/ft² |
3.24 lb/ft² |
3.74 lb/ft² |
4.11 lb/ft² |
Softwood Plywood |
0.72 lb/ft² |
0.90 lb/ft² |
0.99 lb/ft² |
1.26 lb/ft² |
1.35 lb/ft² |
1.53 lb/ft² |
1.62 lb/ft² |
1.89 lb/ft² |
1.98 lb/ft² |
2.34 lb/ft² |
2.70 lb/ft² |
2.97 lb/ft² |
MDF | 1.15 lb/ft² |
1.44 lb/ft² |
1.58 lb/ft² |
2.01 lb/ft² |
2.16 lb/ft² |
2.44 lb/ft² |
2.59 lb/ft² |
3.02 lb/ft² |
3.16 lb/ft² |
3.74 lb/ft² |
4.31 lb/ft² |
4.74 lb/ft² |
MDO | 0.80 lb/ft² |
1.00 lb/ft² |
1.10 lb/ft² |
1.40 lb/ft² |
1.50 lb/ft² |
1.70 lb/ft² |
1.80 lb/ft² |
2.10 lb/ft² |
2.20 lb/ft² |
2.60 lb/ft² |
3.00 lb/ft² |
3.30 lb/ft² |
Particle Board | 1.08 lb/ft² |
1.35 lb/ft² |
1.49 lb/ft² |
1.90 lb/ft² |
2.03 lb/ft² |
2.30 lb/ft² |
2.44 lb/ft² |
2.84 lb/ft² |
2.98 lb/ft² |
3.52 lb/ft² |
4.06 lb/ft² |
4.47 lb/ft² |
Panel Type | Panel Thickness in Inches | |||||||||||
↓ | 1/4″ | 5/16″ | 3/8″ | 7/16″ | 15/32″ | 1/2″ | 19/32″ | 5/8″ | 23/32″ | 3/4″ | 7/8″ | 1″ |
OSB | 0.90 lb/ft² |
1.10 lb/ft² |
1.20 lb/ft² |
1.40 lb/ft² |
1.50 lb/ft² |
1.70 lb/ft² |
2.00 lb/ft² |
2.10 lb/ft² |
2.40 lb/ft² |
2.50 lb/ft² |
2.90 lb/ft² |
3.30 lb/ft² |
Table 2: Plywood Weights in Pounds per Standard Sheet
Weight of Plywood, OSB, and Other Engineered Wood Panels
In Pounds per Standard Sheet (4 feet x 8 feet) by Panel Thickness |
||||||||||||
---|---|---|---|---|---|---|---|---|---|---|---|---|
Panel Type | Panel Thickness in Inches | |||||||||||
↓ | 1/4″ | 11/32″ | 3/8″ | 15/32″ | 1/2″ | 19/32″ | 5/8″ | 23/32″ | 3/4″ | 7/8″ | 1″ | 1⅛” |
APA Plywood Standard |
26 lb | 32 lb | 35 lb | 45 lb | 48 lb | 54 lb | 58 lb | 67 lb | 70 lb | 83 lb | 96 lb | 106 lb |
Baltic Birch Plywood |
29 lb | 37 lb | 40 lb | 52 lb | 55 lb | 62 lb | 66 lb | 77 lb | 81 lb | 95 lb | 110 lb | 121 lb |
Hardwood Plywood |
26 lb | 32 lb | 35 lb | 45 lb | 48 lb | 54 lb | 58 lb | 67 lb | 70 lb | 83 lb | 96 lb | 106 lb |
Marine Plywood |
27 lb | 34 lb | 37 lb | 48 lb | 51 lb | 58 lb | 61 lb | 71 lb | 75 lb | 89 lb | 102 lb | 112 lb |
Pressure-Treated Plywood |
32 lb | 40 lb | 44 lb | 56 lb | 60 lb | 68 lb | 72 lb | 84 lb | 88 lb | 104 lb | 120 lb | 132 lb |
Softwood Plywood |
23 lb | 29 lb | 32 lb | 40 lb | 43 lb | 49 lb | 52 lb | 60 lb | 63 lb | 75 lb | 86 lb | 95 lb |
MDF | 37 lb | 46 lb | 51 lb | 64 lb | 69 lb | 78 lb | 83 lb | 97 lb | 101 lb | 120 lb | 138 lb | 152 lb |
MDO | 26 lb | 32 lb | 35 lb | 45 lb | 48 lb | 54 lb | 58 lb | 67 lb | 70 lb | 83 lb | 96 lb | 106 lb |
Particle Board | 35 lb | 43 lb | 48 lb | 61 lb | 65 lb | 74 lb | 78 lb | 91 lb | 95 lb | 113 lb | 130 lb | 143 lb |
Panel Type | Panel Thickness in Inches | |||||||||||
↓ | 1/4″ | 5/16″ | 3/8″ | 7/16″ | 15/32″ | 1/2″ | 19/32″ | 5/8″ | 23/32″ | 3/4″ | 7/8″ | 1″ |
OSB | 29 lb | 35 lb | 38 lb | 45 lb | 48 lb | 54 lb | 64 lb | 67 lb | 77 lb | 80 lb | 93 lb | 106 lb |
Table 3: Plywood Weights in Kilograms per Square Meter
Weight of Plywood, OSB, and Other Engineered Wood Panels
In Kilograms per Square Meter (kg/m²) by Panel Thickness |
||||||||||
---|---|---|---|---|---|---|---|---|---|---|
Panel Type | Panel Thickness in Millimeters | |||||||||
↓ | 6 mm | 9 mm | 12 mm | 15 mm | 18 mm | 21 mm | 24 mm | 25 mm | 28 mm | 30 mm |
Baltic Birch
Plywood |
4.20 kg/m² |
5.85 kg/m² |
7.80 kg/m² |
9.75 kg/m² |
11.67 kg/m² |
13.65 kg/m² |
15.61 kg/m² |
16.25 kg/m² |
18.20 kg/m² |
19.50 kg/m² |
Hardwood
Plywood |
3.65 kg/m² |
5.09 kg/m² |
6.78 kg/m² |
8.48 kg/m² |
10.15 kg/m² |
11.87 kg/m² |
13.57 kg/m² |
14.13 kg/m² |
15.83 kg/m² |
16.96 kg/m² |
