Table of Contents
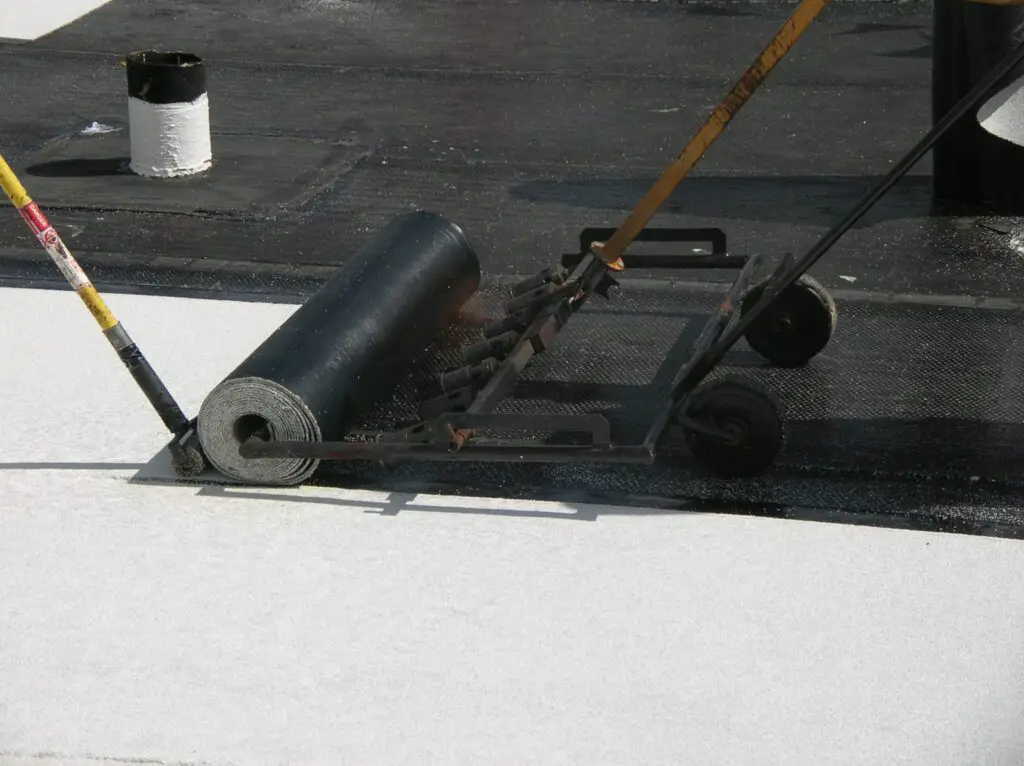
Introduction
Modified bitumen roofing has been used on low-slope (“flat”) roofs for over fifty years. It’s known for being thicker and tougher than the prevailing single-ply membranes that dominate the low-slope roofing market today. Unlike built-up roofing (BUR), another bitumen-based roof system, modified bitumen roofing has kept a good-sized share of the commercial roofing market in the face of competition from single-plies. Modified bitumen is used in around 10% of all new low-slope roofing installations today.
Modified bitumen blends traditional asphalt with modern polymer technology. It’s known for its strength and toughness when compared to single ply membranes, and its flexibility and simpler installation when compared to built-up systems. Mod bit systems provide excellent waterproofing, stand up well to foot traffic, and are suitable for both warm and cold climates.
In this article, I’m going to go over all the important things about modified bitumen roofing that anyone with a low-slope roof should know.
What is Modified Bitumen?
Modified bitumen is also known as polymer-modified bitumen or rubberized asphalt. It is usually called “mod bit” in the roofing industry. Modified bitumen is “modified” when a polymer (a synthetic rubber or plastic) is mixed into liquified asphalt (the “bitumen”) during the manufacturing process. I went on a tour of the Siplast modified bitumen factory in Arkansas once and you could watch the small white polymer pellets being dropped into the vats of hot liquid black asphalt.
While the word “bitumen” can technically refer to either asphalt or coal tar pitch, “bitumen” means “roofing asphalt” in Europe, where modified bitumen was invented and first adopted. Coal tar pitch is not used in the production of mod bit.
Modified bitumen is an asphalt-based roofing product. It is compatible with other asphalt-based roofing products, such as asphalt roofing cement, mastic, asphalt cutback, asphalt coatings, etc.
