Table of Contents
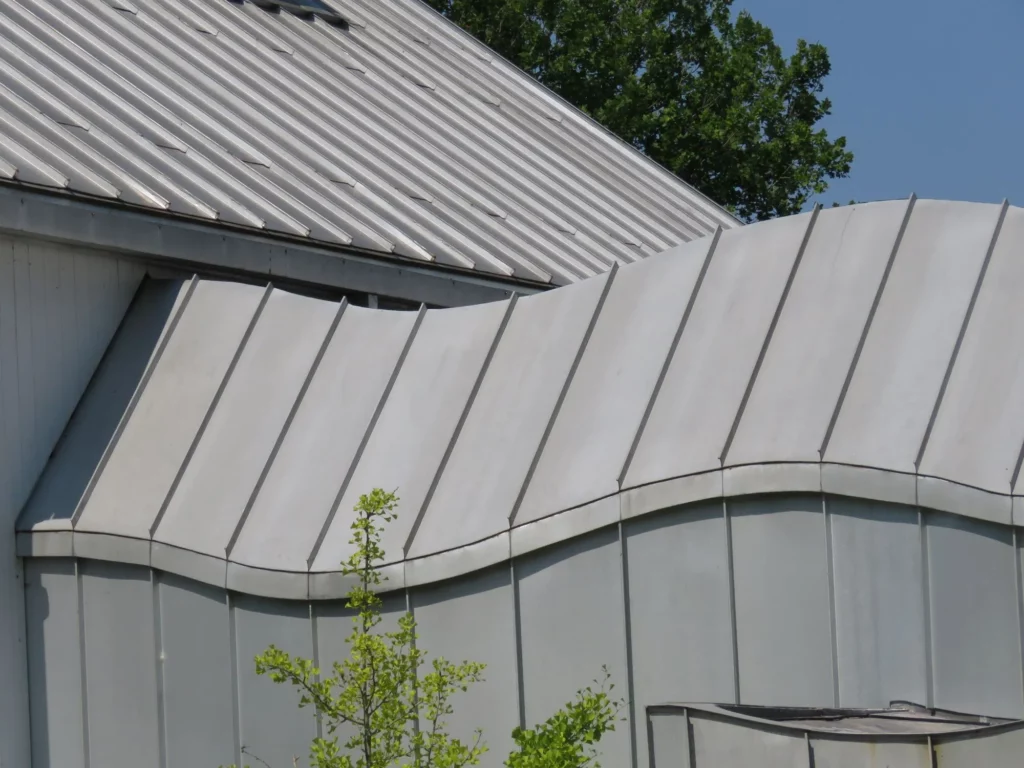
Introduction
Metal roofing is a very large category. There are more metal roofing products available than there are for any other type of roofing material. Metal roof panels are made in many different sizes, from many different metals, with many different panel profiles, with many different coatings, for use in many different situations.
In this article I am going to provide important general information about the different types of metals used to manufacture metal roofing panels. If you are planning on having a metal roof installed, figuring out which type of metal you want to use is one of the first things you should do, and this article should help you do that.
The principal metals used in roofing are aluminum, copper, lead, stainless steel, steel, tin, and zinc. Some of these may be coated with some of the others. Titanium alloys and Monel (nickel-copper alloy) may occasionally be used for extremely niche applications.
The majority of metal roofs in the United States are made of steel sheets with some kind of metallic coating (galvanized, aluminum-zinc alloy, there are others) which are typically finished with a factory-applied paint or coating in just about any color you could want. I’m not going to get into finish coatings or panel profiles here. This article is simply about the metals.
At a Glance: Table of Roofing Metals
Metals Used for Metal Roofing Arranged by Life Expectancy | |||
---|---|---|---|
Metal | Lifespan | Key Features | Common Applications |
Galvanized Steel | 20–50 years | Affordable, zinc coating provides sacrificial protection but vulnerable to scratches and moisture. | Agricultural, industrial buildings, budget-conscious homes. |
Aluminized Steel | 30–60 years | Aluminum coating adds heat and corrosion resistance; suitable for moderate environments. | Factories, warehouses, utility buildings. |
Galvalume® | 40–70 years | Aluminum-zinc coating offers superior corrosion resistance, except in ammonia-rich environments. | Residential, commercial, and industrial buildings. |
Terne Metal | 40–70 years | Steel core with tin/lead alloy coating; modern versions use lead-free coatings for durability. | Historic restorations, traditional buildings. |
Aluminum | 40–70 years | Lightweight, rust-resistant, but can dent under impact; excellent for coastal regions. | Coastal homes, modern residential and commercial buildings. |
Lead | 50–100 years | Corrosion-resistant and malleable, but soft and prone to damage. | Flashing, heritage restorations, specialized architectural use. |
Stainless Steel | 50–100+ years | Highly resistant to corrosion, wear, and environmental stresses. | Industrial facilities, modern commercial buildings. |
Zinc | 70–100+ years | Self-healing patina provides excellent durability and low maintenance. | High-end homes, museums, cultural centers. |
Lead-Coated Copper | 80–100+ years | Combines copper’s strength with lead’s corrosion resistance. | Churches, institutional buildings, high-end architecture. |
Terne-Coated Stainless Steel | 80–100+ years | Blends stainless steel strength with traditional terne aesthetics; highly durable. | Institutional and luxury buildings, premium restorations. |
Copper | 80–150+ years | Develops a patina for natural corrosion resistance; unmatched longevity. | Historic landmarks, luxury homes, prestigious buildings. |
Titanium | 100+ years | Lightweight, extremely strong, and corrosion-resistant; suitable for harsh conditions. Very expensive. | High-tech facilities, marine buildings, cutting-edge designs. |
Nickel Alloys (e.g., Monel) | 100+ years | Exceptional corrosion resistance, particularly in industrial and marine environments; very expensive. | Industrial plants, marine structures, specialized applications. |
Aluminum
Aluminum is widely used as a roofing material because it’s very light and has a high resistance to corrosion. It is especially suitable for coastal or industrial environments where high levels of salt, moisture, or pollutants in the environment may accelerate the deterioration of roofing materials made from steel. It does have a lower tensile strength compared to steel; this may limit its use in structural applications.
