Table of Contents
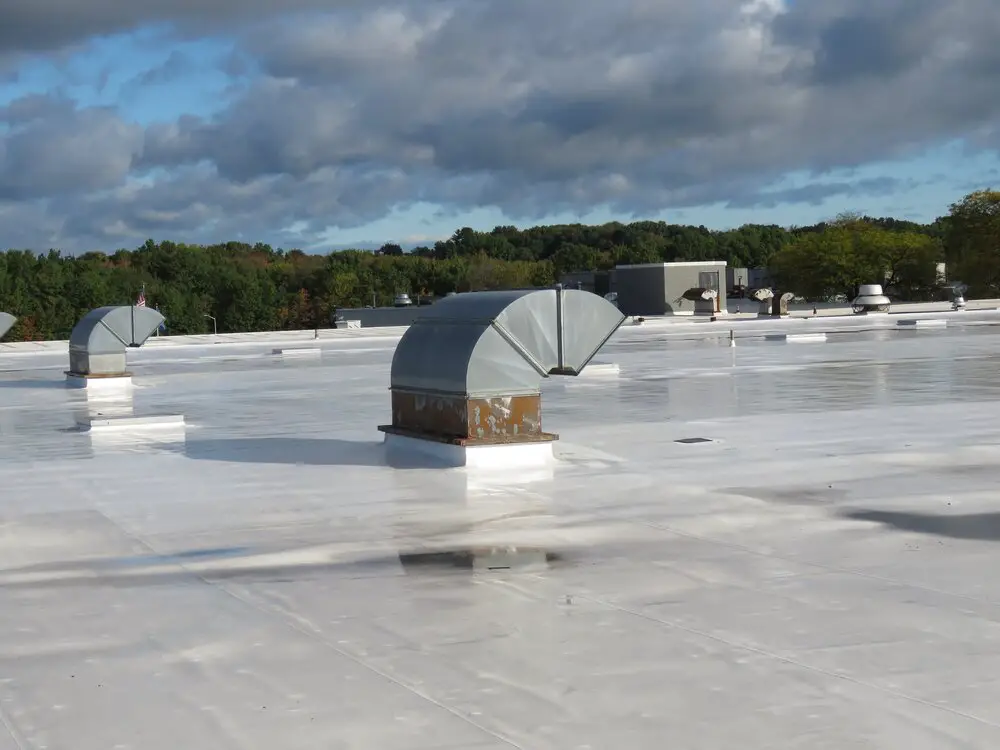
Introduction
An impressive majority of all new commercial roof installations today use a single-ply roofing system. (We’re talking about flat roofs, of course. A single-ply membrane is almost never appropriate for a pitched roof. And a flat roof is more correctly called a “low-slope roof,” by the way.)
Single-ply membranes have gradually gained popularity and overwhelming market share since the 1960s due to their flexibility, relative ease of installation, and their ability to provide a durable, watertight barrier across large surface areas. They also offer various attachment methods, including mechanical fastening, adhesion, or ballasting, which makes them adaptable to different building structures, price points, and environmental conditions.
Before single-ply took over the roofing industry, almost all low-slope roofs were built-up roofs (BUR), using reinforced layers of either asphalt or coal tar pitch to create the roof membrane.
Although modifications and reformulations of single-ply materials sometimes leads to a roofing manufacturer claiming that their product is a new type of membrane, there are basically eight commonly recognized types of single-ply roof membranes found on roofs today. These materials can be categorized based on their chemical composition and installation method, and each offers somewhat different performance characteristics in terms of durability, weather resistance, geographical suitability, and energy efficiency.
I am going to list them here and provide some basic information about each one. For cost information about single-ply roof installation, see my Single-Ply Roofing Cost Guide.
What is Single-Ply Roofing?
Single-ply systems were first called “single-ply systems” to distinguish this type of roofing from hot asphalt and coal tar pitch built-up roofing systems. Built-up systems have membranes formed from multiple layers of bitumen and reinforcement felts, which are called “plies.” These multi-layered systems have been widely used for decades, but the development of single-ply membranes introduced a different approach—one that relies on a single, flexible sheet of material to provide waterproofing and protection.
According to the Glossary of Roofing Terms published by the International Institute of Building Enclosure Consultants (IIBEC), the official definition of single-ply roofing is as follows:
“A roofing system in which the principal roof covering is a single layer flexible membrane, often of thermoset, thermoplastic, or polymer modified bituminous compounds. Generally, there are six types of single-ply roofing systems: 1) Fully-adhered, 2) Loose-laid, 3) Mechanically-fastened, 4) Partially-adhered, 5) Protected membrane roof, and 6) Self-adhering.”
These six types refer to the attachment method of single-ply roofs, not to the type of material used in the single-ply membrane system. The choice of attachment depends on various factors, such as building structure, environmental conditions, and wind uplift requirements.
Single-ply roofing membranes are also classified according to whether the roofing materials are thermoset or thermoplastic. This distinction is important because it affects how the material behaves under heat, how seams are joined, and how repairs are performed.
Thermoplastic Single-Ply Membranes
Thermoplastic single-ply roofing membranes are made of various types of synthetic polymers (TPO, PVC) that can be softened under high heat and will return to its normal form when the temperature decreases. A thermoplastic single-ply membrane can be heated to the point of workability (typically around 1000 °F) and then cooled again without destroying its original properties.
This allows for hot-air welding, where different pieces of the material are welded together, creating seams that are often stronger than the field of the membrane itself. This roof installation technique eliminates the need for adhesives or tapes at seams, reducing the risk of seam failure over time. This is significant; a big issue with early EPDM membrane roofs, which are thermoset and dominated the single-ply market in the 1970s and ’80s, was seam failure. (I should note that EPDM seam issues have been resolved at this point.)