Marine
Plywood |
3.87 kg/m² |
5.40 kg/m² |
7.19 kg/m² |
8.99 kg/m² |
10.76 kg/m² |
12.58 kg/m² |
14.38 kg/m² |
14.98 kg/m² |
16.78 kg/m² |
17.98 kg/m² |
Pressure-Treated
Plywood |
4.56 kg/m² |
6.36 kg/m² |
8.48 kg/m² |
10.60 kg/m² |
12.69 kg/m² |
14.84 kg/m² |
16.96 kg/m² |
17.66 kg/m² |
19.79 kg/m² |
21.20 kg/m² |
Softwood
Plywood |
3.29 kg/m² |
4.58 kg/m² |
6.10 kg/m² |
7.63 kg/m² |
9.14 kg/m² |
10.68 kg/m² |
12.21 kg/m² |
12.72 kg/m² |
14.25 kg/m² |
15.26 kg/m² |
MDF | 5.26 kg/m² |
7.33 kg/m² |
9.76 kg/m² |
12.21 kg/m² |
14.62 kg/m² |
17.09 kg/m² |
19.54 kg/m² |
20.35 kg/m² |
22.80 kg/m² |
24.42 kg/m² |
MDO | 3.65 kg/m² |
5.09 kg/m² |
6.78 kg/m² |
8.48 kg/m² |
10.15 kg/m² |
11.87 kg/m² |
13.57 kg/m² |
14.13 kg/m² |
15.83 kg/m² |
16.96 kg/m² |
OSB | 4.15 kg/m² |
5.75 kg/m² |
7.66 kg/m² |
9.58 kg/m² |
11.47 kg/m² |
13.41 kg/m² |
15.33 kg/m² |
15.97 kg/m² |
17.89 kg/m² |
19.16 kg/m² |
Particle Board | 4.93 kg/m² |
6.87 kg/m² |
9.15 kg/m² |
11.45 kg/m² |
13.70 kg/m² |
16.02 kg/m² |
18.32 kg/m² |
19.08 kg/m² |
21.37 kg/m² |
22.90 kg/m² |
Table 4: Plywood Weights in Kilograms per Standard Sheet
Weight of Plywood, OSB, and Other Engineered Wood Panels
In Kilograms per Standard Sheet (1220 mm x 2440 mm) by Panel Thickness |
||||||||||
---|---|---|---|---|---|---|---|---|---|---|
Panel Type | Panel Thickness in Millimeters | |||||||||
↓ | 6 mm | 9 mm | 12 mm | 15 mm | 18 mm | 21 mm | 24 mm | 25 mm | 28 mm | 30 mm |
Baltic Birch
Plywood |
12.50 kg | 17.41 kg | 23.22 kg | 29.02 kg | 34.74 kg | 40.63 kg | 46.47 kg | 48.37 kg | 54.18 kg | 58.05 kg |
Hardwood
Plywood |
10.87 kg | 15.15 kg | 20.18 kg | 25.24 kg | 30.21 kg | 35.33 kg | 40.40 kg | 42.06 kg | 47.12 kg | 50.49 kg |
Marine
Plywood |
11.52 kg | 16.07 kg | 21.40 kg | 26.76 kg | 32.03 kg | 37.45 kg | 42.81 kg | 44.59 kg | 49.95 kg | 53.52 kg |
Pressure-Treated
Plywood |
13.57 kg | 18.93 kg | 25.24 kg | 31.55 kg | 37.78 kg | 44.18 kg | 50.49 kg | 52.57 kg | 58.91 kg | 63.11 kg |
Softwood
Plywood |
9.79 kg | 13.63 kg | 18.16 kg | 22.71 kg | 27.21 kg | 31.79 kg | 36.35 kg | 37.86 kg | 42.42 kg | 45.43 kg |
MDF | 15.66 kg | 21.82 kg | 29.05 kg | 36.35 kg | 43.52 kg | 50.87 kg | 58.17 kg | 60.58 kg | 67.87 kg | 72.69 kg |
MDO | 10.87 kg | 15.15 kg | 20.18 kg | 25.24 kg | 30.21 kg | 35.33 kg | 40.40 kg | 42.06 kg | 47.12 kg | 50.49 kg |
OSB | 12.35 kg | 17.12 kg | 22.80 kg | 28.52 kg | 34.14 kg | 39.92 kg | 45.63 kg | 47.54 kg | 53.25 kg | 57.04 kg |
Particle Board | 14.68 kg | 20.45 kg | 27.24 kg | 34.08 kg | 40.78 kg | 47.69 kg | 54.53 kg | 56.80 kg | 63.61 kg | 68.17 kg |
Types of Plywood and Other Engineered Wood Panels
APA Standard Plywood Weight
APA Plywood Standard: The Engineered Wood Association (formerly the American Plywood Association) provides standard notional plywood weights for use in determining expected dead loads when performing structural engineering calculations. Softwood plywood is typically used as structural plywood (roof decking, sheathing, flooring).
The APA Standard plywood weights are not weights for actual products and tend to be somewhat heavier than the weights of any real softwood plywood you will find. This is because APA standard weights are intentionally conservative, designed to ensure structural calculations will safely accommodate potential variations in material density and moisture content. Actual plywood panel weights may vary based on wood species, glue type, moisture conditions, and manufacturing tolerances.