This gives it an advantage over many other low-slope roofing materials when it comes to maintenance and repair, because of the variety of easy-to-use asphalt roofing products available.
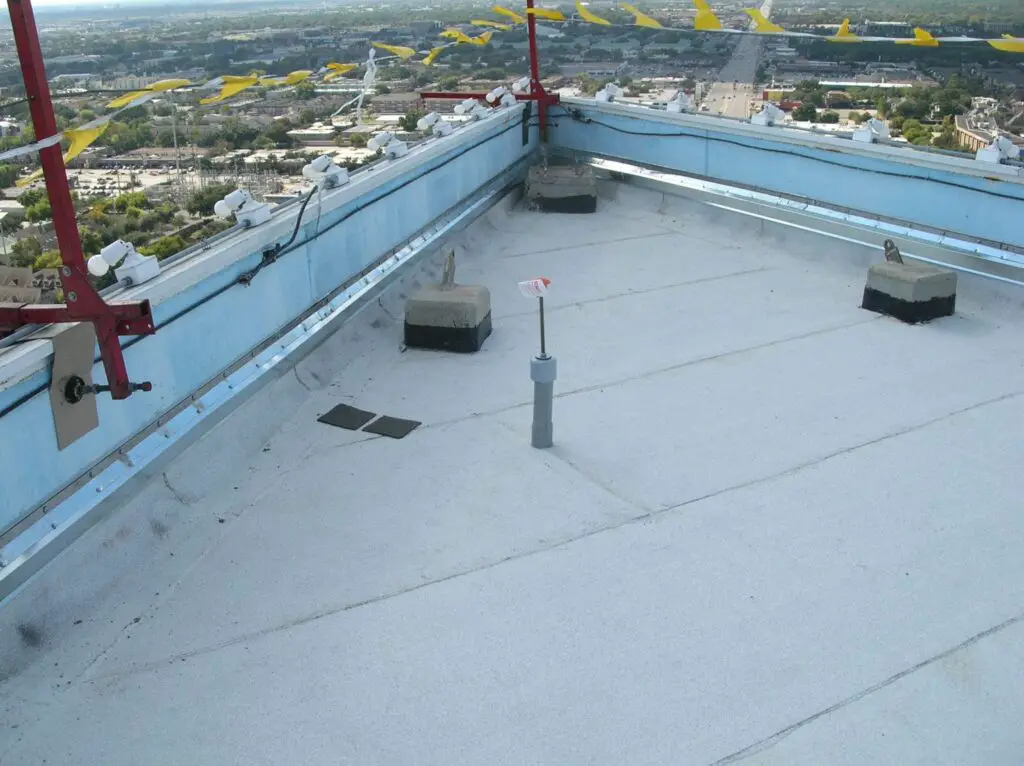
Pros of Modified Bitumen Roofing
- Durability – Modified bitumen roofing systems are designed to withstand harsh weather conditions, including extreme temperatures, heavy rainfall, and high winds. Properly installed, they can last 20 to 30 years with routine maintenance.
- Flexibility and Crack Resistance – Unlike traditional built-up asphalt roofing, modified bitumen contains polymers (APP or SBS) that enhance its flexibility. This makes it less prone to cracking or splitting from thermal expansion and contraction as it ages.
- Excellent Waterproofing – The multiple layers of a modified bitumen roof provides built in redundancies that result in a far more puncture-resistant membrane than single-plies like EPDM.
- Multiple Installation Methods – Modified bitumen can be installed using various techniques, including torch-applied, cold adhesives, hot-mopped asphalt, and self-adhering membranes. This gives contractors the flexibility to address particular site conditions and safety considerations.
- Strong Resistance to Foot Traffic – Modified bitumen membranes are highly resistant to foot traffic, making them ideal for commercial buildings with a lot of rooftop HVAC units and maintenance activity. It also makes mod bit an excellent choice for residential buildings with flat roofs where tenants have unsupervised access to the roof and may be likely to damage other roof systems.
- Easy to Repair and Maintain – Unlike some single-ply systems, modified bitumen is fairly easy to repair, even for building maintenance staff without extensive roof repair training.
