Table of Contents
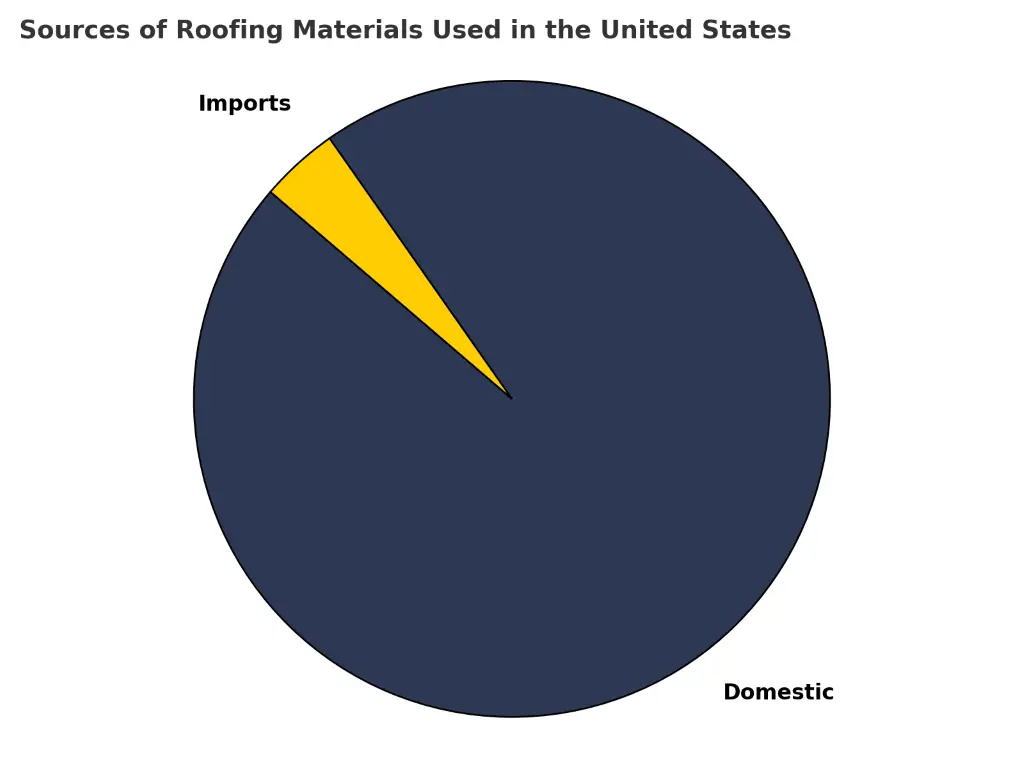
Introduction
Sometimes people email me out of the blue asking for roofing advice (and I try to respond if I have time to give them a proper answer). These emails are usually about the best product for this, the right way to do that, what’s causing this leak, whether the price they got from a contractor was reasonable. Normal roof stuff. But not too long ago I got two different emails where the guys were planning some roof work for later in the year and they wanted to know if it made sense to go out and stock up on roofing materials right now, before prices shot up because of tariffs.
My impression after years of dealing with roofs, roofing products, roofing manufacturers (and so on) was that roofing materials were pretty much all made here in the US, so no, it wouldn’t make sense to run out and start hoarding roofing supplies. But I realized I only felt this way because every roof I’ve ever worked on, around the country, commercial and residential, low-slope and pitched, in over 20 years as a roof consultant, used American-made materials. It was really just an impression that I had.
I’d never done any actual research to confirm that this was really the case, so I decided to look into it so I could cite data if I ever needed to. I gathered all the relevant information I could and turned it into a report. AI processing helped, but I did do a lot of fact-checking, rewriting, verifying sources, etc. The report really got out of hand (it’s very long), but I figured it would be helpful to stick it on a web page in case anyone else wanted to read it, or at least parts of it. Here it is.
Too Long; Didn’t Read
Most roofing materials sold in the United States are produced domestically. Approximately 96% of roofing products are manufactured within the U.S.
Asphalt shingles dominate residential roofing, covering around 80% of American homes. Production is spread across the Midwest, South, and California, led by manufacturers such as GAF, Owens Corning, and CertainTeed.
TPO, EPDM, and PVC membranes for commercial low-slope roofs are overwhelmingly produced in U.S. plants by companies like Carlisle, Holcim Elevate, Johns Manville, and a couple of others.
Metal roofing materials (steel, aluminum, and copper) are mostly U.S.-made from domestic metals. However, zinc roofing material is primarily imported from Europe.
Clay and concrete tiles are largely manufactured domestically in Florida, Texas, Arizona, and California, although some clay tiles are imported from Mexico and Spain.
Slate roofing is a split category: slate is still quarried in traditional American locations like Vermont, New York, Pennsylvania, and Virginia, but the majority of new slate roofs use imported Spanish, Chinese, or Brazilian slate.
Cedar shakes and shingles predominantly come from Canada’s British Columbia, with additional production in Washington State.
Synthetic roofing products (such as composite slates and shakes) are produced almost entirely within the United States, including in Kansas, Pennsylvania, Iowa, and Texas.
Imports account for about 4% of the total U.S. roofing market, primarily sourced from Canada, Mexico, Spain, and China.
Environmental trends are boosting the use of recycled materials, especially in synthetic roofing and rubberized shingle production.
The U.S. roofing supply chain remains strong, localized, and resilient, meaning that roofing material availability is rarely disrupted by international trade issues.
Report on the Sources of Roofing Materials Used in the U.S.
Roofing materials in the United States are primarily produced domestically at dozens of manufacturing plants across the country. In 2022, imports made up only about 4% of U.S. roofing sales. Most roofing imports come from nearby trade partners, with Canada accounting for about 70% of imports, along with a few specialized foreign sources.
This report examines where major roofing materials are manufactured or sourced, covering each material type, key U.S. production hubs, major manufacturers and supply chains, market share and production volumes, and the balance of domestic production vs. imports. Recent data (2022–2024) are highlighted alongside longer-term trends in sourcing and manufacturing.
(Below, roofing materials are grouped into low-slope (commercial/industrial) and steep-slope (residential) categories for clarity. Key manufacturers and their plant locations are noted for each material type, along with whether the U.S. supply is primarily domestic or import-reliant.)
Low-Slope Roofing Materials & Production Origins
Low-slope roofs (typical on commercial buildings) use membranes or built-up systems. The U.S. has a robust domestic industry for these materials, led by companies like Carlisle, Holcim (formerly Firestone Building Products), Johns Manville, GAF, and others. Imports play a minor role, aside from certain specialized products. Below we detail each major low-slope roofing material:
EPDM Membrane Roofing
Production Origin: Ethylene Propylene Diene Monomer (EPDM) rubber membranes are predominantly manufactured in the U.S. EPDM roofing became popular in the 1980s, and American companies built large domestic plants to supply demand. For example, Firestone opened a major EPDM plant in Prescott, Arkansas, in 1983 – once the world’s largest EPDM facility.
Today, Carlisle SynTec and Holcim Elevate (formerly Firestone) are the leading EPDM producers, each operating multiple U.S. manufacturing sites. Carlisle manufactures EPDM at plants in Carlisle, PA; Greenville, IL; and Tooele, UT, among others. Holcim Elevate primarily manufactures its American EPDM roofing products in Prescott, AR. Johns Manville (JM) also manufactures EPDM domestically, having launched a state-of-the-art EPDM production line in Macon, GA, around 2012.
Overall, EPDM roofing is a domestically supplied product in the U.S., with negligible imports. Major raw materials (EPDM polymers and carbon black) are sourced from the petrochemical industry, but membrane production (mixing, calendering, and vulcanizing the sheets) is handled in-house by these manufacturers.
Major EPDM Manufacturers & Supply Chain:
- Carlisle SynTec (Carlisle Companies): The largest EPDM producer, with U.S. plants located in Pennsylvania, Illinois, Utah, and other states. Carlisle sources EPDM rubber polymers from chemical suppliers, is vertically integrated into membrane production, and also manufactures its own insulation and roofing accessories.
- Holcim Elevate (formerly Firestone Building Products): Produces EPDM membranes at a U.S. plant in Prescott, Arkansas and may be expanding EPDM production to other locations. Holcim sources raw materials internationally but compounds and fabricates roof membranes domestically as part of its integrated roofing portfolio, which also includes polyisocyanurate insulation, asphalt products, and metal roofing components.
- Johns Manville (Berkshire Hathaway): Manufactures EPDM membranes at its plant in Macon, Georgia and other U.S. sites. Johns Manville opened an EPDM production facility in Milan, Ohio in 2012 to expand its commercial roofing offerings. The company often leverages its own fiber and nonwovens operations to supply reinforcement or backing materials for its membranes.
- Others: Smaller brands and affiliates often source their EPDM from larger manufacturers. Versico and WeatherBond (both currently secondary brands of Carlisle), source EPDM membranes from Carlisle. The vast majority of EPDM membranes sold in the U.S. are manufactured domestically by Carlisle, Holcim Elevate, and Johns Manville.
Domestic vs. Imports: The U.S. EPDM market is well over 95% supplied by domestic production. EPDM’s weight and curing requirements make imports impractical; even foreign firms have established U.S. production rather than try to export here. This material is not import-reliant. (Firestone’s European EPDM plant in Spain serves other markets, not the U.S.) EPDM membranes sold in America are made in the USA, primarily in states like Pennsylvania, Arkansas, Illinois, Utah, and Georgia.
TPO Membrane Roofing
Production Origin: Thermoplastic Polyolefin (TPO) single-ply membranes are also largely U.S.-manufactured. TPO gained popularity in the 2000s and today represents the largest share of new commercial roofs by area (about 40–42% of single-ply usage). Major domestic producers include Carlisle, GAF, Holcim Elevate (formerly Firestone Building Products), Johns Manville, and Sika Sarnafil.
Carlisle operates multiple TPO production lines, including plants in Greenville, IL and Senatobia, MS. GAF, best known for shingles, invested in TPO plants in New Columbia, PA and Cedar City, UT to become a top TPO supplier. Firestone (now Holcim Elevate) runs TPO production at three U.S. plants, historically including sites like Wellford, SC and Muscle Shoals, AL. Johns Manville expanded its TPO plant in Scottsboro, AL, adding a second production line in 2015 to meet growing demand.
Domestic production dominates TPO in America, though a small volume of TPO membranes may be imported from Canada or Asia under certain private-label brands.
Major TPO Manufacturers & Supply Chain:
- Carlisle SynTec: Produces “Sure-Weld” TPO at U.S. facilities in Illinois, Mississippi, Pennsylvania, and other states. Carlisle often co-locates TPO and polyisocyanurate insulation manufacturing to streamline low-slope roof system production. It sources polypropylene and ethylene propylene rubber resin domestically, with in-house formulation and extrusion of the membrane.
