I participate in the Amazon affiliate program and may earn commissions from purchases made through links on this page.
Table of Contents
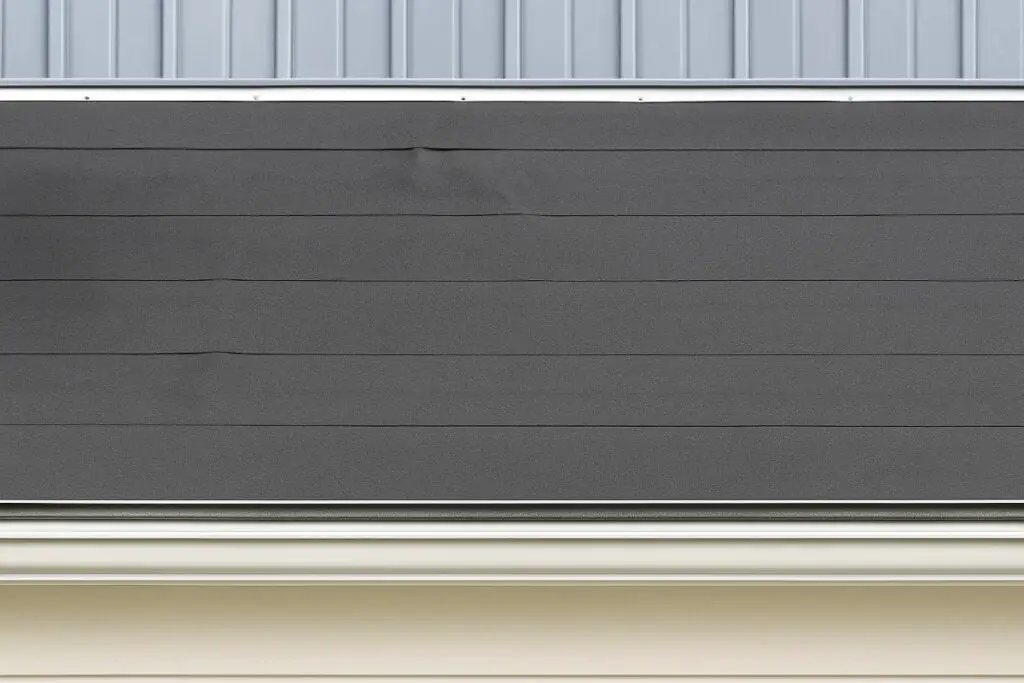
Introduction
The slope of your roof affects how well it sheds rain, snow, and debris, and determines what types of roofing materials are appropriate and allowed by the building code. This article explains what the minimum roof pitch is for mineral-surfaced roll roofing (MSR), a type of asphalt-based roofing commonly used on small residential structures like sheds, garages, porch roofs, and low-cost additions.
Note: Pitch and slope are not technically the same thing, but I’ll be using the terms interchangeably here. The building code uses “slope.”
Roll roofing is a low-cost, asphalt-based roofing material made from a reinforcement mat saturated and coated with asphalt, then covered with mineral granules on the top surface for protection against ultraviolet (UV) radiation. Roll roofing is installed in long, overlapping strips (rolls) and sealed with roofing cement at the seams and laps. It has a short lifespan compared to other roofing materials, and roll roofing is usually used because it’s easy to install, cheap, and good enough for non-critical applications.
Roll roofing is NOT the same thing as modified bitumen roofing, despite their similarities and the confusing information you’ll find on the internet. They are different materials, installed differently, and each has its own separate requirements spelled out in the building code.
See my more detailed general article on roll roofing, as well as my article on modified bitumen, to learn more.
Unlike roofing systems specifically designed for flat roofs, roll roofing is not made or installed so as to resist standing water or hydrostatic pressure. Even though the seams are sealed, it still relies on gravity to shed water and must be installed on roofs with sufficient slope to drain effectively. If it is installed on a roof that is too flat, water can pond, seep through seams, and cause leaks, saturated decking, mold, and structural damage. This can void warranties, violate code, and cost a lot of money to fix.
If you aren’t sure what your roof pitch is, you can get a very cheap, very accurate slope finder from Amazon. I have one of these and it works pretty well.