Aluminum is also a common culprit when galvanic corrosion occurs. Aluminum should not be installed so that it’s in contact, directly or indirectly, with some other common construction metals like copper or steel. Aluminum-compatible roofing accessories like pipe boots or valley flashings plus well-thought-out construction details that prevent this contact are necessary when using aluminum.
Aluminum is typically used to manufacture standing seam panels, corrugated panels, and shingles.
Appearance:
New, uncoated aluminum roofing panels will typically have a bright, silvery finish when first installed, but as they age and the metal oxidizes (forming aluminum’s protective layer), they become a bit dull. This protective layer is often created during the manufacturing process by anodizing the metal, which also improves adhesion for some types of coatings. Aluminum panels are very often pre-painted at the factory to offer a wide range of roof colors as well as to enhance lifespan and performance.
Appropriate for:
- Coastal homes or buildings in areas with high humidity or salt exposure (because of aluminum’s corrosion resistance).
- Lightweight construction projects where structural load is a concern, such as prefabricated homes or mobile buildings.
- Mid-range residential or commercial buildings seeking a durable and moderately priced roofing material.
Aluminum’s light weight and corrosion resistance make it a solid choice for structures in chemically harsh environments, but its relatively high thermal expansion (it has to be able to move a little) and the risk of galvanic corrosion requires careful, informed installation.
Common Issues:
- Galvanic Corrosion: Aluminum is prone to galvanic corrosion when it comes into contact with dissimilar metals like copper or steel in the presence of moisture. Isolation methods, such as the use of protective coatings or non-conductive barriers, must be used if these other materials are necessary.
- Denting: Due to its softness, aluminum can dent more easily than harder metals like steel, particularly in areas with hail or foot traffic. Installers should use extra care when handling aluminum roofing materials.
- Thermal Movement: Aluminum expands and contracts more than most other roofing metals, which can stress and deform fasteners, joints, and panels over time if not properly accounted for during system design and installation.
Lifespan of Aluminum Roof Panels: 40–70 years. Naturally resistant to rust and corrosion due to its oxide layer.
Relative Cost: Medium.
Aluminum is generally more expensive than steel-based roofing materials, including galvanized steel or Galvalume®, but less expensive than premium metals like copper or zinc.
Read more about aluminum roofing costs.
Incompatible Materials:
- Copper and copper alloys (e.g., brass and bronze)
- Carbon steel and galvanized steel
- Stainless steel (unless electrically insulated)
- Mortar, concrete, and other highly alkaline substances
Aluminum is highly reactive with copper, causing galvanic corrosion when in direct contact or in the presence of water. Similarly, contact with carbon steel and galvanized steel can lead to the rapid deterioration of aluminum in wet conditions.
Recommended Fasteners:
- Aluminum fasteners
- Stainless steel fasteners (grade 304 or 316)
Aluminum fasteners are ideal for maintaining uniformity and avoiding galvanic corrosion. Stainless steel fasteners are also acceptable if they can be insulated from direct contact with the aluminum panel.
Thermal Expansion/Contraction:
Aluminum has a relatively high coefficient of thermal expansion (CTE), approximately 13 x 10⁻⁶ in/in/°F. This results in a lengthwise dimensional change of about 0.156 inches for a 20-foot-long aluminum panel during a 50°F temperature change. This means it expands and contracts significantly with temperature changes, more than most other metals used in roofing. This high expansion rate means that specific fasteners and clips must be used and installed in a way that accommodates this movement. Aluminum roofing often requires properly designed expansion joints and slip sheets to accommodate movement without causing buckling or stress at connections.
Copper
Copper has long (millennia!) been appreciated as a roofing material because of its durability, workability, and attractiveness; it often develops a distinctive, protective green patina as the surface of the material oxidizes over time. It is fire-resistant and highly resistant to corrosion (beyond the patina itself), even in harsh environments.
It comes with a high price (both the material itself as well as the skilled labor needed to install a copper roof correctly are expensive) which restricts its use to high-end applications. Copper can be damaged by highly-acidic rain or certain wood treatment chemicals, and care must be taken to keep it out of contact with incompatible materials such as aluminum or galvanized steel (which can lead to galvanic corrosion).
Copper is commonly used for standing seam panels, flat lock panels, and shingles.
The Copper Development Association is a great source of information on copper roofing.