- Energy Efficiency Options – Modern modified bitumen systems can include reflective coatings or reflective granule surfaces that help reduce heat absorption and may lower building cooling costs.
- Strong Adhesion and Wind Resistance – Modified bitumen is known for its excellent adhesion properties, which help it resist wind uplift and storm-related damage.
Cons of Modified Bitumen Roofing
- Higher Initial Cost – Compared to traditional built-up roofing (BUR) and most single-ply systems, modified bitumen can have a notably higher upfront cost. Fewer leaks and reduced maintenance and repair costs may offset the initial expense over time.
- Labor-Intensive Installation – While multiple installation methods are available, they all require more labor and usually more skilled labor than single-ply installations do.
- Safety Concerns – Hot-mopped and especially torch-applied systems require additional safety precautions which can add to the cost of a project. Torch-applied roofing is often forbidden by municipal fire codes because there’s a track record of careless roofers starting fires.
- Potential for Heat Absorption – Uncoated black modified bitumen surfaces can absorb heat, raising indoor temperatures and increasing cooling costs. Reflective coatings or granulated surfacing can help mitigate this issue, but these add to the material cost.
- Limited Environmental Friendliness – While some manufacturers incorporate recycled materials, modified bitumen is still petroleum-based and the material cannot be recycled.
- Seam Vulnerabilities – Over time, seams in modified bitumen roofs may open up, particularly if not properly adhered in the first place or if the adhesive bitumen is allowed to deteriorate due to UV exposure. Regular inspections and maintenance are essential to prevent leaks.
- Roof Blisters – Roof blisters are a common issue in modified bitumen roofs where gaps in the interply adhesive exist due to carelessness on the part of the installers. Read more about roof blisters.
- Shorter Warranties – While modified bitumen has a reasonably long lifespan, manufacturers typically offer shorter warranties than those available for single-ply membranes like TPO or PVC, which are sometimes warrantied for up to 30+ years.
History of Modified Bitumen Roofing
Modified bitumen roofing originated in Italy in 1967, when an Italian engineer named Romolo Gorgati developed and marketed the first atactic polypropylene (APP) polymer-asphalt mix. This innovation was driven by the desire to improve the durability and performance of traditional asphalt roofing, which was prone to brittleness in cold temperatures and excessive softening in hot conditions.
By 1969, modified bitumen roofing had been introduced in Germany, and by the mid-1970s, it had expanded to Holland and Great Britain. The United States saw its first commercial applications of modified bitumen in the late 1970s and early 1980s, as roofing manufacturers recognized its superior flexibility and resistance to weathering.
Italy played a particularly significant role in the early adoption and refinement of modified bitumen technology. The country lacked the infrastructure to produce blown asphalt, which was commonly used for built-up roofing (BUR) in other nations. Instead, Italian manufacturers sought alternative ways to enhance asphalt’s performance, leading to the discovery that adding atactic polypropylene (APP) as a polymer modifier could improve flexibility, UV resistance, and longevity. By the 1980s, nearly 90% of commercial roofing in Italy utilized modified bitumen, cementing its status as a dominant roofing system.
Throughout the 1980s and 1990s, advancements in polymer technology led to the widespread adoption of styrene-butadiene-styrene (SBS) modified bitumen, which offered even greater elasticity and cold-weather performance. By the mid-1990s, modified bitumen had grown to roughly 35% of the U.S. roofing market, a significant increase from its share in the previous decades.
Today, modified bitumen continues to be a leading roofing material worldwide, benefiting from ongoing improvements in reinforcement, surfacing options, and installation techniques. Despite the overwhelming trend toward single-ply roofing since the early 2000s, modified bitumen is still used for around 10% of new commercial roofing installations. That number has remained roughly constant for the past 10 or 15 years.
Types of Modified Bitumen
Modified bitumen is referred to by the type of polymer added to the asphalt.
APP-Modified Bitumen
APP (atactic polypropylene) is a thermoplastic polymer mainly used to modify roofing asphalt. APP mod bit is less elastic but stronger than SBS-modified bitumen and has a higher resistance to UV radiation, oxidation, and high temperatures. APP-modified membranes are typically applied using a torch method, which allows the polymerized asphalt to melt and bond effectively to the substrate. APP has a defined melting point (around 300°F or 149°C); it does not soften adequately in hot asphalt, making the hot-mopping technique ineffective.
