Table of Contents
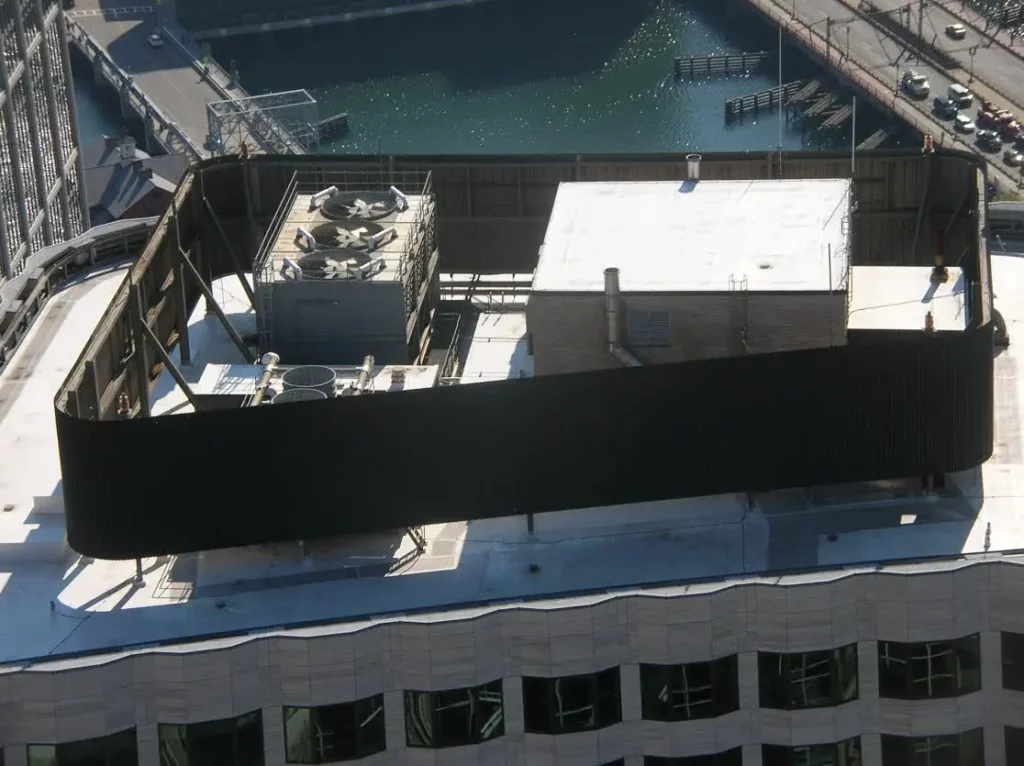
Introduction
Rooftop equipment screens are more than just an architectural afterthought – they serve essential roles in protecting and concealing rooftop mechanical systems. Exposed rooftop equipment is generally an eyesore; equipment screens can give the building a consistent, not unpleasant appearance.
If you’re a building owner, architect, contractor, or facility manager, some understanding of equipment screens is useful for compliance with building codes, mitigating wind loads, reducing noise, and extending the service life of both the rooftop equipment and the roof. Improperly designed or installed screens can become liabilities, leading to structural damage, code violations, and expensive repairs.
Purpose of Rooftop Equipment Screens
A rooftop equipment screen is a barrier, typically non-structural, installed on a roof to conceal HVAC or other rooftop equipment, or to protect the equipment from potentially damaging wind loads. In some cases, these screens may have structural elements, particularly when designed to resist high wind loads or when integrated into the building’s parapet wall or attached to the support structure of the roof.
The use of equipment screens for visual concealment is more common on low-rise buildings where people might see the equipment from the ground, while their use as protection from the wind is more common on high-rise buildings where wind loads are greater.
However, wind mitigation is not limited to tall buildings; low- and mid-rise structures in hurricane-prone regions or areas with high prevailing winds may also require properly engineered screens to prevent damage.
Equipment screens can serve other functions as well, such as reducing noise transmission from mechanical systems, preventing unauthorized access to equipment, and providing shade for rooftop equipment, which may be desirable for certain types of equipment.
Larger or longer rooftop equipment screens are commonly called “screen walls” by roofing professionals. However, industry terminology varies – while ‘equipment screens’ typically refer to non-load-bearing barriers, ‘screen walls’ may sometimes refer to integrated, engineered structures that can bear wind or other loads. In some cases, the term ‘mechanical equipment enclosure’ is used when the structure fully surrounds the equipment rather than acting as a single-plane barrier.
The continuing structural integrity of an equipment screen is important, particularly in areas prone to seismic activity or hurricanes, where additional bracing and anchoring may be required. Improperly secured screens can become hazards in extreme conditions, potentially causing damage to both the equipment and the building itself. Many jurisdictions enforce building codes that regulate wind resistance, seismic stability, and load-bearing requirements for rooftop enclosures.