Thermoplastics tend to have higher tensile strengths than thermosets, which makes them more resistant to punctures and tears. In addition to durability, thermoplastic membranes are typically manufactured with white, reflective surfaces that can improve energy efficiency by reducing the amount of heat from the sun that is transmitted into the building.
Thermoset Single-Ply Membranes
Thermoset single-ply roofing membranes are made of various synthetic rubbers (elastomers). They are called “thermoset” because the material permanently hardens, or sets, when heated during the manufacturing process. This process, known as vulcanization, permanently changes the structure of the material.
Thermosets form a chemical bond when subjected to heat at the time of production. The heat causes the molecules in the material to cross-link and form an irreversible bond, making it impossible to re-soften or melt the material without destroying its original properties. Because of this, thermoset membranes must be joined using adhesives or special seam tapes rather than heat welding.
Thermoset materials cannot be melted or reshaped like thermoplastic materials once they have fully cured. This characteristic makes them exceptionally stable over time, with strong resistance to UV radiation and ozone exposure. Unlike thermoplastics, which may degrade when repeatedly exposed to high temperatures, thermosets maintain their performance without softening or becoming brittle.
EPDM is by far the most common (probably the only type most roofers have ever seen) thermoset roof membrane material used today. Its high flexibility, exceptionally long service life potential, and ability to withstand extreme temperature fluctuations make it a preferred choice for many low-slope roofing applications. It is often installed in very large sheets, minimizing the number of seams required, which reduces potential weak points in the system.
Is Modified Bitumen a Single-Ply Roof Membrane?
There is some confusion in the roofing industry as to whether modified bitumen systems should be placed in the single-ply category or considered a built-up roof system. Over the years, I’ve seen various reputable roofing industry experts categorize modified bitumen as both.
A modified bitumen roof membrane isn’t really built-up on site the way a true built-up roof system is, although a case can be made that out of all other roof systems, it’s most similar to a BUR. I prefer to think of modified-bitumen as it’s own separate type of roofing.
I don’t consider modified bitumen to be a single-ply roof membrane for the simple reason that almost all modified bitumen roofs have two plies.
Attachment Methods for Single-Ply Membrane Roofing
The overwhelming majority of single-ply roof systems are installed using one of three attachment methods:
Fully-Adhered Systems
Fully-adhered means that the entire single-ply roof membrane is bonded to the cover board or the above-deck insulation with a specially-formulated membrane adhesive. This adhesive can be water-based, solvent-based, or a low-rise foam, depending on the specific membrane type and manufacturer recommendations.
The rest of the single-ply membrane system (the insulation and cover board under the membrane) may be attached to the roof deck using either adhesives or fasteners, but no fasteners will penetrate the single-ply membrane itself in a fully-adhered system, which is a benefit of this method. Not having mechanical fasteners can also eliminate the risk of thermal bridging (which reduces insulation effectiveness and leads to energy loss).
Fully-adhered systems tend to suffer from membrane shrinkage far less than mechanically-attached and especially ballasted systems. The continuous bond to the substrate also prevents membrane wrinkling or displacement over time.
Fully-adhered systems are lightweight and suitable for various building sizes and shapes, including high-slope applications. They are particularly good for irregular roof configurations, where securing the membrane with mechanical fasteners may be impractical. Fully-adhered membranes also perform well in high-wind zones, as the uniform attachment helps minimize the risk of wind damage.
Installation requires a very dry and very clean substrate; small debris, moisture, and any dust can interfere with the adhesive’s effectiveness.
This method typically results in the longest-lasting roof, everything else being equal.
Mechanically-Attached Systems
The term “mechanically-attached” (also “mechanically-fastened”) most often means that the single-ply membrane sheets are individually fastened down into the roof deck using lines of fasteners, which are normally hidden inside the seams that join the sheets together, where the sheets overlap. The fasteners are typically specialized screws, with metal or plastic plates designed to distribute the load and prevent damage to the membrane.
Sometimes a mechanically-attached system will not use the seams, and the lines of fasteners will simply be installed at regular intervals across the roof, each line being covered by another separate strip of membrane material. This approach is sometimes preferred for membranes with wider sheets or when additional reinforcement is needed to combat wind uplift.
Sometimes batten strips (flat, narrow strips of plastic or metal) will be included along the fastener lines for increased securement. The screws are fastened through holes in the battens and the battens increase the actual securement area. Batten bars can improve wind uplift resistance, particularly in areas prone to high wind speeds.
These systems are lightweight and can be used for buildings of all sizes and configurations. Because they do not require adhesives, they can be installed in a wider range of weather conditions compared to fully-adhered systems.
This method normally results in the second longest-lasting roof, everything else being equal. While mechanically-attached systems can be durable, their lifespan can be influenced by factors such as fastener corrosion, potential fluttering of the membrane in high winds, and the wind uplift forces being continually concentrated on the seams.
Ballasted Systems
“Ballasted” refers to an attachment system in which all of the layers of the roof system are loose-laid, without using any fasteners or adhesives. Ballasted systems depend on ballast weight to hold the entire roof system in place, making installation simpler and quicker compared to the other methods.
Ballasted single-ply roofing systems offer a quick installation at a relatively low cost. The absence of adhesives and fasteners reduces labor costs and installation time significantly.
The ballast used for securing roof systems normally consists of river-washed stones (no sharp edges), usually around 1 to 3 inches in diameter, concrete pavers, or a combination of the two. The ballast is installed uniformly across the entire surface of the roof.
It’s common to see stone ballast used on most of the roof, with the heavier and more stable concrete pavers installed at the corners for increased wind resistance. Since wind uplift is generally strongest at the perimeter and corners of a roof, additional weight in these areas helps keep the membrane securely in place.
Because of the additional weight the ballast adds (typically from 10 to 20 pounds per square foot), the use of these systems are limited to buildings with structural capacity to support the additional load. Before a ballasted system is specified, a structural engineer should assess whether the roof deck can support the ballast load without excessive deflection or stress.