SBS-Modified Bitumen
SBS (styrene-butadiene-styrene) is a synthetic rubber with many applications, modifying roofing asphalt being just one. SBS-modified bitumen is more elastic than APP-modified bitumen and retains its flexibility even in cold temperatures as low as -20°F (-29°C). SBS-modified membranes can be installed in hot non-modified asphalt, cold-applied adhesives, or as self-adhered systems.
Historically, the option to use hot-mopped asphalt as an adhesive increased the popularity of SBS versus APP-modified bitumen when the only other installation option was torch-application (with its associated risk of fire). Today, self-adhering membranes or cold-applied adhesives provide other safer alternatives for both types.
Other Modified Bitumen Types
Although roofing asphalt is available with other modifiers, such as SEBS (styrene-ethylene-butadiene-styrene), mod bit roof membranes are almost exclusively manufactured using either an APP or an SBS polymer additive. SEBS, an advanced variation of SBS, enhances UV resistance and oxidation stability but is far less commonly used in commercial roofing due to higher costs.
Differences
Differences in chemical structure and physical properties between the two types of modified bitumen make them slightly more or less appropriate than the other type for use on any given roof.
The chief difference is that APP-modified bitumen is preferred in warmer climates due to its high-temperature resistance, while SBS-modified bitumen is preferred in colder climates for its superior flexibility and resistance to cracking.
There aren’t any actual rules requiring the use of one type and not the other simply because of local temperatures. Other considerations, such as roof slope, expected foot traffic, and desired installation method, can also influence which type of modified bitumen is best suited for a particular project. Both types of mod bit can be found wherever mod bit is used for roofing.
Both types of mod bit sheets look nearly identical, and you will not be able to tell the difference simply by looking at or handling the material. Laboratory tests, such as elongation and softening point analysis, are required in order to definitively distinguish between APP and SBS membranes. Unless, of course, you have the project documentation from the installation.
How Modified Bitumen is Made
Mod bit is produced by blending heated, liquid asphalt with polymeric additives (synthetic rubber or plastic), which increase the durability, strength, and flexibility of the asphalt. Anywhere from 3% to 15% of the final product will be polymer additive, depending on the manufacturer and the specific type of product.
Mod bit maintains a more uniform strength and flexibility over a wider range of temperatures compared to the unmodified asphalt used in built-up roofs or unmodified asphalt shingles.
Modified bitumen roofing is manufactured in sheets, with layers of modified asphalt applied to each side of a reinforcement fabric, much the same way as asphalt shingles are made. The reinforcement fabric is made from either fiberglass or polyester, or a combination of the two. Fiberglass reinforcement improves tensile strength and fire resistance, while polyester reinforcement provides better flexibility and impact resistance.
The finished mod bit sheets are typically 39 inches (1 meter) wide and sold in rolls. The rolls are typically between 25 feet and 33 feet (10 meters) long. Some manufacturers also produce rolls in slightly different widths and lengths to meet regional standards.