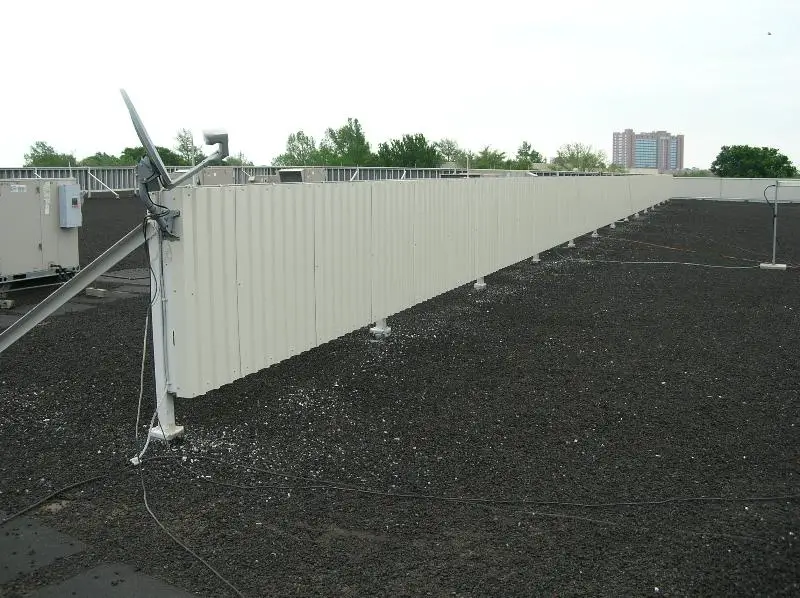
This screen wall was installed for the sole purpose of hiding the rooftop equipment from people in surrounding buildings.
Note that every post penetrates the roof.
Equipment Screen Construction
Equipment screens can be constructed using various materials, including perforated metal panels, louvered assemblies, or solid walls made from fiber cement, composite panels, or reinforced concrete, depending on performance requirements. Some screens are engineered to allow for airflow while still providing adequate concealment. Hinged or removable panel access doors are often incorporated into the design to provide access for equipment maintenance.
A common method of equipment screen construction uses sheet metal panels attached to metal posts, with the posts penetrating the roof membrane and anchored to the roof deck. The posts are typically attached to structural supports under the roof deck to resist wind uplift forces, and the penetration points, being roof penetrations, must be properly flashed and sealed to prevent water infiltration. Depending on the design requirements, posts may be welded, bolted, or anchored with expansion fasteners.
Equipment screens which use non-penetrating supports, secured by concrete or steel weights, are also available. These systems are known as “ballast-mounted” screens; they typically distribute the weight over a large area to avoid damaging the roof membrane.
Non-penetrating systems are generally better for roof system performance (fewer leaks). They are often chosen when adding equipment to existing roofs, where additional penetrations could be difficult or expensive. Due to their reliance on weight for stability, these screens may require higher mass in high-wind regions to prevent displacement.
There are several companies that manufacture modular or custom-made non-penetrating equipment screen systems which are delivered to the site and installed rather than being custom-built in place.
Occasionally, and where sufficient structural support exists, masonry or wood-framed walls will be built on the roof to serve as screens. Masonry screen walls, constructed with brick or concrete block, are durable and provide excellent wind resistance, but they do add significant weight to the roof structure, which typically requires a careful load analysis by a structural engineer before installation.
Wood-framed screens, often clad with composite or fiber-cement panels, are lighter and easier to construct but require weather-resistant finishes to prevent deterioration over time. In some cases, hybrid systems that combine metal framing with composite panels or perforated metal can provide improved airflow while still concealing the equipment.
In high-wind or seismic regions, additional reinforcement, such as guy wires, bracing, or engineered connections to the building’s structural frame, may be necessary to ensure long-term stability. Proper drainage considerations must also be incorporated to prevent water pooling at the base of the support posts, which could accelerate roof membrane degradation. To maintain functionality and longevity, periodic maintenance inspections should be performed to check for fastener loosening, corrosion, or flashing and sealant failures at the roof penetrations.
Building Codes and Equipment Screens
The International Building Code limits the height of rooftop equipment screens to 18 feet (5486 mm), except on buildings of Type IA construction. This restriction is intended to balance structural integrity, wind resistance, and fire safety while preventing excessive loading on the roof structure. Type IA buildings, which include high-rise structures with enhanced fire-resistive construction, are permitted to have taller screens due to their more robust design and greater load-bearing capacity.
Beyond height restrictions, the IBC and other local building codes impose requirements on materials, wind load resistance, and anchoring methods to ensure that equipment screens do not become hazardous in extreme weather conditions. In regions prone to hurricanes, tornadoes, or seismic activity, additional engineering calculations may be required to verify that the screen design meets uplift resistance and lateral force stability criteria. Some jurisdictions also mandate impact-resistant materials for rooftop screens to minimize damage from windborne debris.