Installation of ballasted systems is generally considered to be the easiest among all types of roofing systems. Unlike mechanically-attached or fully-adhered systems, ballasted roofs require minimal surface preparation and can be installed relatively quickly, even in less-than-ideal weather conditions.
The ballast is usually installed directly on top of the single-ply roof membrane, although a geotextile may be laid over the membrane first to protect it from the ballast. This protective layer prevents punctures or abrasions caused by shifting ballast materials over time, especially as time goes by and the ballast stones fracture due to thermal cycling.
Ballasted systems usually have the shortest service life, with the shortest warranty periods. The lifespan of these systems can be affected by membrane movement, membrane shrinkage, and difficulty in locating and repairing leaks. In my experience, ballasted systems are more prone to leaking than the others.
Regular maintenance should be performed to ensure the ballast remains evenly distributed and that no areas of the membrane become exposed. Areas without ballast coverage can quickly become a problem as the wind will agitate the loose membrane, and the unsecured area will get bigger and bigger.
Types of Single-Ply Membrane Materials
CPE (Chlorinated Polyethylene)
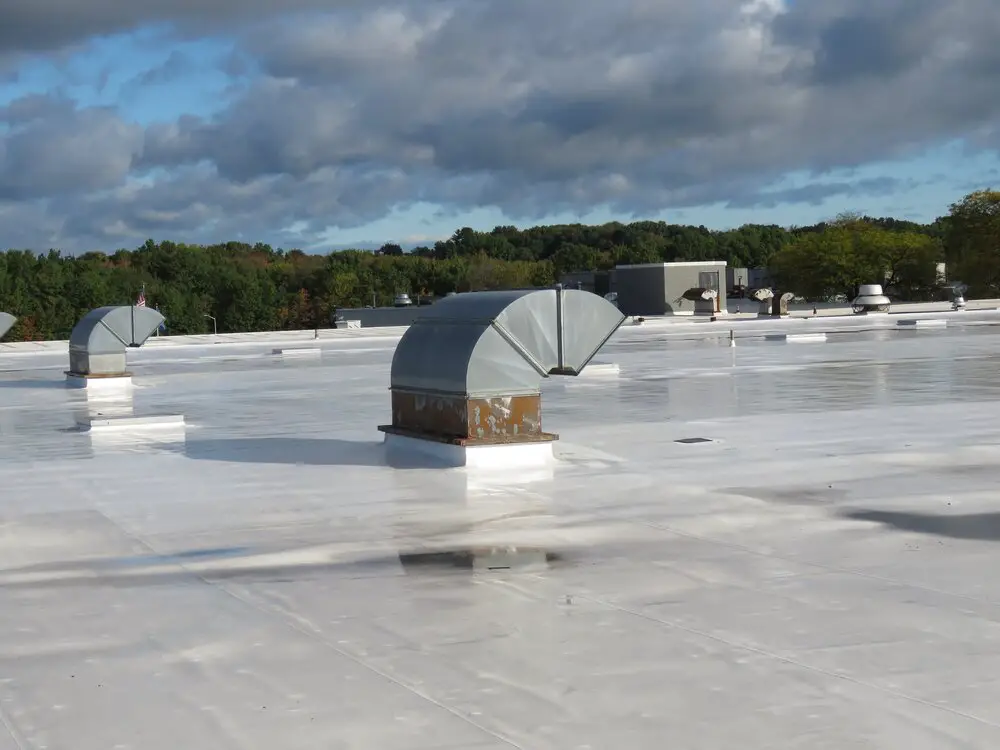
Colors: White, Gray
Attachment Method: Fully-Adhered, Mechanically Fastened, Ballasted
Seaming or Patching Method: Hot Air Welded
Asphalt Compatibility: Good
Resistance to Oils, Coolants, and Grease: Excellent (but not gasoline)
In Use Since: 1970s
Although CPE is not a commonly used single-ply roofing membrane, it is still manufactured and can sometimes be found on commercial roofs. I’ve personally seen more than one existing roof that had a CPE membrane. CPE is similar to CPSE (Hypalon) membranes, both being chlorinated polyethylene-based materials designed for enhanced weatherability and resistance to chemicals.
CPE roofing membranes were introduced in Europe in 1973 and in the United States in 1978. Originally marketed as an alternative to other thermoplastic single-ply systems, CPE offers good chemical resistance, excellent UV stability, and compatibility with a variety of adhesives. CPE does not need plasticizers to make it flexible and elastic, but it tends to shrink a lot, so most CPE membranes are reinforced. This reinforcement is typically polyester or fiberglass, helping to control dimensional changes over time.
Some manufacturers claim that CPE does not cure and remains thermoplastic indefinitely, but this is not entirely true based on real-world experience. CPE does have a tendency to cure after installation, which can make repairing the membrane more difficult as it ages. As the material ages, the surface may become less responsive to heat welding, requiring additional preparation before performing repairs or modifications.
Repair procedures may have to include cleaning, treatment with solvent, priming, and the use of a pressure-sensitive adhesive. In cases where the membrane has aged significantly, repairs may require a specialized primer designed to reactivate the surface before a patch or seam is applied. Contractors experienced with older CPE roofs sometimes use a combination of solvent wiping and hot-air welding to achieve a strong repair bond.
CPE does well with asphalt, and manufacturers have been known to allow CPE membrane installation using asphalt as an adhesive. This makes it somewhat unique among thermoplastic membranes, as most thermoplastics are generally incompatible with asphalt-based adhesives. The ability to bond with asphalt can be useful in re-roofing applications where an existing asphalt-based system is present, reducing the need for extensive tear-off.
