I participate in the Amazon affiliate program and may earn commissions from purchases made through links on this page.
Table of Contents
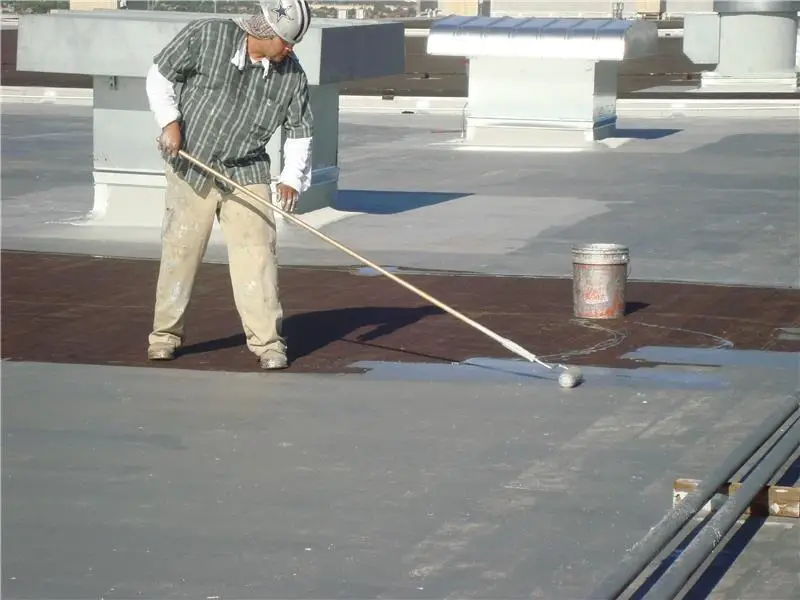
Introduction
This article provides general information about various types of roof coatings. In addition to drawing on my own personal experience overseeing roof coating projects, I compiled much of the technical information here from a wide assortment of manufacturers’ technical data sheets or material safety data sheets for actual coating products. (You can find these data sheets available on roof coating manufacturer websites.) The information on this page should be considered to be representative but not necessarily definitive.
This information should not be used if precise values are needed for critical design calculations. When precision is necessary, always refer to the data sheets of the actual, specific product you intend to use, or contact the technical department of the coating manufacturer.
When is a Roof Coating Appropriate?
(If you’d like to see what I have to say about this in much more detail, see my article “Roof Coatings: Advice From a Roof Consultant“.)
A roof coating can be an effective way to extend the life of your roof, improve energy efficiency through solar reflectance, and protect against the elements—but it’s not the right solution for every situation. If your roof has reached the end of its life, a roof coating will not save it. Here are some scenarios when a roof coating is appropriate:
Generally Sound Roof Condition:
- Minor Aging and Wear: If your roof is showing signs of aging but isn’t severely damaged (e.g., it has minor cracks, slight surface wear, or a few leaks that have been repaired), a roof coating can add an extra layer of protection and help extend its useful life.
- Roof Membrane Integrity Intact: The roof substrate should be in good shape. Coatings work best when applied to a stable, clean, and structurally sound surface. If there are significant issues like widespread water damage, severe degradation, or splits or noticeable cracks in the roof membrane, repairing or replacing the roof is the better course of action. Roof systems with extensive wet insulation should not be considered candidates for roof coating.
Low-Slope (“Flat”) Roofs:
- Roof coatings are primarily suitable for flat or low-slope roofs. These types of roofs can be prone to ponding water and leaks, and a well-applied coating can help seal joints and seams, reduce water infiltration, and even out the surface.
Energy Efficiency Improvements:
- Reflective or “Cool” Roof Coatings: If reducing energy costs is a priority, certain coatings are designed to reflect sunlight and UV rays, keeping the roof – and the building – cooler. This can be especially beneficial in hot or sunny climates (which are not always the same thing).
Cost-Effective Service Life Extension:
- Avoiding a Full Replacement: For roofs that are not yet at the end of their lifespan but have begun to show wear, applying a roof coating can be a fairly cheap way to delay a full replacement. It essentially halts the roof’s deterioration and allows it to perform for a few additional years. Again, the roof must still be in decent condition for this to be effective.
Important Considerations Before Applying a Roof Coating
- Proper Surface Preparation: The roof must be thoroughly cleaned and any necessary repairs made prior to applying the coating. This ensures proper adhesion and performance.
- Type of Coating: Different roof materials (e.g., metal, asphalt, EPDM) and different environmental conditions may require specific types of coatings (e.g., silicone, acrylic, elastomeric). Choose the one that best fits your roof’s needs.
- Consult a Professional: Because the effectiveness of a roof coating largely depends on the condition of the underlying roof and the correct application process, it’s a good idea for property managers or anyone else responsible for a commercial roof to have a professional roof consultant evaluate your roof first. Roof consultants will not try to sell you something that won’t benefit you. The consultant can advise you as to whether a coating is appropriate and what type will work best for your situation.
A roof coating can be appropriate when your low-slope roof is in overall good condition (or has been properly repaired), and when you’re looking to extend its life, improve energy efficiency, or delay a full roof replacement. Always get professional advice to achieve the best results.
Roof Coatings on Shingled Roofs
This is simply a bad idea and goes against the recommendations of every reputable shingle manufacturer. In almost no case will a roof coating be suitable for a pitched roof. According to the Asphalt Roofing Manufacturers Association:
“coatings may negatively impact the performance characteristics (including the fire classification, algae resistance, impact resistance, etc.) of the roof assembly”
and:
“the problems reported after asphalt shingle roofs have been field coated include shrinking of the coating, which may result in unsightly curling and/or cupping of the shingles or loosening of the granule surfacing of the asphalt shingles. In addition, non-permeable roof coatings may create a vapor-retarding layer by sealing the voids around and between the shingles. If this occurs, it may contribute to moisture accumulation within the roofing system.”
The moisture that will tend to accumulate within the roofing system generally comes from interior humidity which would normally pass up and through the roof, but now can’t do that. Heating and air conditioning lead to different levels of humidity and temperature between the inside of the house and the outside air. These differences lead to condensation. If you coat the roof, that moisture will have nowhere to go. It will remain trapped in the sheathing, laying the groundwork for dry-rot and mold.
