Table of Contents
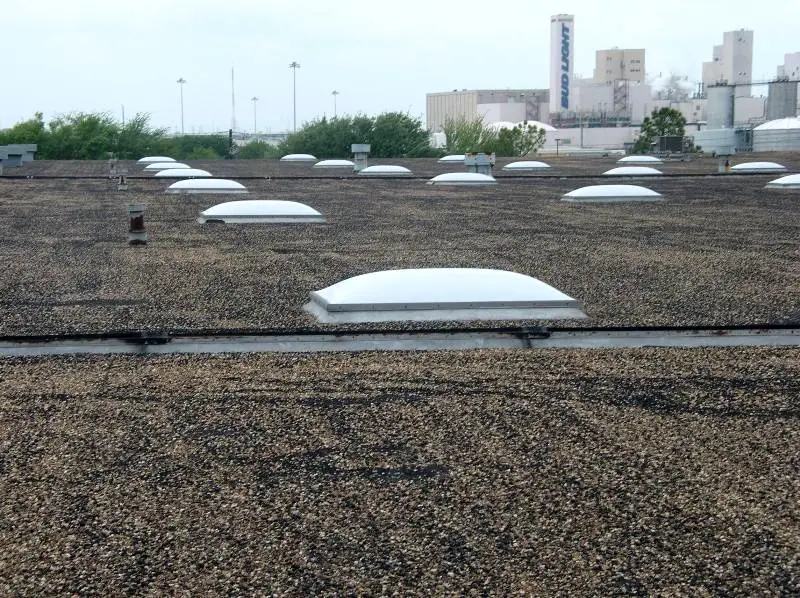
Introduction
I was responsible for maintenance and leak response for several commercial coal tar pitch roofs in Texas that were part of my company’s roof management portfolio for many years. I was also the roof observer on several very large roof replacement projects where coal tar pitch roofs were removed and replaced. I did a lot of research on coal tar pitch roofing so I could do my job better (in addition to the practical experience). This article is an attempt to share some of the things I learned.
Coal tar pitch roofing is a type of built-up roofing (BUR) in which coal tar pitch forms the waterproofing component of the roof membrane.
Coal tar pitch is a thermoplastic, highly viscous, and water-resistant material used primarily as a waterproofing and adhesive agent in built-up roofing and other industrial applications. It is derived from the distillation of coal tar, a by-product of coke production in steel manufacturing.
Coal tar pitch roofing is the original “tar and gravel” roof. It was so common and used on so many flat roofs for such a long time that even today, when most built-up roofs are asphalt-based and aren’t actually made of “tar,” they are still called “tar and gravel.”
Coal tar pitch is very rarely used today due to health concerns and the safety protocols which must be followed when working with it, as well as the steep decline in the use of built-up roof systems in general over the past few decades. Built-up roofing has almost completely been replaced by single-ply systems.
Coal Tar Pitch Built-Up Roof Systems
When used in roofing, coal tar pitch is melted on-site in a mobile industrial kettle and applied to the roof (normally with mops) as a hot liquid. The material is heated to approximately 400°F (204°C) to reach a workable viscosity. Specialized insulated roofing kettles with temperature controls are used to allow for a consistent application temperature. The hot pitch is piped to the roof and used to fill wheeled containers which convey the pitch to the application location.
Pitch-impregnated roofing felts are installed in overlapping courses during the application of the hot coal tar pitch to reinforce and strengthen the roof membrane. These reinforcement felts come in rolls; the individual felts are three feet wide and typically around 150 feet long. Felts may be organic or fiberglass, with fiberglass felts being the most common today due to their dimensional stability and the fact that fiberglass does not absorb moisture like organic felts.
The felts are rolled out into the hot coal tar pitch as the pitch is mopped onto the roof, with each layer of coal tar pitch on the roof getting a full layer of reinforcement felt. Each reinforcement layer of felts is fully embedded into the hot coal tar pitch; this ensures a fully bonded, monolithic roof membrane.
A layer of coal tar pitch that has been applied to the roof, along with the layer of reinforcing felts that are set into it, is called a “ply.” One ply in a finished coal tar roof is usually an eighth to a quarter of an inch thick. The layering process creates a redundant waterproofing system, where each ply provides additional protection against leaks, mechanical damage, and thermal expansion stress. The number of plies can be adjusted based on the specifier’s objectives for the roof, as well as the building owner’s budget.
The number of plies in a coal tar pitch roof roughly determines the length of the useful service life of the roof. A rule of thumb in the roofing industry is that each ply in a coal tar pitch roof system will add about 5 to 10 years to the life of the roof, depending on constraints like workmanship quality and the local environment. Typical coal tar pitch built-up roofs have four or five plies. Heavier-duty applications, such as industrial facilities or buildings in regions with extreme weather conditions, may have six or more plies.
To finish off the roof installation, gravel or other aggregate (such as slag or crushed stone) is typically set into an additional thicker surface layer of coal tar pitch called a “flood coat”. The gravel is applied at a rate of approximately 60-70 pounds per square (100 ft²).
This aggregate surface provides fire resistance and protects the coal tar pitch membrane from mechanical damage (from foot traffic or hail, for example). Unlike asphalt-based built-up roofs, which degrade under prolonged UV exposure, coal tar pitch generally remains stable, but it still benefits from the added protection of gravel. The embedded aggregate helps regulate surface temperature fluctuations, reducing thermal stress on the membrane and prolonging the lifespan of the roof.
You can see a coal tar pitch roof system specification on the Durapax website.
Short History of Coal Tar Pitch Roofing
This timeline highlights coal tar pitch’s progress from an industrial by-product to a dominant roofing material in the 20th century, and finally to its current status as a specialty material only used in a few niche roofing applications.
Early 1800s: Predecessors and Early Uses
- Before coal tar pitch, natural substances like pine tar were used for waterproofing, especially in maritime applications. The application techniques that developed around the use of these early materials laid the groundwork for more engineered low-slope roofing systems.
Mid-1800s: Emergence of Coal Tar
- With the industrial revolution came the rise of coke production for steel manufacturing. This process, known as destructive distillation of bituminous coal, produced a variety of by-products, one of which was coal tar.
- The residue from refining coal tar, known as “coal tar pitch,” was noted for its adhesive and water-resistant properties. Initially used for preserving timber and as a paving material, it was soon also used to waterproof buildings.
Mid-to-Late 1800s: Early Roofing Applications
- As urbanization and industrialization led to more flat-roofed buildings (warehouses, factories, etc.), the need for effective waterproofing solutions on low-slope roofs became urgent. Shingles and tiles only work on pitched roofs, and pine tar deteriorated too quickly.
- Coal tar pitch began being used in combination with organic reinforcement felts to create multilayered built-up roofing (BUR) systems. These systems consisted of alternating layers of coal tar pitch and sheets of felt (“tar paper”), providing a waterproof and very durable membrane.
Late 1800s to Early 1900s: Standardization and Expansion
- Coal tar pitch BUR became increasingly standardized, especially in industrial and commercial construction where flat or low-slope roofs were prevalent.
- Its cold-flow characteristics, which allow coal tar pitch to self-heal minor cracks and imperfections, made it particularly suitable for roofs prone to ponding water or subjected to significant freeze-thaw cycles.
1920s – 1950s: Golden Age of Coal Tar Pitch BUR
- During this period, coal tar pitch was considered the premium bitumen for low-slope roofing. It was widely used in major urban construction, government buildings, and factories. Most commercial low-slope roofs at this time were made with coal tar pitch.
- Formal specifications began to emerge. The ASTM established standards for coal tar pitch, including ASTM D450, which remains a key specification today.
1950s – 1970s: Increasing Competition from Asphalt
- As asphalt became cheaper and more widely available, it began to replace coal tar pitch in many roofing applications.
- Despite this, coal tar pitch retained a niche in the roofing industry, especially in environments where chemical resistance or ponding water was a concern.
1980s – 1990s: Decline Due to Regulatory and Market Changes
- Environmental and health regulations tightened due to concerns about the polycyclic aromatic hydrocarbons (PAHs) in coal tar.
- Many roofers and manufacturers shifted further toward asphaltic materials and the emerging single-ply systems like EPDM and PVC membranes.
- Production of the types of coal tar pitch used in roofing declined due to lower demand and stricter emissions standards.
2000s – Present: Niche Use and Legacy Systems
- Coal tar pitch remains in limited use for specialized applications, particularly for existing coal tar pitch roof system maintenance or for use in applications that demand superior chemical and water resistance.
- It is also occasionally specified in re-roofing projects involving historic buildings where original coal tar systems must be replicated or preserved.
Material Properties of Coal Tar Pitch Roofing
How Coal Tar Pitch is Made
Coal tar pitch is produced by distilling or heat-treating coal tar, which is a by-product of the production of coke or coal gas. The process involves controlled thermal decomposition, during which volatile components are driven off, leaving behind a dense, carbon-rich residue. This residue is then further refined through fractional distillation to achieve the desired consistency and performance characteristics.
Coal tar pitch is technically a fluid, but it seems to be a solid at normal ambient temperatures due to its high viscosity. The term “fluid” in this context refers to its ability to flow under certain conditions, particularly when subjected to heat.
At Australia’s University of Queensland, there’s a decades-long experiment that’s still going on, intended to demonstrate the fluidity of pitch. You can watch the pitch in real time as it drips once every 13 years or so. This is at room temperature; it gets much hotter on a roof, decreasing viscosity, and producing the “self-healing” quality for which pitch roofs are esteemed.
Although technically a fluid, coal tar pitch is extremely viscous, and can be considered a solid for practical purposes at normal temperatures. At room temperature, it can be somewhat brittle and may fracture under stress, but when it’s heated to temperatures exceeding 400°F (204°C), it becomes a workable liquid suitable for application in roofing systems. Its viscosity and hardness can be adjusted by blending it with various softening agents during production.
Beneficial Properties
Coal tar pitch roofing is known for its long service life, waterproofing capability, and chemical stability. It’s one of the most long-lasting roofing materials ever developed. Coal tar pitch is thermoplastic, meaning it softens when heated and hardens when cooled, allowing it to bond seamlessly with the reinforcement layers to create a continuous, waterproof membrane. This property also gives it a notable ability to self-heal, where minor cracks or punctures can gradually seal themselves just from the heat of the sun.
One of the biggest advantages of coal tar pitch roofing is its extreme resistance to standing water. Unlike asphalt, which deteriorates when exposed to prolonged ponding water, coal tar pitch remains chemically stable even in ponding water conditions. This makes it particularly valuable for low-slope (“flat”) roofs where drainage is poor.
Coal tar pitch does not degrade when submerged; historically, water was often pumped onto the surface of coal tar pitch roofs and allowed to sit there and slowly evaporate as a means to cool the building.
Coal tar pitch is also highly resistant to chemicals, UV radiation, and oxidation. It does not become brittle from sun exposure the way asphalt can, nor does it require coatings to remain serviceable. This makes it a good choice for industrial facilities, chemical plants, and roofs exposed to harsh environmental conditions, where chemical exhaust or pollution might degrade other materials.
Detrimental Properties
While coal tar pitch has many advantages, it also has significant drawbacks, which have led to its decline in usage. Health concerns are one of the biggest factors. Coal tar pitch contains polycyclic aromatic hydrocarbons (PAHs), which have been classified as carcinogenic.
Workers applying, maintaining, or removing coal tar pitch roofs must take extensive precautions, including ventilation systems, protective clothing, and personal respiratory protection, to limit exposure to harmful fumes. Increasing regulations has resulted in a growing reluctance on the part of specifiers, contractors, and building owners to use the material for new roof installations.
Another issue is the high-temperature application process common to all built-up roofs. Coal tar pitch must be heated to very high temperatures – typically over 400°F (204°C) – in order to become fluid enough for application. This creates fire hazards, burn risks, and exposure to toxic fumes; installing a built-up roof requires specialized equipment, safety protocols, and highly experienced workers.
The labor-intensive nature of a built-up roof installation makes it more expensive and yes, dangerous, compared to alternatives like single-ply membranes or modified bitumen, which have far fewer safety and health issues.
I was the roof quality assurance inspector on a built-up roof installation back in 2008 where there was an incident. It wasn’t coal tar pitch, it was asphalt, but that’s irrelevant. The roofers were hot-mopping (applying the hot asphalt) around a vent penetration through the roof, and some of the hot asphalt dripped down through the opening in the roof deck (where there was a hole cut for the vent) and somehow the drip lined up perfectly with a small gap in the drop-ceiling underneath the roof. It dripped through the drop-ceiling and landed on the arm of a receptionist in the office below, and burned her arm. She was fine, but it didn’t go over well.
Summary
While coal tar pitch roofing is incredibly durable roofing material and can last 50 years or more, its health risks, environmental concerns, and specialized handling requirements have led to its near disappearance from the modern roofing industry. In situations where a roofing material with an extremely high resistance to standing water and harsh chemicals is necessary, it is still used – but in most cases roof consultants, contractors, and building owners now go with safer, cheaper alternatives.
How to Tell Coal Tar Pitch and Asphalt Roofs Apart
You may be dealing with an old built-up roof and you may have no idea whether the material is asphalt or coal tar pitch. It’s important to know which one it is for a few reasons. There are different safety considerations when it comes to working on a coal tar pitch roof.
Coal tar pitch also behaves differently than asphalt physically. After its initial hot and liquid condition during installation, asphalt turns hard and rigid once it cools, and it becomes more and more brittle as it ages. Coal tar pitch doesn’t. These differences are important.
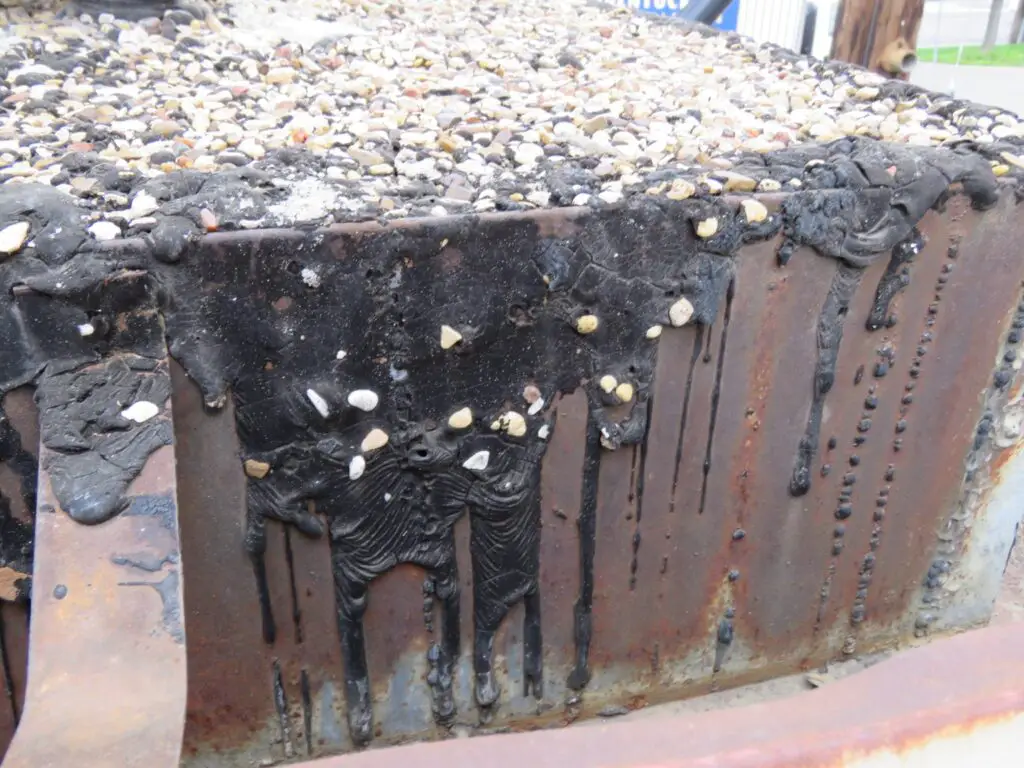
Asphalt would harden completely and would not develop ripples like this.
Roof Removal
Coal tar pitch contains high levels of polycyclic aromatic hydrocarbons (PAHs), which are classified as hazardous substances. Cutting up a coal tar roof releases fumes that require specialized ventilation and protective equipment, such as respirators and full-body coverings, to prevent skin absorption and the inhalation of toxic vapors. Asphalt, while still requiring safety precautions, does not pose the same level of health risk and is generally easier to remove and dispose of under modern regulations.
Roof Repairs
You should also know exactly what type of roof it is if you are repairing the roof. Asphalt and coal tar pitch are actually incompatible materials, so you need to know what you’re dealing with before you buy any repair materials. You really don’t want to use pitch-based material to repair an asphalt roof or vice versa. Coal tar pitch has a much lower softening point than asphalt, meaning that an asphalt patch applied over coal tar will likely fail as the pitch softens in warm weather. And applying coal tar pitch over an asphalt roof can lead to adhesion failures and chemical transfers that degrade both materials over time.
Roof Alterations
You need to know what kind of roof it is if you’re going to modify the roof. I once saw a roofing crew (who didn’t know it was coal tar pitch, they assumed it was asphalt) cut a hole in a coal tar pitch roof in order to install an exhaust vent system for the brand new restaurant kitchen below. The friction from the circular saw they used to cut through the roof caused enough heat to melt the edge of the roof around the new hole.
The now-liquid pitch dripped down through the hole and got all over everything. Coal tar pitch is extremely hard to remove, by the way. Some furious phone calls between the general contractor and the roofing company ensued.
Smell and Appearance
One way to distinguish between the two materials is by odor and appearance. Coal tar pitch emits a strong, sharp, characteristically smoky or creosote-like smell, particularly in warm weather. Asphalt has a milder, petroleum-like odor. Visually, coal tar pitch roofs tend to have a smoother, more glossy surface when freshly installed, while asphalt roofs typically appear duller due to oxidation.
If gravel or slag surfacing is present, it’s common to see the gravel slowly sink a little bit into the soft coal tar pitch as time goes by, whereas on asphalt roofs, the gravel stays exactly where it was when the asphalt cooled after application.
Solvent Test
A simple solvent test can confirm which material you’re dealing with. Coal tar pitch is highly soluble in toluene, benzene, and naphtha, while asphalt is not. The easiest way to conclusively identify a roof as being either asphalt or coal tar pitch is to take a small chunk of the material and drop it into some lighter fluid.
Coal tar pitch will soon turn the lighter fluid a green/yellow color. Asphalt will turn it brown. See the picture below.
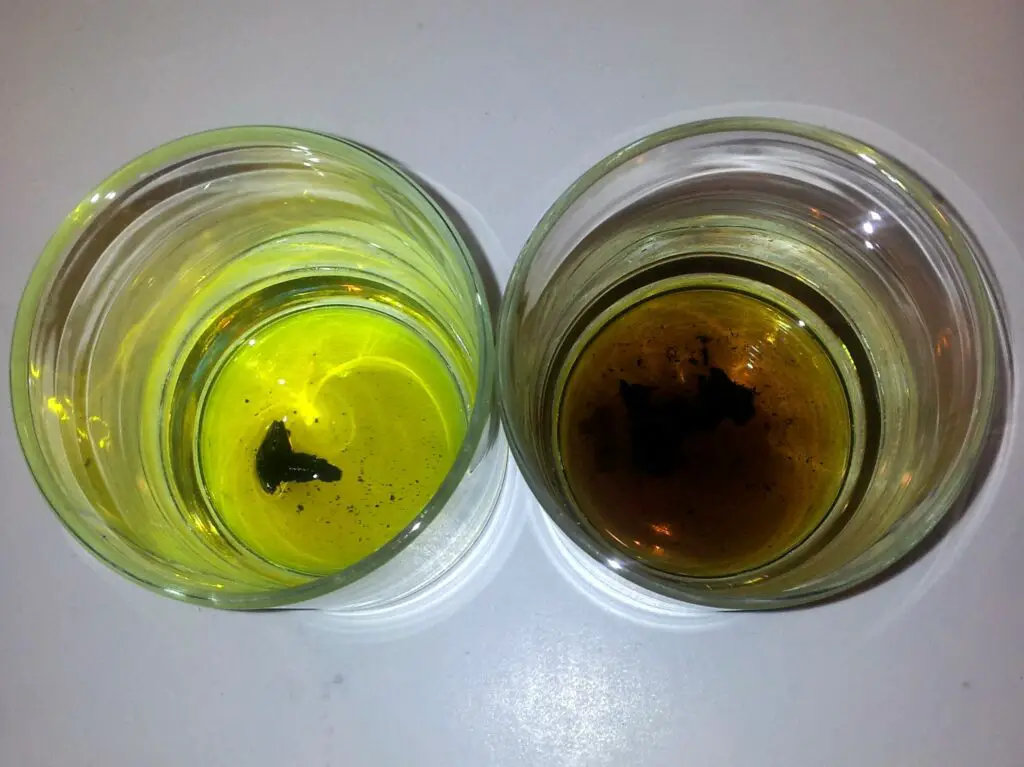
Coal Tar Pitch Roof Repairs
Extensive repairs on a coal tar pitch roof system should be made by a roofing contractor with a lot of experience in coal tar pitch roofing. The number of contractors with this kind of experience is declining steadily, so you may have to settle for a contractor with experience in asphalt built-up roofing. Of course, the number of contractors with experience in built-up roofing in general is also declining…
One important thing to remember when repairing a coal tar pitch roof is that coal tar pitch is not compatible with roofing asphalt or roof repair products made out of asphalt. When working on a coal tar pitch roof, you should use coal tar pitch-based materials. You want to be aware of this, and you want to double-check to make sure that your roofing contractor is aware of this as well, because many contractors don’t know.
It takes a while for asphalt to noticeably damage a coal tar pitch roof, but essentially what happens is that the asphalt and the coal tar pitch begin to combine chemically, to the detriment of each material.
You can easily make smaller repairs yourself by applying a 5-course roof cement patch to damaged or deteriorated areas of the roof. See my article on roof cement for directions on applying a 5-course fabric and mastic (another word for “roof cement”) roof patch. You should see if you can find coal tar pitch-based roofing mastic.
If you have to make emergency repairs that can be replaced fairly soon, or if you’re planning on replacing the roof itself in the near future, you can get away with using asphalt repair material.