CSPE “Hypalon” (Chlorosulfonated Polyethylene)
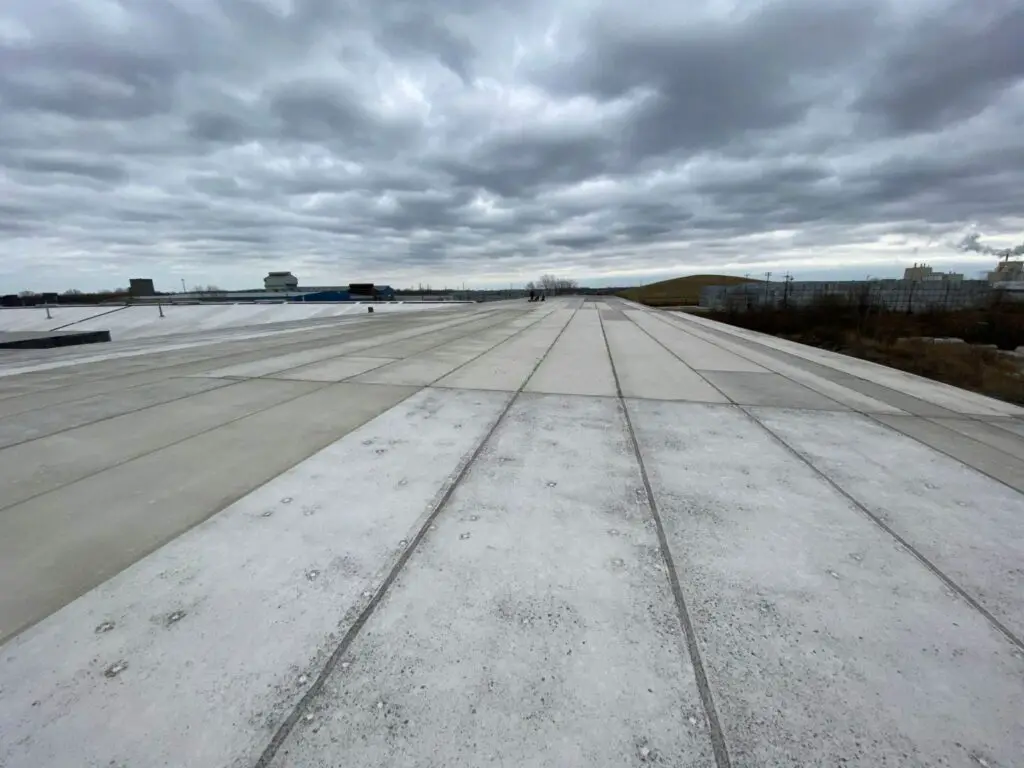
Colors: White (typical), Various Others
Attachment Method: Fully-Adhered, Mechanically Fastened, Ballasted
Seaming or Patching Method: Hot Air Welded (typical), Adhesive
Asphalt Compatibility: Good
Resistance to Oils, Coolants, and Grease: Animal Fats – Excellent; Petroleum – Fair
In Use Since: Mid-1960s, US production stopped in 2009
To learn more about Hypalon, see my article on CSPE Roofing.
Hypalon is a type of roofing material formerly used in low-slope (“flat”) roofing applications. It is made of chlorosulfonated polyethylene (CSPE), a synthetic rubber material that is highly durable and resistant to environmental factors such as UV radiation, ozone, and extreme temperatures. Its chemical composition allows it to combine the best properties of thermoset and thermoplastic membranes, making it unique among single-ply roofing materials.
“Hypalon” was a trademarked name used by DuPont for their chlorosulfonated polyethylene (CSPE) membrane products. However, DuPont discontinued production of Hypalon in 2009, and the trademark is no longer in active use. Despite this, “Hypalon” is still commonly used in the industry to refer to CSPE roofing membranes.
Hypalon roof membranes were installed as fully adhered, mechanically attached, or ballasted systems. They are known for their excellent resistance to chemicals and pollutants, which made them a popular choice for industrial and commercial roofing applications. Because of its high durability, Hypalon was often used in environments with high levels of chemical exposure, such as factories, processing plants, and refineries.
One of Hypalon’s distinguishing characteristics is its ability to undergo post-installation curing. When first installed, Hypalon behaves like a thermoplastic material, allowing for heat-welded seams. Over time, it gradually cures into a thermoset material, making repairs and modifications more difficult as the membrane ages. This curing process can make older Hypalon roofs more challenging to maintain, as hot-air welding may no longer be effective for patching or seam reinforcement.
DuPont stopped production of Hypalon roofing membranes in the United States largely due to environmental concerns related to the manufacturing process and regulatory restrictions on some of its chemical components. However, many existing Hypalon roofs remain in service, as the material was known for its long lifespan when properly maintained. Owners of older Hypalon roofs often face challenges in sourcing compatible materials for repairs, requiring the use of specialty primers, adhesives, or alternative membrane patches.