Fire codes also play a role in equipment screen placement and design, particularly in scenarios where screens may obstruct firefighting access or interfere with smoke ventilation systems. Certain fire-rated assemblies may be required when screens are installed near shared property lines or adjacent structures. Additionally, screen materials must be non-combustible in many applications, especially when enclosing equipment that generates heat or contains flammable components.
Accessibility regulations, such as those outlined in OSHA and NFPA standards, may also affect screen installation. Where maintenance personnel require access to equipment behind a screen, proper clearance, safety railings, and secure openings must be incorporated into the design to comply with worker safety regulations. In some cases, screening systems must include removable or hinged panels to facilitate equipment servicing.
Local amendments to the International Building Code can further refine height limits and material requirements, making it necessary for designers and contractors to be familiar with jurisdiction-specific regulations before installing rooftop screens. Failure to comply with these standards can result in code violations, fines, or the need for expensive modifications after installation.
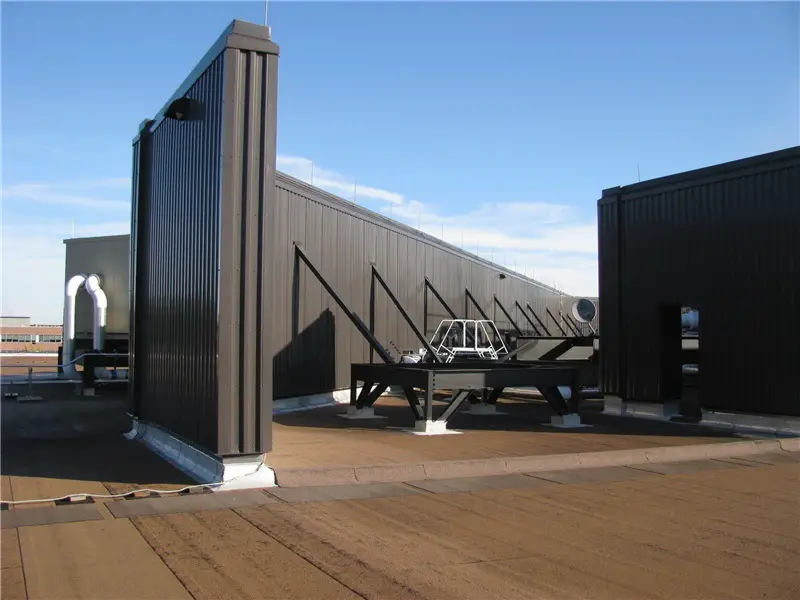
Issues with Rooftop Equipment Screens
Due to the large number of roof penetrations typically required by an equipment screen, they tend to be a common source of roof leaks. As with most roof leaks, water intrusion at these points can lead to membrane deterioration, insulation saturation, and interior water damage. In colder climates, freeze-thaw cycles can exacerbate these issues, causing sealants to crack and flashing components to open up over time.
The flashings or pitch pans at these penetrations should be inspected regularly as part of a preventative maintenance program. Inspection should include checking for deteriorated sealant, loose fasteners, corrosion on metal components, openings in the flashing, and any movement of the equipment screen that could compromise the roof system. In addition to scheduled inspections, it’s a good idea to perform checks after severe weather events, such as high winds or heavy snowfall, as these conditions can dislodge screen supports or stress attachment points.
Other than issues with roof system integrity, improperly secured equipment screens can create structural risks. Screens that are not designed to withstand wind loads may become detached, leading to damage to rooftop equipment or even posing a safety hazard to people on the ground. Over time, vibration from HVAC units or mechanical equipment can loosen fasteners and weaken attachment points, making routine tightening and reinforcement necessary.
Another common issue is poor drainage at the base of the screen wall or around its support posts, which can cause water to pond. This can accelerate membrane degradation and contribute to premature roof failure. To mitigate this, screens should be installed over the structural roof supports where possible, and should be designed with proper clearance above the roof surface, allowing for unimpeded water flow.
References for Equipment Screen Information
1. General: I like this little article/blog post, “Rooftop Equipment Screens” over on Architekwiki. It gives you an architect’s opinion on how equipment screen walls can be used to improve a building’s aesthetics along with some design and construction detail information. (If the link doesn’t send you to the right page, just search for “rooftop equipment screens” on the site’s home page.)
2. Building Codes: “1511.6 Mechanical Equipment Screens” from the 2021 International Building Code. Available at the UpCodes website. Always check with your local building code authority to find out which code is in effect in your jurisdiction and whether there are any pertinent code modifications.
3. Technical: “Rooftop Equipment Wind Load And Its Mitigation For Buildings In Hurricane Prone Regions” discusses research and testing funded by the State of Florida Division of Emergency Management in partnership with the International Hurricane Research Center – Florida International University. Very useful information…”The aim of this research is to develop mitigation techniques that will reduce the wind loading on mechanical rooftop equipment and the forces transferred to the roof supporting structure by the equipment through the use of aerodynamic retrofits such as installation of wind screens.”