Another good source for impartial information about the roof coating products marketed for use on asphalt shingles is Myth Busting: The risks and unverified benefits of field coating asphalt shingles in Professional Roofing magazine (published by the National Roofing Contractors Association).
If you’re interested in what I have to say about asphalt shingle rejuvenation treatments, see “Do Roof Rejuvenation Treatments Like Roof Maxx Really Work?“
Before You Apply a Roof Coating
It is very important to read the manufacturer’s safety information before working with roof coating materials. Some of these coatings are extremely toxic during application and all manufacturer’s safety guidelines must be followed. You can find the safety information in the manufacturer’s technical data sheet and material safety data sheets for the actual product you are considering using. You can find these data sheets online on the manufacturer’s website.
Before purchasing and applying a roof coating material, be sure to check whether a material is legal to use in your jurisdiction. Some types of coatings are subject to environmental and health restrictions. The manufacturer’s product data sheet will also provide coating application instructions (like whether reinforcement fabric is needed, coverage rate, etc.).
Substrate Preparation for Roof Coatings
When applying roof coatings, remember that virtually all surfaces to be coated must be clean, dry, and free of contaminants such as dirt, oil, grease, delaminated areas of previous coatings, and other debris. Do not apply roof coatings on wet or damp surfaces. If you apply a roof coating on a dusty or damp surface, the adhesive bond will not form properly, and the coating will eventually delaminate and fall off. I’ve seen it happen many times. If a primer is recommended by the manufacturer, make sure you apply the primer!
Roof Coatings: General Categories
Bituminous Roof Coatings
Bituminous coatings use asphalt or coal tar pitch as their main waterproofing component.
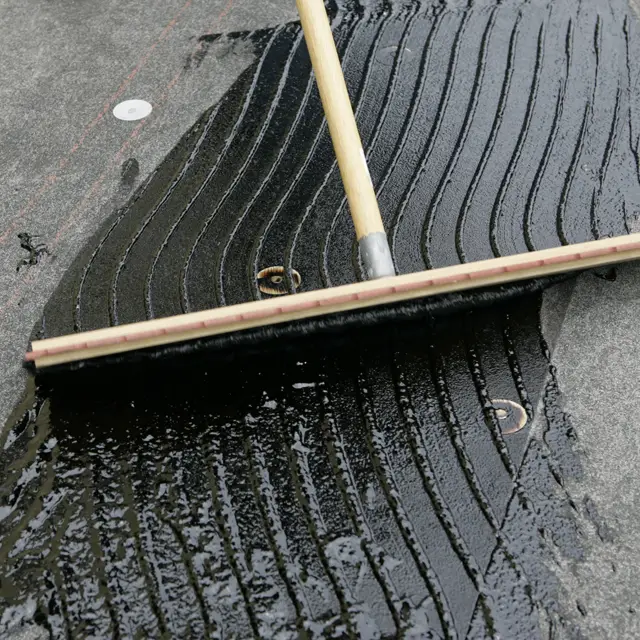
Cool Roof Coatings
A “cool roof” coating is any coating that reduces the amount of heat the roof absorbs from the sun by reflecting a higher proportion of sunlight and increasing thermal emittance as compared to traditional coating materials. White roof coatings and coatings formulated with other reflective pigments are considered “cool”.
See examples of cool roof coatings on Amazon.
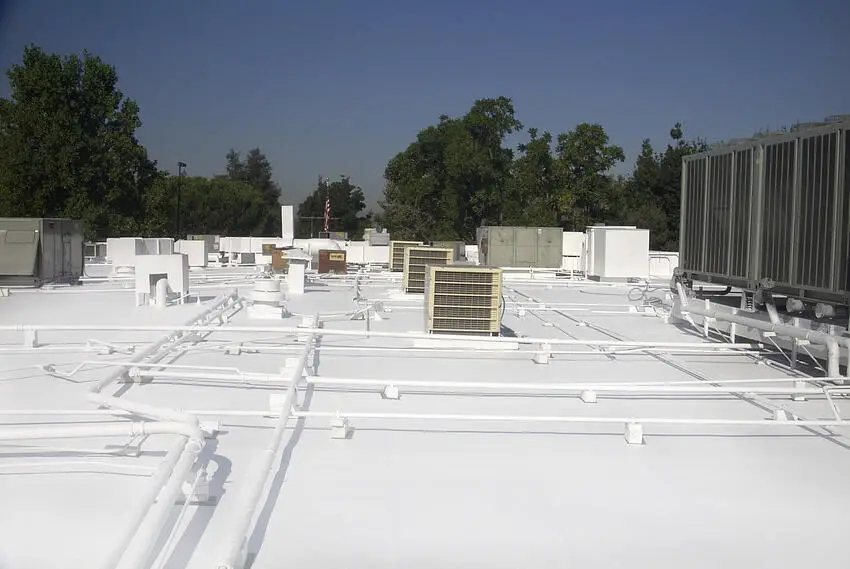
Elastomeric Roof Coatings
Elastomeric coatings have elastic properties which allow them to stretch and return to their original dimensions without being damaged. This allows them to accommodate building movement and particularly the thermal expansion and contraction of the roof membrane on which they are applied. Most non-bituminous roof coatings are elastomeric. This makes them well-suited for use on compatible single-ply membranes.
Non-elastomeric coatings must have similar expansion/contraction rates as the roofing material they are applied to (an asphalt coating on an asphalt roof, for example), or they will split and crack.
See examples of elastomeric roof coatings on Amazon.
Fibered (Fibrated) Roof Coatings
Fibered coatings are formulated with cellulose or fiberglass fibers. The fibers are typically between ¼ inch and 1 inch long. The fibers in a roof coating increase tear resistance in the cured coating and resistance to flow during application (improving its performance when applied to steep slopes or flashings). Generally, only non-elastomeric coatings will be fibered, as the fibers reduce the elasticity of the material.
See examples of fibered roof coatings on Amazon.
