Table of Contents
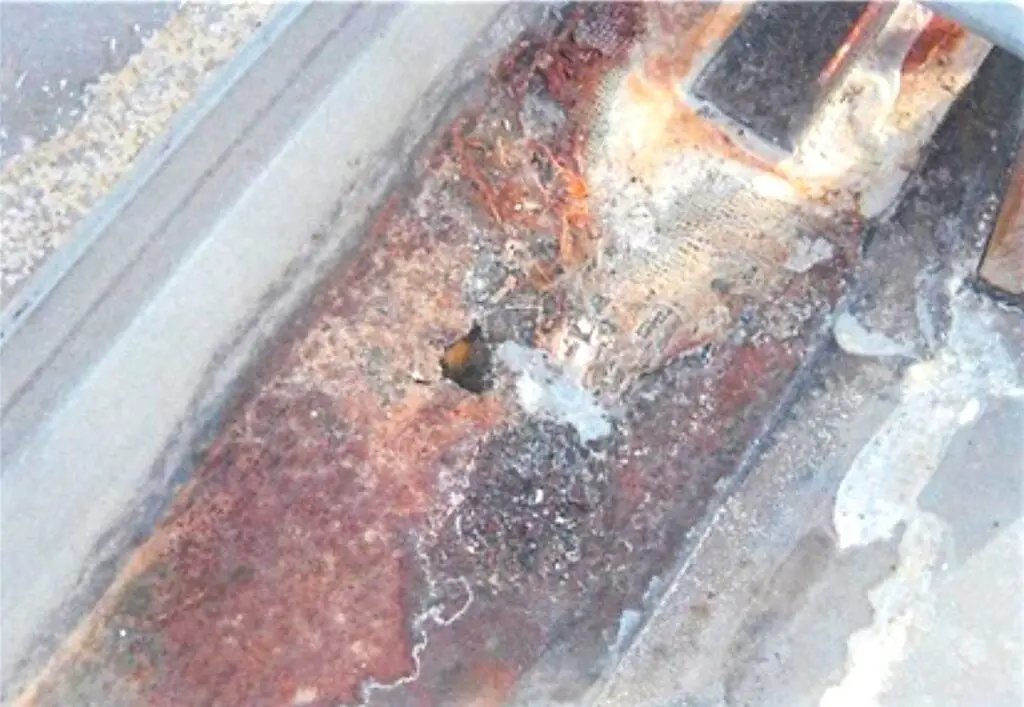
Introduction
When two different metals come into contact in the presence of moisture, they can form a simple electrochemical cell, creating a situation where one metal begins to corrode more rapidly than it would on its own. This process is called galvanic corrosion, and it can lead to unexpected material failures if the designer or installer doesn’t take steps to prevent it.
Galvanic corrosion requires three conditions:
- Two dissimilar metals with different positions in the galvanic series
- A conductive electrolyte, usually moisture such as rain, condensation, or humid air containing salts or pollutants
- An electrical connection between the metals, either through direct contact or by a continuous path of conductive moisture
When all three are present, the metal that is more anodic in the galvanic series will corrode, while the more cathodic metal will be protected. The greater the distance between the metals in the galvanic series, the higher the risk of corrosion.
It’s important to understand that this form of corrosion is not the result of poor material quality. Even corrosion-resistant metals like aluminum or stainless steel can be affected if they’re connected to a more noble metal in a damp environment.
In dry conditions, galvanic corrosion does not occur. Metal parts can be in contact for years with no issue if moisture is absent or if the metals are electrically isolated from one another.
Galvanic corrosion occurs when two dissimilar metals are in electrical contact and are exposed to a conductive electrolyte, such as rainwater, condensation, or damp air containing salts or pollutants. Under these conditions, an electrical current can flow from one metal (the more “anodic” or active metal) to the other (the more “cathodic” or noble metal). This current causes the anodic metal to corrode at an accelerated rate, while the cathodic metal is protected.
It’s important to note that just placing two metals in contact isn’t enough to cause corrosion. Moisture must also be present and it must be capable of conducting electricity. In other words, metals can sit side-by-side for years in a dry attic without issue, but once they’re exposed to rain, dew, or condensation, corrosion can begin quickly.
The risk is highest in areas where moisture gets trapped, such as around fasteners, panel seams, or shaded parts of a roof that dry out slowly. In coastal or urban areas where airborne salts or pollutants are common, the corrosive potential is even greater.