A 4’ x 8’ sheet of 1/2-inch APA Standard Plywood would weigh 48 lbs. However, typical actual weights for 1/2-inch softwood plywood panels generally range from about 40 to 45 lbs. per standard sheet. To accurately determine the weight of plywood for precise engineering calculations or transportation planning, it’s recommended to reference manufacturer-provided specifications or weigh actual product samples directly.
Baltic Birch Plywood Weight
Baltic Birch Plywood: This is a high-quality plywood traditionally produced in Russia and other areas around the Baltic Sea. (Forests around the Baltic Sea can be up to 28% birch trees.)
This type of plywood is made up entirely of birch wood, so unlike typical hardwood plywood (see below), it does not use softwood for the inner plies, and the inner plies are void-free, increasing its stability. The absence of voids also makes Baltic Birch plywood highly desirable for precision woodworking, such as in laser cutting and CNC routing applications. Baltic birch plywood is used mostly for furniture-making and cabinetry, as well as drawer boxes, musical instruments (such as drums and guitars), and other products that require exceptional strength, stability, and uniform appearance.
A 4’ x 8’ sheet of 1/2-inch Baltic Birch Plywood weighs around 55 lbs. Actual weights may vary slightly, typically ranging from about 53 to 56 lbs. per standard sheet, depending on moisture content and manufacturing variations. Due to its dense, consistent composition, Baltic Birch plywood is significantly heavier than comparably sized softwood plywood panels, contributing to its superior durability and stiffness.
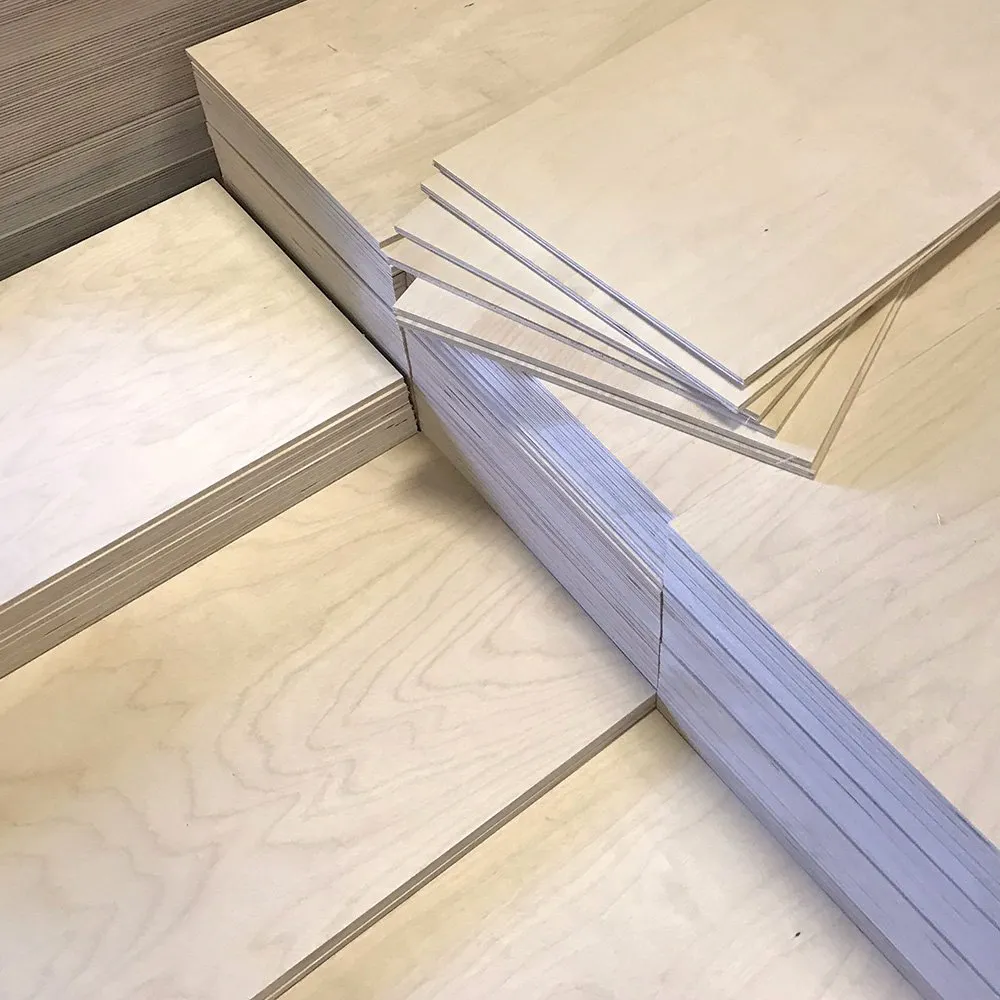
Hardwood Plywood Weight
Hardwood Plywood: At least the front and back veneers (outer plies) of hardwood plywood will be made of a hardwood species such as maple or oak. Although the inner plies may also be hardwood, more often they will be made of a cheaper softwood species. This construction style balances cost-effectiveness with strength and appearance. The hardwood veneers improve strength, stability, and impact resistance; they also provide a smooth surface with a tight, even grain that can result in an attractive and consistent finished appearance.
Hardwood plywood is commonly used in applications where these qualities are desired, like flooring, cabinets, or wall paneling, where the wood’s appearance is important.
A typical 4’ x 8’ sheet of 1/2-inch Hardwood Plywood weighs around 48 lbs. Actual weights can vary depending on the hardwood species, veneer thickness, and core composition, typically ranging from about 45 to 52 lbs. per standard sheet. Denser hardwood species such as oak or walnut generally result in slightly heavier plywood sheets compared to lighter species like poplar.