Polymer-Modified Roof Coatings
A polymer-modified coating is a bituminous coating that has been formulated with the addition of a bitumen-compatible polymer such as styrene-butadiene-styrene to improve its performance. A polymer-modified coating will typically be more flexible, longer-lasting, and more expensive than unmodified coatings. Often referred to as “rubberized”.
Polymeric Roof Coatings
Polymeric coatings are made using any of various synthetic resins (polymers) as the primary waterproofing component. The most commonly seen polymeric coatings are based on acrylics, silicones, or polyurethanes, but there are several other polymer-based coatings.
Reflective Roof Coatings
A reflective coating is any roof coating formulated to be highly reflective of the sun’s rays. Typical reflective coatings are white, aluminized, or include special reflective pigments in other colors. Reflective coatings produce a “cool roof” effect. In the case of a black EPDM roof, for instance, a reflective coating can reduce the normal afternoon temperature of the roof by up to 60°F (34°C).
See examples of reflective roof coatings on Amazon.
Rubberized Roof Coatings
A “rubberized” coating is a bituminous coating that contains a synthetic rubber. See “Polymer-Modified Roof Coatings” above.
White Roof Coatings
A white coating is simply a coating that is white. White coatings are generally considered “cool” or “reflective”. Most polymeric coatings are available in white. Titanium dioxide is the most commonly used pigment in white roof coatings.
See examples of white roof coatings on Amazon.
Types of Roof Coatings by Coating Material
Acrylic Roof Coatings
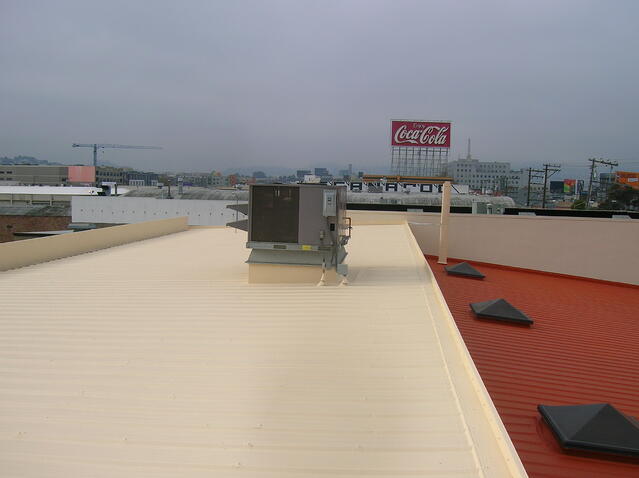
Main Components: (This is an example and actual product formulations will vary) water, calcium carbonate (or other extender pigment) acrylic polymer resin, titanium dioxide (or other prime pigment)
Acceptable Substrates: Acrylic coatings are available in a wide variety of formulations for application on almost every type of substrate. Individual coating products are not applicable to all substrates. It is important to check the product data sheet of the actual product before selecting an acrylic coating.
Unacceptable Substrates: Existing silicone coatings, gravel-surfaced built-up roofs
Colors: White, tan, gray, various other colors
Elastomeric: Yes
Chemical Resistance: Poor
Handles Ponded Water: Poor
Handles Foot Traffic: Poor (some formulations perform better)
Application Method: Brush, roller, or spray
Application Temperature: Above 50°F (10°C)
Notes: Water-based. One of the most inexpensive types of coating. Comes in the widest variety of colors. Does not last nearly as long as some of the other (more expensive) coatings on this list. Acrylic roof coatings typically have the shortest useful life of all the most common types of roof coatings.
Easy to apply. Low VOC. Low toxicity. Ability to accommodate substrate movement is limited. Cracking and delamination can occur over aged or poorly prepared substrates, particularly in cases where the coating is applied too thinly or over embedded gravel. Acrylic coatings should not be applied in wet or highly humid conditions, as curing can be negatively affected. They are not recommended for application over uncured asphaltic materials due to potential chemical interactions that can degrade the coating.
Despite their limitations, elastomeric acrylic coatings remain a viable, low-cost solution for reflective roof coatings, particularly in dry climates where ponding water is not a concern.
See examples of acrylic roof coatings on Amazon.
Aluminum (Aluminized) Roof Coatings
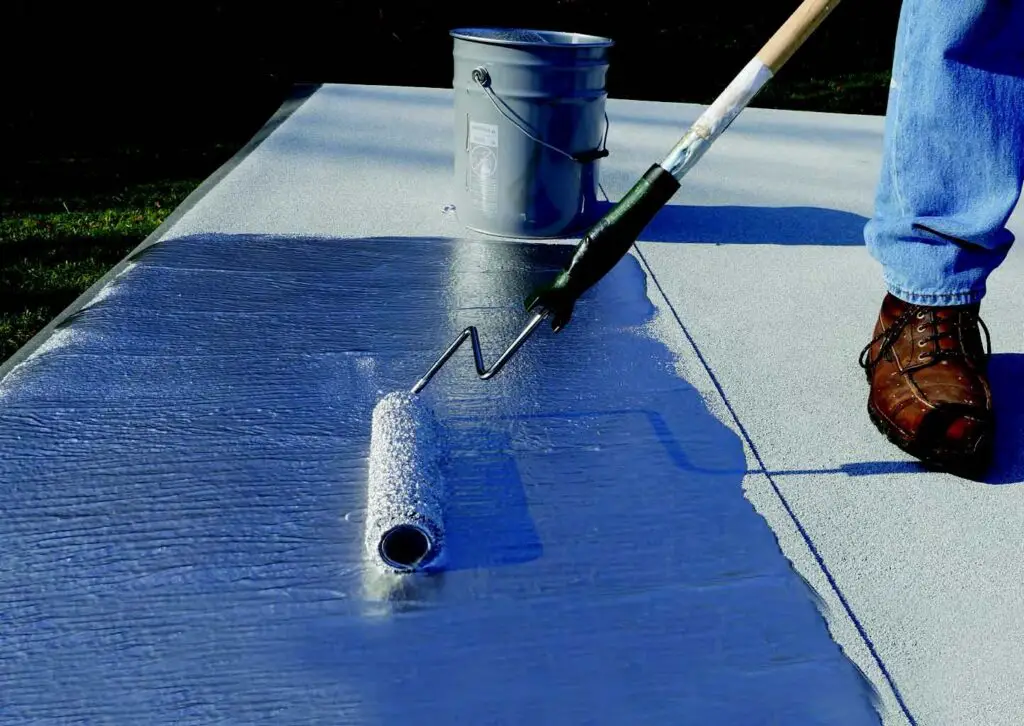
Main Components: Mineral spirits (or other solvent), asphalt, aluminum powder/flakes (up to 30%), perlite (or other filler)
Acceptable Substrates: Smooth-surfaced asphalt built-up roofing, modified bitumen, metal, existing asphalt coatings
Unacceptable Substrates: Coal-tar, single-ply membranes, Kynar®- or Hylar®-coated metal, spray polyurethane foam, gravel-surfacing, existing non-asphalt coatings
Colors: Silver
Elastomeric: No
Chemical Resistance: Poor
Handles Ponded Water: Poor
Handles Foot Traffic: Fair
Application Method: Brush or spray
Application Temperature: Above 40°F (4°C)
Notes: Available fibered or non-fibered. Gives asphalt roofing a reflective surface. Aluminum roof coatings are used for their “cool roof” effects, and to protect and extend the life of asphalt-based roof systems and roof components, especially modified bitumen. On gravel-surfaced roofs, it’s very common to use an aluminized roof coating on the base flashings throughout the roof.