Minimum Allowed Roof Slope for Mineral-Surfaced Roll Roofing
According to both the International Residential Code and the International Building Code, mineral-surfaced roll roofing can only be installed on roofs with a slope of 1:12 or greater. This means the roof must rise at least 1 inch for every 12 inches of horizontal run. A 1-in-12 slope can also be expressed as a 5° slope or an 8% slope. Anything less is a code violation and a very bad idea. Unlike some other low-slope roofing products, roll roofing may not be used on flat roofs or slopes below 1:12.

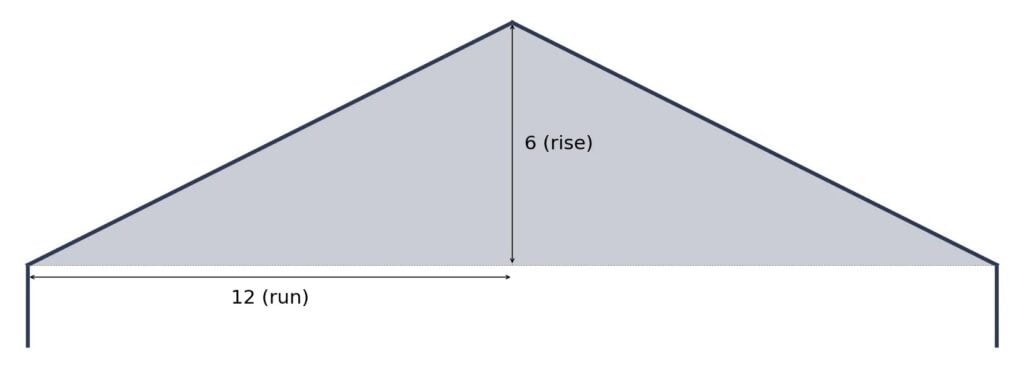
Installing roll roofing on a roof with a slope below 1:12 can lead to serious problems. While the seams are fully sealed using roofing cement or other adhesive, mineral-surfaced roll roofing is a single-layer system and it lacks the multi-ply reinforcement and redundancy needed to handle prolonged water exposure. It is not designed to withstand standing water or hydrostatic pressure, and on flatter roofs, drainage becomes too slow to prevent ponding. Thermal movement also becomes a problem on shallow slopes, since roll roofing is more rigid and less able to flex without cracking or separating at the seams. The unmodified asphalt used in roll roofing is less flexible than modified bitumen roofing, which is designed for flatter surfaces.
Manufacturers prohibit installation below 1:12, and doing so will void the product warranty. It also violates the International Residential Code (IRC), specifically Section R905.5.2, which sets 1:12 as the minimum allowable slope. Improper installation can lead to failed inspections, denied insurance claims, and costly repairs.
While roll roofing does meet code at 1:12, it is not ideal for long-term performance at that minimum slope. It is best used on steeper low-slope roofs where water can drain off more quickly. Based on my experience, roll roofing is better suited for simple roofs (no penetrations, valleys, or anything else that requires flashing) with a pitch of at least 2:12, especially in regions with heavy rain or snow.
Even though it’s allowed, I would not recommend roll roofing on a 1:12 roof. It is often chosen for budget reasons, but for slopes near the minimum, a better choice is modified bitumen, which is engineered specifically for very low-slope applications. Modified bitumen systems are installed with two or three layers (plies) and use polymer-modified asphalt. The multiple layers provide redundancy and exceptional durability. The modified asphalt provides greater elasticity and stronger, more watertight seams, which provides better protection against ponding water, making them far more reliable on flat or nearly flat roofs.
Other Roofing Options for Roof Slopes Under 2:12
Roll roofing cannot be installed on roofs with a slope less than 1:12. It also isn’t the best choice for slopes under 2:12. If your roof is flatter than that, you’ll need to choose a material specifically engineered for very low-slope (“flat”) roof conditions. These systems are designed to be fully watertight and to withstand ponding water, unlike mineral-surfaced roll roofing, which is meant to shed water.