EPDM Rubber (Ethylene Propylene Diene Monomer)
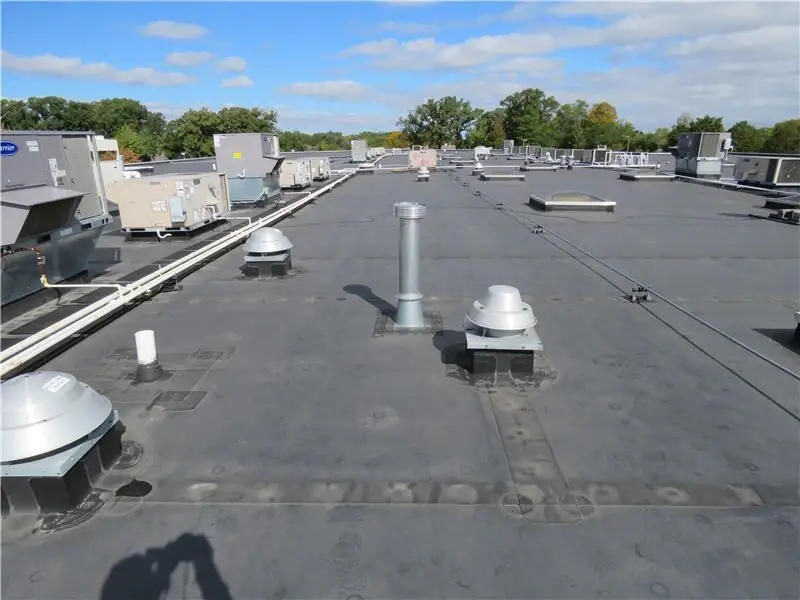
Colors: Black (typical), White
Attachment Method: Fully-Adhered, Mechanically Fastened, Ballasted
Seaming or Patching Method: Adhesive or Adhesive Tape
Asphalt Compatibility: Poor to Fair
Resistance to Oils, Coolants, and Grease: Poor (for petroleum-based oils); Moderate (for animal and vegetable oils)
In Use Since: 1970s
EPDM, which stands for ethylene propylene diene monomer, is a type of roofing membrane made from a highly durable synthetic rubber material more properly referred to as ethylene propylene diene terpolymer. An EPDM single-ply membrane is often referred to as a rubber membrane.
Highly flexible sheets of EPDM are commonly used in low-slope roof applications on buildings both in the United States and around the world. It is one of the most widely used single-ply roofing materials globally, covering billions of square feet of commercial and industrial roofs. Its main ingredients, ethylene and propylene, are derived from oil and natural gas sources.
An advantage of an EPDM rubber membrane is excellent resistance to UV rays, extreme heat, ozone, and other environmental factors, which gives the EPDM field membrane one of the longest lifespans of all single-ply materials.
EPDM, which is commonly black, can also (rarely) be found in white. It comes in different widths, ranging from 7.5 feet to 50 feet, and in three common thicknesses: 45-mil, 60-mil, and 90-mil. You can install EPDM fully adhered, mechanically attached, or ballasted. The membrane seams between the individual EPDM sheets use in the roofing system can be bonded with liquid adhesives or specially formulated tape.
Currently, about 30 percent of EPDM roofing installations use ballasted systems, down significantly over time as fully-adhered and mechanically-attached systems have grown in popularity.
Mechanically-attached systems typically use scrim-reinforced EPDM membranes, although non-reinforced material can also be used depending on the building owner’s requirements.
Fully-adhered EPDM roofing systems can be installed using rolls up to 30 feet by 100 feet, reducing the number of seams. However, 10-foot or 20-foot-wide rolls are more commonly used because they are easier for roofers to handle. Both non-reinforced and scrim-reinforced membranes can be used, but non-reinforced EPDM is more common for fully-adhered applications.
EPDM roofing is the second-most popular single-ply roofing system (behind TPO roofing systems). TPO has overtaken EPDM in new installations, but EPDM remains widely used, especially in northern climates where the advantage of a white membrane is negligible, due to its long service life and reliability.
EPDM roofing systems are commonly used in commercial and industrial roofing applications but can also be used in residential applications, particularly on low-slope or flat roofs.
KEE/PVC (Ketone Ethylene Ester + Polyvinyl Chloride)
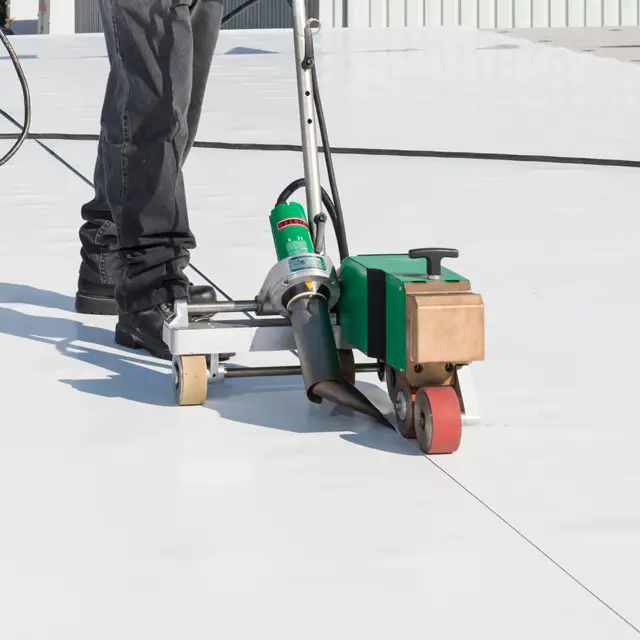
Colors: White, Gray, Tan (custom colors available)
Attachment Method: Fully-Adhered, Mechanically-Fastened, Ballasted
Seaming or Patching Method: Hot Air Welded
Asphalt Compatibility: Good
Resistance to Oils, Coolants, and Grease: Good
In Use Since: 1980s
PVC KEE membrane is a relatively new type of roofing material, developed in the 1980s, but not widely used until the late 1990s. KEE stands for Ketone Ethylene Ester, which is a polymer that is added to PVC (polyvinyl chloride) to make the roofing material more durable, flexible, and resistant to environmental factors. The addition of KEE enhances the performance of standard PVC membranes, making them more resistant to plasticizer migration, which can lead to membrane brittleness over time.
The KEE/PVC roofing membrane is made of a single layer of thermoplastic material that is heat-welded together to form a continuous membrane over the roof surface. These systems are known for durability, resistance to punctures and tears, and exceptional performance in harsh environments. KEE/PVC membranes offer superior chemical resistance, standing up well to UV rays, acid rain, industrial pollutants, and exposure to harsh chemicals.
KEE/PVC roofing membranes are commonly used in commercial roofing applications, particularly in environments where exposure to oils, kitchen grease, or harsh chemicals is a concern. This makes them an ideal choice for restaurants, food processing facilities, airports, and manufacturing plants where traditional PVC might degrade more quickly. They are also more suitable for high-traffic roof areas, as the enhanced durability of KEE-modified membranes allows them to withstand foot traffic and mechanical wear better than standard PVC.