Proper curing of the asphalt substrate before application is very important, and some manufacturers recommend waiting up to three months before applying the coating to prevent premature failure.
Solvent-based aluminum coatings contain reflective aluminum pigments, which help reduce the roof temperature and slow down the oxidation of the underlying asphalt. These coatings must be properly maintained to retain their reflectivity, as weathering can cause oxidation and a dulling of the surface over time.
Aluminum roof coatings can improve energy efficiency by reflecting solar radiation, reducing cooling costs. They also help prolong the life of asphaltic roof materials by reducing the amount of heat they experience during the day. However, they do not typically offer much in terms of waterproofing and should not be used to address leaks or ponding water issues.
Fibrated versions provide additional durability and are often used on flashings for added protection. Regular reapplication is necessary to maintain their effectiveness, especially in areas with high UV exposure.
See examples of aluminum roof coatings on Amazon.
Asphalt Cutback (Solvent-Based) Roof Coatings
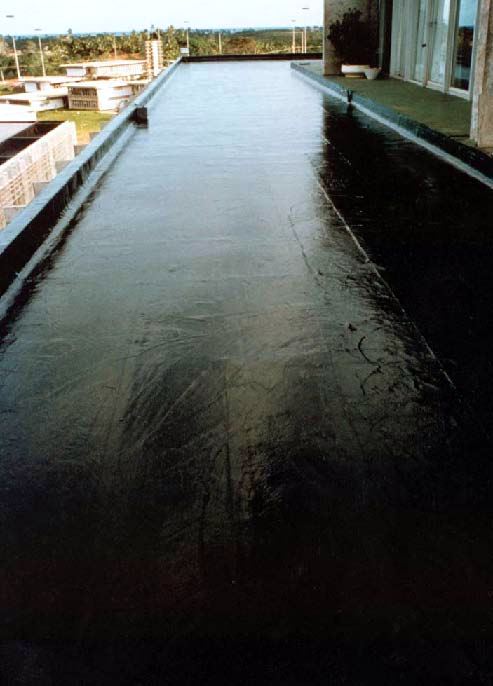
Main Components: Asphalt, mineral spirits
Acceptable Substrates: Smooth-surfaced asphalt built-up roofing, modified bitumen, metal, existing asphalt coatings
Unacceptable Substrates: Coal tar pitch roofing, single-ply membranes, Kynar®- or Hylar®-coated metal, spray polyurethane foam, gravel-surfacing, existing non-asphalt coatings
Colors: Black
Elastomeric: No
Chemical Resistance: Poor
Handles Ponded Water: Poor
Handles Foot Traffic: Fair
Application Method: Brush or squeegee
Application Temperature: Above 40°F (4°C)
Notes: Available fibered or non-fibered. Used to re-coat and extend the life of asphalt roofs. Can be thinned to use as a primer. Can be used to bond asphalt-impregnated felts together when making repairs. Can be used to adhere roll roofing/modified bitumen cap sheets when making repairs. Can be used when re-applying gravel to bare spots on gravel-surfaced roofs.
Cutback asphalt is the main component of roof cement. When it’s used as a coating instead of as a roof cement, it uses much more solvent to make it thinner.
Solvent-based cutback asphalt coatings provide a durable surface for aging built-up roofs (BURs) but must be applied under specific conditions to ensure proper adhesion and performance. Because they contain a high percentage of volatile solvents, they cure by evaporation rather than by chemical reaction. This means that application in humid or low-temperature conditions can extend drying time and lead to improper curing.
Although this type of coating improve the weather resistance of asphalt-based roofs, they do not provide significant strength reinforcement. If an asphalt built-up roof has reached the point where it is experiencing splitting, a coating will not help counteract this.
Cutback asphalt coatings are highly flammable due to their solvent content and should not be applied near open flames or high-heat sources. Proper ventilation is necessary during application to prevent the accumulation of harmful vapors. Many jurisdictions have regulations restricting the use of high-VOC cutback asphalts due to environmental concerns.
Cutback asphalt remains a widely used roof coating for its ability to extend the service life of existing asphalt roofs and improve their resistance to UV degradation. Periodic reapplication is required to maintain its protective properties, especially in areas exposed to high levels of sunlight.