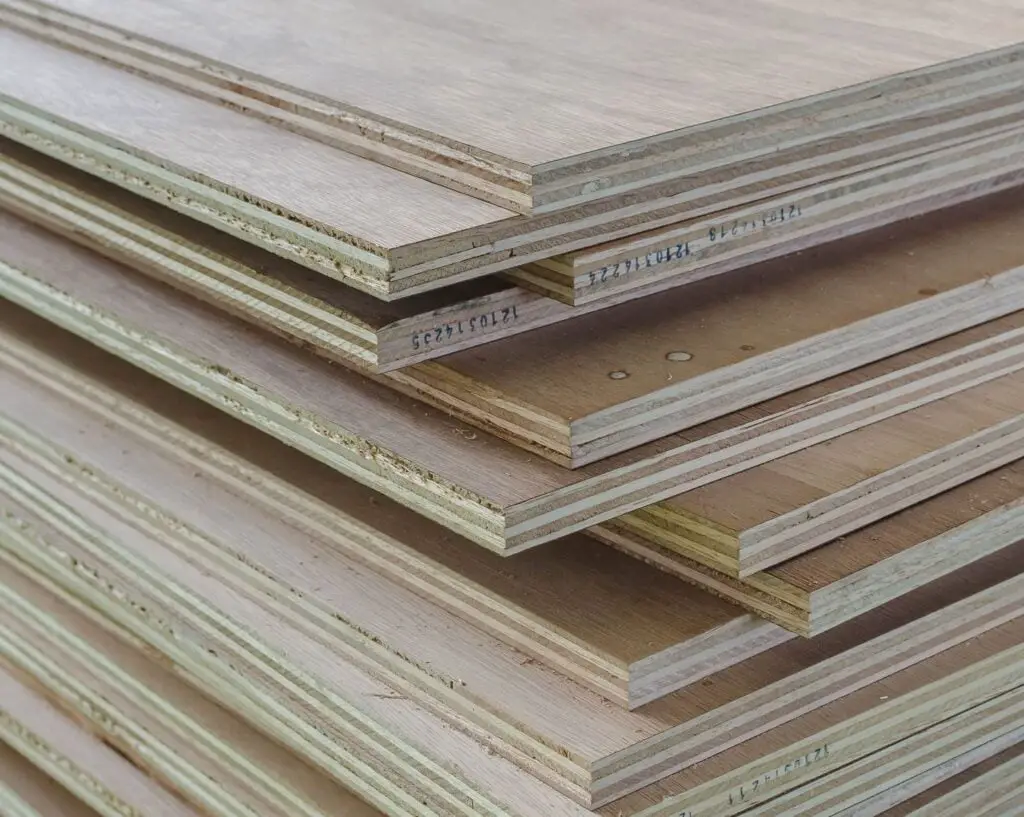
Marine Plywood Weight
Marine Plywood: Despite its name, this is not a waterproof plywood. Marine plywood is manufactured to withstand exposure to moisture better than standard plywood, but it still requires proper sealing and finishing to fully protect against water damage. Marine plywood is manufactured using specially formulated water-resistant adhesive and very dense, high-quality outer plies. These high-quality outer veneers serve to help prevent moisture from penetrating the panel.
Marine plywood is designed to be used where the material will be subjected to higher-than-normal amounts of moisture, such as in marinas and other coastal environments. Marine plywood is often used for boat building, docks, outdoor furniture, and any exterior structures that require enhanced resistance to water and humidity.
A typical 4’ x 8’ sheet of 1/2-inch Marine Plywood weighs around 51 lbs. Actual weights can vary slightly depending on the wood species used, typically ranging from about 48 to 55 lbs. per standard sheet. Because of its dense outer layers and high-quality construction, marine plywood tends to be heavier and more durable than standard softwood plywood of the same dimensions.
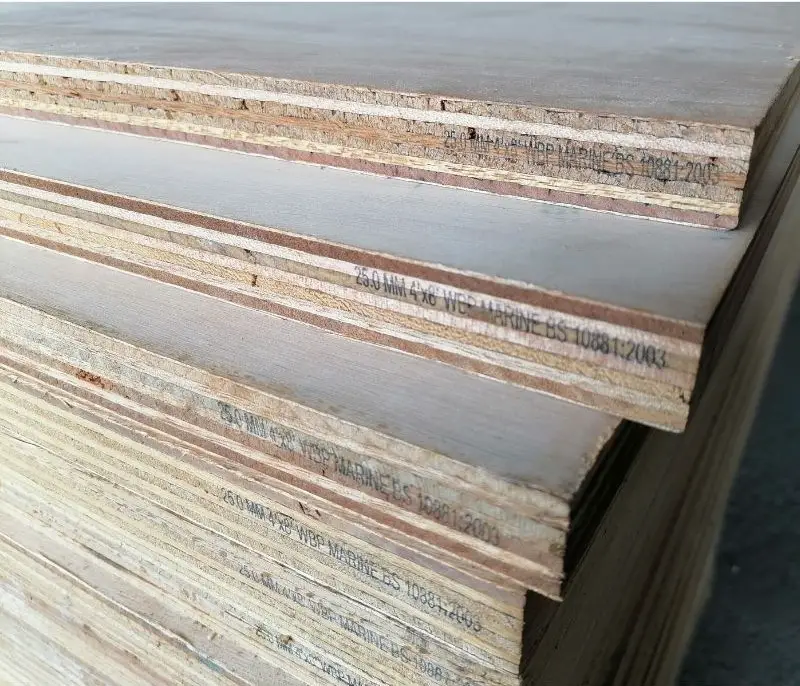
Pressure-Treated Plywood Weight
Pressure-Treated Plywood: This is usually a softwood plywood that has been pressure-treated to help it resist decay caused by fungus, insects, and other organisms. The pressure-treatment process forces chemical preservatives deep into the wood fibers, significantly improving the plywood’s durability and lifespan when exposed to outdoor or ground-contact conditions.
Southern yellow pine is particularly well-suited for pressure treating, and most pressure-treated plywood is made from southern yellow pine. Special waterproof adhesives are used when this plywood is manufactured so it can withstand the pressure-treating process without falling apart. Pressure-treated plywood uses relatively more adhesive than other plywoods. Because of this and the fact that the southern yellow pine used is much heavier than other wood species used in construction, pressure-treated plywood tends to be a heavy plywood.