- GAF: Built a strong TPO presence under the EverGuard TPO brand. GAF operates plants in Pennsylvania, Texas, and Utah, with a new TPO line announced for Arkansas. GAF sources petrochemical resins and blends them in its U.S. factories. As a vertically integrated firm, it also manufactures its own TPO accessories and some raw materials, including fiberglass mats for other products.
- Holcim Elevate (formerly Firestone Building Products): Operates multiple TPO manufacturing plants across the U.S., supplying its UltraPly TPO membranes. Holcim Elevate sources raw polyolefin material globally, maintaining quality standards through ISO-certified production.
- Johns Manville: Manufactures TPO at its Scottsboro, AL facility, and possibly at two other single-ply membrane factories. Johns Manville has invested approximately $200 million in commercial roofing manufacturing in recent years. It purchases polymer pellets and reinforcement fabrics, producing membranes domestically.
- Others: Sika Sarnafil (Swiss-based) produces some TPO membranes in the U.S., notably at its Alabama plant, but is better known for PVC production. CertainTeed (French-owned by Saint-Gobain) introduced its own TPO in North America through an affiliate but primarily sources TPO membranes from other producers. By and large, U.S. demand for TPO is met by U.S. factories operated by the companies listed above.
Domestic vs. Imports: TPO roofing in the U.S. is overwhelmingly domestic, with minimal imports. Foreign TPO manufacturers based in Europe or Asia hold little market share in the American market. A key reason is that major U.S. roofing companies invested heavily in local TPO production, and the transportation cost for bulky rolls discourages offshore sourcing.
One exception is China, which has exported some TPO or raw sheeting to the U.S., although much of this material is classified generically as “roofing sheet” and remains a very small segment of the market.
The U.S. remains largely self-sufficient in TPO production, with plants concentrated in the Midwest and South, including Alabama, Mississippi, Illinois, Pennsylvania, and Utah, to efficiently serve nationwide demand.
PVC Membrane Roofing
Production Origin: PVC (polyvinyl chloride) single-ply membranes for roofing are produced both domestically and, to a lesser extent, imported. Several manufacturers make PVC roofing in the U.S., including Sika Sarnafil, Carlisle, Johns Manville, Duro-Last, and FiberTite (Seaman Corp). Sika Sarnafil operates a PVC membrane plant in Canton, MA, serving the U.S. market, and Sarnafil PVC has been made in Massachusetts for decades to comply with “Buy American” project requirements.
Carlisle recently added a new PVC production line at its Greenville, IL facility, an existing plant that also produces EPDM. Johns Manville manufactures PVC sheeting in Scottsboro, AL (alongside TPO production) and/or Macon, GA. Duro-Last fabricates PVC roof membranes at its plant in Saginaw, MI, where it receives rolls of PVC sheeting and custom-prefabricates roof sections.
These domestic facilities cover much of the U.S. market for PVC roofing membranes.
Imports: Some PVC roofing is imported, mainly high-performance Ketone Ethylene Ester (“KEE”) PVC from Italy or Germany, and commodity-grade PVC from China. For example, FiberTite (Seaman Corp) uses U.S.-made Elvaloy KEE-based membranes, but certain private labels, such as Soprema and Durakool, have historically sourced PVC rolls from Europe, particularly Italy.
Overall, U.S. production meets the majority of PVC roofing demand, with imports filling specific niche or low-cost market segments.
Major PVC Manufacturers & Supply Chain:
- Sika Sarnafil: A leading PVC brand, manufactured in Canton, MA for U.S. projects. Sika sources PVC resin, often from U.S. suppliers like Westlake or Formosa, and proprietary KEE plasticizers, formulating them in-house. They maintain a vertically integrated process, mixing, extruding, reinforcing, and laminating membranes within a single facility to ensure quality.
- Carlisle (Sure-Flex PVC): Carlisle’s PVC membrane production line in Illinois came online in 2014. It enabled Carlisle to supply PVC roofing membranes alongside its EPDM and TPO offerings. Raw vinyl resin and additives are procured domestically, and Carlisle performs calendering of PVC sheets with internal reinforcement at its plant.
- Johns Manville: Manufactures PVC membranes at facilities in Alabama and Georgia. Johns Manville likely uses some internal supply of fiberglass reinforcement (leveraging its glass fiber division) and sources PVC polymer externally. Production is fully domestic.
- Duro-Last: Duro-Last buys PVC master rolls, often from supplier partners in the U.S., and then fabricates custom-fitted roof sheets in Michigan. They operate as both a manufacturer and a fabricator, promoting “Made in USA” status for their finished roofing systems.
- FiberTite (Seaman Corporation): Produces a specialized PVC KEE alloy membrane in Wooster, OH. Although FiberTite membranes are often categorized separately as KEE membranes, they are based on PVC chemistry. Seaman Corporation is vertically integrated in coating fabrics with proprietary formulations.
- Others/Imports: Soprema imports some PVC membranes from its European plants for U.S. distribution. Although Soprema produces modified bitumen membranes domestically, its single-ply PVC membranes may still originate from France or Italy. Chinese-manufactured PVC membranes have appeared via distributors, but quality and code compliance requirements have limited their market reach.
Domestic vs. Imports: The U.S. PVC roofing market is majority domestic, but with a higher import share compared to EPDM and TPO. Industry estimates suggest that around 10 to 20% of PVC roofing used in the U.S. is imported from Europe or Asia, while approximately 80 to 90% is produced domestically.
However, the leading PVC roofing brands used in the U.S. (Sarnafil, JM, Carlisle) are manufactured domestically, with production facilities located in Massachusetts, Illinois, Alabama, Michigan, and Ohio. Most users prefer domestically produced PVC membranes for reliable supply and consistent quality, while imports mainly serve secondary or niche market segments.
Modified Bitumen Roofing (SBS and APP)
Production Origin: Modified bitumen membranes, often used on low-slope roofs in torch-down or self-adhered systems, are widely produced in the United States, though there are also some imports. These membranes are manufactured by blending asphalt with polymers, either SBS (styrene-butadiene-styrene) or APP (atactic polypropylene), and saturating and coating a reinforcement mat.
The U.S. has several plants manufacturing modified bitumen rolls. Key producers include GAF, CertainTeed, Johns Manville, Soprema, IKO, Siplast (owned by Icopal/BMI), Polyglass (owned by Mapei), and Malarkey. CertainTeed operates an asphalt roll roofing plant in Little Rock, AR, which manufactures rolled roofing and modified bitumen. Johns Manville has a bituminous membrane plant in Macon, GA.
Polyglass established U.S. production facilities in Fernley, NV, and Winter Haven, FL, despite being an Italian-owned company. IKO (a Canadian firm) operates modified bitumen lines at its U.S. shingle plants, including locations in Sumas, WA and Hillsboro, TX. Soprema built a large SBS membrane plant in Wadsworth, OH decades ago to serve the North American market.
There is a strong domestic manufacturing base for modified bitumen membranes across the Midwest, South, and West.
Major Mod-Bit Manufacturers & Supply Chain:
- GAF: Produces APP and SBS cap sheets under brands like Ruberoid. GAF operates asphalt roofing plants that manufacture both shingles and modified membranes, often on separate lines within the same facility. Key locations include Michigan City, IN, and Dallas, TX. GAF sources asphalt from U.S. refineries and polymer modifiers (SBS and APP) from chemical suppliers, then performs in-house blending and roll production. GAF does not mine its own minerals but partners with granule surfacing suppliers.
- CertainTeed (Saint-Gobain): Manufactures the Flintlastic® line of SBS and APP membranes. Facilities in Little Rock, AR, and Oxford, NC handle rolled roofing production. CertainTeed sources oxidized asphalt from refineries, sometimes produced on-site via asphalt “blowing” towers, and uses fiberglass or polyester mats, often supplied internally or by sister companies within Saint-Gobain.
- Johns Manville: Operates a large SBS mod-bit plant in Macon, GA and likely other facilities in Indiana or Alabama. JM uses its own glass fiber for mat reinforcement and sources SBS polymer to blend with asphalt on-site.
- Soprema: A French-Canadian manufacturer with U.S. operations. Its Wadsworth, OH plant produces SBS membranes (Sopralene, etc.) and APP sheets. Soprema often sources bitumen from local refineries and may import some specialty polymers from France. They have a high degree of vertical integration globally (even owning bitumen terminals), but in the U.S. they partner with suppliers.
- Polyglass (Mapei): Italian-owned but with U.S. plants (FL, NV). They initially imported rolls from Italy in the 1990s, but now manufacture locally. Polyglass uses Italian technology in U.S. factories to make APP torch membranes and self-adhered SBS sheets, using U.S. asphalt and imported APP polymer.
- Siplast (Icopal/BMI): Known for high-performance SBS (Teranap, Paradiene). U.S. manufacturing in Arkansas or Texas (Siplast is headquartered in Irving, TX).
- IKO & Malarkey: Both produce polymer-modified membranes alongside their shingle products. IKO in the U.S. (and Canada) makes torch-down and self-adhered rolls; Malarkey (based in OR) makes an SBS modified base sheet used in low-slope roofing, leveraging their polymer-modified asphalt expertise (Malarkey uses recycled polymers in asphalt mixes for both shingles and low-slope products).
- Others: Smaller regional asphalt refineries sometimes produce generic modified bitumen sheets or provide custom toll-blending for private labels, but the companies listed above are the major players.
Domestic vs. Imports: The majority of modified bitumen roofing sold in the U.S. is domestically produced, although import reliance is somewhat higher than for single-ply membranes. Italy has long exported APP membranes to the U.S., and some imported brands, such as INDEX and other Italian manufacturers, are available through distributors. Mexico also supplies asphalt roofing materials to the U.S. market.
Nonetheless, U.S. and Canadian producers satisfy most domestic demand. ARMA data indicate that in the low-slope asphalt roofing category, approximately 75% of U.S. shipments are modified bitumen products (48% SBS and 27% APP), while 25% are built-up roofing systems. This reflects strong domestic modified bitumen output. In the second quarter of 2024, mod-bit shipments reached a record 12.8 million squares across North America.
Production hubs for modified bitumen include the Gulf Coast and Southeast (due to proximity to asphalt sources) and the industrial Midwest. Imports from Italy, the UAE, and Mexico fill specific niche needs but remain relatively limited. The supply chain for modified bitumen membranes is heavily dependent on petroleum resources, and access to heavy asphaltic crude oil from the U.S. Gulf Coast or Canada is critical, tying production locations closely to refinery infrastructure.