Asphalt Emulsion (Water-Based) Roof Coatings
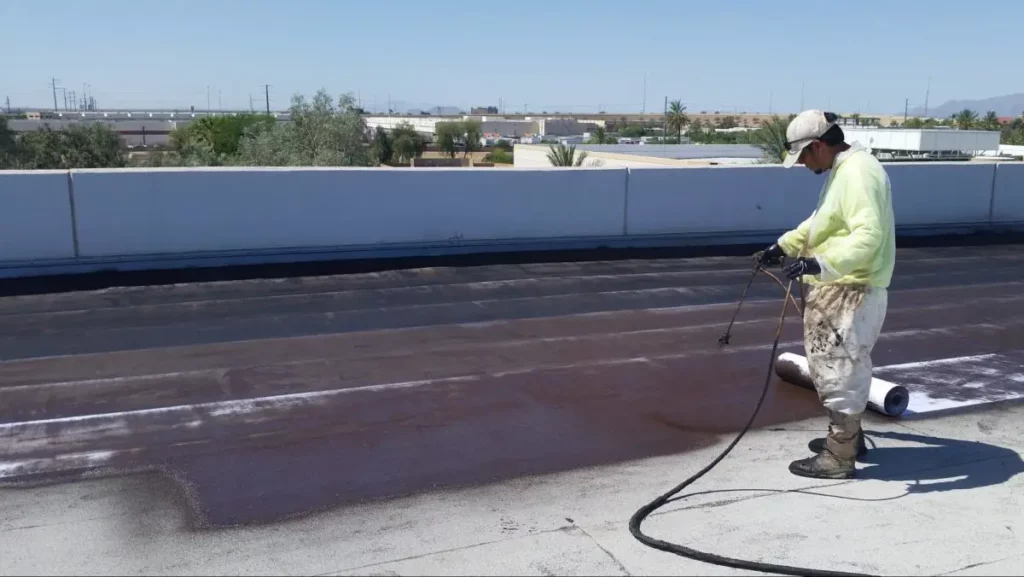
Main Components: Water, asphalt, bentonite clay (or other stabilizer)
Acceptable Substrates: Smooth-surfaced asphalt built-up roofing, modified bitumen, metal, existing asphalt coatings
Unacceptable Substrates: Coal-tar, single-ply membranes, Kynar®- or Hylar®-coated metal, spray polyurethane foam, gravel-surfacing, existing non-asphalt coatings
Colors: Black, brown
Elastomeric: No
Chemical Resistance: Poor
Handles Ponded Water: Poor
Handles Foot Traffic: Fair
Application Method: Brush, roller, or spray
Application Temperature: Above 50°F (10°C)
Notes: Available fibered or non-fibered. Only used in surface applications or as a base-coat for another asphalt-compatible coating. Best suited for smooth-surfaced asphalt roofing. Used to re-coat and extend the life of asphalt roofs. Low in volatile organic compounds (VOCs), making it less of a health hazard and a more environmentally friendly alternative to solvent-based coatings. Requires dry weather conditions for application and curing, as high humidity or rain before full curing can compromise adhesion and performance. Provides some UV resistance but generally requires an additional reflective coating for long-term solar protection. Asphalt emulsion coatings are typically further coated with an aluminized coating.
Butyl Roof Coatings
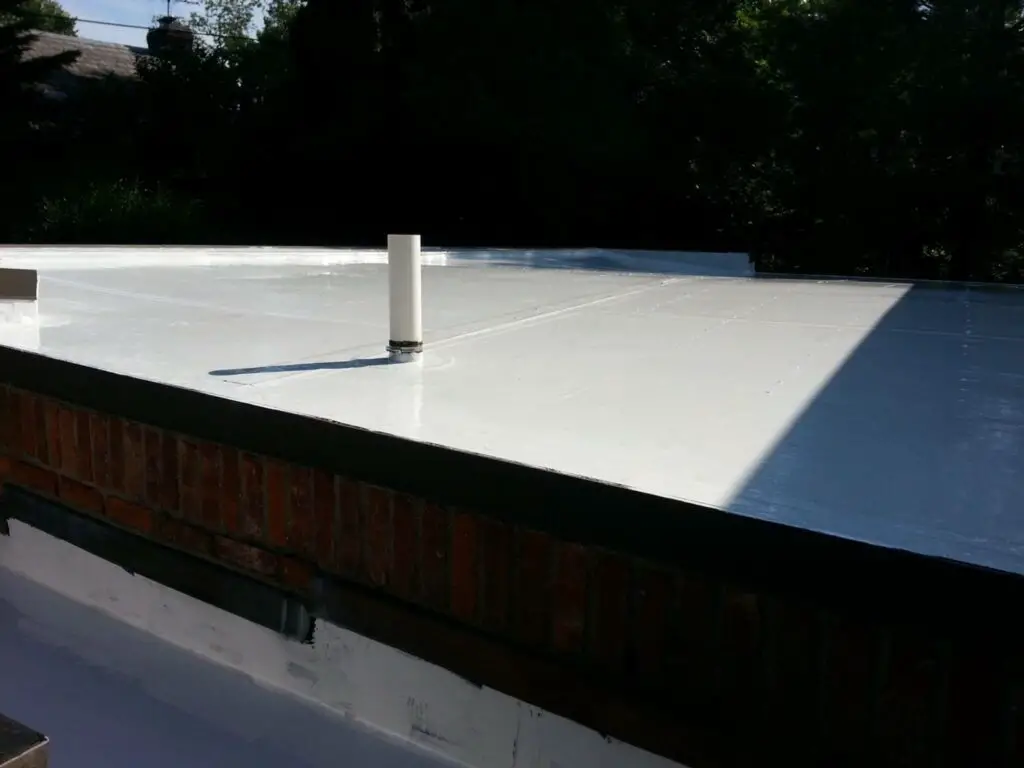
Main Components: (This is an example and actual product formulations will vary) aliphatic hydrocarbon, petroleum resin, polybutene, titanium dioxide, styrene, butadiene, xylene
Acceptable Substrates: Metal, spray polyurethane foam, smooth-surfaced built-up roofing, modified bitumen, EPDM, TPO, and PVC membranes
Unacceptable Substrates: Gravel-surfaced roofing, existing silicone coatings. Always check specific product data sheets for material compatibility.