Pressure-treated plywood is heavier than other plywoods even after drying out from the pressure-treating process. Before drying out, of course, it can be much, much heavier.
A typical 4’ x 8’ sheet of 1/2-inch Pressure-Treated Plywood weighs around 60 lbs. Actual weights can vary considerably depending on moisture content and specific treatment methods, with fully dry sheets typically weighing between 56 and 65 lbs. per standard panel.
Due to the chemical preservatives used, proper handling and safety precautions are recommended when working with pressure-treated plywood, including the use of gloves and dust masks when cutting or sanding.
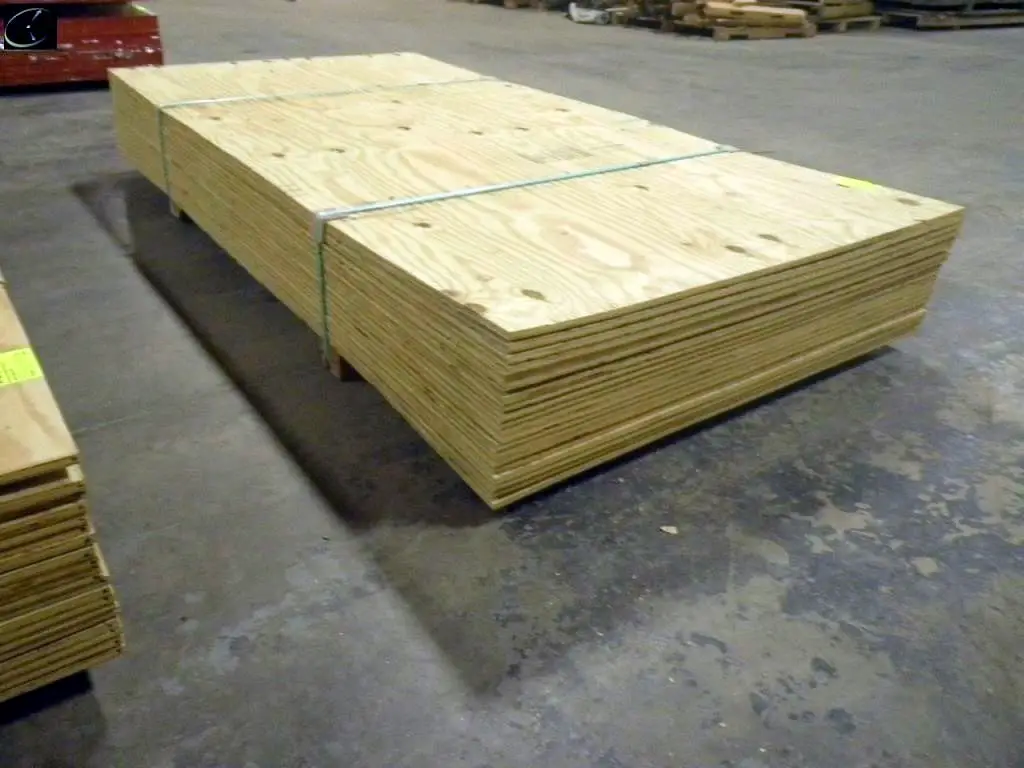
Softwood Plywood Weight
Softwood Plywood: This is the type of plywood most commonly used in construction. When people talk about structural plywood, it’s almost always softwood plywood that they’re talking about. Softwood plywood is used for roof sheathing, wall sheathing, subfloors, and more, including temporary construction, concrete formwork, and general-purpose structural applications.
Softwood plywood comes from coniferous trees, primarily fir, pine, or spruce. It is generally the lightest type of engineered wood panel, due to the light weight of the wood species used and the (relatively) low amount of adhesive used in the manufacturing process. Softwood plywood weight is further reduced by the presence of unfilled voids within the inner plies, which also results in slightly lower overall strength and stiffness compared to hardwood plywood or Baltic birch plywood. Softwood plywood is normally the cheapest plywood.
CDX plywood, the most common plywood used for roof sheathing, is a grade of softwood plywood, with the letters “CD” referring to the quality of the veneer faces, and the “X” indicating that exterior-grade adhesives have been used, making it suitable for limited exposure to moisture during construction.
A typical 4’ x 8’ sheet of 1/2-inch Softwood Plywood weighs around 43 lbs. Actual weights can vary from about 40 to 46 lbs. per standard sheet, depending on species, moisture content, and manufacturing variations. Fir plywood tends to be slightly heavier and stronger, while pine and spruce plywoods are lighter but may offer slightly less structural strength.