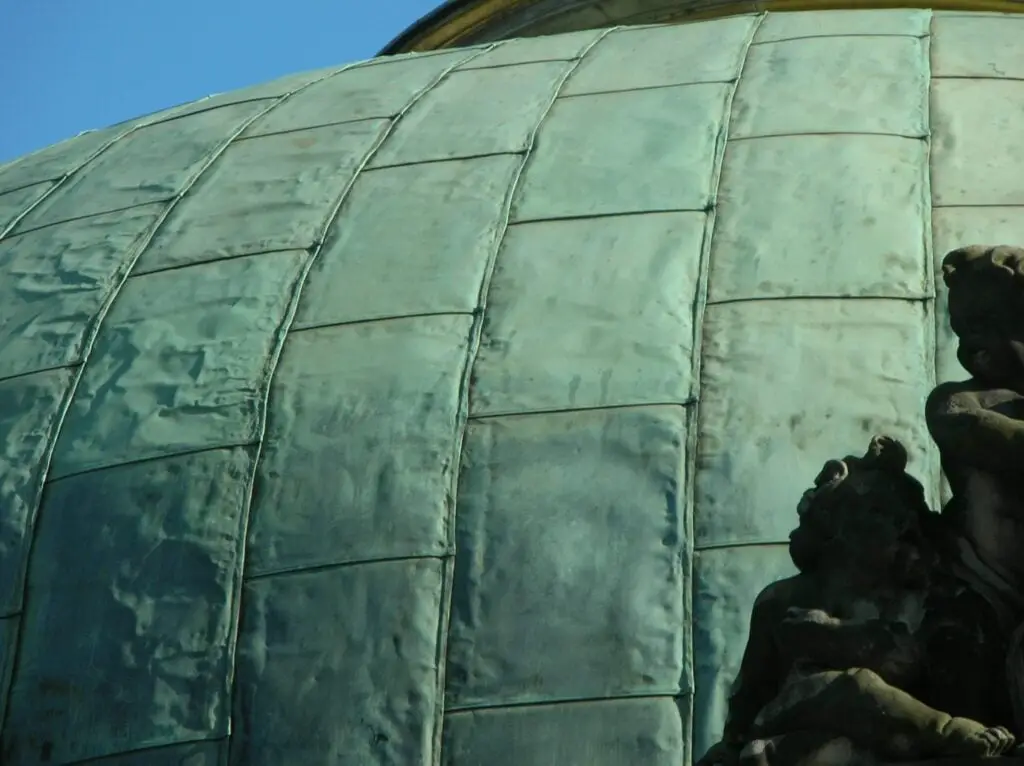
Appearance:
Copper starts out with a shiny, reddish-brown metallic sheen that gradually develops a dark brown, purple, and eventually green patina as it weathers. Copper is almost always left uncoated to allow the patina to form naturally, although pre-patinated panels are available for an aged look immediately upon installation.
Appropriate for:
- High-end residential homes, historical restorations, and other architecture that wants to emphasize stateliness and tradition.
- Churches, schools, other government buildings, and university buildings where a long service life (without much concern for the cost) and the distinctive patina are desirable.
- Custom-designed or specialty buildings requiring extremely durable, good-looking roofing materials.
The high cost of copper roofing limits its use to buildings where such an investment makes sense, but its long lifespan and desirable appearance often justify the expense.
Common Issues:
- Staining: Water runoff from copper panels can stain adjacent materials such as concrete or light-colored siding due to the copper oxides on the surface of the panels.
- Electrolytic Corrosion: Direct contact with metals like steel or aluminum can cause rapid corrosion of the copper or the other metal. Proper construction detailing is critical to avoiding this.
- Copper Theft: Copper’s high value can make it a target for thieves, especially on less-secure properties with easy roof access.
Lifespan of Copper Roof Panels: 80–150+ years. The useful life of a copper roof system typically varies according to the thickness of the copper sheet used to make the panels. Thicker copper = longer useful life.
Relative Cost: Very High.
Copper is among the most expensive roofing materials because it’s made from copper, which is more expensive than almost any other raw materials used to make roofing products. The labor costs more, too, as copper roof installation requires relatively highly trained workers who are skilled at copper-specific techniques like seam soldering, for instance.
Incompatible Materials:
- Aluminum
- Galvanized steel and zinc
- Lead-coated metals
- Unprotected steel
Copper promotes galvanic corrosion in metals lower in the galvanic series, such as aluminum and zinc. Drainage from copper surfaces can corrode underlying or nearby incompatible metals.
Recommended Fasteners:
- Copper nails or screws
- Silicon bronze fasteners
Copper fasteners prevent galvanic corrosion and match the durability of the roofing material (you don’t want your roofing fasteners to fail before the roof panels!). Silicon bronze fasteners are an acceptable alternative with similar corrosion resistance and strength.
Thermal Expansion/Contraction:
Copper has a moderate CTE of about 9.4 x 10⁻⁶ in/in/°F, which is less than aluminum but still significant. This results in a lengthwise dimensional change of about 0.113 inches for a 20-foot-long copper panel during a 50°F temperature change. Copper roofs are less prone to warping or buckling compared to aluminum, but proper detailing is still essential, especially for large panels or long seams, to accommodate thermal movement. Soldered joints and standing seams are often used to manage expansion.
(Copper) Lead-Coated Copper
This material combines the benefits of copper (workability, long service life, relative strength) with a protective lead coating, improving its resistance to certain forms of corrosion and giving it a classic gray appearance. It is often used in high-end projects, although its use may be restricted due to environmental concerns associated with lead. It is particularly well-suited for use on low-slope parts of slate roofs, such as flat-topped dormers, or as a material for slate roof valley flashing and gutters because of its appropriate lifespan and color. Proper disposal and handling of lead-coated copper are necessary to minimize environmental concerns.
A big benefit of using lead-coated copper instead of copper alone is that water runoff from a lead-coated copper roof does not cause stains on the outside of the building over time to the extent that runoff from a pure copper roof does.
Lead-coated copper is often used in flat seam panels, standing seam panels, and specialty panels for custom architectural applications.
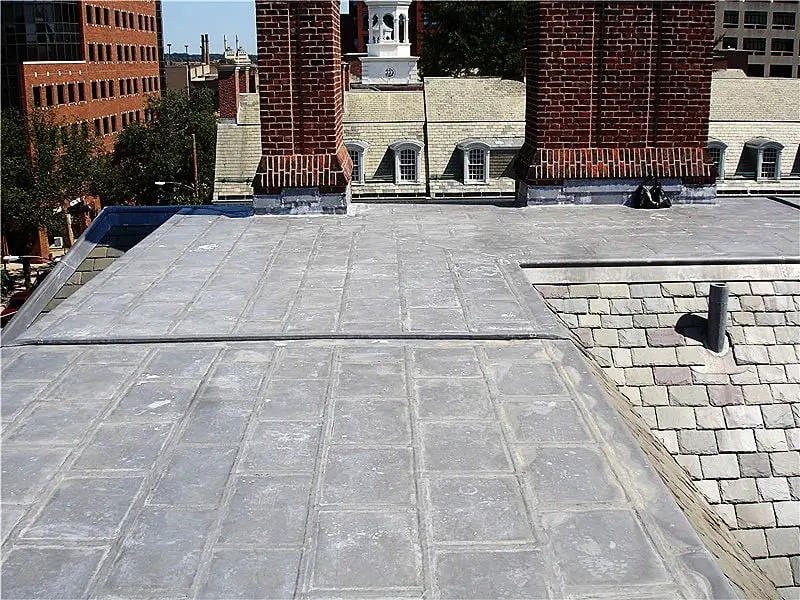
Appearance:
Lead-coated copper has a muted gray finish due to the lead coating. This material is not typically painted and relies on the lead coating to maintain a consistent stately appearance.