Colors: White, gray, custom colors available
Elastomeric: Yes
Chemical Resistance: Fair
Handles Ponded Water: Excellent
Handles Foot Traffic: Fair
Application Method: Brush, roller, spray
Application Temperature: Above 40°F (4°C)
Notes: Polymeric coating. Solvent based. High VOC. Relatively expensive. Highly elastomeric. Can qualify as a vapor barrier. Resistant to UV degradation, maintaining flexibility and durability even in extreme temperature fluctuations. Performs well in environments with high movement and expansion, making it a strong option for roofs prone to structural shifts or thermal cycling. It has limited chemical resistance, which may require additional protective coatings in areas with exposure to industrial pollutants or harsh chemicals.
Butyl coatings have a slow curing time compared to some other solvent-based coatings, requiring careful planning for application if high humidity or rain is expected.
Coal Tar Pitch-Based Roof Coatings
Main Components: Refined coal tar pitch, aromatic solvent, Fuller’s earth (or other stabilizer)
Acceptable Substrates: Smooth-surfaced coal tar pitch built-up roofing, concrete
Unacceptable Substrates: Asphalt roofing, single-ply membranes, spray polyurethane foam, existing non-coal tar pitch coatings
Colors: Black
Elastomeric: No
Chemical Resistance: Good
Handles Ponded Water: Good
Handles Foot Traffic: Fair
Application Method: Brush or squeegee
Application Temperature: Above 40°F (4°C)
Notes: May be difficult or impossible to find these days. Coal tar pitch roof coatings are used to re-coat and extend the life of coal tar pitch roofs, which have almost completely disappeared as far as new roofing installations go. Exceptionally resistant to water and many chemicals, making them highly effective in industrial or harsh environmental conditions. Can self-heal small cracks due to their unique chemical composition, maintaining long-term flexibility and durability. Highly resistant to UV degradation, often outlasting conventional asphalt-based coatings in terms of longevity.
Extremely high VOC content and health hazards, with coal tar pitch being classified as a known carcinogen, leading to severe regulatory restrictions in many regions. Proper protective gear is essential during application. Can soften in high temperatures, potentially causing issues in hot climates.
Polyurea Roof Coatings
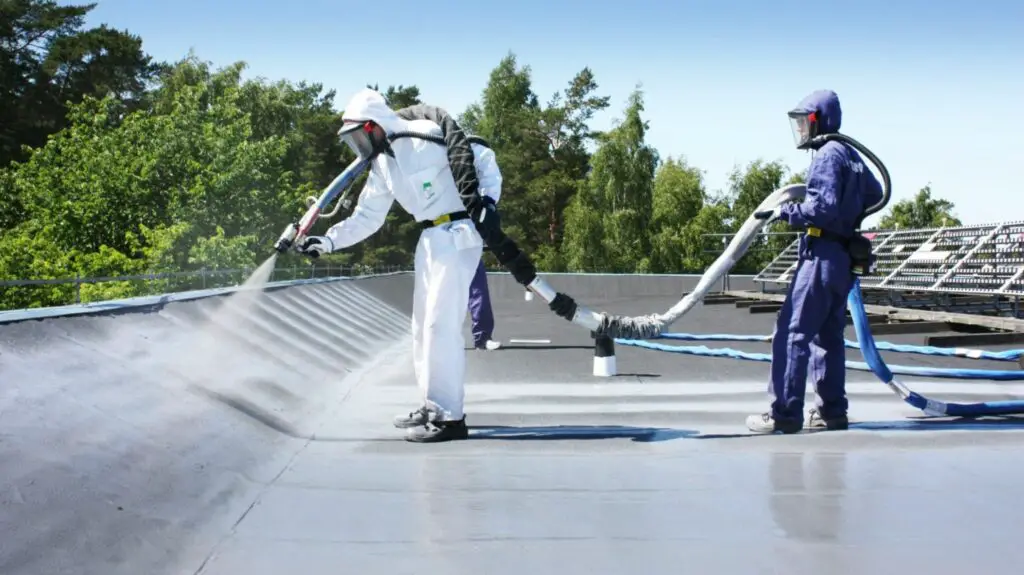
Main Components: An isocyanate component is combined with an amine resin blend component at the time of application.
Acceptable Substrates: Concrete, spray polyurethane foam, metal, built-up roofing, modified bitumen, EPDM, PVC, TPO single-ply membranes
Unacceptable Substrates: Gravel-surfaced roofing, existing silicone coatings
Colors: Many colors available
Elastomeric: Yes
Chemical Resistance: Excellent
Handles Ponding Water: Excellent
Handles Foot Traffic: Excellent
Application Method: Spray
Application Temperature: 5°F (3°C) above the dew point and rising
Notes: Cures in seconds, requires special equipment and training to apply. Relatively expensive. Highly durable and impact-resistant, making it an excellent choice for roofs subject to excessive mechanical stress or frequent foot traffic. Exceptional resistance to water, chemicals, and UV exposure; significantly reduced degradation over time compared to other coatings. Can be applied in a wide range of temperatures and humidity levels, allowing for greater flexibility in installation scheduling.
Limited working time due to rapid curing, which means application mistakes are difficult to correct. Requires precise surface preparation to ensure proper adhesion, as improper substrate conditions can lead to delamination and premature failure.
Polyurethane (Aliphatic) Roof Coatings

Main Components: (This is an example and actual product formulations will vary) polyoxypropylene glycol, cyclohexane, aliphatic hydrocarbon, titanium dioxide (or other prime pigment), hexamethylene diisocyanate, xylene, ethyl benzene
Acceptable Substrates: Spray polyurethane foam, EPDM, Hypalon, PVC, TPO, smooth-surfaced built-up roofing, metal, modified bitumen, concrete
Unacceptable Substrates: Gravel-surfaced roofing, existing silicone coatings
Colors: White, gray, various other colors
Elastomeric: Yes
Chemical Resistance: Good
Handles Ponded Water: Fair
Handles Foot Traffic: Excellent
Application Method: Brush, roller, spreader, or sprayer
Application Temperature: Above 40°F (4.45°C), below 100°F (38°C), and more than 5°F (3°C) above the dew point and rising
Notes: Solvent-based. Very UV stable, often used as a top coat over an aromatic polyurethane coating. More expensive than aromatic polyurethane. Has a strong odor during application.