To prevent galvanic corrosion, you need to:
- Use metals that are close together in the galvanic series
- Electrically isolate dissimilar metals with sealants, coatings, or gaskets
- Design roof assemblies to shed water and dry quickly
Galvanic Compatibility of Metals Used in Construction
The following table provides general guidance on the compatibility of different metals when they come into contact. It is based primarily on the galvanic series, but also reflects practical experience in the building industry.
The table assumes typical outdoor exposure and common construction conditions. It accounts for the kinds of metal pairings that are generally accepted or avoided in practice. However, it does not dynamically factor in protective coatings, fastener installation methods, isolation materials, or environmental severity (such as marine or industrial conditions).
Use this chart as a guide to help avoid problematic pairings, especially where dissimilar metals may contact one another in the presence of moisture. You should always take into account any job-specific factors and especially manufacturer recommendations.
Learn more about the metals used in roofing.
Galvanic Compatibility Chart
This compatibility chart follows the U.S. military standard MIL-STD-889C – Dissimilar Metals; Department of Defense, Standard Practice, 2016. The metals in the table are listed from most anodic/active to most noble/passive.
- ✅ Safe: less than ~0.15V difference, and low corrosion risk in uncontrolled exposure.
- ⚠️ Caution: moderate difference or pairing needs mitigation (barriers, sealants, coatings, rubber washers for fasteners, etc).
- ❌ Unsafe: large potential difference, high corrosion risk to anodic member.
Galvanic Series
The table below includes metals commonly used in construction. It is a limited version of the galvanic series, which is a ranking of common metals from most anodic (most prone to galvanic corrosion) to most cathodic (least prone) based on their behavior in typical atmospheric environments. This table can help you choose compatible metals or determine where to apply protective barriers or coatings.
This table is especially relevant in roofing, where different metals are often used together in flashings, fasteners, gutters, panels, and other exposed building components. If incompatible metals are used without proper separation or isolation, galvanic corrosion can lead to premature component failures.
It’s important to understand that the galvanic series does not show how corrosion-resistant a metal is in general. A metal may resist corrosion well on its own when exposed to the weather, but if it comes into contact with a more noble metal, it can still corrode rapidly due to galvanic action. For example, aluminum is generally extremely corrosion-resistant, but when it touches copper on a wet roof, it will degrade quickly unless separated by a non-conductive barrier.
The order of the metals shown here is specific to roofing environments: outdoor exposure to air, rain, and dew, where metals tend to stay in their natural passive state. It assumes oxygen is available to maintain protective oxide layers on metals like aluminum and stainless steel. In submerged, stagnant, or acidic conditions, the relative position of some metals (especially stainless steel) can shift significantly.
Note on Stainless Steel: Stainless steels can appear in two very different places in a galvanic series depending on their surface condition. When their protective oxide layer is intact (this is called the passive state), they are highly corrosion-resistant and rank near the most noble metals like titanium. However, in certain environments, such as tight crevices, stagnant water, or acidic conditions, they can lose that protection and become active, making them far more susceptible to corrosion.
For most architectural applications, stainless steel stays in the passive state due to regular exposure to air and moisture. In these conditions, passive stainless steels like 304 and 316 are highly durable and unlikely to corrode when in contact with other building metals. Only in submerged or poorly ventilated areas is there a significant risk of galvanic corrosion involving stainless steel.
Galvanic Series Table
General Note: Galvanic rankings vary by environment. This chart reflects relative positions based on MIL-STD-889C for general seawater conditions. Other sources (e.g., stagnant or low-oxygen water) may show different positions, especially for copper and stainless steel.
Anodic – Active Most Susceptible to Corrosion |
---|
Magnesium and Magnesium Alloys |
Zinc |
Galvanized Steel |
Galvalume |
Aluminum |
Steel (Carbon) |
Aluminized Steel |
Weathering Steel |
Cast Iron |
Lead |
Tin |
Stainless Steel (300 Series, Active) |
Terne (Lead-Tin Alloy) |
Terne-Coated Stainless Steel |
Brass |
Bronze |
Copper |
Cupronickel |
Monel |
Nickel |
Stainless Steel (400 Series, Passive) |
Stainless Steel (300 Series, Passive) |
Titanium |
Cathodic – Noble Most Resistant to Corrosion |
Table Showing Which Metal is at Risk of Corrosion
This table shows which metal is at greater risk of corrosion when two dissimilar metals are in contact. It follows the galvanic series ranking from most anodic (corrodes easily) to most cathodic (resists corrosion).