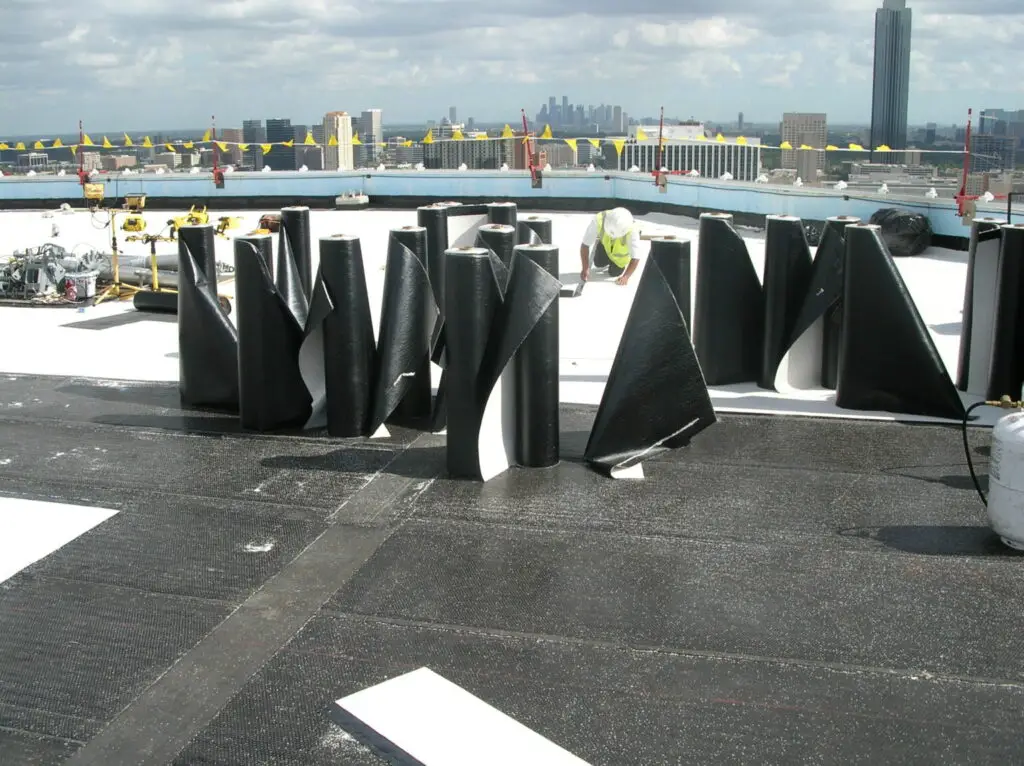
Weight and Thickness of Modified Bitumen Roofs
In the US, individual sheets of mod bit are typically between 120 mils (3.05 mm or 0.12 inches) and 180 mils (4.6 mm or 0.18 inches) thick, depending on the specific product and reinforcement type. In the metric system, this is typically standardized at 3 mm or 4 mm thicknesses, which are common designations for European modified bitumen membranes.
A typical sheet of modified bitumen roofing weighs about 1.1 lbs. per square foot, though this can vary slightly depending on the composition of the reinforcement and surface treatment. For instance, APP-modified bitumen with a granulated surface may weigh slightly more than smooth-surfaced SBS-modified bitumen.
The vast majority of installed mod bit roof membranes have two plies, a base sheet and a cap sheet. So the average modified bitumen roof membrane (not including other roof system components) is about 300 mils (7.62 mm or 0.3 inches) thick and weighs around 2.2 pounds per square foot. Occasionally, an additional interply layer may be added which bumps the membrane weight up to 3.3 pounds per square foot.
In addition to the roof membrane, layers of insulation and cover board under the membrane itself may lead to the whole roof system being several inches thick. The actual thickness of the roof system will depend on the type of insulation used and the total roof system R-value requirements of the local energy code. In cold climates, thicker insulation layers are often required to meet thermal performance standards, which can increase the total system thickness significantly.
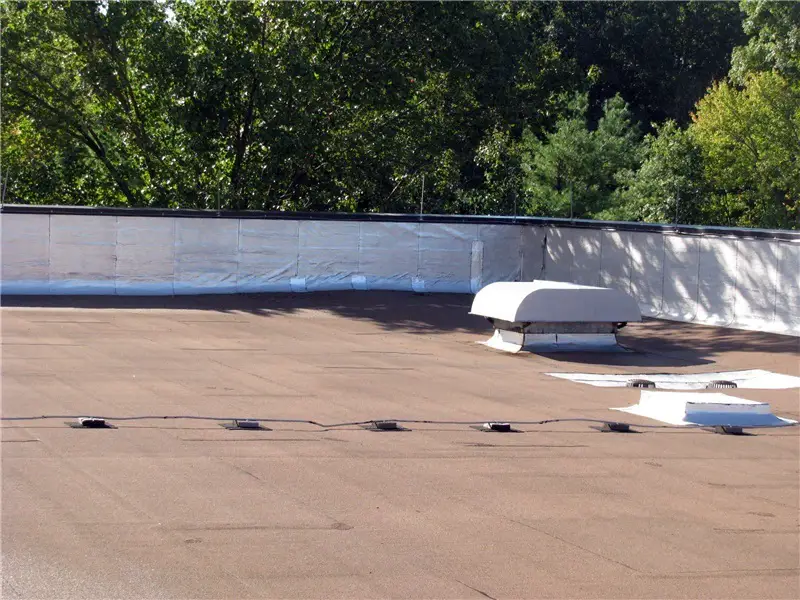
Surfacing for Modified Bitumen Roofs
Unprotected asphalt is highly vulnerable to the sun’s UV rays. The UV radiation breaks down the long-chain hydrocarbon molecules that give asphalt its strength and durability. This is an issue common to all asphalt-based roofing materials.