Polyurethane (Aromatic) Roof Coatings
Main Components: (This is an example and actual product formulations will vary) diphenylmethane diisocyanate, methylene bisphenyl isocyanate, trimethylbenzene, aromatic hydrocarbons, calcium carbonate (or other extender pigment), xylene
Acceptable Substrates: Spray polyurethane foam, EPDM, Hypalon, PVC, TPO, smooth-surfaced built-up roofing, metal, modified bitumen, concrete
Unacceptable Substrates: Gravel-surfaced roofing, existing silicone coatings
Colors: Gray
Elastomeric: Yes
Chemical Resistance: Good
Handles Ponded Water: Fair
Handles Foot Traffic: Excellent
Application Method: Brush, roller, spreader, or sprayer
Application Temperature: Above 40°F (4.45°C), below 100°F (38°C), and more than 5°F (3°C) above the dew point and rising
Notes: Susceptible to UV degradation, it is not acceptable as a roof surface coating by itself (see above). Used as a base coat beneath an aliphatic polyurethane or other compatible UV-resistant coating. Less expensive than aliphatic polyurethane. Has a strong odor during application.
PUMA Roof Coatings (Polyurethane Modified Acrylic)
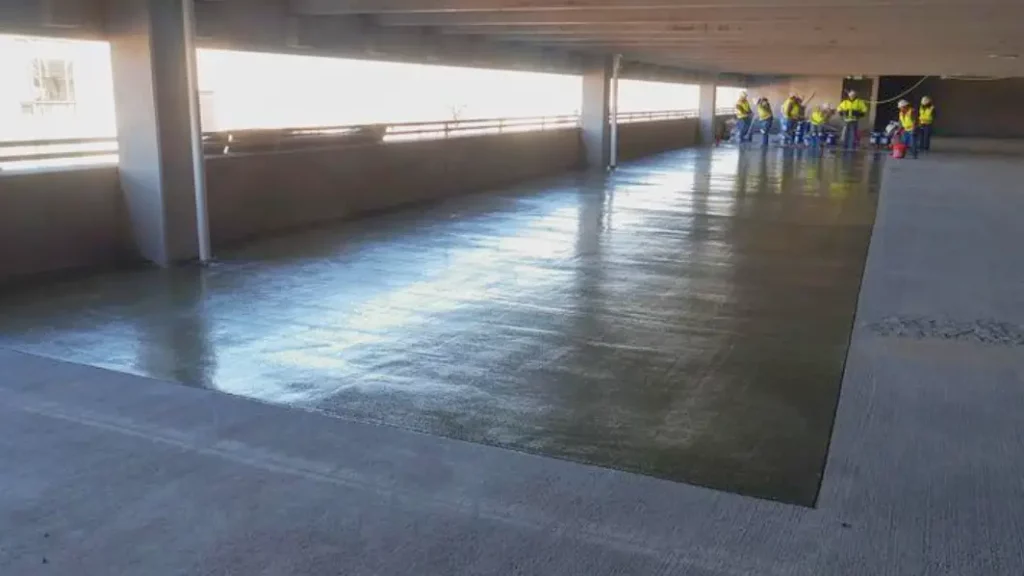
Main Components: (This is an example and actual product formulations will vary) methyl methacrylate, 2-propenoic acid, 2-ethylhexyl ester, titanium dioxide (or other prime pigment), barium sulfate
Acceptable Substrates: Concrete, spray polyurethane foam, metal
Unacceptable Substrates: Consult manufacturer’s technical department.
Colors: White, gray
Elastomeric: Yes
Chemical Resistance: Excellent
Handles Ponded Water: Good
Handles Foot Traffic: Excellent
Application Method: Brush, roller, spray
Application Temperature: Above 40°F (4.45°C), below 100°F (38°C), and more than 5°F (3°C) above the dew point and rising
Notes: PUMA coatings last much longer than typical acrylic coatings. A mixture of polyurethane and acrylic coating chemistry. PUMA coatings are often used to waterproof concrete surfaces that support vehicular traffic, such as in parking garages.
PVDF Roof Coatings (Polyvinylidene Fluoride)
Main Components: (This is an example and actual product formulations will vary) water, N-methyl-2-pyrrolidone, polyvinylidene fluoride resin, acrylic modifier, pigments
Acceptable Substrates: Metal. Other substrates require the application of a compatible base coating.
Unacceptable Substrates: Consult manufacturer’s technical department.
Colors: Various colors available
Elastomeric: Yes
Chemical Resistance: Excellent
Handles Ponded Water: Good
Handles Foot Traffic: Excellent
Application Method: Spray
Application Temperature: Above 60°F (15°C)
Notes: Based on the formulation known as Kynar 500. Very long lasting. Typically applied at the factory.
SEBS Roof Coatings (styrene ethylene butadiene styrene)
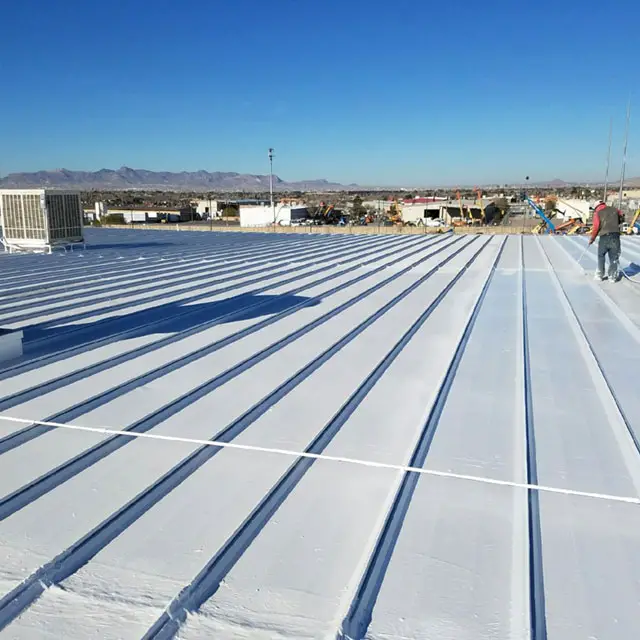
Main Components: (This is an example and actual product formulations will vary) Calcium carbonate, mineral spirits, hydrocarbon resin, styrene/butadiene copolymer
Acceptable Substrates: Hypalon, metal, TPO, other substrates with application of compatible base coat
Unacceptable Substrates: EPDM, KEE, PVC
Colors: White, black, gray, various other colors
Elastomeric: Yes
Chemical Resistance: Fair
Handles Ponded Water: Good
Handles Foot Traffic: Good
Application Method: Brush, roller, spray
Application Temperature: Above 40°F (4.45°C), and more than 5°F (3°C) above the dew point and rising
Notes: Solvent-based. Strong odor during application. Dries quickly. Very compatible with steel roofing. Compared to more common coatings, it has relatively low moisture permeability.