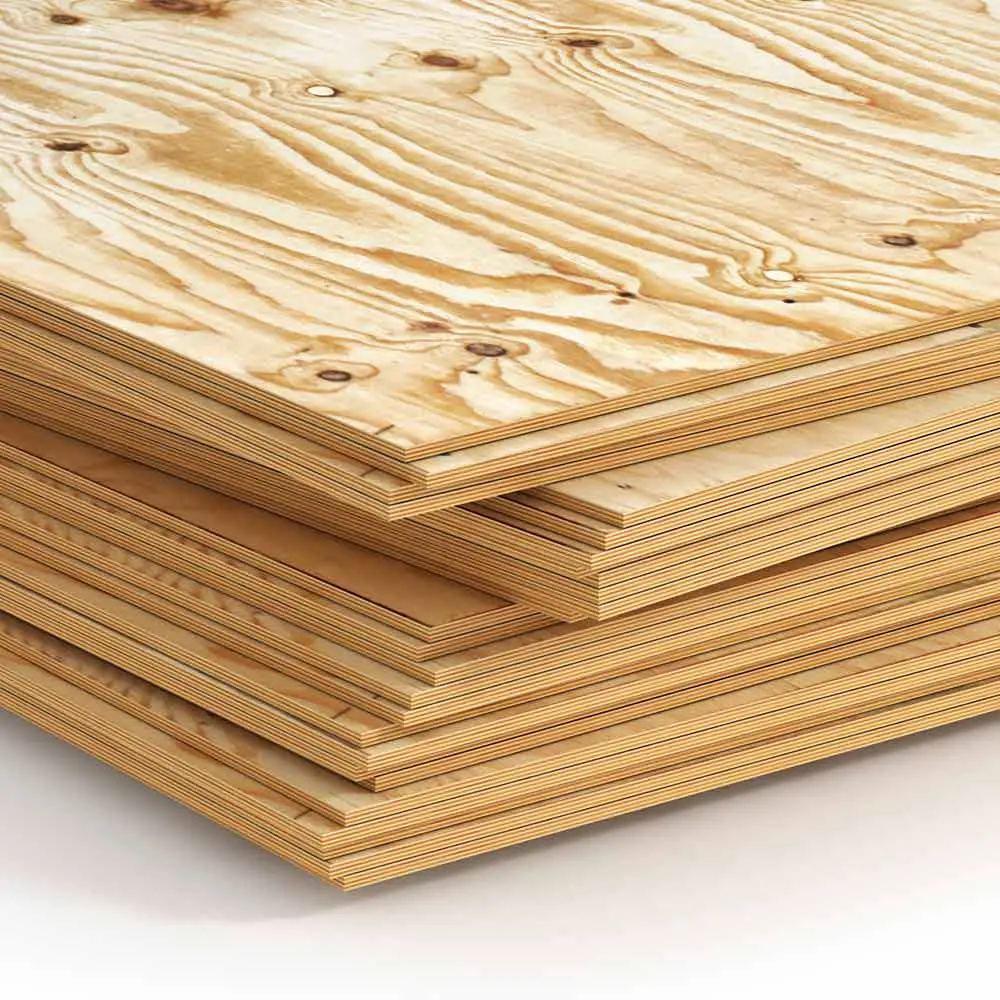
MDF Panel Weight
MDF: Medium Density Fiberboard is produced from wood scraps left over from other wood product manufacturing activities. This waste wood can be either hardwood or softwood. The scraps are broken down into very small wood fibers, which are combined with wax and adhesive resin to form the MDF panels. These fibers and resins are then compressed under heat and pressure, creating a smooth, dense panel with uniform strength and density throughout.
MDF does not handle moisture well, and is normally only used for interior applications, such as flooring or furniture. It can also be used when a cheaper material is wanted for cabinets, shelving, decorative moldings, and other projects where a smooth, consistent surface finish is desired.
Because of the extremely high resin content, MDF tends to be one of the heaviest types of engineered wood panels. The density and weight of MDF make it exceptionally stable and resistant to warping, but this heaviness also makes it more difficult to handle, cut, and install compared to lighter-weight plywood products.
A typical 4’ x 8’ sheet of 1/2-inch MDF weighs around 69 lbs. Actual weights typically range from about 65 to 72 lbs. per standard sheet, depending on the manufacturer and specific formulation. Moisture-resistant (MR) MDF and fire-resistant MDF may weigh slightly more due to specialized additives included during manufacturing.
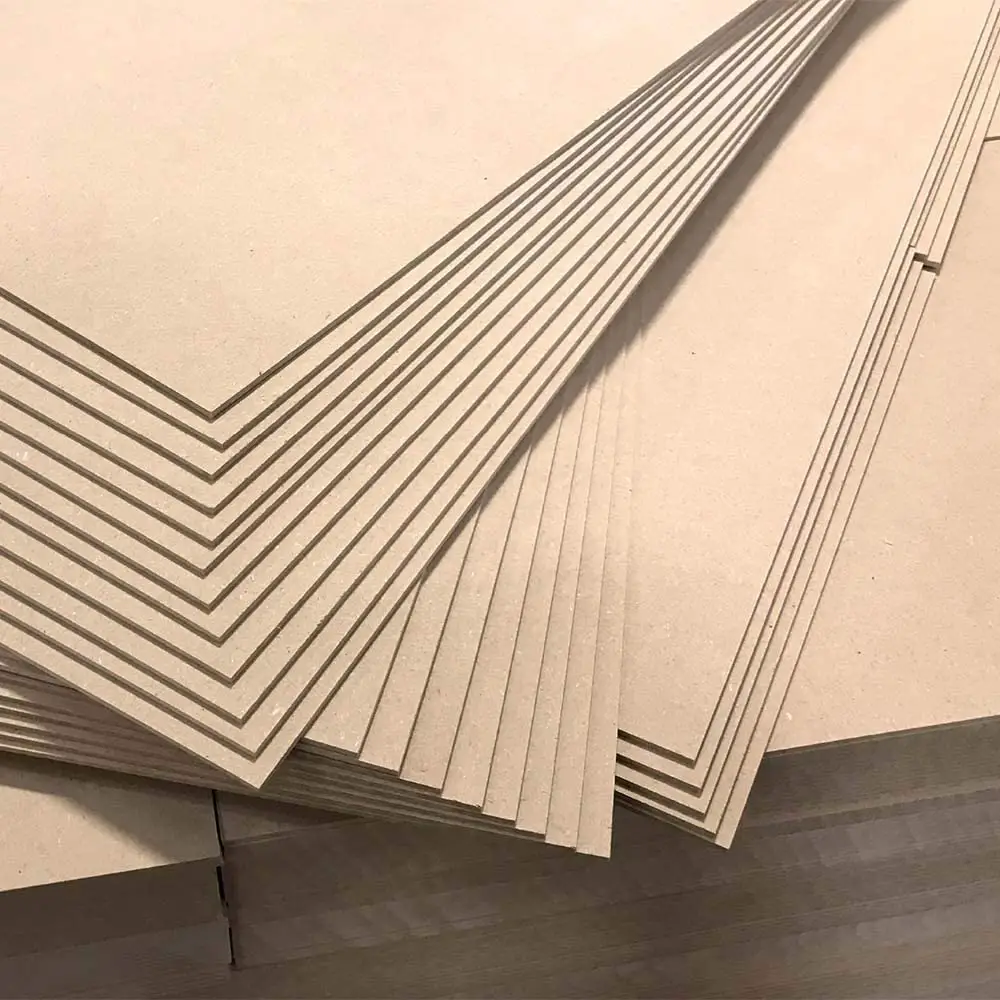
MDO Panel Weight
MDO: Medium Density Overlay is a type of exterior plywood specifically designed to be painted easily. The use of MDO for sign boards is very common. Due to its extremely smooth surface, it holds paint better, and looks better after being painted, than other types of engineered wood panels. In addition to signs, MDO is frequently used for exterior siding, concrete forms, cabinetry, and other applications where a smooth painted surface and/or increased weather resistance are needed.
The wood plies in MDO panels are typically softwood, and a thick, smooth layer (the overlay) of a highly water-resistant resin-impregnated paper is applied to either one or both sides of the panel. This resin-impregnated overlay provides protection against moisture and creates an ideal painting surface, and improving the panel’s durability and appearance in outdoor settings.
A typical 4’ x 8’ sheet of 1/2-inch MDO weighs around 48 lbs. Actual weights can vary somewhat depending on moisture content, the specific wood species used, and the thickness of the overlay layer, typically ranging from about 45 to 50 lbs. per standard sheet.
Because MDO is specifically engineered to resist weathering and moisture, it is often considered an excellent alternative to standard plywood or MDF for exterior projects requiring a painted, high-quality finish.
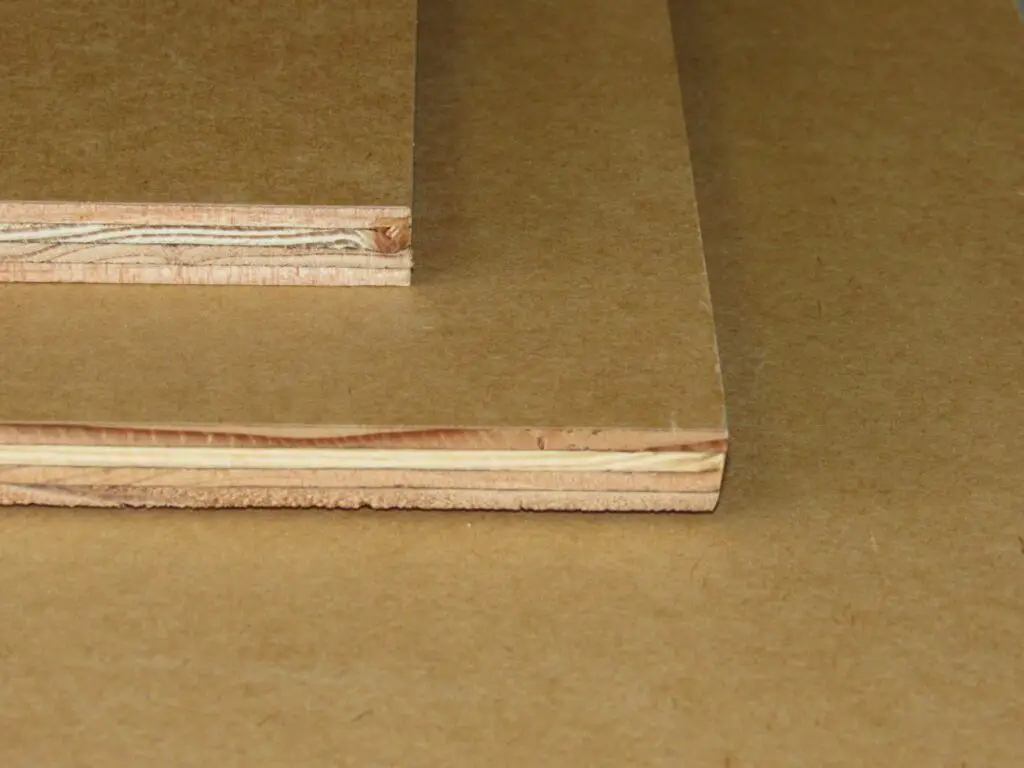
Particle Board Weight
Particle Board: The product generally known as “particle board” is similar to MDF. It is made with similar manufacturing techniques, but the end product is cheaper, weaker, and of lower density. It is also called LDF (low-density fiberboard) or chipboard. Unlike MDF, particle board is produced using larger wood particles, flakes, and shavings rather than finely ground fibers, resulting in a less uniform texture and a coarser surface.
Particle board typically has a lower strength-to-weight ratio compared to MDF or plywood, making it less suitable for structural applications. It is often used as a cost-effective material for non-structural purposes like shelving, cabinets, inexpensive furniture, cheap countertops, and underlayment for flooring. Like MDF, particle board has poor resistance to moisture and should be used primarily in dry, interior environments.
A typical 4’ x 8’ sheet of 1/2-inch Particle Board weighs around 66 lbs. Actual weights may range from about 60 to 68 lbs. per standard sheet, depending on manufacturing methods, density variations, and moisture content. Particle board panels generally weigh slightly less than MDF panels of comparable thickness but more than similarly sized softwood plywood panels.