In order for asphalt-based roofing to perform for an acceptable length of time, the asphalt has to be protected from the sun. This is why asphalt shingles are covered with ceramic-coated mineral granules, and it’s the main reason why built-up roofs have gravel surfacing on them. Similarly, modified bitumen membranes require a protective surfacing to maintain their long-term durability and performance.
There are three main types of surfacing for the cap sheet (top ply) of mod bit roof systems:
Granule-Surfaced Mod Bit
Ceramic-coated mineral granules are embedded in the top surface of mod bit cap sheets (the top layer of a multi-layer roof membrane) at the factory, as with asphalt shingles or roll roofing. This is by far the most common surfacing for mod bit roofing.
These granules are most often some shade of gray, but custom colors are available, and tan, brown, black, or white granules are common. Lighter-colored granules are frequently chosen for their ability to reflect sunlight and reduce rooftop temperatures.
Foil-Surfaced Mod Bit
Metallic foil is laminated to the top surface of the cap sheet in the factory. This foil layer provides exceptional protection against UV degradation and prevents premature aging of the asphalt beneath. Aluminum foil is used most often, but copper and stainless steel foil are also used.
Foil-surfaced mod bit is often used as flashing material on mod bit roofs, while normal granule-surfaced modified bitumen is used for the rest of the roof. This is due to the increased sun exposure of the (mostly) vertical flashings compared to the flat roof surface. The foil surfacing provides better UV protection than granules, but the material also costs more.
While granules tend to wear off as time goes by, gradually exposing the asphalt to more and more sunlight, laminated foil generally provides total UV protection for the life of the roof.
As foil-surfaced mod bit is relatively expensive, and the foil is vulnerable to damage from foot traffic, it is less suitable for areas where regular foot traffic is expected.
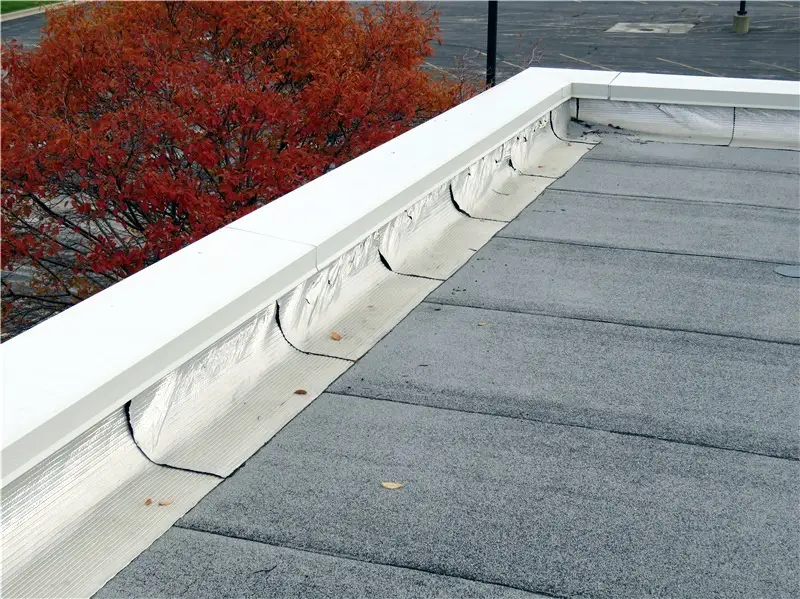
Coated Modified Bitumen
Roof coatings are typically applied after the roof has been installed, although factory-applied reflective roof coatings are becoming more common as manufacturers try to meet the demand for reflective roofing due to changing energy codes and LEED requirements.
When applying a roof coating to an existing, uncoated mod bit roof, extremely thorough preparation of the surface is necessary. Modified bitumen does not hold a coating as well as unmodified asphalt. Manufacturers always recommend thorough cleaning and priming of the surface before applying a coating to ensure maximum adhesion and service life.