Built-Up Roofing (BUR) & Roofing Asphalt
Production Origin: Built-up roofing (BUR) involves multiple plies of felt embedded in hot asphalt or coal-tar pitch. It is one of the oldest low-slope roofing systems and is still produced domestically, although its market share has declined massively in the past 25 years. Built-up roofs now account for less than 5% of low-slope roofing installations.
Roofing asphalt, the bitumen used as the waterproofing component in BUR systems and asphalt shingles, is a refinery byproduct and is largely sourced from U.S. petroleum refineries. Companies like Trumbull Asphalt (a division of Owens Corning) specialize in oxidizing asphalt to roofing grade. Most asphalt used in roofing applications, whether for BUR, membranes, or shingles, comes from domestic refineries processing heavy crude oil.
There is virtually no importation of finished roofing asphalt into the United States. However, raw bitumen feedstock can be imported, particularly from Canada’s oil sands, which is used to produce a significant portion of the asphalt used in U.S. roofing products.
Roofing felts, the reinforcing plies used in BUR, are also made domestically. Organic felt (paper felt) is less common today, having been largely replaced by fiberglass roofing felts produced by companies like Owens Corning and Johns Manville. These felts are manufactured in the U.S., with Owens Corning and Johns Manville operating fiberglass mat plants dedicated to roofing materials.
Overall, BUR systems and their component materials are domestically produced, often integrated into the same facilities that manufacture modified bitumen membranes or asphalt shingles.
Major BUR/Asphalt Producers & Supply Chain:
- Asphalt Refineries (Various): Roofing asphalt (asphalt “flux”) is produced by major U.S. refiners such as ExxonMobil, Citgo, and Phillips 66. Some roofing manufacturers maintain long-term supply agreements or operate their own asphalt processing units. For example, CertainTeed and GAF each operate asphalt blowing stills at select facilities to oxidize soft refinery asphalt into durable roofing-grade asphalt.
- Trumbull (Owens Corning): Historically operated dedicated roofing asphalt plants, including Trumbull facilities in New Jersey and Illinois, which processed asphalt for Owens Corning and other manufacturers. These facilities helped ensure a steady domestic supply of roofing-grade bitumen.
- Johns Manville and Others: Johns Manville’s bitumen needs for BUR and modified bitumen membranes are supplied from U.S. sources. Johns Manville and CertainTeed both manufacture fiberglass roofing felts domestically, which serve as the reinforcing plies for built-up roofing systems.
- BUR Felt Manufacturers: Atlas Roofing and GAF produce roofing felts, including asphalt-coated and uncoated base sheets, in the United States as part of their product lines. These components are distributed to roofing contractors for on-site assembly of built-up roofs.
- Coal Tar Pitch: Coal tar pitch, a niche material used in some built-up roofing systems, is a byproduct of coal coking and is produced domestically in limited quantities. Koppers Inc. is a primary U.S. supplier of coal tar pitch for specialty roofing applications. Although coal tar BUR systems are rare today, any coal tar roofing materials used in the U.S. market are sourced from North American production.
Domestic vs. Imports: Nearly 100% of built-up roofing (BUR) materials used in the U.S. are domestically produced. Asphalt is bulky and cheap, making international importation uneconomical. Historically, small amounts of natural asphalt or foreign bitumen may have been imported during shortages, but this has remained negligible overall. U.S. and Canadian crude oil supplies provide sufficient roofing asphalt. When Venezuela was a major source of heavy crude oil, it was imported and refined in the U.S., rather than importing finished asphalt products.
Roofing felts and fiberglass mats are also manufactured in the U.S. and Canada. BUR is an American-made roofing system, with production located near refinery hubs along the Gulf Coast and in the Midwest for asphalt, and in industrial centers like the Mid-Atlantic and Midwest for felts.
The key supply chain factor is the availability of heavy petroleum residuum. Environmental regulations and the industry’s shift toward lighter shale oil have sometimes tightened the domestic asphalt supply. However, the roofing sector has adapted by increasing imports of heavy crude from Canada and other countries.
(Many roofing companies that produce mod-bit also produce built-up roofing materials. For instance, GAF and JM sell asphalt and felts for BUR, leveraging the same domestic manufacturing base.)
Roof Insulation (Polyiso, EPS, XPS, SPF)
Production Origin:
Most of the low-slope commercial roof insulation in the U.S. is manufactured domestically. Rigid polyisocyanurate (polyiso) board, the most widely used roof insulation, is produced at dozens of facilities across the country. Expanded polystyrene (EPS) and extruded polystyrene (XPS) foam boards are also made in the U.S. by major manufacturers like DuPont (Styrofoam™) and Owens Corning, both of which rely on domestic petrochemical supply chains.
Spray polyurethane foam (SPF), another roof insulation type, is applied on-site, but its two-part chemical components, MDI isocyanate and polyol resin, are typically blended by U.S.-based chemical manufacturers and shipped within the country. While most insulation boards and SPF components are produced domestically, some raw ingredients (such as MDI isocyanate) are imported, often from China, to supplement U.S. supply.
Major Insulation Manufacturers & Supply Chain:
Carlisle SynTec (Hunter Panels/Insulfoam): Carlisle produces Hunter Panels polyiso at several U.S. facilities, often co-located with membrane plants for supply chain efficiency. It also owns Insulfoam, which manufactures EPS insulation nationwide. Carlisle sources most raw materials—polyols, facers, and blowing agents—domestically and integrates them into its roofing assemblies.
Johns Manville (a Berkshire Hathaway company): JM manufactures polyiso under the ENRGY 3® brand at plants in Ohio, Pennsylvania, and Texas. It also produces SPF systems and fiberglass insulation. JM sources polymeric MDI and polyols both domestically and globally, and laminates boards using fiberglass-faced facers made in-house or nearby.
Atlas Roofing: Atlas operates polyiso plants in Pennsylvania, Texas, Illinois, Georgia, Colorado, Arizona, and Canada. It also runs Atlas Molded Products for EPS insulation. Atlas sources blowing agents and isocyanates primarily through domestic suppliers and uses recycled-fiber or fiberglass facers. Its U.S. footprint helps minimize transportation costs and reliance on imports.
GAF: GAF manufactures EnergyGuard™ polyiso at plants in Cedar City, UT; Gainesville, TX; Statesboro, GA; and other locations. The company sources MDI, polyols, and facers domestically and formulates boards in-house for compatibility with EverGuard® membranes. GAF’s vertical integration also includes shingle and fiberglass mat production, enabling efficient material coordination across product lines.
Owens Corning: Owens Corning produces FOAMULAR® XPS insulation at several U.S. plants. It uses domestically sourced polystyrene resins and recently transitioned all XPS production to NGX® technology, which eliminates HFC-134a blowing agents. The company’s production is mostly domestic, with only limited imports of specialty chemicals.
DuPont (formerly Dow Building Products): DuPont manufactures Styrofoam™ brand XPS boards at U.S. plants in Illinois and Texas. It secures styrene monomer and polymers from Gulf Coast suppliers and uses HFO-based blowing agents that meet U.S. environmental standards. DuPont rarely imports XPS, since shipping it is cost-prohibitive.
Holcim Elevate (formerly Firestone): Elevate produces ISOGARD™ polyiso boards at U.S. facilities including those in Florence, KY and Bristol, CT. These plants use domestically sourced MDI and polyol ingredients and fiberglass facers. Most of Holcim’s insulation products for the U.S. market are produced domestically, with only minor raw material inputs from global sources.
Other Notable Players:
- CertainTeed (Saint-Gobain) markets FlintBoard® polyiso insulation, produced in U.S. and Canadian plants. Saint-Gobain may leverage ISOVER for technical inputs.
- Rmax (a division of Sika): Operates polyiso factories in Texas, Arkansas, and Nevada to serve U.S. markets.
- Soprema manufactures SOPRA-ISO™ polyiso boards in Quebec and distributes them into the northern U.S., supplemented by sourcing from U.S. partners.
Most significant suppliers operate U.S.-based manufacturing or source from just across the border, minimizing reliance on long-haul imports and supporting domestic supply continuity.
Domestic vs. Imports:
The vast majority of commercial roofing insulation used in the United States is manufactured domestically. Polyiso boards, in particular, are overwhelmingly made in the U.S. PIMA member companies operate more than 30 manufacturing sites nationwide, fully covering national demand. Because foam insulation boards are so bulky, shipping them long distances is not particularly cost-effective, which effectively eliminates foreign-made polyiso and EPS boards from the U.S. market. XPS insulation is similarly dominated by U.S. production from companies like DuPont, Owens Corning, and Kingspan, with only minimal volume potentially imported from nearby Canadian or Mexican facilities.
Where imports do exist, they are generally limited to raw material inputs or small-scale specialty products. For example, the U.S. imports some polymeric MDI, a critical polyurethane ingredient, to supplement domestic chemical production. A portion of EPS bead stock and polystyrene materials are also imported (primarily from Asia) but this is a small share of total market volume.
Importantly, many foreign insulation manufacturers have chosen to establish U.S. plants rather than export to the market. For instance, Kingspan (Ireland) manufactures XPS boards in Virginia, and Soprema (Canada/France) produces polyiso within North America for use in U.S. projects. High freight costs and insulation’s low value-to-volume ratio make importing finished foam products uneconomical in most cases.
Environmental regulations have further encouraged domestic production. When states like California began banning high–global warming potential (GWP) HFC blowing agents, companies such as Owens Corning invested in upgrading U.S. manufacturing to meet new standards rather than relying on imported alternatives.
Currently over 90% of commercial roof insulation used in the U.S. is manufactured domestically, with only minor reliance on imports for chemical ingredients or specialty materials.
Roofing Cover Boards (Gypsum, Cement, High-Density Polyiso)
Production Origin:
Roofing cover boards, whether gypsum-based, cementitious, or high-density foam, are overwhelmingly produced in the United States. Glass mat-faced gypsum boards like Georgia-Pacific’s DensDeck® and National Gypsum’s DEXcell®, along with USG’s Securock® gypsum-fiber panels, are manufactured at domestic gypsum board plants. These facilities use gypsum sourced from U.S. mines or synthetic gypsum (a byproduct of power plant scrubbers), which is widely available across North America.
Cement-based roofing cover boards, such as USG’s Securock® Cement Board and PermaBASE/DEXcell Cement, are also produced domestically. They are typically made using Portland cement, lightweight aggregates, and fiberglass mesh. The U.S. cement industry provides a strong local supply chain for these raw materials, and many plants leverage existing infrastructure from the wallboard or tile-backer board industry.
High-density polyiso cover boards, such as Carlisle’s SecurShield® HD and GAF’s EnergyGuard™ HD, are manufactured by the same domestic producers of standard polyiso insulation. These products are typically made on modified polyiso board lines at U.S.-based facilities.
Cover board products are made close to the construction markets, due to their weight and bulk. Importing cover board materials from overseas is rare, as the cost per pound to ship them would be uneconomical compared to making them domestically and trucking them regionally.
Major Cover Board Manufacturers & Supply Chain:
Georgia-Pacific (Koch Industries): GP is a top producer of gypsum roof cover boards, best known for its DensDeck® product line. These boards are manufactured at GP’s U.S. gypsum plants, many of which also produce wallboard and various fiberglass-faced panels. Facilities like the one in Savannah, GA source gypsum from Southeastern mines, while others use synthetic gypsum from power plant scrubbers. GP’s vertical integration, including gypsum mining and facer production, gives it stable domestic supply and reduces import needs. Its DensDeck boards are shipped from a nationwide network of over 20 manufacturing sites.
USG (Knauf): USG produces the Securock® line, including glass-mat-faced gypsum boards and gypsum-fiber boards. U.S. plants in Baltimore, MD; Rainier, OR; Aliquippa, PA; and Shoals, IN serve the roofing market using both natural and synthetic gypsum. The Securock Cement Board is also made domestically, though some production occurs in Canada. USG’s gypsum is mined in Iowa and Oklahoma, and the company incorporates recycled paper and fibers into certain boards. While Knauf brings international resources, Securock boards remain U.S.-manufactured.
National Gypsum (private): Through its Gold Bond division, National Gypsum makes the DEXcell® line of cover boards, including glass mat gypsum and cement variants. Plants in Anniston, AL; Shippensburg, PA; Mount Holly, NC; and elsewhere produce boards from domestic gypsum or synthetic gypsum and in-house facers. Cement board manufacturing is supported by various plants, using U.S. limestone, sand, and fiberglass. With its own gypsum mines and a strong U.S. logistics network, National Gypsum is a fully domestic supplier.
Carlisle SynTec: Carlisle manufactures SecurShield® HD, a high-density polyiso cover board, at its U.S. insulation plants. These ½-inch foam boards are produced using modified polyiso formulas and coated glass facers. The company sources MDI, polyol, and other ingredients domestically and integrates production into its broader commercial roofing systems. While Carlisle specifies the use of DensDeck® in some roof systems, it remains self-sufficient in manufacturing its own HD foam boards.
Holcim Elevate (formerly Firestone Building Products): Elevate offers ISOGARD™ HD, a high-density polyiso cover board made in the U.S. at insulation facilities like those in Florence, KY and Bristol, CT. Elevate sources polymeric MDI, polyol, and facers through North American channels, blending and laminating in-house. Its internal manufacturing approach supports full control over quality and availability, reducing the need for third-party boards.
Johns Manville (Berkshire Hathaway): JM produces ProtectoR® HD, a thin, high-density polyiso board. Plants in Ohio and Texas manufacture ProtectoR® HD using modified polyiso formulations. JM also distributes gypsum boards like DensDeck and Securock to fulfill many of its full roof system material orders. JM’s strategy emphasizes domestic integration across its roofing components.
GAF: GAF manufactures the EnergyGuard™ HD Composite Roof Board, combining high-density polyiso foam core with durable coated glass facers. The polyiso core is made at American GAF plants (in Texas and Pennsylvania, for example). GAF’s full assembly is completed in the U.S., and its polyiso components come from domestic and North American suppliers.
Other Cover Board Suppliers:
- CertainTeed (Saint-Gobain) manufactures fiberglass-faced gypsum panels under names like GlasRoc® or DiamondDeck, produced in U.S. and Canadian plants.
- FinPan and other regional players make cement boards that can serve as roof cover boards in specialty applications.
- Kingspan, while focused on PIR boards in Europe, sources U.S. gypsum boards or operates local acquisitions for stateside supply.
This market is dominated by North American production. Raw gypsum, cement, and foam ingredients are sourced and manufactured domestically. Even foreign-owned firms rely on U.S. facilities and local supply chains to serve the roofing cover board segment efficiently.
Domestic vs. Imports:
The U.S. roofing cover board market is supplied almost entirely by domestic manufacturers. Imports of cover boards are extremely rare. These products are heavy, bulky, and not high-value enough to justify overseas freight costs. Industry sources confirm that nearly all gypsum roof boards used in North America are produced within the region.
In practice, a “foreign” board might simply be one made in Canada, such as from CertainTeed’s Montreal plant, and shipped to northern U.S. markets. True imports from Europe or elsewhere are exceedingly rare and typically reserved for specialty applications. Even during temporary demand surges, suppliers expand local output or pull from nearby inventory rather than import product.
Economically, domestic production makes far more sense. Gypsum and cement boards have a low value-to-weight ratio, and long-haul transport significantly inflates costs. For example, a standard ½-inch-thick, 4’×8′ gypsum roof board weighs around 65 pounds; shipping that from overseas would be uneconomical relative to its price. That’s why manufacturers operate regional plants to keep transport distances short.
All major cover board producers also maintain supply chains rooted in North American raw materials—gypsum, cement, polymer chemicals, which eliminates much of the need for imported supplies. U.S.-made boards are engineered to meet ASTM, UL, and FM standards common in domestic specifications. Imported boards, by contrast, might not meet these standards without additional testing or certification.
In recent years, U.S. manufacturers have invested in new technologies, like hail-resistant gypsum boards and advanced polyiso formulations, developed and produced domestically rather than sourced abroad. As a result, virtually every cover board used in a commercial roof assembly in the U.S., whether a ½-inch gypsum panel or a high-density foam board, is produced in the United States or Canada. The combination of abundant raw materials, vertical integration, and economic and logistical constraints ensures the roofing cover board market demand is filled by North American products.
Steep-Slope Roofing Materials & Production Origins
Steep-slope roofs (typical on single-family homes) use shingles, tiles, metal panels, or wood. The U.S. is a huge producer of these materials, particularly asphalt shingles, although it also imports some specialty products (like natural slate or clay tile). Below we examine each steep-slope material:
Asphalt Shingles
Production Origin: Asphalt shingles are the dominant roofing material in U.S. housing, covering approximately four out of five residential roofs. The United States has a highly-developed domestic asphalt shingle manufacturing industry, with plants distributed across the country.
Major producers like GAF, Owens Corning, CertainTeed, IKO, TAMKO, Atlas Roofing, Malarkey, and PABCO operate dozens of shingle factories in various states. For example, GAF (the largest shingle manufacturer) has over 30 manufacturing locations across the U.S., including plants in Texas, California, Michigan, Pennsylvania, and elsewhere. Owens Corning’s roofing division operates 17 shingle plants in the United States, with a new facility planned in the Southeast by 2027. CertainTeed maintains approximately a dozen shingle plants, located in cities such as Milan (Avery), OH; Ennis, TX; Shakopee, MN; Oxford, NC; Peachtree City, GA; Shreveport, LA; Fremont and Wilmington, CA; Glenwood, AR; and Jonesburg, MO.
Other companies have strong regional manufacturing bases. TAMKO operates plants primarily in the central U.S., including locations in Joplin, MO; Dallas, TX; Phillipsburg, KS; Tuscaloosa, AL; and Frederick, MD. IKO operates plants across the South, Midwest (and also imports product from its Canadian facilities), with U.S. plants in Hillsboro, TX and Sylacauga, AL. Atlas Roofing manufactures shingles at plants in Mississippi, Oklahoma, and Virginia. Malarkey Roofing Products (bought by Holcim in 2022) has plants in Oregon, California, and Oklahoma.
Asphalt shingle production is heavily domestic and widely distributed across the country, often located near major population centers and raw material sources.
Major Asphalt Shingle Manufacturers & Supply Chain:
- GAF: The largest North American roofing manufacturer (part of Standard Industries). GAF’s shingle plants are strategically located across more than 20 states. Facilities include locations in New Jersey (Parsippany headquarters), Pennsylvania, Illinois, Minnesota, Texas, Georgia, and California. GAF recently announced a new plant in Newton, Kansas. GAF practices vertical integration by producing its own fiberglass mat at its Chester, SC plant, which ships mat to other GAF shingle plants on the East Coast. GAF sources asphalt from regional refineries and obtains ceramic-coated mineral granules from third-party suppliers, such as 3M, or through partnerships. With a network of over 30 plants, GAF ensures that most U.S. regions are served by a nearby factory, reducing freight costs and lead times.
- Owens Corning: A major shingle manufacturer known for its Duration® and Oakridge® shingles. Owens Corning operates 17 U.S. shingle plants and is expanding capacity to meet rising demand. Key locations include Toledo, OH (headquarters), Medina, OH, Summit, IL, Minneapolis, MN, Irving, TX, Kearny, NJ, Savannah, GA, and Portland, OR. Owens Corning is vertically integrated in glass fiber production, operating two glass melting plants to supply fibers for its roofing mats. Asphalt is sourced from U.S. refineries, and granules are obtained from suppliers like U.S. Silica or internal sources.
- CertainTeed (Saint-Gobain): A leading asphalt shingle producer known for its Landmark® series. CertainTeed operates shingle plants across the East, South, and West. It recently expanded its Oxford, NC plant, doubling production capacity, and opened a new facility in Jonesburg, MO, in 2020. CertainTeed benefits from Saint-Gobain’s vertical integration, leveraging in-house fiberglass mat production and ownership of aggregate mines. CertainTeed operates a granule mine in St. Louis, MO, and another in California. Asphalt is acquired domestically, and Saint-Gobain has invested over $100 million to boost shingle output in the Southeast to ensure supply security.
- IKO: A Canadian company with a growing U.S. manufacturing footprint. IKO operates plants in Illinois, Ohio, and the South, including facilities in Hillsboro, TX (opened in 2018) and Sylacauga, AL (opened in 2022). IKO is highly vertically integrated, producing its own fiberglass mat, mining its own granules (in Ontario and elsewhere), and operating asphalt flux refining facilities. However, much of IKO’s supply to the U.S. still comes from Canadian plants in Calgary and Ontario, especially for northern states.
- TAMKO: A long-standing U.S. shingle manufacturer, best known for its Heritage® series. Headquartered in Joplin, MO, TAMKO operates plants in Joplin, Phillipsburg, KS, Tuscaloosa, AL, Knoxville, TN, Frederick, MD, and Dallas, TX. TAMKO is vertically integrated, historically operating facilities for glass mat production, asphalt transportation, and other critical components. Its plants are strategically located near refineries, such as its Tuscaloosa facility near Gulf Coast asphalt sources.
- Atlas Roofing: A privately held company with shingle manufacturing plants in Hampton, GA, Ardmore, OK, Daingerfield, TX, and Franklin, OH. Atlas sources raw materials domestically and focuses on regional distribution strategies.
- Malarkey Roofing Products: An innovative manufacturer based in Portland, OR, with additional plants in South Gate, CA, and Oklahoma City, OK (opened in 2022). Malarkey incorporates recycled rubber and plastic into its asphalt binder, enhancing sustainability. Each Malarkey roof reportedly recycles the equivalent of thousands of rubber tires and plastic bags. The company sources materials within North America and owns granule coloring factories for surface finishes. Malarkey was acquired by Holcim in 2022.
- Others: PABCO Roofing operates a large shingle plant in Tacoma, WA, serving the West Coast. Building Products of Canada (BP) exports some shingles into the northern U.S. from Canadian facilities, although its presence in the U.S. market remains relatively minor. Several smaller regional brands and private-label shingles also exist, often relying on production through these major manufacturers.
Domestic vs. Imports: Asphalt shingle supply in the U.S. is overwhelmingly domestic. The United States not only meets its own demand but also exports shingles to other countries. Imports are minimal, consisting primarily of some volume from Canada. Canadian shingle manufacturers, such as IKO and BP, ship products to U.S. distributors, but many have built U.S. plants to avoid tariffs and reduce freight costs. Trade data shows that Canada is the leading foreign source of asphalt roofing imports, accounting for the bulk of the approximately 4% import share across all roofing categories.
Beyond Canada, only a small quantity of shingles is imported from Mexico, where a few Mexican shingle producers operate, or from Asia, although this volume remains insignificant in the overall U.S. market. According to the National Association of Home Builders and Freedonia Group, only about 7% of all construction materials (by value) are imported into the U.S., and the percentage is even less for roofing materials. More than 95% of asphalt shingles used in the United States are made domestically.
The Midwest and Southeast serve as major asphalt shingle manufacturing corridors, supported by access to petroleum refineries in the Midwest and Gulf Coast and proximity to growth markets in the South. States such as Ohio, Georgia, Texas, Arkansas, and Alabama host multiple shingle plants and act as distribution centers for surrounding regions.
Environmental and economic factors also influence plant locations. Manufacturers locate facilities near oil refineries to secure easy access to raw asphalt and near rail lines or stone quarries for the delivery of mineral granules. This explains why clusters of shingle plants exist in areas such as Houston and the Gulf Coast, the Midwest near Chicago and Toledo, and Southern California, all aligning with critical raw material logistics.
Market Share & Trends: Asphalt shingles hold by far the largest market share of any roofing material in the United States, accounting for approximately 75 to 80% of the overall residential roofing market by volume. However, alternative materials, particularly metal roofing, have been gradually chipping away at that dominance. As of 2023, metal roofing claimed about 18% of the U.S. residential market, making it the second most popular choice for residential roofing.
This trend has slightly reduced the share of asphalt shingles, which was around 85% a decade ago but is now between 75 and 80%. See here for 2024 production numbers.
The top three manufacturers (GAF, Owens Corning, and CertainTeed) likely account for over half of U.S. asphalt shingle sales. In fact, one industry report lists the market leaders in the overall U.S. roofing market as GAF, CertainTeed, Owens Corning, IKO, and TAMKO, notably all companies specializing in asphalt shingles. This highlights how central domestic shingle production remains to the overall U.S. roofing supply chain.
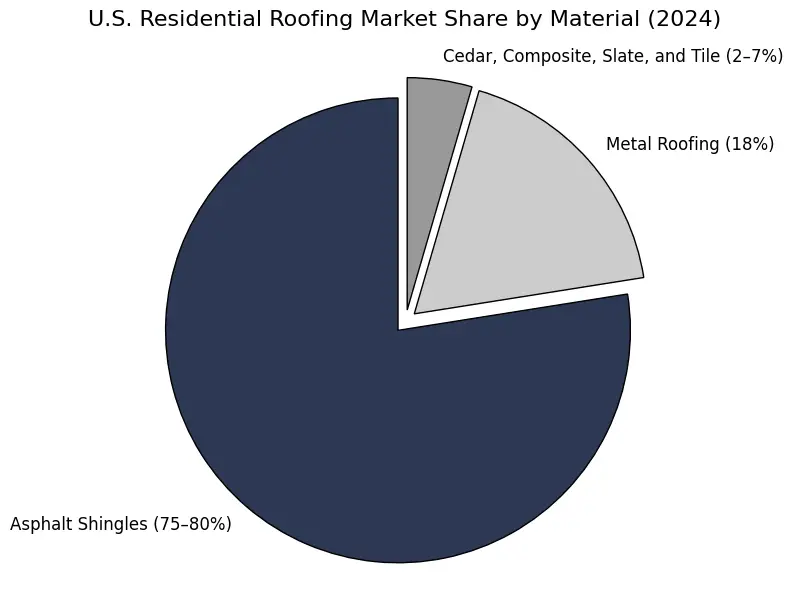
Clay Tile Roofing
Production Origin: Clay roof tiles (terra cotta tiles) are produced both domestically and internationally for the U.S. market. In the United States, clay tile manufacturing is centered in regions with suitable clay deposits and high demand for tile roofs, primarily the Southeast, South Central, and Southwest. Historically, Florida and Southern California served as major hubs.
Ludowici Roof Tile in New Lexington, Ohio, one of the oldest U.S. clay tile manufacturers (operating since the 19th century), continues to produce architectural clay tiles using Ohio clay. In the South and West, Boral Roofing (formerly Australian-owned, now part of Westlake Royal Building Products of the U.S.) operated several clay tile plants in states like Texas, Florida, Arizona, and California. Boral’s U.S. clay tile operations, now under Westlake Royal Roofing, include facilities in Lake Wales, FL, and Kilgore, TX. Another manufacturer, Eagle Roofing Products, primarily focuses on concrete tiles but has produced clay tiles or acquired clay tile lines in California.
Imports also play a role in the U.S. clay tile market, particularly for high-end and mass-produced Mediterranean-style tiles. Mexico is a significant source due to proximity and style similarity; many “Spanish” or “Mission”-style clay tiles used in Texas and California are manufactured in Mexico. Spain and Italy also export clay tiles to the U.S., supplying premium glazed products and unique tile profiles for specialty projects. According to trade data, Mexico and Spain are among the leading suppliers of roofing tiles to the U.S.
Because clay tiles are heavy and relatively expensive to ship, domestic production and Mexican sources (via land transport) fulfill most of the U.S. market demand.
Major Clay Tile Manufacturers & Supply Chain:
- Westlake Royal Roofing (formerly Boral US): Westlake acquired Boral’s North American roof tile business in 2021. They manufacture clay (and concrete) tiles in multiple U.S. locations. Notable clay tile plants: Florence, AL (a newer plant for clay tile), Lake Wales, FL, and Stockton, CA (which was Boral’s clay tile kiln for West Coast). Westlake Royal sources raw clay locally (Florida clay, Alabama clay, etc.) and utilizes natural gas kilns to fire the tiles. They are vertically integrated to some degree, owning clay pits and controlling the glaze/finishing processes.
- Ludowici Roof Tile: Based in Ohio, Ludowici uses local Ohio clay to produce a wide range of barrel and shingle tiles, often for historic restorations or luxury homes. They are unique in the Midwest; their products are proudly “Made in USA” and even exported. They source their own clay (on-site quarry) and operate advanced kilns – vertically integrated from raw earth to finished tile.
- Redland / MCA: MCA (Maruhachi Ceramics of America) produces clay tiles in Corona, CA. Redland Clay Tile (offshoot of an English company) had U.S. production too (though some CA plants have closed or been absorbed by others). These West Coast producers use California or Arizona clay and serve the Western states.
- Import Brands: A few European brands have U.S. distributors: Santafé (Colombian clay tile, some distribution in Florida), Tejas Borja or La Escandella (Spanish tile companies) ship high-end tiles for specialty projects. Some of these imports are used when a specific look or profile is desired that domestic makers don’t produce. Import supply chains involve container shipments to U.S. ports (adding cost).
Domestic vs. Imports: Clay tile roofing in the U.S. is supplied by a combination of domestic production and imports, with the balance varying by year. Although clay tiles represent only a small share of the overall roofing market, their physical weight gives domestic producers a cost advantage for most projects.
Mexico leads in clay tile import volume, due to lower labor costs and proximity for trucking into markets like the Southwest and Texas. Spain is also a notable exporter, particularly for premium clay tile products. Spain also plays an important role in clay tile exports to the U.S.
After major hurricanes in Florida, imports of clay tiles from Latin America and Europe typically increase temporarily to meet rapid re-roofing demand. Overall, the clay tile supply chain in the U.S. is partially import-reliant – more so than lighter materials like asphalt shingles – but there remains a strong domestic manufacturing base.
Environmental and economic factors: access to quality clay is key (hence plants near clay quarries in Ohio, Alabama, etc.), and energy costs for firing kilns are significant (U.S. natural gas prices give domestic plants an edge over some international competitors).
(A regional note: Florida and California consume a lot of clay tile roofing, and conveniently each of those states hosts tile factories (Lake Wales, FL and Corona, CA, etc.) as well as receives imports by sea. This regional production-consumption alignment reduces supply chain friction.)
Concrete Tile Roofing
Production Origin: Concrete roof tiles, made from cement, sand, and pigments, are a common steep-slope roofing material, particularly popular in the Sunbelt states, including Florida, Texas, Arizona, and California. Concrete tiles are primarily produced domestically because the product is relatively inexpensive and extremely heavy, typically almost 40% heavier than clay tiles, so long-distance shipping doesn’t normally make sense financially.
Major U.S. concrete tile producers include Westlake Royal Roofing Solutions (formerly Boral Roofing) and Eagle Roofing Products, along with a few regional manufacturers. Westlake Royal manufactures concrete tiles at several U.S. facilities, including Rialto, CA (a large plant serving the West Coast), San Antonio, TX, Lake Wales, FL (adjacent to its clay tile plant), and Oahu, HI (serving Hawaii’s market). Eagle Roofing Products, a U.S.-owned company, operates significant concrete tile plants in Rialto, CA; Phoenix, AZ; Stockton, CA; and Sumterville, FL. Eagle’s Rialto and Sumterville facilities are among the largest in production capacity in North America.
Concrete tile production is generally concentrated in the Southwest (California and Arizona) and Southeast (Florida), located strategically near sources of raw materials (cement production and aggregates) and close to the core markets for tile roofing in hot climates.
Because concrete tiles can be manufactured using widely available materials like cement and sand, imports are minimal. One rare example involves imported fiber-cement slates or tiles from Europe, used occasionally as specialty alternatives to concrete tile, but these are niche products. Standard concrete tiles are not commonly imported, as any cost savings would be offset by freight costs. Although Mexico may ship small volumes of concrete tiles to U.S. border regions, domestic plants in Texas and California largely cover those needs. As a result, concrete tile roofing in the United States is overwhelmingly supplied by domestic production.
Major Concrete Tile Manufacturers & Supply Chain:
- Westlake Royal Roofing (Boral): Largest producer after acquiring Boral’s US operations. They use local cement (often from nearby cement plants – southern California cement factories supply the Rialto plant, for example), and local sand/aggregate. The production process is highly automated: extrusion or molding of wet concrete tiles, curing in kilns/autoclaves, and applying pigmented coatings. Westlake’s plants in California, Arizona, Texas, Florida give national coverage. Because cement is bulky, these plants are usually near cement sources (California’s Inland Empire for west, Texas for central, etc.).
- Eagle Roofing Products: A key U.S. owned competitor. Eagle’s facilities, like the 40-acre Sumterville, FL plant, produce tens of thousands of tiles per day, using Floridian sand and cement. Eagle similarly has a West Coast hub in Rialto adjacent to cement mills. Eagle is vertically integrated in that it designs its own molds and coatings, but it buys cement and sand (which are readily available commodities).
- Crown Roof Tiles: A smaller entrant with a plant in Arcadia, FL (opened mid-2010s by a UK-based firm) and another in Mexico. The Arcadia plant supplies some U.S. Southeast demand; the Mexico plant can supply the Texas market if needed. This shows a slight import channel (from Mexico) but Crown also localized with a U.S. plant.
- Entegra (formerly): South Florida had local producers like Entegra, but many have been acquired by bigger players or consolidated.
- Specialty: Some companies make lightweight concrete tiles or fiber-cement tiles. James Hardie once made fiber-cement roof tiles in the U.S. but exited the business. Eternit (Belgium) might export small quantities of fiber-cement slates.
Domestic vs. Imports: Well over 90% of concrete roofing tiles used in the U.S. are domestically produced. As noted before, the economics of shipping such heavy, low-margin products means imports are rare. Any imports that do occur are typically on a regional basis, like a Mexican plant sending a truckload into southern Texas, or a Canadian plant (if there was one) sending to Washington state (but Canada doesn’t export many concrete tiles).
One factor influencing production location is access to raw materials: cement plants and lots of sand are needed. Fortunately, the U.S. has both in key areas. Another factor is demand clustering: concrete tiles are used extensively in Florida, Gulf Coast Texas, Arizona, Nevada, California – all places where domestic plants exist relatively nearby, minimizing the need for imports.
The U.S. concrete tile market is essentially self-sufficient, with Florida and the Southwest as production heartlands.
Slate Roofing
Production Origin: Natural slate roofing (stone shingles split from metamorphic rock) has a long history in the United States, with major domestic production centered historically in New York, Pennsylvania, Virginia, and Vermont.
The U.S. still has active slate quarries today, particularly in these key regions:
- Slate Valley (spanning Vermont and New York) produces high-quality, colored slates (green, red, purple).
- Pennsylvania’s Slate Belt (Lehigh and Northampton Counties) still produces gray and black slates, although at reduced output levels.
- Virginia’s Buckingham County is home to the famous durable black Buckingham slate.
Several U.S. companies continue to supply domestic slate roofing, especially for restoration and high-end projects that specify American material. Notable suppliers include Vermont Structural Slate Co. and Newmont Slate (Vermont); Penn Slate (Pennsylvania); and Buckingham Slate (Virginia).
However, domestic production volume has declined over recent decades, as cheaper imported slate became more widely available.
Imports: Today, a large – possibly a majority – share of the slate roofing used in the U.S. is imported, primarily from:
- Spain: The world’s largest slate exporter, with vast quarries in Galicia. Spanish slate is high quality and cost-competitive. By the 2010s, Spain captured a significant share of the U.S. market. One report notes the U.S. is the sixth largest importer of Spanish slate, receiving about 8,500 tons in 2016.
- China: Exports a medium-grade blue-gray slate. China is a major source of low-cost slate, often used for residential projects where budget is a priority. Chinese slate made major inroads in the American market in the 2000s.
- Brazil: Exports primarily black and gray slates, softer than Spanish or Vermont slate but inexpensive and often used in both flooring and roofing.
Other minor sources include Canada (Newfoundland slate) and specialty producers in Wales and Italy, but their share of U.S. imports is small.
Recent trade data shows that Spain, China, and Brazil dominate U.S. slate imports, with Spain accounting for the largest share by value.
Major Slate Suppliers & Supply Chain:
- Domestic Quarries (VT, NY, PA, VA): Companies such as Newmont Slate Co. (Vermont), Greenstone Slate (Vermont), Penn Big Bed Slate (Pennsylvania), Buckingham Slate (Virginia), Hilltop Slate (New York and Vermont) operate quarries that extract blocks of slate, split them by hand or machine into shingles, and distribute primarily in the U.S. Northeast. They employ local labor, and the supply chain is simple: quarry to customer, with minimal processing beyond cutting and drilling nail holes. Transportation is typically by truck. Domestic slate is often specified for historical restoration projects requiring authenticity, such as roofs that use Buckingham or Vermont slate to match original materials.
- Spanish Slate Producers: Companies like Cupa Pizarras, Del Carmen Slate, and Camara Slate are major exporters. Slate is shipped in containers from Spain to U.S. East Coast ports such as Baltimore or New York. Spanish slate typically enters the U.S. supply chain through importers, who handle customs and distribution to roofing contractors and distributors. Spanish slate is valued for its consistency and usually arrives pre-cut to standard sizes, ready for installation.
- Chinese Slate: Various Chinese quarry companies export slate that is imported and relabeled by U.S. distributors. Chinese slate typically enters through West Coast or Gulf Coast ports. While quality can vary, earlier industry concerns about oxidation (pyrite content causing rust) have been partially addressed by sourcing from better quarries. Chinese slate remains a popular budget option, distributed through stone suppliers and specialty importers.
- Brazilian Slate: Primarily originating from Minas Gerais, Brazilian slate is typically black or gray, somewhat thinner than other types, and often sold through stone wholesalers who also handle floor tile. Imports usually arrive at U.S. East Coast or Gulf Coast ports.
- Synthetic Slate: Some projects use synthetic slate shingles made from rubber or plastic composites. These products are manufactured domestically to avoid the weight, fragility, and shipping costs associated with real slate. While it isn’t really slate at all, synthetic slate does compete directly in the same steep-slope roofing segment.
Domestic vs. Imports: The balance has shifted toward imports in the U.S. slate roofing market. By some estimates, imported slate now accounts for more than two-thirds of the slate roofing volume in the United States, while domestic quarries supply less than one-third, focusing primarily on high-end niche projects. In terms of dollar value, imported slate is generally cheaper; so even if imports represent around 70% by volume, they might be less by total market value.
Specific numbers: one industry report and another industry overview noted that Spain, China, and Brazil together accounted for the majority of roofing slate sold in the U.S. by the mid-2010s. Spain alone likely provides over half of all slate shingles installed in the country, with some reports indicating Spanish slate is used on more than 50% of new slate roofs. However, domestic slate still maintains a significant presence in specific regions. For example, in the Mid-Atlantic, many architects and builders prefer Buckingham slate from Virginia for its quality and historical authenticity.
Slate roofing in the United States illustrates how imports can dominate a market due to cost advantages, even though domestic production persists for specialty and premium applications.
Environmental and economic factors: Slate is heavy and highly durable. Surprisingly, freight from Spain by sea is cost-effective, as a single shipping container can carry many squares of slate, and ocean freight costs are lower per mile than overland trucking. As a result, Spanish quarries with lower labor costs can undercut U.S. suppliers even after accounting for trans-Atlantic shipping. Some U.S. slate, such as Buckingham slate, is regarded as far superior in appearance and durability (touted to last 150 years or more), maintaining steady demand for the higher-quality, locally-sourced products despite higher costs.
Cedar Shakes and Shingles
Production Origin: Cedar shakes and shingles (wood roofing) are produced primarily from Western Red Cedar trees, which grow in the Pacific Northwest. The historic center of cedar shake production is British Columbia, Canada, with significant output also coming from Washington State.
A very large portion of cedar roofing sold in the United States is produced in Canada, just across the border. British Columbia’s coastal forests supply cedar logs (often old-growth or salvage logs) that are split or sawn into shakes and shingles. Towns in the Fraser Valley and on Vancouver Island host many cedar mills. On the U.S. side, Washington’s Olympic Peninsula and Cascades foothills are home to several cedar shake mills.
Companies such as SBC Cedar (Quebec-based) and Teal-Jones (British Columbia-based) are major Canadian producers supplying the U.S. market.
Imports vs. Domestic: In this case, imports from Canada are so significant that the supply chain could be considered binational. Some estimates suggest that well over half of cedar roofing used in the United States originates from Canada, perhaps 60 to 70% historically. The U.S. Pacific Northwest supplies much of the remainder. There is minimal production of roofing shakes outside of this region, as Western Red Cedar does not grow abundantly elsewhere. (Some Alaska cedar is used for specialty shingles in Alaska, and Eastern White Cedar has historically been used for siding shingles in the Northeast, but not for roofing shakes or shingles in significant quantities.)
In the 1980s, trade issues cropped up, and the U.S. International Trade Commission examined potential import relief for the domestic cedar shake industry, due to competition from Canadian imports. Cedar Shake and Shingle Bureau sources also note that tariffs or quotas were considered because of the flood of Canadian cedar products. Over the long term, Canadian supply has proven indispensable, although availability has declined as old-growth cedar logging has been increasingly curtailed.
Major Cedar Roofing Producers & Supply Chain:
- Canadian Mills (British Columbia): Companies such as Waldun Forest Products, Teal-Jones Group, Direct Cedar Supplies, and SBC Cedar (marketed under the Resistas brand) process Western Red Cedar into shingles and shakes. These companies often manage their own logging operations or have agreements to source cedar blocks, including salvaged wood from downed trees. Many products are graded under Cedar Shake & Shingle Bureau (CSSB) standards, with #1 Blue Label representing the highest quality. Finished shakes and shingles are shipped by truck or rail into the U.S., often entering through Washington State distribution yards. Proximity to the U.S. border makes logistics straightforward and cost-effective.
- U.S. Mills (Washington State): Various smaller producers operate mills on the Olympic Peninsula and in the Puget Sound region, manufacturing cedar shakes from regional forests or from cedar logs imported from British Columbia. (Canadian logs are sometimes milled in Washington when regulations differ between the two countries.) The supply chain frequently involves logging companies in Washington’s national forests or on tribal lands selling cedar to local mills. The CSSB, headquartered in Washington, certifies many of these U.S. producers.
- Value-Added Treaters: Some cedar roofing products undergo fire-retardant treatment to comply with building codes, particularly in fire-prone regions. U.S.-based facilities apply pressure treatments to raw cedar shakes to achieve Class A or Class B fire ratings. For example, Chemco, Inc. in Washington operates a fire-treatment facility as part of the cedar roofing supply chain, ensuring material compliance for use in elevated fire risk zones.
- Alaska and Other Regional Producers: Small operations such as Alaska Cedar produce yellow cedar shingles for local use in Alaska. In the Northeast, Certi-label Eastern White Cedar shingles are manufactured primarily for siding applications, not roofing, as they are typically not durable enough for roof exposure. The center for cedar roofing production remains in the Pacific Northwest.
Western Red Cedar roofing is regionally produced in the Pacific Northwest for the entire U.S. The supply chain is constrained by natural resource location. Buyers in the Eastern U.S. are effectively importing cedar from 3,000 miles away, usually via wholesale distributors. This is an example of a product where U.S. production alone cannot meet domestic demand due to resource limitations, making Canada a key partner.
Domestic vs. Imports: Cedar roofing is one area where imports from Canada have historically exceeded domestic production. At times during the 20th century, Canada supplied as much as 80% of the cedar shingles used in the United States, although current data likely reflects a somewhat lower percentage due to reduced logging activity in British Columbia. Nevertheless, the U.S. continues to rely heavily on Canadian cedar. Tariff classifications specifically track “Western Red Cedar Shakes & Shingles,” highlighting its importance in trade data.
Canadian mills often benefit from lower stumpage costs, as much of the timberland in British Columbia is government-owned, which has historically given Canadian producers a pricing advantage. U.S. International Trade Commission (USITC) reports from past decades indicate that U.S. producers sought import relief due to Canadian imports undercutting domestic prices.
Today, environmental regulations and dwindling cedar resources on both sides of the border have tightened supply, leading to higher prices and some substitution with alternative products, such as composite shakes or asphalt shingles designed to mimic wood appearance. However, when genuine cedar is used, it still predominantly comes from the Pacific Northwest region, with a mix of U.S. and (mostly) Canadian production.
Western Red Cedar roofing is regionally produced in the Pacific Northwest for the entire United States. The supply chain is constrained by the natural distribution of the resource. Buyers in the Eastern U.S. are effectively importing cedar from approximately 3,000 miles away, moving it from British Columbia or Washington State to regions like New England, usually through wholesale distributors. Cedar roofing is a clear example of a product where U.S. production alone cannot meet domestic demand, making Canada an essential supply partner.
(It’s worth noting that alternative “cedar” products like synthetic cedar shakes have emerged, partly due to cost and availability issues. These synthetics are made domestically. See the Synthetic Composite section below.)
Metal Roofing (Steel, Aluminum, Copper, Zinc)
Production Origin: Metal roofing is a very broad category, including steel and aluminum panels (for residential and commercial roofs), architectural metal roofs (such as standing seam, flat seam, and metal shingles), zinc roofing, and copper roofing, used for high-end projects and often field-fabricated. The production and supply chain vary depending on the metal type.
Steel Roofing: The majority of steel roofing panels used in the United States, such as corrugated and standing seam panels, are manufactured domestically from domestically produced or sourced steel. Steel roofing typically begins as coils of galvanized or Galvalume® steel. Major U.S. steel mills, including U.S. Steel, Cleveland-Cliffs (formerly AK Steel), and Nucor, produce coil steel suitable for roofing. Some coils are imported from South Korea, Vietnam, or other countries, although tariffs imposed since 2018 have reduced steel imports.
Coils are then painted domestically, often by coil coaters such as Steelscape or Beckers Group. Regional manufacturers called roll-formers shape the coils into roofing profiles. There are hundreds of small roll-forming facilities across the country, especially in the South and Midwest, that custom-cut panels for local contractors. Larger companies such as American Building Components (ABC), MBCI, Fabral, Englert, and ATAS International operate multiple plants supplying metal roofing nationally, with facilities in states like Texas, Missouri, Pennsylvania, Arizona, and Idaho. Steel roofing production in the U.S. is highly decentralized.
Aluminum Roofing: Aluminum roofing, usually in shake, shingle, or standing seam form, uses rolled aluminum sheet, often alloy 3105 or similar, with a painted finish. The United States produces aluminum sheet (with companies like Novelis in Georgia and Arconic), although some material is imported. Aluminum coil for roofing is also coated domestically. Manufacturers such as Classic Metal Roofing Systems in Ohio and Interlock Roofing use primarily domestic aluminum. Some Canadian companies produce aluminum panels occasionally sold into the northern U.S. market. Aluminum’s lighter weight makes imports feasible, but the great majority of U.S. aluminum roofing products are domestically manufactured.
Copper Roofing: Copper sheet and coil used for roofing components such as standing seam roof panels, flashings, and gutters are typically produced domestically from mined or recycled copper. Revere Copper Products in Rome, New York, one of the oldest copper works in the country, supplies copper coil for roofing and other architectural uses. While some copper coil is imported from European producers like KME and Aurubis, a significant share of roofing copper is recycled domestically. Fabrication – such as forming panels or custom flashings – is typically performed by local sheet-metal shops, regional manufacturers, or even on-site, rather than in large factories.
Zinc Roofing: Zinc roofing materials are largely imported from Europe. VMZinc (French) and Rheinzink (German) are the two biggest manufacturers shipping zinc coils and sheets to the U.S. There is minimal domestic production of rolled zinc sheet in the United States; domestic zinc mining largely serves the galvanizing industry rather than roofing sheet production. As a result, zinc roofing materials are foreign-sourced, although installation is performed by U.S.-based roofers. Zinc roofing remains a small, high-end niche market.
Stone-Coated Steel Tiles: Companies like DECRA Roofing Systems and Westlake produce steel shingles coated with ceramic stone to mimic traditional roofing materials. DECRA operates a major manufacturing facility in Corona, California. Originally established by New Zealand’s Fletcher Metals, DECRA now manufactures domestically in the U.S. Tilcor, another New Zealand brand, occasionally distributes stone-coated panels to the U.S., but DECRA’s U.S. production expanded after trade cases in the 2000s reduced foreign imports.
Overall Trends: Metal roofing in the United States is largely domestically produced, particularly for mainstream steel and aluminum products. While raw metal inputs may still include imports (about 30% of steel used in U.S. construction was imported pre-2018 tariffs), fabrication into roofing profiles overwhelmingly occurs within the country. Reports indicate that China and South Korea export some raw coil and inexpensive stamped panels targeting the DIY market, but the majority of quality metal roofing materials by value are domestically produced and fabricated.
Major Metal Roofing Manufacturers & Supply Chain:
- Classic Metal Roofing Systems: Based in Ohio, Classic Metal Roofing manufactures aluminum shingles such as the Country Manor Shake using primarily U.S.-sourced aluminum.
- Englert: Based in New Jersey, Englert produces metal coil and portable roll-formers for standing seam roofing. It supplies painted coil and supports on-site fabrication for contractors, primarily serving the East Coast market.
- NCI Building Systems / Cornerstone Building Brands: This conglomerate owns brands such as American Building Components (ABC), MBCI, Metal Depots, and Fabral. They operate multiple roll-forming plants across the United States, producing panels for commercial and residential markets. NCI sources steel coil from U.S. mills whenever possible, supplemented by limited imports, and completes painting and panel forming domestically.
- ATAS International: Headquartered in Pennsylvania with a secondary facility in Arizona, ATAS manufactures metal shingles, tiles, and standing seam panels, primarily from aluminum and steel. They source raw coil domestically whenever available and produce all finished products in the United States.
- Union Corrugating: With several plants in the Southeastern U.S., Union Corrugating manufactures metal roofing and siding panels from domestically sourced coil.
- Rheinzink and VMZinc: These companies import zinc coils from Germany and France, respectively, for U.S. distribution. Some panel profiling and fabrication occurs stateside, but the base zinc material remains imported.
- Copper Suppliers: Companies such as Revere Copper Products in New York supply most of the architectural copper used in roofing. Typically, domestic copper scrap is refined and rolled into sheets in U.S. mills. Final fabrication—such as forming roof panels and gutters—is usually handled by sheet metal shops or on-site craftsmen, making copper roofing highly craft-driven.
- Metal Roofing Alliance (MRA): This industry organization represents U.S.-based metal roofing manufacturers and reports that residential metal roofing reached an 18% market share in 2023.
Domestic vs. Imports: The metal roofing segment in the United States is primarily based on domestic production, with some reliance on imported raw metal. Freedonia reports that aside from Canada, China and South Korea are notable sources for metal roofing imports, mainly referring to steel coils or inexpensive finished panels. Canada supplies some steel and aluminum coil to the U.S. market; Canadian steel producers such as Stelco and Dofasco have historically been exempted from certain tariffs and supply coil suitable for roofing applications.
Some specialized metal products, such as particular standing seam systems or designer metal tiles, are occasionally imported when foreign systems are specified for projects, although this remains rare. Metals used in U.S. roofing mostly come from North America or Asia.
The U.S. metal roofing industry benefits from vertical integration and strong localization. The supply chain typically moves from steel mills to coil coaters to roll formers to installers, with many of these steps occurring domestically. This structure has helped the metal roofing sector remain resiliently domestic. For example, during supply chain disruptions in 2021–2022, steel shortages extended lead times, but domestic mills ramped up production to help compensate.
Material sourcing factors also play a role. Steel and aluminum are energy-intensive materials but are highly recyclable. Many steel and aluminum coils used in metal roofing contain between 25 and 90% recycled content. Copper and zinc are 100% recyclable and often include a high percentage of recycled material. As a result, metal roofing materials in the United States frequently originate from domestic recycling streams, reducing the need for virgin raw material imports and improving the overall sustainability profile of metal roofs.
(Metal roofing’s growth in the United States — with metal now holding 18% of the residential re-roofing market — suggests that domestic manufacturers have been scaling up production to meet demand. The Metal Roofing Alliance (MRA) reported that 84% of metal roofing volume by square footage in the U.S. is in the residential sector as of 2023. This shift indicates that residential demand is the primary driver of metal roofing production, and that demand is largely met by U.S.-based manufacturers.)
Synthetic Composite Shingles and Tiles
Production Origin: Synthetic roofing materials, meant to mimic slate, wood, or tile, are a small but growing category. These include polymer composite shingles (often made of recycled rubber/plastic or polymer blends) and synthetic thatch or tile. These products are primarily produced domestically by a handful of specialized manufacturers. Key players in this niche are DaVinci Roofscapes (Kansas), Enviroshake (Canada), EcoStar (Pennsylvania), Brava Roof Tile (Iowa), CertainTeed (Symphony shingles, historically made in the U.S.), and F-Wave (Texas) among others.