Appropriate for:
- Historic restorations where traditional roofing materials are required.
- Premium commercial or institutional buildings where the durability of copper is desired, but the green color is not.
- Roofs where compatibility with traditional materials like slate is important.
Lead-coated copper roofing keeps the strong points of copper while adding further resistance in certain corrosive environments. It also provides a color alternative, gray instead of green.
Common Issues:
- Lead Contamination: Handling and disposal of lead-coated copper must be done carefully to avoid environmental contamination.
- Coating Wear: Over time, the lead coating can degrade or wear thin, exposing the underlying copper.
- Compatibility Issues: Like copper, lead-coated copper can corrode when improperly installed in contact with incompatible materials like aluminum or uncoated steel.
Lifespan of Lead-Coated Copper Roof Panels: 80–100+ years. The lead may eventually, in the very long term, wear off. Adds the corrosion resistance of lead to the structural strength of copper. Also used for flashing, guttering, and specialized architectural elements.
Relative Cost: Very High.
Lead-coated copper combines the high cost of copper with the added expense of coating it with lead. This material is typically reserved for special applications or very high-end architectural projects.
Incompatible Materials:
- Aluminum
- Galvanized steel and zinc
- Direct contact with uncoated copper
Lead-coated copper carries similar risks to copper. It can promote galvanic corrosion in aluminum and zinc. Believe it or not, care should also be taken to avoid direct contact with bare copper roofing accessories like flashings or copper conduits, as the lead coating can deteriorate.
Recommended Fasteners:
- Copper nails or screws
- Stainless steel fasteners (grade 316, with proper insulation)
Copper fasteners match the material’s properties, certain types of stainless steel fasteners can be used if direct contact with the lead-coated surface is avoided to minimize galvanic reactions.
Thermal Expansion/Contraction:
Lead-coated copper retains the thermal properties of copper, with a similar CTE of 9.4 x 10⁻⁶ in/in/°F. This results in a lengthwise dimensional change of about 0.113 inches for a 20-foot-long lead-coated copper panel during a 50°F temperature change. The lead coating does not significantly affect thermal movement. Exercise care at expansion joints to avoid compromising the lead layer while accommodating copper’s natural thermal movement.
Lead
Lead has been valued as a building material throughout history because it’s easy to work and exceptionally resistant to corrosion. Lead is often used for roofing accessories like flashing, where a highly malleable material is needed to get the best result. Lead pipe boots are still extremely common because of how easy it is to fold the lead sheet down into the top of the vent pipe.
Its use is typically restricted due to environmental and health concerns. Lead is very heavy and exceptionally durable but susceptible to creep deformation over time, particularly in warmer climates. Lead is very soft, and it should be handled carefully during installation and maintenance to prevent damaging it.
Lead is mainly used for roofing accessories and specialty panels, such as flashing, gutters, and custom roof detailing, rather than full roofing panels. You may still see it used for flat seam panels on small flat roofs.
Appearance:
Lead has a bluish-gray color that can darken over time. Lead roofing products often develop a whitish surface layer due to the formation of lead carbonate as the lead reacts to moisture in the air over time. Lead carbonate is powdery and can stain other parts of the roof that are down-slope from it. Lead isn’t normally painted or coated, as its natural oxidation forms a protective layer.
Appropriate for:
- Historic or traditional structures requiring authentic restoration, such as cathedrals or landmarks. The roof on the Notre Dame cathedral was notably rebuilt with lead (amid some controversy).
- Buildings with complex roofing details, as lead’s malleability makes it better than almost anything else for flashing and other applications where the material has to conform faithfully to the shape of some other building component.
Due to health and environmental concerns, lead is rarely used for entire roofs these days but it remains a useful option in restoration and specialty applications.
Common Issues:
- Environmental Concerns: Lead poses significant environmental and health risks, necessitating careful handling, installation, and eventual disposal.
- Creep Deformation: Lead panels can deform under their own weight over time, especially in warmer climates, leading to sagging or gaps.
- Corrosion from Acids: Acidic rain or exposure to certain chemicals can cause lead to corrode, reducing its lifespan.
Lifespan of Lead Roofing Products: 50–100 years. Lead is highly resistant to corrosion but it’s also relatively soft, which makes it susceptible to physical damage. It’s better used for flashing rather than full roof systems.
Relative Cost: High.
Since lead isn’t normally used as a primary roofing material, it’s not fair to compare it to other roofing metals on roof system price. But roofing accessories made out of lead can be very pricy when compared to alternatives.
Incompatible Materials:
- Aluminum
- Zinc
- Galvanized steel
Lead can cause galvanic corrosion in aluminum and zinc, particularly in wet conditions. While durable, lead’s chemical reactivity can lead to deterioration when exposed to some metals in direct contact.
Recommended Fasteners:
- Lead-head nails
- Stainless steel fasteners (grade 316)
Lead-head nails (nails with a lead-coated head) are commonly used for material uniformity and corrosion resistance. Stainless steel fasteners can provide added strength and corrosion protection in compatible assemblies.
Thermal Expansion/Contraction:
Lead exhibits a relatively high CTE of about 16.2 x 10⁻⁶ in/in/°F. This results in a lengthwise dimensional change of about 0.194 inches for a 20-foot-long sheet of lead during a 50°F temperature change. Lead’s malleability allows it to tolerate thermal movement without cracking, but creep (permanent deformation under stress) can occur over time, especially in warmer climates. Installation should account for its thermal behavior to avoid stress on fasteners and seams.
Stainless Steel
Stainless steel is an excellent roofing material for areas that commonly experience hail or high winds or where the roof will be exposed to high levels of pollutants, thanks to its relatively high strength and corrosion resistance. Stainless steel is available in several grades, with higher-grade alloys having better resistance to specific corrosive agents like chloride in coastal areas. Stainless steel roof installations should be professionally specified and detailed to minimize the risk of stress corrosion cracking and must be installed with compatible fasteners to prevent galvanic reactions.
Stainless steel is used to produce standing seam panels, corrugated panels, and custom fabricated panels, typically for modern architectural designs and industrial buildings.
Appearance:
Stainless steel roofing is available in finishes ranging from polished and reflective to brushed or matte. It’s silvery, shiny and can stay that way, although it typically becomes a bit more dull over time. While not typically painted, stainless steel can be coated or tinted. Its corrosion resistance ensures that the surface maintains its appearance very well over time.
Appropriate for:
- Commercial and industrial buildings such as warehouses or factories in locations with harsh weather or corrosive pollutants.
- Modernistic residential or commercial designs that call for a bright shiny roof.
- Structures in regions with extreme weather fluctuations, such as high-snow or high-wind areas.
Stainless steel’s strength and corrosion resistance make it a good roofing choice for challenging environments and long-lasting applications.
Common Issues:
- Stress Corrosion Cracking: Stainless steel can develop cracks in environments with high chloride levels, such as coastal areas, especially if the material is under stress.
- Galvanic Corrosion: Stainless steel can cause corrosion in adjacent metals, like aluminum or galvanized steel, if not properly separated.
- Surface Scratches: Polished finishes on stainless steel can show scratches, which may compromise its corrosion resistance if the protective chromium oxide layer is damaged.
Lifespan of Stainless Steel Roof Panels: 50–100+ years. Extremely resistant to corrosion and wear. Ideal for corrosive environments, including coastal or industrial areas.
Relative Cost: High.
Stainless steel roofing is more expensive than regular carbon steel or aluminum, but not as expensive as zinc or copper. Installation costs are also higher, as the material is harder to work with and requires experienced skilled labor.
Incompatible Materials:
- Aluminum (without proper separation in wet conditions)
- Galvanized steel and zinc (especially in high-salt environments)
- Carbon steel (prone to rapid corrosion when coupled with stainless steel)
Stainless steel’s high position in the galvanic series can cause significant corrosion in aluminum, zinc, and carbon steel if proper electrical isolation is not maintained.
Recommended Fasteners:
- Stainless steel screws or nails (grade 304 or 316, depending on exposure conditions)
Stainless steel fasteners are the best match for stainless steel panels, as they will be compatible under all conditions.
Thermal Expansion/Contraction:
Stainless steel has a moderate CTE of approximately 9.6 x 10⁻⁶ in/in/°F, but it does vary a little depending on the alloy. This results in a lengthwise dimensional change of about 0.115 inches for a 20-foot-long stainless steel panel during a 50°F temperature change. Thermal expansion is manageable but must still be considered in designs involving large panels or long spans. Fasteners and joints must allow for movement to avoid stress cracking or distortion.
(Stainless Steel) Terne-Coated Stainless Steel
Terne-coated stainless steel is a specialty material used for roofing due to its exceptional durability. The product consists of stainless steel sheet that is coated with terne, traditionally a lead-tin mixture, although terne coatings today are lead-free, using a tin-zinc alloy or almost pure tin. It offers exceptional corrosion resistance as the stainless steel substrate already provides robust corrosion resistance, especially in marine or industrial environments, and the terne coating acts as a sacrificial layer, further improving the material’s performance.
Terne-coated stainless steel should be regularly inspected and maintained to make sure that the protective coating remains intact; damage or wear of the coating can expose the underlying stainless steel.
Terne-coated stainless steel is commonly used to make standing seam panels and flat seam panels, as well as specialty architectural panels.
Appearance:
This material features a dull gray finish created by its tin or (on older roofs) its tin-lead or tin-zinc alloy coating. It is not typically painted, as the terne coating itself provides both protection and the desired look.
Appropriate for:
- Traditional or modern buildings where a long-lasting gray matte finish is wanted.
- High-end residential and commercial projects that prefer stainless steel with a more traditional matte gray appearance.
- Roofs that require exceptionally high corrosion resistance.
The terne coating is often considered to improve stainless steel’s visual appeal while increasing its durability.
Common Issues:
- Coating Damage: Scratches or wear on the terne coating can expose the stainless steel underneath, possibly making it vulnerable to localized corrosion.
- Discoloration: The coating can discolor unevenly over time, affecting the way the roof looks.
- Maintenance Needs: Regular inspections and maintenance are recommended to ensure the coating remains intact, although terne-coated stainless steel generally requires less maintenance than most other materials.
Lifespan of Terne-Coated Stainless Steel Roof Panels: 80–100+ years. Longer than uncoated stainless steel due to the additional protection of the sacrificial terne coating.
Relative Cost: High.
The cost of terne-coated stainless steel panels is slightly higher than standard stainless steel due to the added protective coating. It should be considered a premium option that may well be worth the price for certain projects.
Incompatible Materials:
- Aluminum
- Zinc and galvanized steel (especially if the coating has deteriorated or been damaged)
The stainless steel core minimizes compatibility issues, but the tin in the terne coating can react poorly with aluminum and zinc in the presence of moisture.
Recommended Fasteners:
- Stainless steel screws or nails (grade 304 or 316)
Stainless steel fasteners are the most compatible choice, as they can last as long as the roof panels and won’t cause galvanic corrosion.
Thermal Expansion/Contraction:
The CTE of terne-coated stainless steel is similar to standard stainless steel, approximately 9.6 x 10⁻⁶ in/in/°F. As with regular stainless steel, this results in a lengthwise dimensional change of about 0.115 inches for a 20-foot-long panel during a 50°F temperature change. The tin or tin-lead coating does not significantly influence the material’s thermal behavior. Proper installation practices, such as expansion joints and floating clips, are necessary to accommodate movement.
(Steel) Aluminized Steel
Aluminized steel is regular carbon steel coated with aluminum. The aluminum coating on aluminized steel is typically applied through a process known as hot-dip coating, where the steel sheet is immersed in molten aluminum. Aluminized steel has excellent corrosion resistance and excellent heat resistance, much higher heat resistance than galvanized steel, for example. It is typically used in high-heat environments where superior thermal reflectivity is desired and long-term performance in hot conditions is a concern. If the surface is damaged and the aluminum coating is compromised, the steel substrate will be exposed to corrosion in those locations (just like with galvanized steel).
Aluminized steel is used to make corrugated panels and standing seam panels, particularly for industrial and agricultural buildings.
Appearance:
Basic aluminized steel has a silvery, metallic finish because of its aluminum coating. It can also be factory-coated (pre-painted) with a number of different colors and finishes.
Appropriate for:
- Commercial or industrial buildings where keeping costs down is a major priority, but thermal reflectivity and corrosion resistance that exceeds that of galvanized steel is also important.
- Residential garages, workshops, or barns needing a durable but affordable metal roofing option.
- Utility buildings or temporary structures where decent performance is required at a lower cost.
Aluminized steel offers a good balance between affordability and performance, so it’s a solid option for cost-conscious applications.
Common Issues:
- Coating Damage: If the aluminum coating is scratched or punctured, the underlying steel can start to rust.
- Edge Corrosion: Cut edges are particularly prone to corrosion if not sealed or protected. This is a particular concern at roof penetrations installed later by amateur roofers or other trades. All cut edges should have a protective coating applied after the cut is made.
- Thermal Cycling: In some cases, repeated heating and cooling cycles can stress the bond between the aluminum coating and the steel substrate, leading to delamination. This is something to watch out for during maintenance inspections. The two materials do have different rates of thermal expansion.
Lifespan of Aluminized Steel Roof Panels: 30–60 years. These roof panels combine the strength of steel with the corrosion resistance of aluminum. They wear out faster if the coating is damaged. Maintenance inspections and the prompt treatment with an anti-corrosion paint at any damaged locations will help get the maximum life out of aluminized steel roof panels.
Relative Cost: Medium-Low.
Aluminized steel is moderately priced and generally less expensive than stainless steel or non-steel materials.
Incompatible Materials:
- Copper and copper alloys
- Zinc and galvanized steel (if the protective aluminum coating is compromised)
- Stainless steel (direct contact with the aluminum coating should be avoided)
- Contact with mortar, concrete, and other highly alkaline substances should be avoided
Aluminized steel relies on its aluminum coating for protection. If this layer is damaged, the underlying steel becomes vulnerable to galvanic corrosion, especially near dissimilar metals.
Recommended Fasteners:
- Stainless steel screws or nails (grade 304 or 316). Use rubber or plastic washers to separate the materials.
- Aluminized steel fasteners
Stainless steel fasteners offer corrosion resistance, while aluminized steel fasteners maintain material uniformity and are suitable for drier environments with lower corrosion risks.
Thermal Expansion/Contraction:
Aluminized steel has a CTE of about 6.7 x 10⁻⁶ in/in/°F, similar to plain carbon steel. This results in a lengthwise dimensional change of about 0.08 inches for a 20-foot-long aluminized steel panel during a 50°F temperature change. The aluminum coating has minimal impact on its expansion properties. This relatively low thermal expansion means aluminized steel is less prone to distortion under temperature changes.
(Steel) Galvalume®
Galvalume® refers to steel products with an aluminum-zinc alloy coating, which have better corrosion resistance than traditional galvanized steel. Galvalume® is especially effective in marine environments and industrial areas with heavy localized pollutants in the air.
Like other coated steel products, Galvalume® can be vulnerable to edge creep corrosion. “Edge creep corrosion” refers to the progressive corrosion that occurs at the unprotected edges of coated sheet metals, where the protective coating is either absent or damaged, especially at edges that have been cut or trimmed by the installers. Galvalume® should not be used in direct contact with concrete or other alkaline materials.
Galvalume® is a registered trademark of BIEC International Inc. The Galvalume® alloy is 55% aluminum, 43.4% zinc, and 1.6% silicon. There are other 55% aluminum/zinc alloy coatings available, but they are all commonly referred to as “Galvalume”.
Galvalume® is a popular material for corrugated panels, standing seam panels, and ribbed panels, and it’s widely used in both residential and commercial roofing.
Appearance:
Unpainted Galvalume® has a smooth, shiny, metallic finish with a spangled “snowflake” pattern, similar to galvanized steel. It is available uncoated or pre-painted in many different colors.
Appropriate for:
- Homeowners who want a durable and budget-friendly metal roof.
- Agricultural buildings such as barns or storage sheds.
- Light industrial or commercial buildings needing cost-effective, long-lasting roofing.
Galvalume® is a popular choice for its corrosion resistance and affordability; it’s an option for a wide range of structures.
Common Issues:
- Edge Creep Corrosion: The edges of Galvalume® panels can experience corrosion over time, particularly in harsh environments.
- Surface Damage: Scratches or dents that damage the protective coating can leave the steel core vulnerable to rust.
- Incompatibility with Concrete or Alkaline Materials: Direct contact with concrete or other alkaline materials can accelerate corrosion.
- Vulnerable to Ammonia: High levels of ammonia in the air can degrade the coating, so it isn’t typically suitable for roofing on farm buildings where animal manure is present.
Lifespan of Galvalume® Roof Panels: 40–70 years. Combines aluminum and zinc in its coating, offering superior corrosion resistance compared to galvanized steel.
Relative Cost: Low-Medium.
Galvalume® is competitively priced and considered one of the most cost-effective types of metal roofing. Its affordability makes it popular for both residential and commercial jobs.
Incompatible Materials:
- Copper and copper alloys
- Uncoated carbon steel
- Stainless steel
- Direct contact with concrete or alkaline materials
The aluminum-zinc coating of Galvalume® protects the steel but is vulnerable to galvanic reactions with copper and high-pH substances, like wet concrete.
Recommended Fasteners:
- Stainless steel screws or nails (grade 304 or 316)
- Coated steel fasteners (zinc-aluminum coating or equivalent)
Stainless steel fasteners prevent corrosion at connection points. Coated steel fasteners with a compatible finish are also good. Galvanized fasteners are not recommended.
Thermal Expansion/Contraction:
Galvalume® has a CTE of approximately 6.7 x 10⁻⁶ in/in/°F, consistent with other steel products. This results in a lengthwise dimensional change of about 0.08 inches for a 20-foot-long panel during a 50°F temperature change. Its low expansion rate reduces the risk of damage due to thermal stress.
(Steel) Galvanized Steel
Galvanized steel roof panels are steel panels that are coated with a layer of zinc, typically using the hot-dip method (electroplating results in a thinner zinc layer, which isn’t very good for roofing). Galvanized steel roof panels are very often pre-painted before they are sold to the consumer, and they come in all kinds of colors.
Galvanized steel is the cheapest and most common metal roofing material. It performs well in mild environments but may corrode in areas with high humidity, industrial pollutants, or exposure to salt spray. Over time, the zinc coating may wear away, allowing the underlying steel to rust. Regular maintenance and protective coatings can extend its lifespan.
Galvanized steel is often used for corrugated panels, ribbed panels, and standing seam panels, and it’s the most common material for low-cost metal roofing.
Appearance:
New unpainted galvanized steel is a shiny, metallic gray and silver material with a distinct spangled surface created by the zinc coating. As it ages, the surface weathers to a more uniform dull, matte gray. It’s normally pre-painted or coated at the factory to provide color options (and additional protection).
Appropriate for:
- Basic residential homes or rental properties.
- Agricultural or utility buildings such as barns, garages, and workshops.
- Temporary or semi-permanent structures where there’s no sense spending any more on the roofing than you have to.
Galvanized steel may require more careful maintenance than other materials to get the full amount of useful service life out of it.
Common Issues:
- Coating Erosion: Over time, the zinc coating can wear away, especially in areas with heavy rain or acidic conditions, leaving the steel vulnerable to rust.
- Rust Formation: If the coating is damaged or improperly applied, rust can develop on the underlying steel.
- Shorter Lifespan in Coastal Areas: Salt spray can quickly degrade the zinc coating, reducing the lifespan of galvanized steel in marine environments. Aluminum panels are strongly recommended as a substitute in these conditions.
Lifespan of Galvanized Steel Roof Panels: 20–50 years. The steel panels are protected by a zinc coating, which provides sacrificial corrosion resistance. The durability depends on the coating thickness and environmental conditions. Vulnerable to scratches that expose the steel core to rust.
Relative Cost: Low.
Galvanized steel is one of the cheapest metal roofing materials, widely used in both residential and commercial applications. While affordable, it typically has a somewhat shorter lifespan compared to other metal roofing materials like Galvalume® or aluminum.
Incompatible Materials:
- Copper and copper alloys
- Stainless steel
- Aluminum (if prolonged wet contact occurs)
The zinc coating on galvanized steel corrodes when in contact with copper or copper runoff. It also does not resist corrosion well when paired with stainless steel in wet conditions.
Recommended Fasteners:
- Galvanized steel nails or screws (hot-dip galvanized)
Hot-dip galvanized fasteners match the properties of galvanized panels.
Thermal Expansion/Contraction:
Galvanized steel has a CTE of about 6.7 x 10⁻⁶ in/in/°F, similar to other steel materials. This results in a lengthwise dimensional change of about 0.08 inches for a 20-foot-long galvanized steel panel during a 50°F temperature change. Thermal movement is minimal, but installers must take care that the zinc coating remains undisturbed, especially at fasteners and panel laps, to maintain corrosion resistance.
(Steel) Terne Metal
Traditional terne metal involved a lead-tin alloy coating over carbon steel sheets. Carbon steel began to be replaced by stainless steel in the 1960s. After concerns about environmental lead resulted in anti-lead regulations in the 1970s and 1980s, manufacturers started producing terne made with zinc-tin alloys. Zinc-tin gave way to a pure or almost pure tin coating around 2010. Terne metal available today consists of stainless steel sheet coated with tin.
It is durable and provides a matte appearance that weathers gracefully. Terne metal can be damaged by acidic materials or environments and tin should not be exposed to asphalt-based materials like asphaltic roof coatings or roof cement.
Terne metal is primarily used for standing seam panels, flat seam panels, and specialty architectural panels.
Appearance:
Unpainted terne metal typically has a dull, matte gray appearance. Traditional terne metal roofs were always painted to help preserve the material, so the appearance of a terne metal roof was up to the consumer. Terne made with zinc-tin or pure tin over stainless steel can be painted or left unpainted.
Appropriate for:
- Historical buildings or restorations needing authentic roofing materials.
- Premium residential or commercial structures that are going for a traditional look.
Common Issues:
- Coating Wear: The terne metal coating can degrade over time, especially if exposed to acidic rain or abrasive environments.
- Maintenance Requirements: Regular repainting may be needed to maintain the protective coating and prevent rust.
- Environmental Sensitivity: Traditional lead-tin coatings may face regulatory restrictions, and modern zinc-tin alternatives may not provide the same longevity.
Lifespan of Terne Metal Roof Panels: 40–70 years. Durable in areas with moderate exposure to the elements. The longevity depends on the maintenance of the tin coating.
Relative Cost: Medium-High.
Traditional terne metal, coated with lead-tin, is not produced today, but modern zinc-tin or pure tin terne variants are moderately priced for a specialty material.
Incompatible Materials:
- Aluminum
- Copper and copper alloys
- Zinc (in modern zinc-tin variants, avoid direct contact with uncoated steel)
Traditional lead-based terne is more tolerant of material contact, but modern zinc-tin coatings require care to avoid exposure to reactive metals like copper or bare steel.
Recommended Fasteners:
- Stainless steel screws or nails (grade 316)
- Terne-coated fasteners
Stainless steel fasteners ensure long-term corrosion resistance. Terne-coated fasteners provide compatibility with traditional lead-tin coatings, though modern zinc-tin terne panels require careful fastener selection to avoid galvanic issues.
Thermal Expansion/Contraction:
Terne metal, typically steel with a zinc-tin or lead-tin coating, has a base steel CTE of 6.7 x 10⁻⁶ in/in/°F. This results in a lengthwise dimensional change of about 0.08 inches for a 20-foot-long panel during a 50°F temperature change. The steel core governs thermal behavior, which is relatively stable. Roof system design should accommodate movement to ensure that the protective coating will remain intact at joints and fastener locations to prevent corrosion.
Zinc
Zinc is known for its natural patina which gives the material a stately matte gray appearance. The patina begins to form immediately after installation, and becomes noticeable in a few months to a few years, depending on how humid and/or polluted the location is. The patina serves as a protective layer for the metal, preventing corrosion and allowing it to “self-heal” scratches or minor surface damage.
Zinc is highly resistant to corrosion but it can be adversely affected by acidic conditions, prolonged exposure to standing water, or environments with very high industrial pollutants. Zinc roofs should be designed and installed with good ventilation between the panels and the roof underlayment or deck to avoid issues due to condensation, which may degrade the underside of zinc panels.
Zinc is often used in standing seam panels, flat lock panels, and shingles.
Appearance:
Zinc starts with a shiny, silvery metallic finish that naturally becomes a duller light or medium gray as it patinates. Zinc is not typically painted but can be coated or pre-weathered to ensure a consistent color upon installation.
Appropriate for:
- High-end homes, particularly for people who want a unique yet traditional look.
- Cultural or institutional buildings emphasizing sustainability and a dignified aesthetic.
- Structures in regions with moderate to harsh weather conditions, as zinc’s patina protects against corrosion.
Zinc is often chosen for its anti-corrosion properties and natural gray appearance which is reminiscent of slate roofing. It’s a high-end choice for distinctive or architecturally significant buildings.
Common Issues:
- White Rust: Prolonged exposure to standing water can lead to the formation of white rust, which may degrade the surface.
- Fragility: Zinc can become brittle in extremely cold conditions, making it susceptible to cracking under stress.
- Corrosion from Acidic Conditions: Zinc is vulnerable to corrosion in acidic environments or where runoff from acidic materials (like cedar shingles) occurs.
- Difficult to Find: In the United States, it can be hard to find a manufacturer or supplier who provides zinc roofing. It is also hard to find a roofing contractor with experience installing zinc roofs.
Lifespan of Zinc Roof Panels: 70–100+ years. Self-healing patina provides excellent corrosion resistance and the material requires minimal maintenance. Performs exceptionally well in varied climates but requires proper ventilation to prevent underside corrosion, which can shorten the useful service life of zinc roofing.
Relative Cost: High.
Zinc is a semi-premium roofing material, typically more expensive than steel (but not as much as copper). Besides higher material costs, zinc roof installation is also more expensive due to the need for experienced professionals who may be hard to find.
Incompatible Materials:
- Copper and copper alloys
- Stainless steel
- Lead and lead-coated metals
Zinc corrodes rapidly when in contact with copper or stainless steel. Drainage runoff from copper roofing or copper flashing can also cause zinc to corrode. It is also incompatible with lead in some environments.
Recommended Fasteners:
- Zinc-coated (galvanized) nails or screws
- Stainless steel fasteners (grade 304 or 316, but must be isolated (insulated/separated) from the zinc panels)
Zinc-coated fasteners maintain material compatibility. Stainless steel fasteners may be used with proper isolation to prevent galvanic corrosion.
Thermal Expansion/Contraction:
Zinc has a high CTE of about 17.4 x 10⁻⁶ in/in/°F, slightly higher than lead. This results in a significant lengthwise dimensional change of about 0.209 inches for a 20-foot-long zinc panel during a 50°F temperature change. Zinc panels are prone to thermal movement, especially in large applications. Limited panel lengths and proper system design with expansion joints, sliding clips, and adequate fastening systems is critical to prevent warping or buckling.
Sources
- Gayle, Margot, and Look, David W., Metals in America’s Historic Buildings: Uses and Preservation Treatments. U.S. Department of the Interior, National Park Service, Cultural Resources Preservation Assistance, Washington, D.C., 1992.
- Griffin, C.W., and Fricklas, R.L., Manual of Low-Slope Roof Systems, Fourth Edition. New York: McGraw-Hill, 2006.
- Laaly, Heshmat O. The Science and Technology of Traditional and Modern Roofing Systems. 1st ed., Laaly Scientific Publishing, 1992.
- Leonard-Hawes Real Estate School, Principles of Home Inspection: Roofing. Published by Dearborn Real Estate Education, a Kaplan Professional Company, 2005.
- National Roofing Contractors Association (NRCA), Architectural Sheet Metal and Metal Roofing Manual, Fifth Edition, 2003. Rosemont, IL: National Roofing Contractors Association.
- National Roofing Contractors Association (NRCA), NRCA Manual – Volume Two – Metal Roofing. Fifth Edition Update, 2008. Rosemont, IL: National Roofing Contractors Association.