In addition to commercial use, KEE/PVC membranes can also be used in residential applications, particularly in cases where homeowners require a long-lasting, low-maintenance, and energy-efficient roofing solution. These membranes are available in a range of colors and thicknesses, allowing for customization based on project-specific needs. Some manufacturers offer cool roofing formulations, which enhance reflectivity and contribute to improved energy efficiency by reducing heat absorption.
PIB (Polyisobutylene)
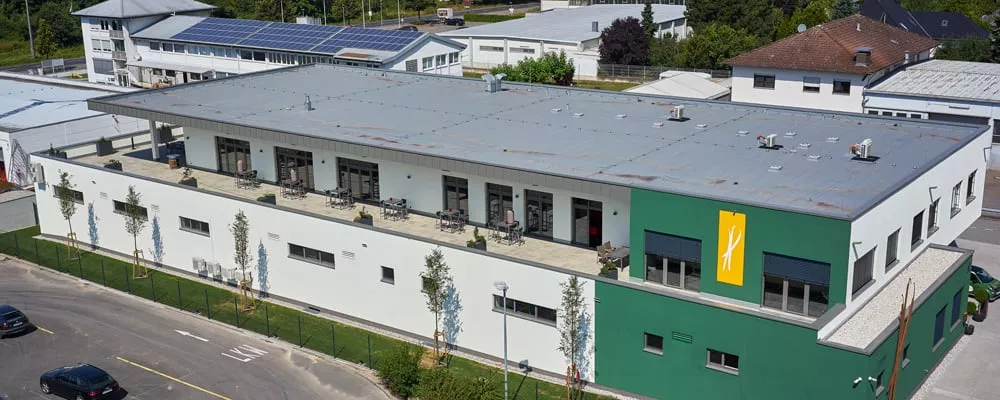
Colors: Black, Gray, White
Attachment Method: Fully-Adhered, Mechanically-Fastened, Ballasted
Seaming or Patching Method: Adhesive or Hot Air Welded
Asphalt Compatibility: Good
Resistance to Oils, Coolants, and Grease: Poor
In Use Since: 1930s
PIB (polyisobutylene), which was created in the 1930s, is the world’s oldest single-ply roofing system. Some roofs made with this material have been in use for over 50 years and are still functional, a testament to its durability and long-term weathering performance. Unlike some other roofing materials that degrade significantly over time, PIB membranes retain their elasticity and resistance to cracking, making them one of the more reliable legacy roofing options.
PIB was a more common roofing system before the advent of EPDM in the 1970s, and especially before TPO began to dominate the commercial roofing market starting in the 1990s. While other materials gained popularity due to cost and availability, PIB remained a niche choice for projects requiring exceptional longevity and resistance to environmental degradation.
It’s unusual to run across a PIB membrane these days, although they are still being manufactured and used in select applications. Some European manufacturers continue to produce PIB membranes, particularly for specialized commercial and industrial applications where long-term performance and environmental sustainability are priorities.
PIB is relatively safe for the environment. The PIB membrane has undergone a full life cycle assessment to ISO14040, which indicates the product has no significant environmental impact. Additionally, PIB membranes are often fully recyclable at the end of their service life, making them an attractive option for sustainability-focused projects.
PIB membrane has a self-sealing edge, which simplifies installation somewhat by reducing the need for additional adhesives or heat welding at seams. This characteristic also improves waterproofing reliability, as the edges bond naturally without creating excessive stress points.
PIB is normally only available in gray, but there is a copper paint finish (copper flakes suspended in a PIB carrier), which weathers to the color of a natural copper patina. This specialty finish provides an aesthetic option for buildings where a metallic appearance is desired while still benefiting from PIB’s durability and flexibility.
PVC (Polyvinyl Chloride)
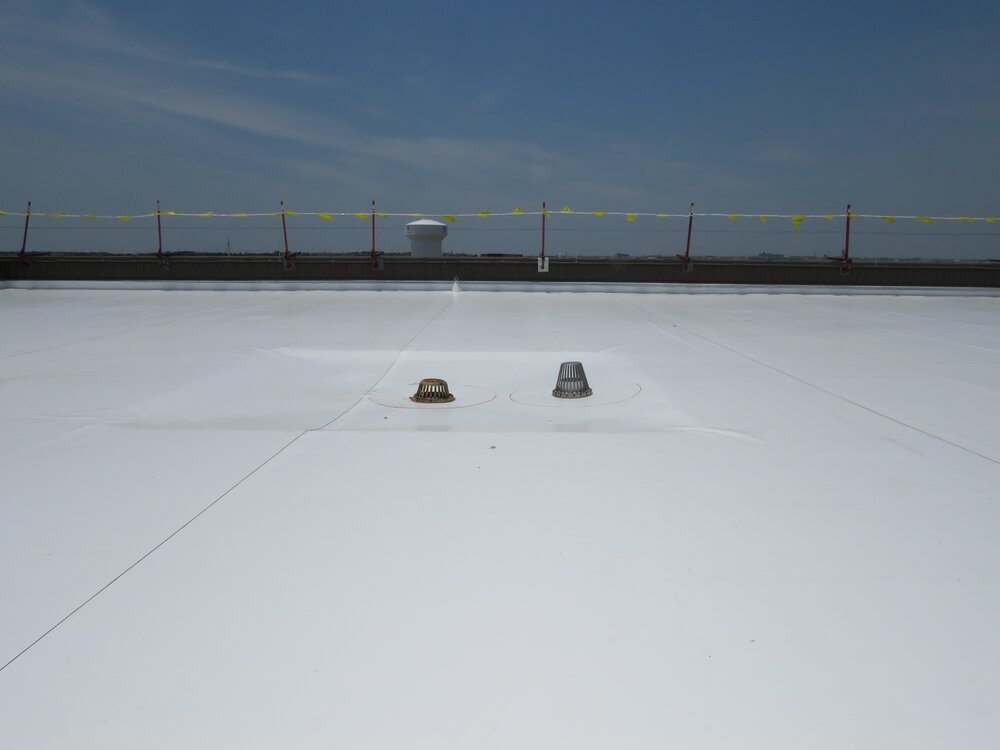
Colors: White, Gray, Tan (custom colors available)
Attachment Method: Fully-Adhered, Mechanically-Fastened
Seaming or Patching Method: Hot Air Welded
Asphalt Compatibility: Poor
Resistance to Oils, Coolants, and Grease: Fair
In Use Since: Late 1960s
To learn more about PVC, see my article on PVC Roofing.