Modified Bitumen
Modified bitumen is one of the best alternatives to roll roofing for low-slope roofs. It’s a durable asphalt-based membrane that includes rubber or plastic modifiers for improved flexibility, strength, and weather resistance. It’s usually installed in two or more layers with staggered seams and can be applied using heat, cold adhesive, or peel-and-stick methods. Modified bitumen is typically surfaced with protective granules and is approved for use on slopes as low as ¼-in-12, making it a true low-slope roofing material. It’s more expensive than roll roofing but much more reliable.
Single-Ply Membranes (TPO, PVC, or EPDM)
Single-ply roofing membranes are typically used on commercial buildings, but they’re also a good solution for residential low-slope roofs. These systems are fully waterproof and can be mechanically fastened, fully adhered, or ballasted. TPO and PVC are available in reflective white or light gray colors, while EPDM is usually black. These systems are more expensive, but they offer long service life and excellent resistance to ponding water. All of them are approved for installation on roofs with slopes down to ¼-in-12.
Standing Seam Metal Roofing
One of the best-performing and best-looking roof systems for lower-sloped residential roofs. Standing seam metal panels can be installed on slopes as low as ¼-in-12 by code (and with manufacturer approval, of course). They shed water effectively, resist ice damming, and have a very long lifespan. But they do cost a lot more than roll roofing, so they probably aren’t what you’re looking for if you were thinking of using roll roofing.
Code Sections: Minimum Roof Slope
From the 2024 International Residential Code, here’s the section that dictates acceptable roof slope for asphalt shingles:
Mineral-surfaced roll roofing shall not be applied on roof slopes below 1 unit vertical in 12 units horizontal (8-percent slope).
And here’s the equivalent section from the 2024 International Building Code:
Mineral-surfaced roll roofing shall not be applied on roof slopes below 1 unit vertical in 12 units horizontal (8-percent slope).
Underlayment Requirements
While underlayment isn’t explicitly mandated by code for roll roofing, it is still required if the manufacturer specifies it, which most do. The 2024 International Residential Code says underlayment must be installed “in accordance with the manufacturer’s instructions,” and nearly all major manufacturers recommend applying roll roofing over a base layer of asphalt-saturated felt or synthetic underlayment. Using underlayment helps protect the roof deck from moisture and may extend the life of the roof. Skipping it may void the warranty, fail inspection, or lead to premature roof failure.
Here are the IRC underlayment requirements for roll roofing:
Underlayment Application – Mineral-Surfaced Roll Roofing (Table R905.1.1(2))
Areas Where Wind Design Is Not Required In Accordance With Figure R301.2.1.1:
Apply in accordance with the manufacturer’s installation instructions.
Areas Where Wind Design Is Required In Accordance With Figure R301.2.1.1:
Underlayment shall be one of the following:
1. Two layers of mechanically fastened underlayment applied in the following manner: Apply a strip of underlayment that is half the width of a full sheet parallel to and starting at the eaves, fastened sufficiently to hold in place. Starting at the eave, apply full width sheets of underlayment, overlapping successive sheets half the width of a full sheet plus 2 inches. End laps shall be 4 inches and shall be offset by 6 feet.
2. A minimum 4-inch-wide strip of self-adhering polymer modified bitumen underlayment complying with ASTM D1970, installed in accordance with the manufacturer’s installation instructions for the deck material, shall be applied over all joints in the roof decking. An approved underlayment complying with Table R905.1.1(1) for the applicable roof covering shall be applied over the entire roof over the 4-inch-wide membrane strips.
3. A single layer of self-adhering polymer modified bitumen underlayment complying with ASTM D1970, installed in accordance with the underlayment and roof covering manufacturer’s installation instructions for the deck material, roof ventilation configuration and climate exposure of the roof covering.
Note that the second part of this (Areas Where Wind Design Is Required) applies to geographic regions where buildings must be engineered to withstand higher wind forces due to increased risk of strong winds. These areas include designated hurricane-prone regions, coastal high-wind zones, and areas like mountain foothills and tornado-prone zones.
The language in the code means that the double underlayment requirement for roll roofing applies to all roofs, regardless of slope, in these areas. Increased roofing fastener requirements will normally also apply in these areas.