Silicone Roof Coatings
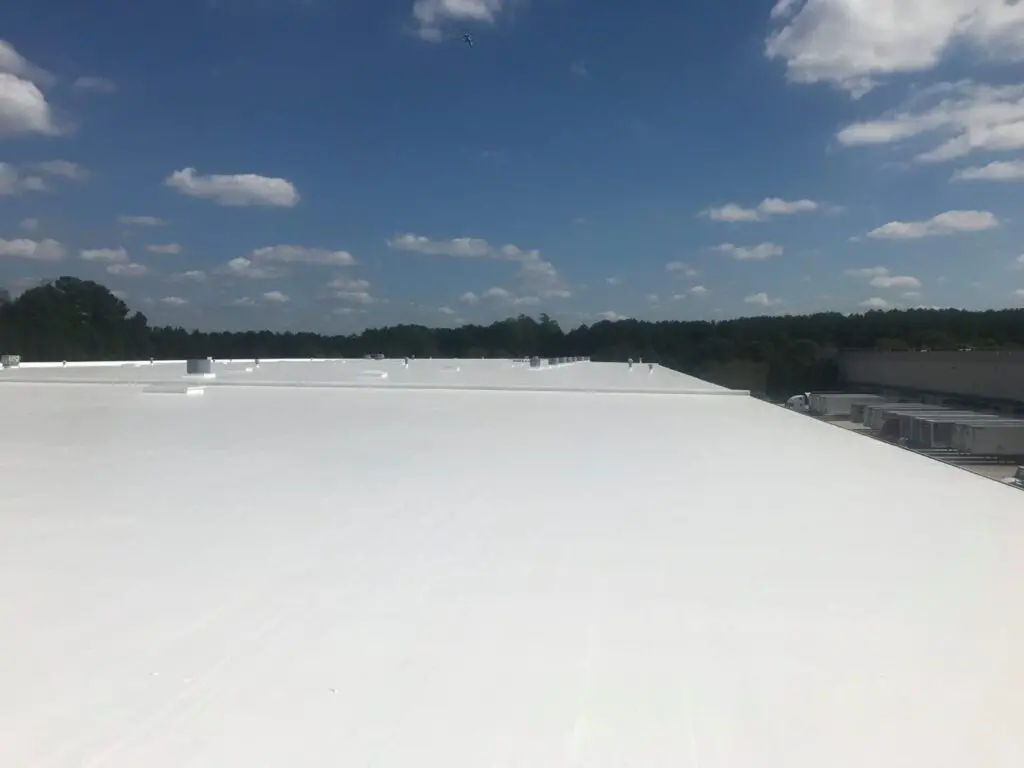
Main Components: (This is an example and actual product formulations will vary) crystalline silica, titanium dioxide (or other prime pigment), petroleum hydrocarbon distillates, methyl oximino silane
Acceptable Substrates: EPDM, Hypalon, PVC, and TPO single-ply membranes, metal roofing, existing roof coatings, spray polyurethane foam
Unacceptable Substrates: Asphalt or coal tar pitch roofing (may be possible with appropriate primer), gravel-surfaced roofing
Colors: White, tan, gray, various other colors
Elastomeric: Yes
Chemical Resistance: Good
Handles Ponded Water: Good
Handles Foot Traffic: Poor
Application Method: Brush, roller, spray
Application Temperature: 35°F (1.7°C) and rising
Notes: Silicone is hard for anything else to adhere to. This restricts re-coating options; generally old silicone coatings must either be removed or re-coated with another silicone coating. Silicone coatings can be much more expensive compared to lower-end acrylic coatings.
Silicone coatings are relatively long-lasting. Silicone coatings can last two or three times as long as most acrylic coatings if properly applied. Silicone roof coatings typically have the longest useful life of all the most common types of roof coatings.
Reinforcement fabric is recommended for many applications, especially at flashings, angle changes, and joints between roof components or sections. Many substrates will need to be primed before a silicone roof coating is applied. Many substrates won’t. It depends on the substrate as well as the specific product. Silicone coating formulations vary from manufacturer to manufacturer.
Always check the product data sheet or contact the manufacturer’s technical department. Application to clean concrete and clean existing silicone coatings can generally be done without priming.
See examples of silicone roof coatings on Amazon.
Soy-Based Roof Coatings
Main Components: Some soy-derived polymers, other components depend on the primary chemistry of the coating, typically polyurethanes or acrylics
Acceptable Substrates: Varies according to the primary chemistry
Colors: White, various other colors
Elastomeric: Usually
Chemical Resistance: Varies
Handles Ponding Water: Varies
Handles Foot Traffic: Varies
Application Method: Brush, roller, spray
Application Temperature: Varies
Notes: Most “soy-based” roof coatings are kind of like salad dressings that are advertised as being made with olive oil, but when you read the ingredients, you find out that half the dressing consists of canola oil and the olive oil is only 5%. It’s important to check what the chemistry of the actual product is before selecting a soy-based coating. The attraction of soy-based coatings is that a renewable resource, rather than petroleum, is being used to produce a portion of the material. It’s a lot like adding ethanol to gasoline that way.