PVC (polyvinyl chloride) roof membranes are widely used on commercial and industrial buildings. PVC rounds out the big three in the world of single-ply roofing membranes, being the third-most popular membrane after TPO and EPDM. It’s a good choice for environments where chemical resistance and resistance to mechanical damage are critical.
It has been a trusted low-slope roofing option ever since the 1980s, after early issues with the fracturing of unreinforced PVC membranes were dealt with by adding a reinforcement scrim to the membrane and reformulating the plasticizers used to keep the membrane flexible.
PVC is a thermoplastic; thermoplastic membranes are installed by joining the individual sheets together with heat-welded seams, and they can be repaired using heat-welded patches for the life of the roof. Because PVC membranes remain weldable even after years of service, they offer an advantage over some other materials that degrade or become more difficult to patch as they age.
Chemical plasticizers are added to the PVC during the manufacturing process to ensure flexibility throughout the life of the roof. These plasticizers prevent the membrane from becoming brittle, especially in cold temperatures, helping to maintain long-term performance. Some manufacturers also offer KEE (Ketone Ethylene Ester)-reinforced PVC (see above), which improves plasticizer retention and enhances durability.
PVC is highly resistant to UV rays, chemicals, and extreme temperatures. It is particularly resistant to oils, animal fats, and many industrial chemicals, making it a preferred choice for buildings such as restaurants, food processing plants, chemical facilities, and airports. Unlike some other roofing materials, PVC will not significantly deteriorate when exposed to grease, making it ideal for rooftops with kitchen exhausts.
PVC roofing is relatively tough and long-lasting. It can resist foot traffic better than some other roofing systems, making it suitable for roofs with frequent maintenance access or heavy mechanical equipment.
Another advantage of PVC roofing is that it is highly fire-resistant, with inherent flame-retardant properties that help prevent the spread of fire. It is also highly resistant to mold and bacterial growth, which can contribute to long-term durability in humid environments.
It can last for decades if installed correctly and receives proper maintenance. Many high-quality PVC membranes can exceed 30 years of service life.
The white PVC membrane is also known for its high reflectivity, which minimizes energy usage by reflecting sunlight and reducing heat absorption by the building. Many PVC membranes meet Cool Roof and Energy Star requirements, making them an excellent choice for energy-efficient roofing applications. Some manufacturers also offer colored PVC membranes with high reflectivity, allowing for custom aesthetics while maintaining high solar reflectance.
PVC roofing is fairly easy to install and repair, making it a cost-effective option. While it is typically more expensive than TPO upfront, its durability, long-term weldability, and chemical resistance can provide a lower lifecycle cost compared to some other roofing materials.
PVC roofing is available in white, gray, and tan. It is also available in a variety of thicknesses, including 50-mil, 60-mil, and 80-mil membranes. PVC membranes are reinforced with polyester or fiberglass scrim for added tensile strength and improved puncture resistance.
TPE (Thermoplastic Polyolefin Elastomer)
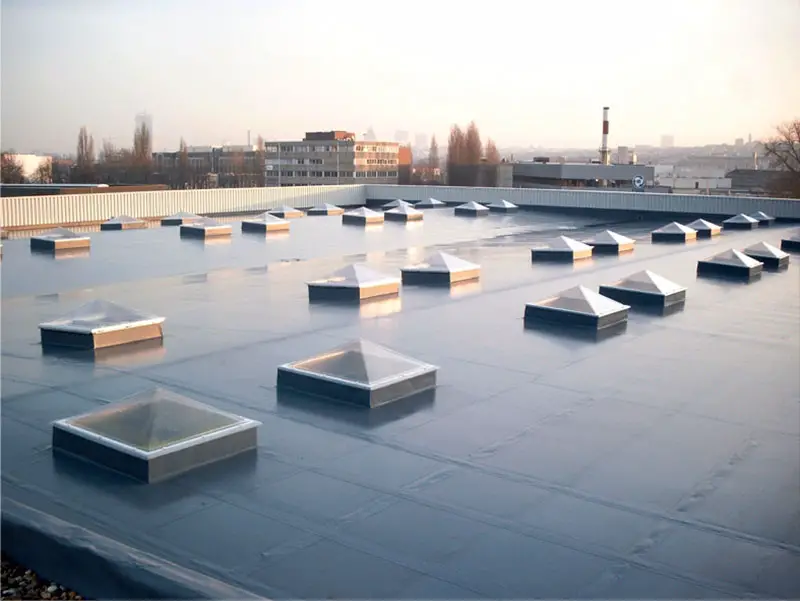
Colors: Gray
Attachment Method: Fully-Adhered, Mechanically-Fastened, Ballasted
Seaming or Patching Method: Hot Air Welded
Asphalt Compatibility: Good
Resistance to Oils, Coolants, and Grease: Animal Fats – Excellent; Petroleum – Poor
In Use Since: 1990s
TPE stands for thermoplastic polyolefin elastomer. This is a relatively new roofing product developed to improve on some of the drawbacks of regular TPO roofing membranes while retaining many of the desirable properties of thermoplastic roofing. By addressing installation difficulties, seam welding sensitivity, and long-term flexibility issues, TPE has emerged as a high-performance alternative in the single-ply roofing market.