Production Origin: Synthetic roofing materials, designed to replicate the appearance of slate, wood, or tile, represent a small but growing segment of the U.S. roofing market. These materials include polymer composite shingles and tiles (typically made with recycled rubber or plastics contributing to the polymer blend) and synthetic thatch. These products are primarily manufactured domestically by a handful of specialized companies.
Key players in this category include DaVinci Roofscapes (Kansas), Enviroshake (Canada), EcoStar LLC (Pennsylvania), Brava Roof Tile (Iowa), CertainTeed (with historical products like Symphony shingles), and F-Wave (Texas), among others.
DaVinci Roofscapes manufactures synthetic slate and shake products in Lenexa, Kansas, using engineered polymer formulas that include virgin resins combined with UV stabilizers to enhance durability and longevity. DaVinci is now part of Westlake Royal (parent company of Westlake Roofing), although production remains in Kansas.
EcoStar LLC, formerly a division of Carlisle, produces Majestic Slate, a rubber and plastic slate alternative, at its facility in Scranton, Pennsylvania. Their products are primarily made from recycled rubber (including post-consumer tires) and plastics.
Brava Roof Tile operates out of Cedar Rapids, Iowa, manufacturing composite Spanish tiles, cedar shakes, and synthetic slates using proprietary polymer blends designed for durability and UV resistance.
F-Wave, a newer entrant to the market, manufactures flexible synthetic shingles designed to replicate the appearance of asphalt shingles. Production takes place in Burleson, Texas, at a facility that opened around 2018.
Enviroshake, based in Ontario, Canada, manufactures a recycled rubber and plastic shake product. Although production is located in Canada, Enviroshake exports heavily to the U.S., particularly for coastal areas seeking a cedar-like appearance with a longer lifespan and reduced maintenance needs.
Major Composite Manufacturers & Supply Chain:
- DaVinci Roofscapes: Manufactured in Kansas, DaVinci’s supply chain involves sourcing polymer resins, UV inhibitors, and fire retardants domestically. The company molds synthetic tiles in a variety of shapes and colors. Vertical integration is limited; DaVinci purchases its raw chemical inputs rather than producing its own plastics. As part of Westlake, DaVinci could leverage Westlake’s broader chemical production capabilities, as Westlake is a major PVC and polymer manufacturer.
- Brava Roof Tile: Based in Iowa, Brava manufactures composite roofing products using a blend of recycled and virgin materials, including recycled agricultural plastic bags and other post-consumer sources. Their production is fully domestic. Brava markets heavily to the luxury home segment as a lightweight alternative to traditional clay or concrete tile.
- EcoStar LLC: Originally developed by Carlisle Companies in the 1990s, EcoStar’s products were designed using recycled rubber (primarily car tires) and plastics (including EPDM and TPO factory scrap). Now operating independently in Holland, NY, EcoStar continues to emphasize recycled content, keeping thousands of tires out of landfills annually. Their production remains fully domestic.
- F-Wave: Based in Texas, F-Wave manufactures synthetic shingles that install similarly to traditional asphalt shingles but are made from a single-piece polymer layer, avoiding issues like granule loss. F-Wave sources its polymers domestically and manufactures entirely in Texas, leveraging local polymer expertise. The company positions itself as a high-tech, fully American-made roofing material supplier.
- Enviroshake: Manufactured in Ontario, Canada, Enviroshake uses reclaimed materials to produce synthetic shakes. They export their products into the U.S. through distributors, with a modest share of the American synthetic roofing market.
- Euroshield (Gentek Building Products): A Canadian manufacturer specializing in rubber shingles made from recycled tires. Euroshield products, such as rubber shakes, are distributed in northern U.S. markets, particularly in the Great Lakes and New England regions. Although their U.S. presence is relatively small, they do contribute to the synthetic roofing market.
Domestic vs. Imports: The synthetic roofing segment is predominantly supplied by domestic production, driven largely by North American innovation. Canada contributes modestly through manufacturers like Enviroshake and Euroshield, but the United States and Canada together effectively supply this market, with little competition from overseas producers.
One reason is that synthetic shingles are typically tailored to North American roofing practices and sizing standards. Additionally, because synthetic roofing remains a relatively low-volume market, it has not attracted mass production from Asia. Many products also rely on recycled feedstock available locally, such as used tires, making North American production both logical and cost-effective.
In terms of market share, synthetic composites likely account for less than 2% of the residential roofing market. However, in the high-end re-roofing sector, synthetics have made some progress, replacing wood shakes in fire-prone areas and offering a lower-cost, lighter-weight alternative to natural slate.
Because these products are niche, production tends to be concentrated in single-factory operations. Each major manufacturer typically operates only one or two production lines, distributing through specialty roofing suppliers across the country. There are no significant imports from Europe or Asia in this segment; although Europe has its own synthetic slate producers, they have yet to penetrate the U.S. market meaningfully. As a result, the synthetic roofing market in the United States is almost entirely supplied by U.S. and Canadian manufacturers, with raw materials sourced mostly from domestic or USMCA-region recycling streams.
Supply Chain and Sustainability: A notable strength of the synthetic roofing segment is its reliance on recycled materials. Many products, such as those produced by EcoStar and Euroshield, boast recycled content rates as high as 80 to 95%. This reduces dependence on virgin raw materials and supports local recycling programs. As environmental concerns and sustainability demands grow, manufacturers have positioned their domestic production as eco-friendly, potentially providing a market advantage and opening the door to future government incentives.
Conclusion: Imports vs. Domestic Supply Summary
The United States roofing market is largely supplied by domestic manufacturing across all major material categories. Asphalt shingles, by far the largest segment, are produced in an extensive network of plants located coast to coast. Single-ply membranes for commercial roofs are manufactured by a few major companies concentrated in the Midwest and South, but these facilities more than meet national demand with minimal reliance on imports.
Traditional materials such as wood shakes and natural slate exhibit higher import shares, but they remain niche segments in terms of overall volume. Metal roofing involves some imported raw materials; however, most value-added work such as painting, coating, and roll-forming takes place domestically. This domestic orientation provides greater resilience against global supply shocks.
The supply chains for each roofing material are closely tied to U.S. natural resources: petroleum for asphalt products, aggregates for roofing granules, clay for tiles, forests for wood products, and mines for metals. The United States’ industrial strengths in steel production, aluminum rolling, and polymer chemistry also underpin roofing material production. Canada and Mexico complement the U.S. supply chain by contributing resources such as cedar, bitumen, and clay, forming a North American roofing supply bloc that is notably self-reliant. Buyers in the United States can be confident that their roofing materials are extremely likely to have been made in America.
As stated earlier, the U.S. roofing market is about 96% supplied by domestic production overall, with only about 4% imported. This imported fraction is very low compared to many other construction materials. The chief sources of these few imported roofing materials are:
Canada: The number one foreign source of roofing materials, constituting 70% of roofing material imports. Canadian imports include cedar shakes/shingles (majority of U.S. supply), asphalt shingles (some overflow from Canadian plants), and modified bitumen membranes (Canadian companies like IKO, Soprema shipping product). Canada’s similar climate, common standards, and geographic proximity facilitate this trade.
China: Provides some metal roofing materials (cheap metal panels, raw coil) and some slate. Chinese steel panels might be found in retail hardware stores or used in farm buildings, but after tariffs, their share dropped. Chinese slate (as discussed) has a presence in roofing.
Mexico is a key supplier of clay roofing tiles to the U.S., particularly barrel tiles, popular in the Southwest. Mexico also exports some bituminous roofing membranes and roll roofing products to the U.S. Mexico’s trade is aided by NAFTA/USMCA as well.
Europe: Italy was noted for bituminous membranes (modified bitumen was first developed in Italy) – Italian SBS/APP rolls (from makers like Index, Polyglass before it localized, etc.) have been imported. Spain is a principal source for natural slate and imported clay tiles. Germany/France send zinc and some copper, as well as high-end clay tiles occasionally. U.K. or Belgium might send small amounts of specialty products (some synthetic slate from U.K. has been trialed).
Rest of the world: Brazil for slate (as mentioned earlier). Japan or South Korea for metal (Korean steel/aluminum often comes indirectly via distributors).
However, none of these foreign sources exceed a few percentage points of the U.S. market on their own. The trade pattern underscores that roofing materials are heavy, specialized, and tied to local building codes, which naturally limits imports. In roofing, “Made in the USA” (or occasionally Canada) is the norm.
From a supply chain resilience standpoint, the dominance of domestic roofing material production is a strong advantage. The United States is not heavily exposed to international disruptions when it comes to roofing products. Trade issues such as steel tariffs have influenced material costs to some extent, but because the supply chain can normally pivot to domestic steel sources, roofing production has continued largely uninterrupted.
In fact, the U.S. roofing industry’s greatest dependencies are internal factors: for example, oil prices (which affect asphalt production), environmental regulations (which could impact asphalt or cedar availability), and the availability of domestic labor and manufacturing equipment. International factors such as shipping costs and currency exchange rates play only a minor role in roofing compared to many other building materials.
Sources & Citations
This report drew on data from industry associations (ARMA, NRCA, SPRI, Metal Roofing Alliance), government surveys (U.S. Geological Survey (USGS), U.S. Census Bureau), and trade publications (Roofing Contractor, Professional Roofing, Metal Construction News). Key references include:
- Freedonia Group, U.S. Commercial Roofing (2023) – for market size and import/export figures.
- Mordor Intelligence, United States Roofing Market Analysis (2024) – for recent survey statistics on material usage.
- Asphalt Roofing Manufacturers Association (ARMA) – press releases and “Fast Facts” on asphalt shingles (the “four out of five roofs” statistic, for example).
- Metal Roofing Alliance (MRA) – market share data for residential metal roofing (18% market share).
- Roofing Contractor Magazine – various reports on shipment trends and company expansions.
- Company reports and press releases:
- Owens Corning Newsroom – for plant expansions and production announcements.
- Holcim Group – for Firestone Building Products acquisition details.
- Carlisle Construction Materials – for U.S. plant locations and manufacturing capacity.
- U.S. International Trade Commission (USITC) and U.S. Census Bureau trade data – for notes on imports by country (such as Mexico’s share of asphalt roofing imports).
- Cedar Shake & Shingle Bureau (CSSB) and historical ITC documents – for background on cedar shake industry competition and trade issues.
- Professional Roofing (NRCA) and Roofing Magazine – for anecdotal insights on topics like recycling initiatives, labor availability, and regional production trends (cited where relevant).