The name of the metal in the table cell is (typically) the one that will corrode.
Metal at Risk of Corrosion
When Two Metals Are in Contact
Metal | Magnesium and Magnesium Alloys |
Zinc | Galvanized Steel | Galvalume | Aluminum | Steel (Carbon) | Cast Iron | Lead | Tin | Terne-coated Stainless Steel |
Stainless Steel (300 Series, Active) |
Brass | Bronze | Copper | Cupronickel | Monel | Nickel | Stainless Steel (400 Series, Passive) |
Stainless Steel (300 Series, Passive) |
Titanium |
---|---|---|---|---|---|---|---|---|---|---|---|---|---|---|---|---|---|---|---|---|
Magnesium and Magnesium Alloys |
Same Metal | Magnesium | Magnesium | Magnesium | Magnesium | Magnesium | Magnesium | Magnesium | Magnesium | Magnesium | Magnesium | Magnesium | Magnesium | Magnesium | Magnesium | Magnesium | Magnesium | Magnesium | Magnesium | Magnesium |
Zinc | Magnesium | Same Metal | Zinc | Zinc | Zinc | Zinc | Zinc | Zinc | Zinc | Zinc | Zinc | Zinc | Zinc | Zinc | Zinc | Zinc | Zinc | Zinc | Zinc | Zinc |
Galvanized Steel | Magnesium | Zinc | Same Metal | Galvanized Steel | Galvanized Steel | Galvanized Steel | Galvanized Steel | Galvanized Steel | Galvanized Steel | Galvanized Steel | Galvanized Steel | Galvanized Steel | Galvanized Steel | Galvanized Steel | Galvanized Steel | Galvanized Steel | Galvanized Steel | Galvanized Steel | Galvanized Steel | Galvanized Steel |
Galvalume | Magnesium | Zinc | Galvanized Steel | Same Metal | Galvalume | Galvalume | Galvalume | Galvalume | Galvalume | Galvalume | Galvalume | Galvalume | Galvalume | Galvalume | Galvalume | Galvalume | Galvalume | Galvalume | Galvalume | Galvalume |
Aluminum | Magnesium | Zinc | Galvanized Steel | Galvalume | Same Metal | Aluminum | Aluminum | Aluminum | Aluminum | Aluminum | Aluminum | Aluminum | Aluminum | Aluminum | Aluminum | Aluminum | Aluminum | Aluminum | Aluminum | Aluminum |
Steel (Carbon) | Magnesium | Zinc | Galvanized Steel | Galvalume | Aluminum | Same Metal | Steel (Carbon) | Steel (Carbon) | Steel (Carbon) | Steel (Carbon) | Steel (Carbon) | Steel (Carbon) | Steel (Carbon) | Steel (Carbon) | Steel (Carbon) | Steel (Carbon) | Steel (Carbon) | Steel (Carbon) | Steel (Carbon) | Steel (Carbon) |
Cast Iron | Magnesium | Zinc | Galvanized Steel | Galvalume | Aluminum | Steel (Carbon) | Same Metal | Cast Iron | Cast Iron | Cast Iron | Cast Iron | Cast Iron | Cast Iron | Cast Iron | Cast Iron | Cast Iron | Cast Iron | Cast Iron | Cast Iron | Cast Iron |
Lead | Magnesium | Zinc | Galvanized Steel | Galvalume | Aluminum | Steel (Carbon) | Cast Iron | Same Metal | Lead | Lead | Lead | Lead | Lead | Lead | Lead | Lead | Lead | Lead | Lead | Lead |
Tin | Magnesium | Zinc | Galvanized Steel | Galvalume | Aluminum | Steel (Carbon) | Cast Iron | Lead | Same Metal | Tin | Tin | Tin | Tin | Tin | Tin | Tin | Tin | Tin | Tin | Tin |
Terne-coated Stainless Steel |
Magnesium | Zinc | Galvanized Steel | Galvalume | Aluminum | Steel (Carbon) | Cast Iron | Lead | Tin | Same Metal | Terne-coated Stainless Steel |
Terne-coated Stainless Steel |
Terne-coated Stainless Steel |
Terne-coated Stainless Steel |
Terne-coated Stainless Steel |
Terne-coated Stainless Steel |
Terne-coated Stainless Steel |
Terne-coated Stainless Steel |
Terne-coated Stainless Steel |