Installing TPE roofing is somewhat easier than other thermoplastic single-ply roofing materials. A significant advantage of TPE over TPO is that it doesn’t have the extreme sensitivity to dirt on the membrane while heat-welding the seams that TPO has. This makes seam welding easier, allowing for more consistent and reliable installations with fewer installation failures due to contaminants.
Unlike PVC and TPO, TPE roofing membrane allows successful welding across a wider temperature range, which makes the installation process much easier for the roofers. Because of this, TPE membranes can be installed in a wider range of weather conditions, reducing the likelihood of cold-weather welding failures or overheating issues that can sometimes affect other thermoplastic membranes.
TPE roofs are also much easier to repair – small punctures can be resealed through the application of heat, a feature completely absent in PVC and TPO roofing membranes, which require a separate patch to be applied. This self-healing characteristic enhances long-term maintenance, as minor damage can be addressed quickly without additional materials. Additionally, TPE remains flexible over time without requiring the use of plasticizers, reducing the risk of cracking or embrittlement.
TPE roofing membranes combine the positives of PVC, including flexibility and high weldability, and those of TPO, including being plasticizer-free, chlorine-free, and heavy metal-free. As a result, TPE offers an environmentally friendly alternative while maintaining high performance, chemical resistance, and durability. Its formulation resists degradation from UV exposure and weathering, making it a long-lasting choice for commercial and industrial applications.
TPO (Thermoplastic Polyolefin)
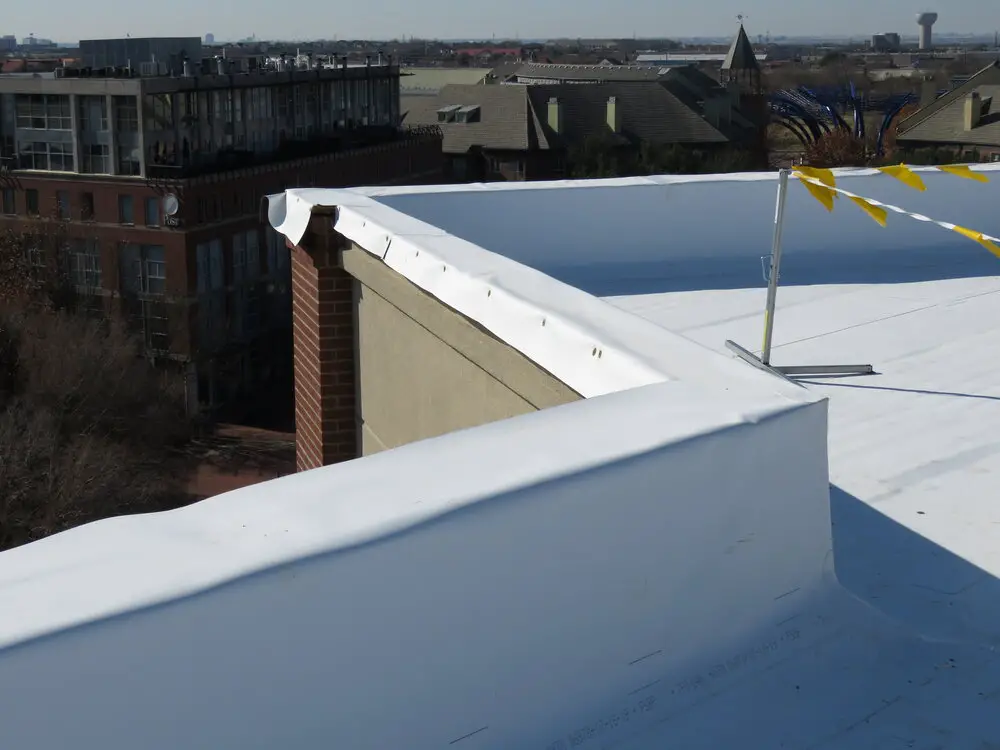
Color Availability: White, Gray
Attachment Method: Fully-Adhered, Mechanically-Fastened, Ballasted
Seaming or Patching Method: Hot Air Welded
Asphalt Compatibility: Good
Resistance to Oils, Coolants, and Grease: Animal Fats – Excellent; Petroleum – Poor
In Use Since: 1980s
TPO (Thermoplastic Polyolefin) is the most common type of roofing material used in new low-slope (“flat”) roofing applications. It is a highly durable, although relatively stiff material, that is resistant to many environmental factors, making it a very decent roofing material. TPO is engineered to combine the best characteristics of PVC and EPDM, offering the heat-weldability of PVC while remaining free of chemical plasticizers, like EPDM.
TPO single-ply roofing systems are by far the most popular commercial roofing systems being installed today. Its widespread adoption is due to its relatively low cost, ease of installation, and ability to meet modern energy efficiency standards. Most TPO membranes are white and reflect heat, helping reduce cooling costs and meet cool roofing requirements set by organizations such as ENERGY STAR and LEED.
TPO sheets are thermoplastic; they are heat-welded together to form a continuous, seamless roofing membrane. The seams created by heat welding are typically stronger than the membrane itself, providing superior waterproofing performance compared to other seaming methods like adhesives or tapes.
TPO membranes are available in different thicknesses, including 45-mil, 60-mil, and 80-mil, allowing building owners and contractors to select a membrane that meets their specific durability and performance needs. They can be installed in different ways, such as fully adhered, mechanically attached, or ballasted, making them adaptable to various building structures and project requirements. Mechanically attached TPO systems are particularly common, as they provide a balance of cost-effectiveness and wind uplift resistance.
As fairly recent part of the commercial roofing industry, TPO membranes continue to evolve, with manufacturers still improving on their formulations to enhance flexibility, long-term weathering performance, and overall durability.