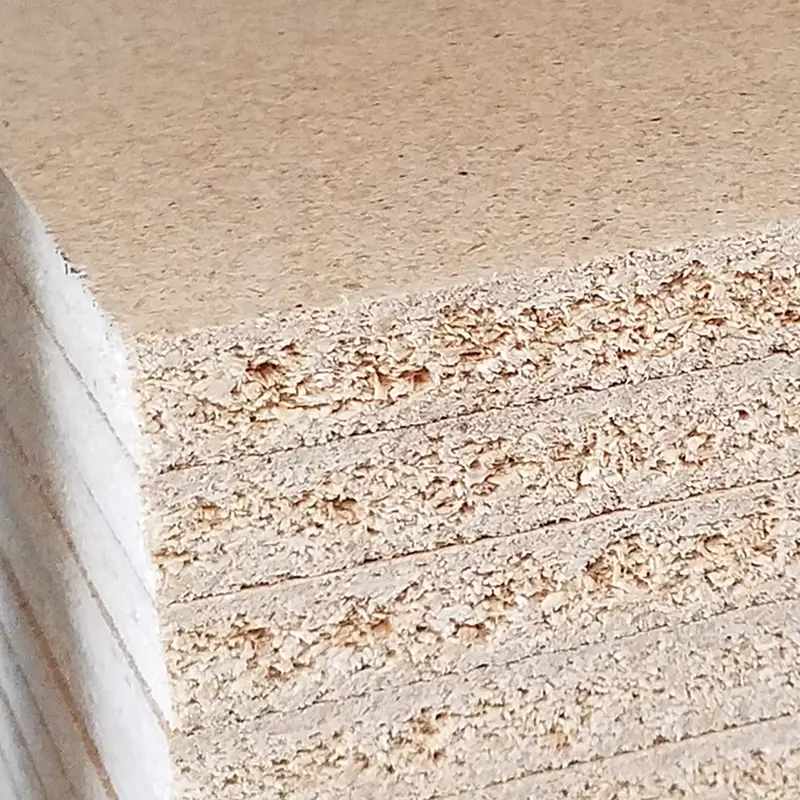
OSB Weight
OSB: Oriented Strand Board is plywood’s biggest competitor as a structural wood panel in North America. In large-scale commercial construction, OSB has largely replaced softwood plywood in wall sheathing, roof sheathing, and subflooring applications. This, of course, is due to the fact that a sheet of OSB costs about 20% less than the equivalent sheet of plywood. OSB panels also generally have more consistent density and fewer internal voids compared to softwood plywood, which can lead to more uniform strength across the panel.
OSB is made by breaking down wood into small strips, or “strands,” up to 6 inches long, and combining these strands with wax and adhesive resin under pressure and heat to form layers. These strands are commonly derived from fast-growing softwood species such as aspen, poplar, southern yellow pine, or mixed hardwoods.
The strands in each layer are all generally “oriented” in the same direction. These layers are combined to form OSB panels of the desired panel thickness. The wood strands in the outer layers are oriented one way, and the strands in the interior layers are oriented the other way, which increases panel strength, rigidity, and dimensional stability.
OSB is manufactured in a slightly different range of thicknesses than plywood. For instance, common OSB thicknesses include 5/16 and 7/16 inch, which are not standard plywood thicknesses.
A typical 4′ x 8′ sheet of 1/2-inch OSB weighs around 54 lbs. Actual weights usually range from about 50 to 56 lbs. per standard sheet, depending on species used, moisture content, and manufacturing specifics. In general, OSB sheets are slightly heavier than softwood plywood of equivalent dimensions due to their consistent density and adhesive content.
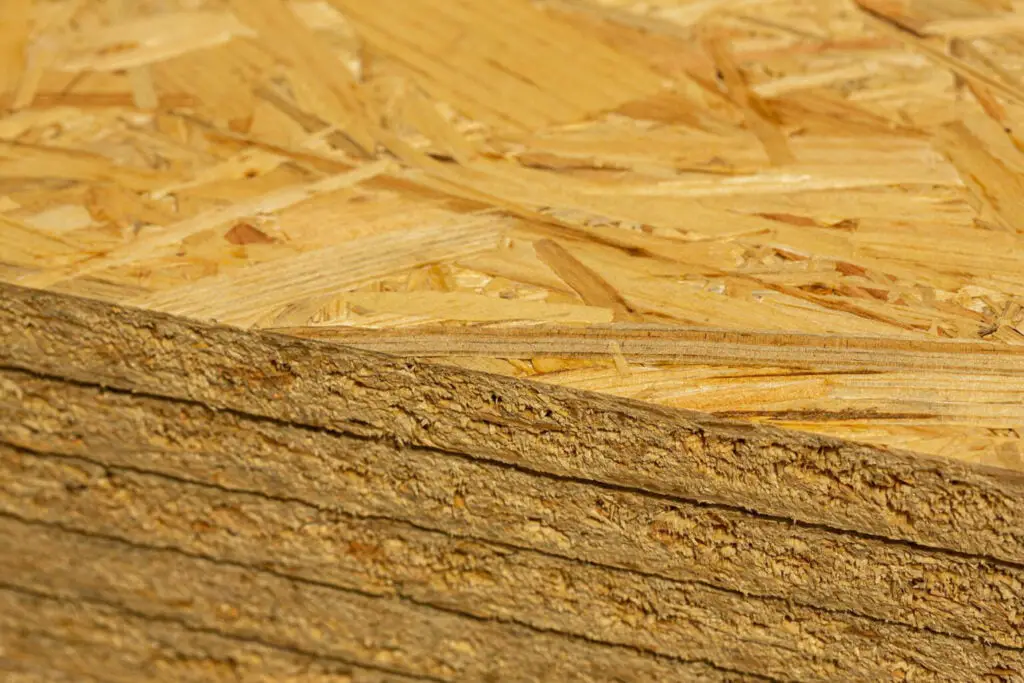
Ask the Lumber Company!
Remember, the values for plywood weight, OSB weight, etc. provided in this article are meant to give you a general idea of typical engineered wood panel weights, and should not be used if precise values are needed for critical engineering calculations. When precision is necessary, always refer to the specification sheet for the actual, specific product you intend to use, or contact the technical department of the panel manufacturer.
Most lumber yards or plywood manufacturers will list a phone number for their technical department on the contact page on their website. Go ahead and call them if you have any questions!