Terne-coated Stainless Steel |
Stainless Steel (300 Series, Active) |
Magnesium | Zinc | Galvanized Steel | Galvalume | Aluminum | Steel (Carbon) | Cast Iron | Lead | Tin | Terne-coated Stainless Steel |
Same Metal | Stainless Steel (300 Series, Active) |
Stainless Steel (300 Series, Active) |
Stainless Steel (300 Series, Active) |
Stainless Steel (300 Series, Active) |
Stainless Steel (300 Series, Active) |
Stainless Steel (300 Series, Active) |
Stainless Steel (300 Series, Active) |
Stainless Steel (300 Series, Active) |
Stainless Steel (300 Series, Active) |
Brass | Magnesium | Zinc | Galvanized Steel | Galvalume | Aluminum | Steel (Carbon) | Cast Iron | Lead | Tin | Terne-coated Stainless Steel |
Stainless Steel (300 Series, Active) |
Same Metal | Brass | Brass | Brass | Brass | Brass | Brass | Brass | Brass |
Bronze | Magnesium | Zinc | Galvanized Steel | Galvalume | Aluminum | Steel (Carbon) | Cast Iron | Lead | Tin | Terne-coated Stainless Steel |
Stainless Steel (300 Series, Active) |
Brass | Same Metal | Bronze | Bronze | Bronze | Bronze | Bronze | Bronze | Bronze |
Copper | Magnesium | Zinc | Galvanized Steel | Galvalume | Aluminum | Steel (Carbon) | Cast Iron | Lead | Tin | Terne-coated Stainless Steel |
Stainless Steel (300 Series, Active) |
Brass | Bronze | Same Metal | Copper | Copper | Copper | Copper | Copper | Copper |
Cupronickel | Magnesium | Zinc | Galvanized Steel | Galvalume | Aluminum | Steel (Carbon) | Cast Iron | Lead | Tin | Terne-coated Stainless Steel |
Stainless Steel (300 Series, Active) |
Brass | Bronze | Copper | Same Metal | Cupronickel | Cupronickel | Cupronickel | Cupronickel | Cupronickel |
Monel | Magnesium | Zinc | Galvanized Steel | Galvalume | Aluminum | Steel (Carbon) | Cast Iron | Lead | Tin | Terne-coated Stainless Steel |
Stainless Steel (300 Series, Active) |
Brass | Bronze | Copper | Cupronickel | Same Metal | Monel | Monel | Monel | Monel |
Nickel | Magnesium | Zinc | Galvanized Steel | Galvalume | Aluminum | Steel (Carbon) | Cast Iron | Lead | Tin | Terne-coated Stainless Steel |
Stainless Steel (300 Series, Active) |
Brass | Bronze | Copper | Cupronickel | Monel | Same Metal | Nickel | Nickel | Nickel |
Stainless Steel (400 Series, Passive) |
Magnesium | Zinc | Galvanized Steel | Galvalume | Aluminum | Steel (Carbon) | Cast Iron | Lead | Tin | Terne-coated Stainless Steel |
Stainless Steel (300 Series, Active) |
Brass | Bronze | Copper | Cupronickel | Monel | Nickel | Same Metal | Stainless Steel (400 Series, Passive) |
Stainless Steel (400 Series, Passive) |
Stainless Steel (300 Series, Passive) |
Magnesium | Zinc | Galvanized Steel | Galvalume | Aluminum | Steel (Carbon) | Cast Iron | Lead | Tin | Terne-coated Stainless Steel |
Stainless Steel (300 Series, Active) |
Brass | Bronze | Copper | Cupronickel | Monel | Nickel | Stainless Steel (400 Series, Passive) |
Same Metal | Stainless Steel (300 Series, Passive) |
Titanium | Magnesium | Zinc | Galvanized Steel | Galvalume | Aluminum | Steel (Carbon) | Cast Iron | Lead | Tin | Terne-coated Stainless Steel |
Stainless Steel (300 Series, Active) |
Brass | Bronze | Copper | Cupronickel | Monel | Nickel | Stainless Steel (400 Series, Passive) |
Stainless Steel (300 Series, Passive) |
Same Metal |