When the loss of granules becomes noticeable on a granule-surfaced roof, and the asphalt on parts of the roof is exposed (when you can see bare asphalt), a common roof maintenance practice is to apply a roof coating to those areas of the roof.
Reflective coatings, such as aluminized or white coatings, can also improve the energy efficiency of the roof.
Attachment Methods for Modified Bitumen Roof Membranes
After the specified amount and type of insulation is installed over the roof deck, a cover board compatible with the specified mod bit membrane attachment method is installed over the insulation.
A cover board is always used in situations where the insulation may be damaged by a direct application of the roof membrane. There are a number of reasons that a roof membrane may not be suitable for direct application over the insulation; heat damage to the insulation from hot asphalt, for example.
The cover board layer of a roof system typically consists of one layer of gypsum board, wood fiberboard, or perlite board an inch or less thick. Both the cover board and the insulation are either fastened through to the roof deck or adhesive is used to hold the layers together, with the bottom layer adhered or fastened to the deck. The modified bitumen sheets are then adhered to the cover board.
There are four acceptable methods for attaching the sheets of modified bitumen:
Torch-Applied (or “Heat Welded”)
This method uses propane torches (hand-held torches for flashing materials, and rolling “torch wagons” for the field of the roof) to melt the asphalt on the underside of the mod bit rolls. The melted asphalt bonds the roofing to the substrate as the sheets are slowly unrolled across the roof.
Although this was a very common application method in the past, it has fallen out of favor with the development of alternatives such as cold-process adhesives and peel-and-stick (self-adhering) mod bit membranes.
Many municipalities now ban torch-application of modified bitumen due to the risk of fire, and some insurance providers have increased premiums for contractors using torch-applied roofing.
Anyone performing a torch application should also ensure the presence of a fire monitor on the roof for an appropriate time after the day’s work is complete to ensure that no hidden, smoldering insulation, wood blocking, or other flammable substrate results in a fire on the roof.
One hour is typically the minimum amount of time the fire monitor should stay on the roof, but the roofing manufacturer or the local code may have other recommendations or requirements. Always check with the local fire marshal’s office before proceeding with a torch-down roofing project.
Mopped in with Hot Asphalt
This method uses hot asphalt melted in special asphalt roofing kettles to bond the modified bitumen rolls to the substrate. Hot liquid asphalt is transferred from the kettle to the area of application and mopped onto the roof. The mod bit is rolled out into position and set into the hot liquid asphalt.
This method is effective with SBS-modified bitumen but not with APP, which has a more unforgiving application temperature range. Contractor error regarding the use of APP vs. SBS-modified material is something to watch out for.
The hot asphalt method has also fallen out of favor recently, mainly due to the serious decline of built-up roofing in general. Most roofing contractors no longer maintain the asphalt kettles and other hot asphalt application equipment needed for this method. Health and safety concerns related to asphalt fumes and the high-temperature application process have also led to an increase in regulations.
Cold-Process Adhesive
Instead of hot asphalt from a kettle, asphaltic adhesives can be brought to the roof in buckets and poured onto the substrate at the ambient temperature. The liquid is then squeegeed out to the proper application rate, and the roofing is rolled into it as with hot asphalt.
The first generation of cold-applied adhesives had a serious odor issue due to the high level of VOCs in the available products. These fumes could make their way into the building and cause problems for the occupants. According to the manufacturers, this is no longer an issue, as current products are “low VOC” and have almost no odor.
This video from Siplast gives you a remarkably detailed look at how modified bitumen roofing is installed in cold-process adhesive:
Self-Adhering (Peel-and-Stick) Membrane
The latest development in mod bit application technology, peel-and-stick rolls of mod bit come from the factory with adhesive already applied to the back of the sheets, protected by a plastic film.
A compatible underlayment, cover board, or both specified by the manufacturer is installed on the roof. The rolls of mod bit are unrolled into position on the roof. The protective film is then pulled off the bottom of the material, and the roof membrane is pressed down for full adhesion, usually with a specialized heavy roller.
Self-adhering membranes are particularly useful in areas where open-flame or hot-asphalt applications are not feasible or permitted and the use of liquid adhesives may cause problems due to the configuration of the roof.
This video from the Garland Company walks you through the installation of a peel-and-stick modified bitumen system: