Table of Contents
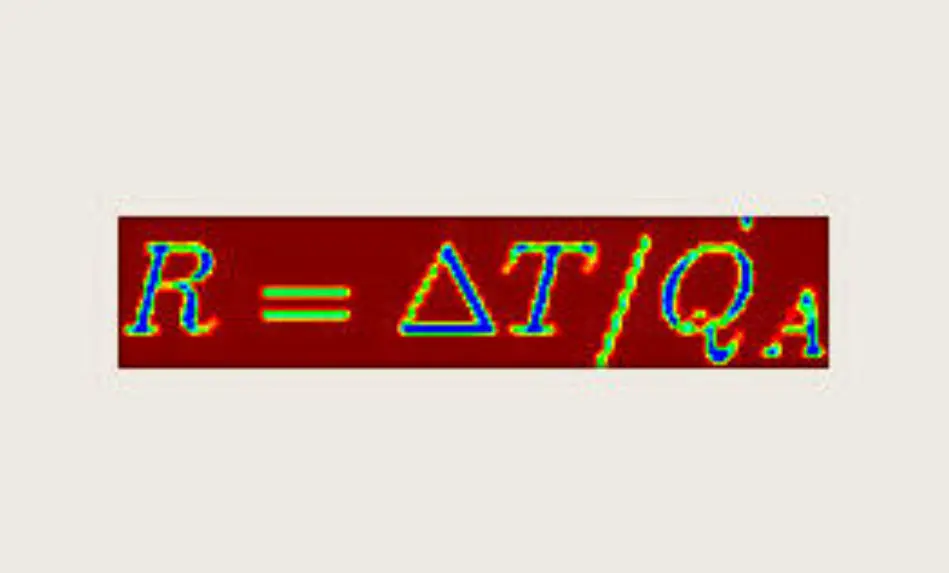
Introduction
R-value is critical attribute of low-slope roofing with above-deck insulation where the roof is a part of the building’s thermal envelope. The code-required roof R-value guides the selection of the type of insulation to be used, the amount of insulation, and the installation method of the insulation. A good understanding of R-value will help the specifier or contractor produce a code-compliant low-slope roof. (Pitched roofs almost never include insulation within the roof system; R-value requirements for most single family homes are typically met through attic or above-ceiling insulation instead.)
R-value measures resistance to heat flow. A higher roof R-value can reduce heating and cooling costs. Energy codes like the International Energy Conservation Code (IECC) set minimum R-values based on climate zone and building type, with periodic updates in order to improve energy conservation. Since these updates usually increase minimum R-value requirements (effectively increasing the amount of insulation you will need), it’s important to be aware of which version of the code is current in your area.
New construction or full roof replacements will have to meet the current roof R-value requirements for the local jurisdiction, but roof recovery systems may allow compliance without adding insulation.
This article should help you better understand how much insulation your new roof will need and why. I’ll discuss how R-value and related measurements are determined, code requirements and how to meet them, and more.
Quick Reference for R-Value
This article gets pretty involved describing R-value calculations, the ins and outs of the building code, and other (relevant!) roofing details you might not be interested in or have time for right now. If you just wanted to look up some basic information, try these links:
1. For minimum required roof R-values by climate zone, see TABLE C402.1.3 (in the 2021 IECC).
2. You can find your climate zone by city or zip code here.
3. To see current minimum roof R-value requirements for roofs with above-deck insulation by state, I recommend this table put together by Carlisle. There’s a chance some of the information may be slightly out of date, but it’s worth taking a look at.
4. If you want to look up the R-values for different types of insulation, see my R-Value Table for 49 Types of Insulation & Roofing Materials.
What is R-Value?
R-value is a number that represents a measurement of the thermal resistance of a material. It tells us how well a material resists heat flow. A higher R-value means better insulation.
To better understand R-value, let’s look at the formulas that define it, what they mean, and how they relate to one another.
Basics: The Concept of Thermal Resistance
R-value is defined as the ratio of temperature difference across a material to the amount of heat transferred per unit area. Mathematically:
1. R-Value Based on Heat Transfer
Formula 1: R-Value Based on Heat Transfer
Where:
- = Thermal resistance (R-value)
- = Temperature difference across the material (°F or K)
- = Heat transfer per unit area (BTU/h·ft² or W/m²)
What is ? (Heat Transfer Per Unit Area)
represents how much heat energy (in BTUs or Watts) passes through a given area of material per unit time. (“Q” comes from “quantity” and “A” comes from “Area”). The standard area used for this equation when determining the general R-value of a material is 1 square foot (1 ft²) in the imperial system and 1 square meter (1 m²) in the metric system.
Units:
- In imperial units: BTU/h·ft² (British Thermal Units per hour per square foot).
- In metric units: W/m² (Watts per square meter).
Lower means better insulation because less heat is being transferred in the given amount of time.
Example:
- If is high, a lot of heat is passing through the material per hour, meaning poor insulation.
- If is low, only a small amount of heat is being transferred, meaning good insulation.
A well-insulated roof may have a large temperature difference () between the interior and the exterior, but low heat transfer (), indicating a high R-value.
2. R-Value Based on Material Properties
Since different materials conduct heat differently, we can express R-value in terms of a material’s thermal conductivity () and thickness ().
Formula 2: R-Value in Terms of Thickness and Conductivity
Where:
- = Thickness of the material (inches or meters)
- = Thermal conductivity of the material (BTU·in/(ft²·h·°F) or W/m·K)
What is ? (Thermal Conductivity)
measures how easily heat moves through a material.
Lower
= better insulation (resists heat flow).
Higher
= worse insulation (allows heat to pass easily).
Units:
- In imperial units: BTU·in/(ft²·h·°F)
- In metric units: W/m·K
Example:
- Metals like aluminum or copper have a very high , meaning they conduct heat easily and are very poor insulators.
- Foam insulation like polyisocyanurate has a low , meaning it resists heat flow and is a good insulator.
Relationship Between , , and
- If a material is thicker ( increases), R-value increases → better insulation.
- If a material has lower thermal conductivity ( decreases), R-value increases → better insulation.
3. How These Two Formulas Are Related
Now, let’s connect these two formulas:
Since R-value depends on thickness () and conductivity (), we can substitute into the first equation like so:
Rearranging:
Main Takeaways:
If you increase insulation thickness (), heat transfer () decreases.
If you use a material with lower thermal conductivity (), heat transfer () decreases.
Both lead to a higher R-value, meaning better insulation.
Using RSI or U-Value Instead of R-Value
While R-value is a standard measure of thermal resistance in the United States, other regions use different metrics to express thermal performance.
RSI (R-Value in SI Units)
RSI (R-Value System International) is the metric system equivalent of R-value and is used in Canada, Europe, and other countries following SI (International System of Units). It is measured in:
RSI = (m² · K) / WWhere:
- RSI = Thermal resistance (metric equivalent of R-value)
- m² = Square meters (unit of area)
- K = Kelvin (unit of temperature difference)
- W = Watts (unit of heat transfer rate)
To convert between R-value (imperial) and RSI (metric), use the following formulas:
RSI = R / 5.678R = RSI × 5.678
For example:
- An R-30 insulation has an RSI of 5.28
- An RSI of 3.5 corresponds to an R-value of 19.87
U-Value (Thermal Conductance)
Instead of R-value, thermal performance may be measured in U-value, especially when rating doors or windows. Insulation product data sheets from Europe often use U-Value as well. U-Value represents the rate of heat transfer through a material or assembly rather than the heat resistance of the material. The letter “U” is used for thermal transmittance (U-value) because it comes from the word “unit”, as in “unit heat loss per unit area”.
Unlike R-value, where higher numbers indicate better insulation, lower U-values indicate better insulation performance. U-value is the inverse of R-value and RSI.
U = 1 / RU = 1 / RSI
For example:
- If an insulation assembly has an R-value of 25, its U-value is 0.04 (in Btu/h·ft²·°F).
- If an assembly has an RSI of 4.5, its U-value is 0.22 (in W/m²·K).
Notes:
- RSI is the standard unit used in metric-based building codes such as Canada’s National Building Code and European regulations.
- U-Value is commonly used in energy modeling and HVAC calculations to express overall heat transfer efficiency.
- Some building codes and energy standards require U-value calculations instead of R-value to account for thermal bridging and overall assembly performance rather than just material thickness.
Conversion Formulas
Conversion | Formula | Example |
---|---|---|
R to RSI | RSI = R / 5.678 | R 20 → RSI 3.52 |
RSI to R | R = RSI × 5.678 | RSI 5 → R 28.39 |
R to U | U = 1 / R | R 30 → U 0.033 |
U to R | R = 1 / U | U 0.04 → R 25 |
RSI to U | U = 1 / RSI | RSI 4.5 → U 0.22 |
U to RSI | RSI = 1 / U | U 0.22 → RSI 4.5 |
R-Value Calculation Walk-through
Given that R-value is calculated using the formula:
where:
- R is the thermal resistance (R-value)
- d is the thickness of the material
- k is the material’s thermal conductivity
In this formula, the thickness d is measured in inches, and the thermal conductivity k is defined as:
k represents the amount of heat (in BTUs) that passes through a material of a given thickness (in inches) over a square foot area per hour for each degree Fahrenheit of temperature difference from one side of the material to the other. The value of k depends on the particular material; different materials have different thermal conductivities.
For example, if a material has a thickness of 2 inches and a thermal conductivity of 0.25 BTU·in/(ft²·h·°F), its R-value would be:
This means that a two-inch-thick installation of the material has an effective R-value of 8. The material itself would typically be described as having an R-value of 4, because when the R-value for a material is stated, it normally indicates the R-value of a 1-inch thickness, regardless of any real-world installation thicknesses. Always using a one inch standard thickness when stating R-value allows materials to be compared more easily.
However, you should be aware that manufacturer product data sheets often list the total R-value of the actual product based on its actual thickness and not the per-inch R-value.
Some types of insulation will have different R-values for the same thickness due to differences in density, and some will even increase in R-value per inch as the total thickness increases. This phenomenon is often observed in materials like polyisocyanurate and phenolic foam, where trapped gas within the insulation contributes to an increase in resistance with additional layers. On the other hand, some materials may lose effective R-value if they are compressed.
The actual R-value of installed insulation will ultimately depend on the type of material, its thickness, and its density.
Common Formats for R-Value Data
- Per Inch of Thickness – This is the most commonly used format and represents the R-value of a material for every one inch of thickness.
- Example: Polyisocyanurate rigid foam insulation has an R-value of approximately R-5.6 per inch, meaning a 2-inch thick board would have R-11.2.
- Total R-Value of a Product – Some manufacturers list the total R-value of an insulation product based on its actual thickness.
- Example: A 3.5-inch fiberglass batt may be labeled as R-13, instead of showing its per-inch R-value.
- Assembly R-Value – This includes the combined thermal resistance of multiple layers in a system, such as a wall or roof assembly.
- Example: A commercial low-slope roof might have an insulation layer with R-30 with additional minor contributions from cover boards and adhesive.
- Effective R-Value – In some cases, an assembly’s thermal performance is adjusted for real-world conditions, such as thermal bridging, aging, or compression.
- Example: Metal fasteners or framing members can create heat-conductive pathways, lowering the effective R-value of the system.
Notes:
- Thicker insulation does not always provide a perfectly linear increase in roof R-value. Some materials, like spray foam, may become less efficient per inch at greater thicknesses.
- R-value is not the only factor in thermal performance. Air sealing, vapor barriers, and installation quality can significantly affect insulation effectiveness.
- Different insulation materials have different R-values per inch.
- Fiberglass batt insulation: ~ R-3.14 to R-4.29 per inch
- Extruded polystyrene (XPS): ~ R-5 per inch
- Spray polyurethane foam (closed-cell): ~ R-6.5 per inch
- See my R-Value Table for a full list
Minimum Roof R-Value Requirements
Low-slope roof systems are typically required to include above-deck insulation so that the roof system will meet the minimum R-value requirements specified by the local energy code. Building and energy codes list required minimum R-values for exterior walls, attics or ceilings, and roof assemblies with above-deck insulation.
These minimum roof R-value requirements vary by location and especially by climate zone. Your local building code will incorporate a version of the IECC (energy code); since the version of the building code that your state uses may be from a different year than the version of the IECC that it uses, it’s important to double check with your local building authority and make sure you’ve got all of this straight. For more about building codes and roofing see my article here.
The minimum required roof R-value in your local jurisdiction is something that you need to take into account when planning a roofing project.
The energy code R-value requirements can be different from state to state and even city to city. When new energy codes are adopted, the required roof R-value is often increased. For instance, the 2021 International Energy Conservation Code (IECC) increased the minimum ceiling insulation R-value from R-49 to R-60 in Climate Zones 4 through 8.
The R-value you need for the new roof system will be a big part of figuring out the type and thickness of the insulation you will have to install.
You can read about the details of the code-required minimum roof R-values for different climate zones in the IECC 2021 Section C402 Building Envelope Requirements. Of course, that’s the 2021 version, which may not be in effect where you are. Also remember that it’s possible that your own jurisdiction may have amended the code, so you should look into that. Several states have amended their energy codes to increase the required roof R-value above what is specified in the International Energy Conservation Code (IECC).
How R-Value Requirements are Determined
The International Energy Conservation Code (IECC) establishes minimum R-value requirements for roof insulation to improve energy efficiency in buildings. These requirements vary based on Climate Zones, which are defined by factors such as temperature, humidity, and precipitation. The United States is divided into Climate Zones 1 through 8, with Zone 1 being the warmest and Zone 8 the coldest.
You can look up climate zone by zip code here.
In the 2021 version of the IECC, the prescriptive R-value requirements for attic insulation in residential buildings are as follows:
- Climate Zones 1-2: R-49
- Climate Zone 3: R-49
- Climate Zone 4: R-60
- Climate Zones 5-8: R-60
For commercial buildings with continuous insulation entirely above the roof deck, the minimum R-values are:
- Climate Zone 1: R-20
- Climate Zone 2: R-20
- Climate Zone 3: R-25
- Climate Zone 4: R-30
- Climate Zone 5: R-30
- Climate Zone 6: R-30
- Climate Zone 7: R-35
- Climate Zone 8: R-35
For example, in Climate Zone 5, which includes regions like the northern parts of Illinois and Ohio, residential buildings are required to have attic insulation with an R-value of R-60. In the same zone, commercial buildings with insulation entirely above the roof deck must have a minimum R-value of R-30.
It’s important to note that these are prescriptive requirements; alternative compliance paths may allow for different roof R-values if overall energy performance can be shown to meet or exceed code requirements. Additionally, local amendments can modify these standards, so it’s essential to consult the specific code adopted in your jurisdiction.
For detailed information and any updates, refer to the official IECC documentation and your local building authority.
What Counts Toward the Total R-Value of a Roof System?
Low-slope (“flat”) roof systems almost always include a layer (or layers) of building insulation. This roof insulation typically comes in 4′ x 4′ or 4′ x 8′ boards, 1 to 3 inches thick, which are fastened or adhered to form one or more layers across the entire roof. This insulation is the primary source of the roof’s total R-value.
In a commercial roof system, the R-values of other components, such as cover boards and certain foam adhesives, may sometimes be included when calculating the total R-value of the system. For example, some high-density polyisocyanurate cover boards have an R-value that can contribute significantly to the overall total. Certain foam adhesives can also provide slight insulation benefits. Energy codes permit these components to be included in the total for the system.
The roof deck, most underlayment, most roof coverings/membranes, and air films cannot be included when calculating the R-value of the system. These materials may have some insulating properties, but they are not typically recognized as part of the effective thermal barrier under energy codes. Spray polyurethane foam is one roof covering that can be included because it doubles as building insulation and provides an average R-value of approximately 6.5 to 7 per inch.
How to Determine the R-Value of a Roof
To calculate the total roof R-value, find the total thickness in inches of each type of insulating material within the roof system.
For each different material, multiply the thickness in inches by the standard R-value per inch for that material. I put together a table of typical R-values where you can look up R-value by material if you want to. You should always check the R-value listed on the manufacturer’s product data sheet for the actual product being used.
Since roof R-value code requirements are so often used as a target when calculating the amount and type of insulation required for a job, the R-value of a product is an important part of the product data provided by insulation manufacturers, and can normally be found on the technical data sheets on their websites. (You can find usually find product data sheets under a “Documents” or “Technical Library” tab or by searching the website for “data sheets”.)
When looking at these data sheets, you should remember that although the standard way of describing the R-value for a given material is per inch, manufacturers often publish the total R-value of a product, reflecting the actual thickness of that particular product.
The total R-value of a roof assembly is calculated by adding up the R-values of all individual layers, assuming there is no significant thermal bridging or other heat transfer mechanisms that reduce effectiveness (this isn’t normally an issue for properly installed above-deck roof insulation).
For example, if a roof assembly contains:
- 3 inches of polyisocyanurate insulation (R-5.6 per inch) → Total: R-16.8
- 2 inches of extruded polystyrene (R-5 per inch) → Total: R-10
- A 1/2-inch thick gypsum board cover board (R-0.5) → Total: R-0.5
- 4 applications of polyurethane foam adhesive between layers (R-0.2 each) → Total: R-0.8
So the total R-value of the assembly is R-28.1. It’s actually pretty simple.
Again, remember that when you’re calculating roof R-value for energy code compliance, the R-value of roof membranes, shingles, tiles, air films, and roof deck materials typically can’t be included in your calculation of total roof R-value for code purposes.
Always check your local code to be sure, but these parts of the roof system are almost always excluded. Generally, only the R-value of actual insulation products can be used. In some cases, thermal resistance values for vapor barriers and specialty underlayments may be considered, but this is uncommon and subject to local code interpretations.
Roof Recovery vs. Roof Replacement
Going with a roof recovery system instead of a full roof replacement can help you avoid the need to add insulation to comply with updated energy code R-value requirements. This can save a lot of money. The IECC distinguishes between roof recoveries and roof replacements, with different insulation requirements for each.
- Roof Recovery: This process involves installing a new roofing layer over the existing one without removing the existing roof covering. According to the IECC, roof recoveries are generally exempt from additional insulation requirements due to updated codes, provided the building’s energy use hasn’t increased. This means you can put on a new roof without putting on more insulation to meet current R-value standards.
- Roof Replacement: This entails removing the existing roof system(s) down to the deck and installing a new roof assembly. In this scenario, the IECC requires that the new roof assembly meet current insulation R-value requirements, which usually means you’ll need more insulation in the new roof than their was in the old roof in order to comply with updated energy codes.
A roof recovery is not an option for roofs that have two (or more) existing roof systems in place, that is, if a roof recovery was done last time, you can’t do it again. Their are also several reasons why a roof recovery may not be a good idea for your roof even if there’s only one existing roof in place. Extensive areas of wet insulation, for instance. Unless your roof is very small, it’s a good idea to get a roof consultant involved before making these decisions.
R-Value for Pitched Roofs
Steep-slope (or “pitched”) roofs will almost never include insulation as a part of the roof assembly. For pitched roofs, energy codes are concerned with ceiling or attic insulation R-value, not roof R-value.
While roof coverings such as asphalt or wood shingles do have a very small as-installed R-value, this is not used when calculating the attic/ceiling R-value for the purpose of meeting energy code requirements.
The insulation which provides the R-value in pitched-roof structures will be underneath the roof deck and therefore considered attic insulation, or it will be above the ceiling assembly and also considered attic insulation.